Индуктор своими руками схема для плавки: Индукционная печь своими руками: схема, как собрать?
Простая индукционная печь своими руками по схеме
Индукционная печь — это словосочетание хорошо знакомо тем, чья профессия косвенно или напрямую связана с металлургией. Ведь именно в таких печах осуществляется процесс плавки металла.
Принцип работы индукционной печи — это процесс получения тепла от электричества, вырабатываемого переменным магнитным полем. В печах индукционного типа происходит преобразование энергии по схеме электромагнитная-электрическая-тепловая.
Индукционные печи подразделяются по видам:
— канальные;
— тигельные.
Для канального типа печей характерно расположение индуктора с сердечником внутри металла.
В тигельной — индуктор располагается вокруг металла.
У индукционных печей имеется целый ряд преимуществ по сравнению с другими печками или котлами:
— моментальный разогрев;
— фокусировка энергии;
— безопасность и экологическая чистота устройства;
— отсутствие угара;

В промышленности такие печи используют для плавки чугуна и стали, меди и алюминия, а также драгоценных металлов. Эти печи имеют различную емкость и частоту.
Именно принцип работы индукционной печи привел к созданию известной всем нам в быту микроволновой печи.
Индукционная печь
Собираем индукционную печь самостоятельно по схеме
При наличии специальной электрической схемы для этого устройства, вполне реально сделать ее своими руками. Вам необходим высокочастотный генератор с частотой колебаний 27,12 МГц.
Схема собирается на 4-х электронных лампах(тетрадах), нужна также нелегкая лампа для сигнализации о готовности к началу работы.
Особенностью такой индукционной печи, собранной своими руками по такой схеме, будет то, что ручка конденсатора находится снаружи. А, самое главное, что часть металла, расположенная в катушке, расплавится очень быстро даже в устройстве с малой мощностью.
Индукционная печь своими руками — схема
Прежде, чем собрать индукционную печь своими руками, надо прояснить, от каких факторов зависит скорость плавки металла:
— от скорости теплопередачи;
— от мощности генератора;
— от вихревых потерь и потерь на гистерезисе;
— от частоты.
Используйте лампы высокой мощности, но не более 4 штук. Питание печи будет происходить от сети 220В с выпрямителем. Если вы будете использовать печь для плавки металла, используйте графитовые щётки, если для обогрева — нихромовую спираль.
Собрать индукционную печь своими руками несложно и экономически выгодно. Ее можно применять для обогрева гаража, дачи или как дополнительный источник обогрева своего жилища.
Посмотрите видео
Читайте также:
Муфельная печь: особенности конструкции, собираем сами
Делаем индукционные котлы отопления своими руками
Самодельный индуктор для нагрева. Простейший индукционный нагреватель своими руками. Печь для плавки металла на сварочном инверторе
Индукционные отопительные котлы – это приборы, которые отличаются очень высоким КПД. Они позволяют заметно снизить затраты на электроэнергию по сравнению с традиционными приборами, оборудованными ТЭНами.
Модели промышленного производства недешевы. Однако сделать индукционный нагреватель своими руками сможет любой домашний мастер, владеющий нехитрым набором инструментов. Ему в помощь мы предлагаем подробное описание принципа действия и сборки эффективного обогревателя.
Индукционный нагрев невозможен без использования трех основных элементов:
Индуктор представляет собой катушку, обычно выполненную из медной проволоки, с ее помощью генерируют магнитное поле. Генератор переменного тока используют для получения высокочастотного потока из стандартного потока домашней электросети с частотой 50 Гц.
В качестве нагревательного элемента применяется металлический предмет, способный поглощать тепловую энергию под воздействием магнитного поля. Если правильно соединить эти элементы, можно получить высокопроизводительный прибор, который прекрасно подходит для подогрева жидкого теплоносителя и .
С помощью генератора электрический ток с необходимыми характеристиками подается на индуктор, т.е. на медную катушку. При прохождении через нее поток заряженных частиц формирует магнитное поле.
Принцип действия индукционных нагревателей основан на возникновении электротоков внутри проводников, появляющихся под воздействием магнитных полей
Особенность поля состоит в том, что оно обладает способностью на высоких частотах изменять направление электромагнитных волн. Если в это поле поместить какой-нибудь металлический предмет, он начнет нагреваться без непосредственного контакта с индуктором под воздействием созданных вихревых токов.
Высокочастотный электрический ток, поступающий от инвертора к индукционной катушке, создает магнитное поле с постоянно изменяющимся вектором магнитных волн. Помещенный в это поле металл быстро разогревается
Отсутствие контакта позволяет сделать потери энергии при переходе из одного вида в другой ничтожными, чем и объясняется повышенный КПД индукционных котлов.
Чтобы подогреть воду для отопительного контура, достаточно обеспечить ее контакт с металлическим нагревателем. Часто в качестве нагревательного элемента используют металлическую трубу, через которую просто пропускают поток воды. Вода попутно охлаждает нагреватель, что значительно увеличивает срок его службы.
Электромагнит индукционного прибора получают путем намотки проволоки вокруг сердечника из ферромагнита. Полученная в результате катушка индукции разогревается и передает тепло нагреваемому телу или протекающему рядом теплоносителю через теплообменник
Преимущества и недостатки прибора
“Плюсов” у вихревого индукционного нагревателя великое множество. Это простая для самостоятельного изготовления схема, повышенная надежность, высокий КПД, относительно низкие затраты на электроэнергию, длительный срок эксплуатации, малая вероятность возникновения поломок и т.п.
Производительность прибора может быть значительной, агрегаты этого типа успешно используются в металлургической промышленности.
Во время функционирования индукционного котла нагреватель слегка вибрирует. Эта вибрация стряхивает со стенок металлической трубы известковый осадок и другие возможные загрязнения, поэтому в очистке такой прибор нуждается крайне редко. Конечно, отопительную систему следует защитить от этих загрязнений с помощью механического фильтра.
Индукционная катушка нагревает металл (трубу или куски проволоки), помещенные внутри нее, с помощью высокочастотных вихревых токов, контакт не обязателен
Постоянный контакт с водой сводит к минимуму и вероятность перегорания нагревателя, что является довольно частой проблемой для традиционных котлов с ТЭНами. Несмотря на вибрацию, котел работает исключительно тихо, дополнительная шумоизоляция в месте установки прибора не понадобится.
Еще индукционные котлы хороши тем, что они практически никогда не протекают, если только монтаж системы выполнен правильно. Это очень ценное качество для , так как исключает или значительно сокращает вероятность возникновения опасных ситуаций.
Отсутствие протечек обусловлено бесконтактным способом передачи тепловой энергии нагревателю. Теплоноситель с помощью описанной выше технологии можно разогреть чуть ли не до парообразного состояния.
Это обеспечивает достаточную тепловую конвекцию, чтобы стимулировать эффективное перемещение теплоносителя по трубам. В большинстве случаев отопительную систему не придется оборудовать циркуляционным насосом, хотя все зависит от особенностей и схемы конкретной системы отопления.
Выводы и полезное видео по теме
Ролик #1. Обзор принципов индукционного нагрева:
Ролик #2. Интересный вариант изготовления индукционного нагревателя:
Для установки индукционного нагревателя не нужно получать разрешение контролирующих органов, промышленные модели таких устройств вполне безопасны, они подходят и для частного дома, и для обычной квартиры. Но владельцам самодельных агрегатов не следует забывать о технике безопасности.
Целью является практическая реализации обогрева дома с использованием техники индукционной плавки металлов. Идея, не обладает новизной и состоит в том, чтобы индуктор разместить вокруг трубы отопления. Нагревая трубу, тем самым мы нагреваем воду которая циркулирует в системе отопления. Базовой предпосылкой, которая может значительно снизить затраты на электроэнергию является колебательный контур (индуктор->конденсаторы) который работает в резонансе. Возникает повышение напряжения примерно в десятки раз, которым и осуществляется нагрев металла.
Классические индукционные схемы, как показала практика замены выходящих из строя транзисторов, требует дорогой элементной базы. За основу была взята схема индукционного нагрева использующая ZVS (zero voltage switching) метод переключения транзисторов. Схема взята с сайта http://www.rmcybernetics.com/projects/DIY_Devices/diy-induction-heater.htm.
В собранной схеме, были использованы транзисторыы STP40N10, диоды шоттки 50SQ100 5A,100В; резисторы 240 ОМ, измереенная ёмкость батареи конденсаторов CBB81/224/2000V — 2,3 мкф. Магнитная проницаемость ферритового кольца — L2, по заявлению продавца 10000, но схема запускается с ферритовым кольцом. Источниеи питания — два аккумулятора замененны на трансформатор ОСМ1-1.6 c переменным напряжением 24 вольта и постоянным на конденсаторе порядка 27 Вольт. Схема заработала сразу, каких либо настроек не протребовалось. Более или менее интересный результат при данном размере индуктора начинается от 20 вольт.
Напряжение на каждом из транзисторов относительно корпуса по 800 Вольт, не важно где мерять. Частота работы схемы без металлической трубы в индукторе, 321 Кгц, ток потребления 1,7 Ампера. При добавлении металлической трубы частота понижается до 138 Кгц, ток потребления вырастает до 5А. Труба 0,5 дюйма, индуктором с внутренним диаметром 85 мм нагревается в районе средней точки до вишневого цвета.
Лучше всего в таких схемах использовать плёночные конденсаторы фирм Evox Rifa,Faratronic,Pilcor. КПД поднимется,да и количество кондёров потребуется в разы меньше.
Ток потребления определяется заполнением индуктора металлом. Стоит использовать под бесшовную трубу с максимальной толщиной стенок. При токе потребления более 12 ампер, транзисторы STP40N10 долго не живут. Рекомендованное на сайте водяное охлаждение не используется. Греются радиатор и индуктор, конденсаторы холодные. Для охлаждения транзисторных радиаторов я использовал вентилятор от компьютера. При необходимости отвод тепла можно организовать на тот же стояк отопления.
Трансформатор тока.
Вторым, не менее, если не более интересным способом нагрева теплоносителя является трансформатор тока. Трансформатор тока представляет из себя ферритовое кольцо, установленное на проводе идущем от блока конденсаторов к индуктору. Подойдут ферритовые кольца, любой магнитопроницаемости. В том числе и кольцо из трансформаторного железа. Чем ниже магнитная проницаемость магнитопровода, тем меньший радиус кольца допустим, тем ниже частота тока на выходе, тем сильнее греется магнитопровод. В случае использования трансформаторного железа эффективность нагрева максималена. Ферритовые кольца с внутренним диаметром менее 60мм для длительной работы схемы не использовать. При малом, внутреннем, диаметре ферритового кольца, менее 50мм, резко растает ток потребления, необходимый для поддержания резонанса, транзисторы выходят из строя. В случае использования сердечника от ТВС необходим зазор, это не по феншую. В случае встречной намотки обмоток, как показано на фотографии, эдс отсутсвует.
Ниже представлена схема подключения нагрузки. Лампу 220В 95W включать без диодного моста можно, но при этом следует уменьшить число витков трансформатора тока примерно до пяти, иначе лампа эффектоно сгорит. На сдвоенную пару витков, используемых в намотке обращать внимание не стоит. Так же следует поступить с парой проводов черный и красный, на транзисторных радиаторах к ним подключались высоковольтные конденсаторы от СВЧ печей. Конденсаторы сильно грелись, пришлось их заменить, провода пусть пока будут.
Ферритовые кольца размещенные в индукторе увеличивают частоту до 400 кГц, токовый трансформатор ее понижает до 100 кГц. Яркость свечения лампы регулируется частотой за счет увеличения либо уменьшения сердечника из ферритовых колец в индукторе.
На тестере видно, что при подключении нагрузки ток вырос на два ампера. (В первом случае ток необходимо умножить на 100) Это примерно равно мощности используемой лампы. Безвомездного съема энергии с токового трансформатора нет. Подключение активной нагрузки увеличивает ток потребляемый устройством. А вот использовать ферритовые кольца для нагрева теплоносителя в дополнение к индуктору — очень интересный вариант.
Дуговой разряд.
На каждые три-четыре витка токового трансформатора приходится 1000 вольт. Попытка замера напряжения на большем числе витков закончилась неудачей по причине выхода из строя тестера. Можно предположить, что напряжение на токовом рансформаторе около пяти-шести тысяч вольт, поэтому третьим источником тепла, в предлагаемой схеме является дуговой разряд. Как его еспользовать для нагрева теплоносителя, я пока не решил. Плавится все с чем дуговой разряд находится в тесном контакте.
Промежуточный итог.
1. Осуществлять нагрев трубы отопления токами фуко.
2. Дополнительная тепловая мощность за счет охлаждения радиаторов, на которых установлены транзисторы.
3. Охлаждения феррита токового трансформатора теплоносителем (водой).
4. Использование дугового разряда — проблематично. Очень высокая температура. Но очень перспективно. Наличие дуги не увеличивает потребление тока устройством.
Пример страниц руководства:
Скачать руководство полностью:
Индукционный нагреватель — это высокая стадия эволюции электроприборов. Благодаря такому устройству можно значительно экономить потребление энергии. Тепловой генератор, используемый в этом приборе, совершенно безвреден, при работе не выделяет копоти. Например, по эффективности отопительный котел (схема индукционного нагревателя приведена ниже) уступает лишь инфракрасному обогревателю. Однако в отличие от ИК-приборов, которые продаются лишь в специализированных магазинах, индукционные нагреватели можно не только купить, но и собрать своими руками.
Такие устройства бывают нескольких уровней сложности и назначения, например, для воды и металла. Их устройства, конечно, отличаются, однако принцип работы идентичный. На фото ниже изображена схема индукционного нагревателя металла, по ней достаточно легко собрать данный прибор.
Итак, в этой статье мы рассмотрим процесс сборки индукционного нагревателя из подручных средств, которые можно найти в «закромах» любого домашнего мастера.
Как работает индукционный нагреватель, сделанный своими руками?
Принцип работы самодельного нагревателя ничем не отличается от заводского прибора. То есть теплоноситель циркулирует в сердечнике, нагреваясь от его стенок или содержимого. Он разогревается благодаря вихревым токам, генерируемым обмоткой.
Важно : полимерные сердечники набивают рубленой проволокой!
В свою очередь, обмотка накручивается на тело сердечника и замыкается на источник тока высокой частоты. Именно такая энергия способна сгенерировать переменное электромагнитное поле — первопричину появления вихревых токов в неподвижном сердечнике (или его наполнителе).
Схема индукционного нагревателя воды, представленная ниже, часто используется в отопительных котлах.
В роли источника высокочастотного переменного тока может выступать обычный или более сложная система на основе трансформатора и частотного преобразователя.
Необходимо отметить, что при правильном подходе к выбору источника и формированию обмотки можно создать действительно эффективный прибор, который будет работать не хуже заводского аналога. Кстати, в его комплекте всегда есть инструкция и схема индукционного нагревателя.
Своими руками собираем индукционный прибор: важные детали
Для сбора такого нагревателя понадобятся:
Именно этот прибор будет источником переменного электрического тока высокой частоты, питающего индуктор.
После этого необходимо взять Намотать ее пружиной на корпус сердечника. Это устройство будет выполнять роль индуктора. Очень важно контакты проволоки соединить с клеммами инвертора, избегая спаек и скруток. Исходя из этого, отрезок данного материала, используемый для формирования сердечника, должен иметь достаточную длину. Количество витков обычно равно 50, а диаметр проволоки, как правило, равен 3 мм. Схема индукционного нагревателя показывает последовательность соединения отдельных составляющих.
Делаем сердечник
В роли сердечника выступает обычная полимерная труба, изготовленная из сшитого полиэтилена или полипропилена. Эти сорта пластмасс выдерживают максимально высокую температуру. Пропускной диаметр трубы-сердечника должен равняться 50 мм, а толщина стенок не может быть меньше 2,5-3 мм. Тогда эту деталь можно использовать в роли калибра, на который навивают медную проволоку, формируя индуктор.
Приблизительная схема индукционного нагревателя отображена на этой картинке.
Нагревательным элементом такого котла будет наполнитель полимерного сердечника — рубленые отрезки диаметром 7 мм. Причем длина их не может быть менее 5 см.
Сборка устройства на примере отопительного индукционного котла
Сам процесс сборки всех этих компонентов в единую систему выглядит следующим образом:
- Вначале берете отрезок полимерной трубы, фиксируете его и наматываете поверх будущего сердечника 50 витков 3-миллиметровой медной проволоки.
- Далее обрезаете торцы сердечника, оставляя по 7-10 см от края проволоки на отводы.
Важно : Схема индукционного нагревателя своими руками выполняется в несколько этапов, последовательность которых нарушать ни в коем случае нельзя. Во избежание ошибок необходимо в точности следовать инструкции.
Изготавливая индукционный нагреватель собственными руками, необходимо побеспокоиться о безопасности устройства. Для этого требуется руководствоваться следующими правилами, повышающими уровень надежности общей системы:
- В верхний тройник стоит врезать предохранительный клапан, стравливающий лишнее давление.
Иначе при выходе из строя циркуляционного насоса сердечник попросту лопнет под воздействием пара. Как правило, схема простого индукционного нагревателя предусматривает такие моменты.
- Инвертор включается в сеть только через УЗО. Это устройство срабатывает в критических ситуациях и поможет избежать короткого замыкания.
- Сварочный инвертор нужно заземлить, выводя кабель на особый металлический контур, смонтированный в грунте за стенами сооружения.
- Корпус индукционного нагревателя нужно размещать на высоте 80 см над уровнем пола. Причем расстояние до потолка должно быть не менее 70 см, а до других предметов меблировки — более 30 см.
- Индукционный нагреватель — это источник очень сильного электромагнитного поля, поэтому такую установку нужно держать подальше от жилых помещений и вольеров с домашними животными.
Подведение итогов
Индукционный нагреватель, изготовленный своими руками, будет работать не хуже заводского прибора. Он не уступает в производительности, эффективности и безопасности, конечно же, если были соблюдены все правила.
Умельцы придумали много способов для отопления дома. Один из них — индукционный нагреватель. Как и любой другой, он имеет свои преимущества и недостатки.
Принцип действия
В основе работы лежит закон Джоуля-Ленца, который отражает прямую зависимость тепловой отдачи проводника от напряженности электрического поля. Всем известна взаимосвязь магнетизма и электричества, которые просто не могут существовать одно без другого. Если на катушку подать ток высокой частоты, вокруг нее образуется магнитное поле. Его поток будет пронизывать токопроводящий сердечник, вставленный в катушку. Возникшая магнитная индукция будет постоянно меняться по направлению и времени, что вызовет появление вихревых токов, движущихся по замкнутому кругу. А это преобразовывает электромагнитную энергию в тепловую. Такова в общих чертах схема индукционного нагревателя.
Индукционные нагреватели блестяще зарекомендовали себя в самых разных областях применения. С их помощью можно проводить поверхностную закалку металлических изделий, сверхчистую, бесконтактную сварку, точечный прогрев и даже плавку токопроводящих материалов. Производственные индукторы оборудованы мощным трансформатором, способным подавать на них большие токи.
Индуктор в быту
Поскольку схема подобного нагревателя не отличается сложностью, а КПД такого устройства очень высок (до 98%), вихревой индукционный нагреватель не мог не заинтересовать народных умельцев.
Очень часто у многих возникает идея об использовании принципа индукции для отопления дома. Ведь индукционный обогреватель способен нагревать воду чуть ли не мгновенно. Поэтому существует целый ряд конструкций, представляющих собой самодельный индукционный нагреватель.
В физике много законов, обойти которые не получится никогда. Энергия не берется из ниоткуда, а потому количество потребляемого электричества не может быть меньше, чем требуется тепловой энергии.
Другими словами, если для прогрева помещения требуется 5 кВт/ч, то не получится сделать это, потребляя всего 2 кВт/ч электроэнергии, какой бы замечательной ни была конструкция нагревателя. Если планируется отапливаться с помощью индуктора, нужно быть готовым к повышению выплат за электричество.
Самым популярным вариантом среди мастеров-умельцев является индукционный нагреватель из сварочного инвертора. Этому есть ряд причин:
- Инвертор выдает ток повышенных частот, что значительно повышает напряженность электрического поля, а это благотворно сказывается на теплоотдаче.
- Сварочный инвертор способен на подачу больших токов. Из всех приборов, доступных для бытового применения, инвертор лучше всего подходит для использования в качестве блока питания индукционного нагревателя.
Элементы конструкции
Индукционный нагреватель своими руками делается следующим образом:
- Кусок пластиковой трубы с толщиной стенок не менее 3 мм заполняется кусками металлической проволоки. Длина их примерно около 5 см.
- Оба края этого отрезка трубы закрываются металлической сеткой, чтобы она удерживала эти куски на месте. Труба должна быть заполнена проволокой полностью.
- После этого она должна быть аккуратно обмотана толстым медным проводом — порядка 90 витков. Желательно выбирать провод с диаметром не ниже 3 мм.
- С помощью переходников и фитингов труба присоединяется к отопительной системе, которая после этого заполняется водой.
- Концы провода присоединяются к клеммам сварочного инвертора.
- Необходимо обеспечить выполнение всех мер пожарной и электробезопасности.
После включения устройства металлические куски проволоки мгновенно нагреются и начнут отдавать тепло проходящей свозь них воде.
Особо стоит заострить внимание на том, что вода обязательно должна непрерывно циркулировать.
В противном случае температура трубы поднимется настолько, что появится угроза ее расплавления
Это является 1 из самых серьезных недостатков подобных нагревателей. В случае частого отсутствия хозяев необходима система автоматического компьютерного контроля за работой нагревателя.
Индукционный нагреватель вполне пригоден для отопления, но при этом имеет свои недостатки. Они вполне исправимы и при грамотной проработке деталей данная конструкция способна конкурировать с другими.
Индукционный нагрев (Induction Heating) — метод бесконтактного нагрева токами высокой частоты (англ. RFH — radio-frequency heating, нагрев волнами радиочастотного диапазона) электропроводящих материалов.
Описание метода.
Индукционный нагрев — это нагревание материалов электрическими токами, которые индуцируются переменным магнитным полем. Следовательно — это нагрев изделий из проводящих материалов (проводников) магнитным полем индукторов (источников переменного магнитного поля). Индукционный нагрев проводится следующим образом. Электропроводящая (металлическая, графитовая) заготовка помещается в так называемый индуктор, представляющий собой один или несколько витков провода (чаще всего медного). В индукторе с помощью специального генератора наводятся мощные токи различной частоты (от десятка Гц до нескольких МГц), в результате чего вокруг индуктора возникает электромагнитное поле. Электромагнитное поле наводит в заготовке вихревые токи. Вихревые токи разогревают заготовку под действием джоулева тепла (см. закон Джоуля-Ленца).
Система «индуктор-заготовка» представляет собой бессердечниковый трансформатор, в котором индуктор является первичной обмоткой. Заготовка является вторичной обмоткой, замкнутой накоротко. Магнитный поток между обмотками замыкается по воздуху.
На высокой частоте вихревые токи вытесняются образованным ими же магнитным полем в тонкие поверхностные слои заготовки Δ (Поверхностный-эффект), в результате чего их плотность резко возрастает, и заготовка разогревается. Нижерасположенные слои металла прогреваются за счёт теплопроводности. Важен не ток, а большая плотность тока. В скин-слое Δ плотность тока уменьшается в e раз относительно плотности тока на поверхности заготовки, при этом в скин-слое выделяется 86,4 % тепла (от общего тепловыделения. Глубина скин-слоя зависит от частоты излучения: чем выше частота, тем тоньше скин-слой. Также она зависит от относительной магнитной проницаемости μ материала заготовки.
Для железа, кобальта, никеля и магнитных сплавов при температуре ниже точки Кюри μ имеет величину от нескольких сотен до десятков тысяч. Для остальных материалов (расплавы, цветные металлы, жидкие легкоплавкие эвтектики, графит, электролиты, электропроводящая керамика и т. д.) μ примерно равна единице.
Например, при частоте 2 МГц глубина скин-слоя для меди около 0,25 мм, для железа ≈ 0,001 мм.
Индуктор сильно нагревается во время работы, так как сам поглощает собственное излучение. К тому же он поглощает тепловое излучение от раскалённой заготовки. Делают индукторы из медных трубок, охлаждаемых водой. Вода подаётся отсасыванием — этим обеспечивается безопасность в случае прожога или иной разгерметизации индуктора.
Применение:
Сверхчистая бесконтактная плавка, пайка и сварка металла.
Получение опытных образцов сплавов.
Гибка и термообработка деталей машин.
Ювелирное дело.
Обработка мелких деталей, которые могут повредиться при газопламенном или дуговом нагреве.
Поверхностная закалка.
Закалка и термообработка деталей сложной формы.
Обеззараживание медицинского инструмента.
Преимущества.
Высокоскоростной разогрев или плавление любого электропроводящего материала.
Возможен нагрев в атмосфере защитного газа, в окислительной (или восстановительной) среде, в непроводящей жидкости, в вакууме.
Нагрев через стенки защитной камеры, изготовленной из стекла, цемента, пластмасс, дерева — эти материалы очень слабо поглощают электромагнитное излучение и остаются холодными при работе установки. Нагревается только электропроводящий материал — металл (в том числе расплавленный), углерод, проводящая керамика, электролиты, жидкие металлы и т. п.
За счёт возникающих МГД усилий происходит интенсивное перемешивание жидкого металла, вплоть до удержания его в подвешенном состоянии в воздухе или защитном газе — так получают сверхчистые сплавы в небольших количествах (левитационная плавка, плавка в электромагнитном тигле).
Поскольку разогрев ведётся посредством электромагнитного излучения, отсутствует загрязнение заготовки продуктами горения факела в случае газопламенного нагрева, или материалом электрода в случае дугового нагрева. Помещение образцов в атмосферу инертного газа и высокая скорость нагрева позволят ликвидировать окалинообразование.
Удобство эксплуатации за счёт небольшого размера индуктора.
Индуктор можно изготовить особой формы — это позволит равномерно прогревать по всей поверхности детали сложной конфигурации, не приводя к их короблению или локальному непрогреву.
Легко провести местный и избирательный нагрев.
Так как наиболее интенсивно разогрев идет в тонких верхних слоях заготовки, а нижележащие слои прогреваются более мягко за счёт теплопроводности, метод является идеальным для проведения поверхностной закалки деталей (сердцевина при этом остаётся вязкой).
Лёгкая автоматизация оборудования — циклов нагрева и охлаждения, регулировка и удерживание температуры, подача и съём заготовок.
Установки индукционного нагрева:
На установках с рабочей частотой до 300 кГц используют инверторы на IGBT-сборках или MOSFET-транзисторах. Такие установки предназначены для разогрева крупных деталей. Для разогрева мелких деталей используются высокие частоты (до 5 МГц, диапазон средних и коротких волн), установки высокой частоты строятся на электронных лампах.
Также для разогрева мелких деталей строятся установки повышенной частоты на MOSFET-транзисторах на рабочие частоты до 1,7 МГц. Управление транзисторами и их защита на повышенных частотах представляет определённые трудности, поэтому установки повышенной частоты пока ещё достаточно дороги.
Индуктор для нагрева мелких деталей имеет небольшие размеры и небольшую индуктивность, что приводит к уменьшению добротности рабочего колебательного контура на низких частотах и снижению КПД, а также представляет опасность для задающего генератора (добротность колебательного контура пропорциональна L/C, колебательный контур с низкой добротностью слишком хорошо «накачивается» энергией, образует короткое замыкание по индуктору и выводит из строя задающий генератор). Для повышения добротности колебательного контура используют два пути:
— повышение рабочей частоты, что приводит к усложнению и удорожанию установки;
— применение ферромагнитных вставок в индукторе; обклеивание индуктора панельками из ферромагнитного материала.
Так как наиболее эффективно индуктор работает на высоких частотах, промышленное применение индукционный нагрев получил после разработки и начала производства мощных генераторных ламп. До первой мировой войны индукционный нагрев имел ограниченное применение. В качестве генераторов тогда использовали машинные генераторы повышенной частоты (работы В. П. Вологдина) или искровые разрядные установки.
Схема генератора может быть в принципе любой (мультивибратор, RC-генератор, генератор с независимым возбуждением, различные релаксационные генераторы), работающей на нагрузку в виде катушки-индуктора и обладающей достаточной мощностью. Необходимо также, чтобы частота колебаний была достаточно высока.
Например, чтобы «перерезать» за несколько секунд стальную проволоку диаметром 4 мм, необходима колебательная мощность не менее 2 кВт при частоте не менее 300 кГц.
Выбирают схему по следующим критериям: надёжность; стабильность колебаний; стабильность выделяемой в заготовке мощности; простота изготовления; удобство настройки; минимальное количество деталей для уменьшения стоимости; применение деталей, в сумме дающих уменьшение массы и габаритов, и др.
На протяжении многих десятилетий в качестве генератора высокочастотных колебаний применялась индуктивная трёхточка (генератор Хартли, генератор с автотрансформаторной обратной связью, схема на индуктивном делителе контурного напряжения). Это самовозбуждающаяся схема параллельного питания анода и частотно-избирательной цепью, выполненной на колебательном контуре. Она успешно использовалась и продолжает использоваться в лабораториях, ювелирных мастерских, на промышленных предприятиях, а также в любительской практике. К примеру, во время второй мировой войны на таких установках проводили поверхностную закалку катков танка Т-34.
Недостатки трёх точки:
Низкий кпд (менее 40 % при применении лампы).
Сильное отклонение частоты в момент нагрева заготовок из магнитных материалов выше точки Кюри (≈700С) (изменяется μ), что изменяет глубину скин-слоя и непредсказуемо изменяет режим термообработки. При термообработке ответственных деталей это может быть недопустимо. Также мощные твч-установки должны работать в узком диапазоне разрешённых Россвязьохранкультурой частот, поскольку при плохом экранировании являются фактически радиопередатчиками и могут оказывать помехи телерадиовещанию, береговым и спасательным службам.
При смене заготовок (например, более мелкой на более крупную) изменяется индуктивность системы индуктор-заготовка, что также приводит к изменению частоты и глубины скин-слоя.
При смене одновитковых индукторов на многовитковые, на более крупные или более малогабаритные частота также изменяется.
Под руководством Бабата, Лозинского и других учёных были разработаны двух- и трёхконтурные схемы генераторов, имеющих более высокий кпд (до 70 %), а также лучше удерживающие рабочую частоту. Принцип их действия состоит в следующем. За счёт применения связанных контуров и ослабления связи между ними, изменение индуктивности рабочего контура не влечёт сильного изменения частоты частотозадающего контура. По такому же принципу конструируются радиопередатчики.
Современные твч-генераторы — это инверторы на IGBT-сборках или мощных MOSFET-транзисторах, обычно выполненные по схеме мост или полумост. Работают на частотах до 500 кГц. Затворы транзисторов открываются с помощью микроконтроллерной системы управления. Система управления в зависимости от поставленной задачи позволяет автоматически удерживать
А) постоянную частоту
б) постоянную мощность, выделяемую в заготовке
в) максимально высокий КПД.
Например, при нагреве магнитного материала выше точки Кюри толщина скин-слоя резко увеличивается, плотность тока падает, и заготовка начинает греться хуже. Также пропадают магнитные свойства материала и прекращается процесс перемагничивания — заготовка начинает греться хуже, сопротивление нагрузки скачкообразно уменьшается — это может привести к «разносу» генератора и выходу его из строя. Система управления отслеживает переход через точку Кюри и автоматически повышает частоту при скачкообразном уменьшении нагрузки (либо уменьшает мощность).
Замечания.
Индуктор по возможности необходимо располагать как можно ближе к заготовке. Это не только увеличивает плотность электромагнитного поля вблизи заготовки (пропорционально квадрату расстояния), но и увеличивает коэффициент мощности Cos(φ).
Увеличение частоты резко уменьшает коэффициент мощности (пропорционально кубу частоты).
При нагреве магнитных материалов дополнительное тепло также выделяется за счет перемагничивания, их нагрев до точки Кюри идет намного эффективнее.
При расчёте индуктора необходимо учитывать индуктивность подводящих к индуктору шин, которая может быть намного больше индуктивности самого индуктора (если индуктор выполнен в виде одного витка небольшого диаметра или даже части витка — дуги).
Имеются два случая резонанса в колебательных контурах: резонанс напряжений и резонанс токов.
Параллельный колебательный контур – резонанс токов.
В этом случае на катушке и на конденсаторе напряжение такое же, как у генератора. При резонансе, сопротивление контура между точками разветвления становится максимальным, а ток (I общ) через сопротивление нагрузки Rн будет минимальным (ток внутри контура I-1л и I-2с больше чем ток генератора).
В идеальном случае полное сопротивление контура равно бесконечности — схема не потребляет тока от источника. При изменение частоты генератора в любую сторону от резонансной частоты полное сопротивление контура уменьшается и линейный ток (I общ) возрастает.
Последовательный колебательный контур – резонанс напряжений.
Главной чертой последовательного резонансного контура является то, что его полное сопротивление минимально при резонансе. (ZL + ZC – минимум). При настройке частоты на величину, превышающую или лежащую ниже резонансной частоты, полное сопротивление возрастает.
Вывод:
В параллельном контуре при резонансе ток через выводы контура равен 0, а напряжение максимально.
В последовательном контуре наоборот — напряжение стремится к нулю, а ток максимален.
Статья взята с сайта http://dic.academic.ru/ и переработана в более понятный для читателя текст, компанией ООО «Проминдуктор».
Простой индукционный нагреватель своими руками
Приветствую, радиолюбители-самоделкины!Сейчас на кухнях довольно часто можно встретить новый тип варочных плит — индукционные. В отличие от газовых и простых электрических, в них не нагревается конфорка, не горит с высокой температурой газ, ведь электрическая энергия в таких плитах поступает «напрямую» к разогреваемой посуде, не нагревая ненужные посторонние части плиты. Работает это следующим образом — специальный индуктор создаёт в толще металла посуды сильные вихревые токи, которые и разогревают металл. Помимо кухонных плит, такая технология используется в разных областях промышленности для нагрева и плавки металла. Возможно, на первый взгляд индукционный нагрев выглядит сложно и очень труднореализуемо в домашних условиях, но на самом деле, схема простого индукционного нагревателя не содержит дорогих либо редких деталей, собрать её под силу каждому радиолюбителю. Мощность такой схемы достаточна для того, чтобы раскалить до красна небольшие металлический предметы — лезвия канцелярского ножа, отвёртки, гвозди.
На самом деле, данная схема является довольно универсальной, на её основе также строят различные высоковольтные генераторы и прочие устройства, где требуется генерация высокочастотных импульсов.

Резисторы номиналами 220 Ом должны быть рассчитаны на мощность как минимум в 1 ватт, иначе возможен их чрезмерный нагрев. После этих резисторов на схеме можно увидеть стабилитроны, имеющими маркировку на схеме «15 v».
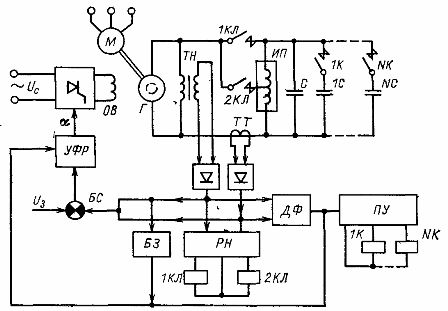
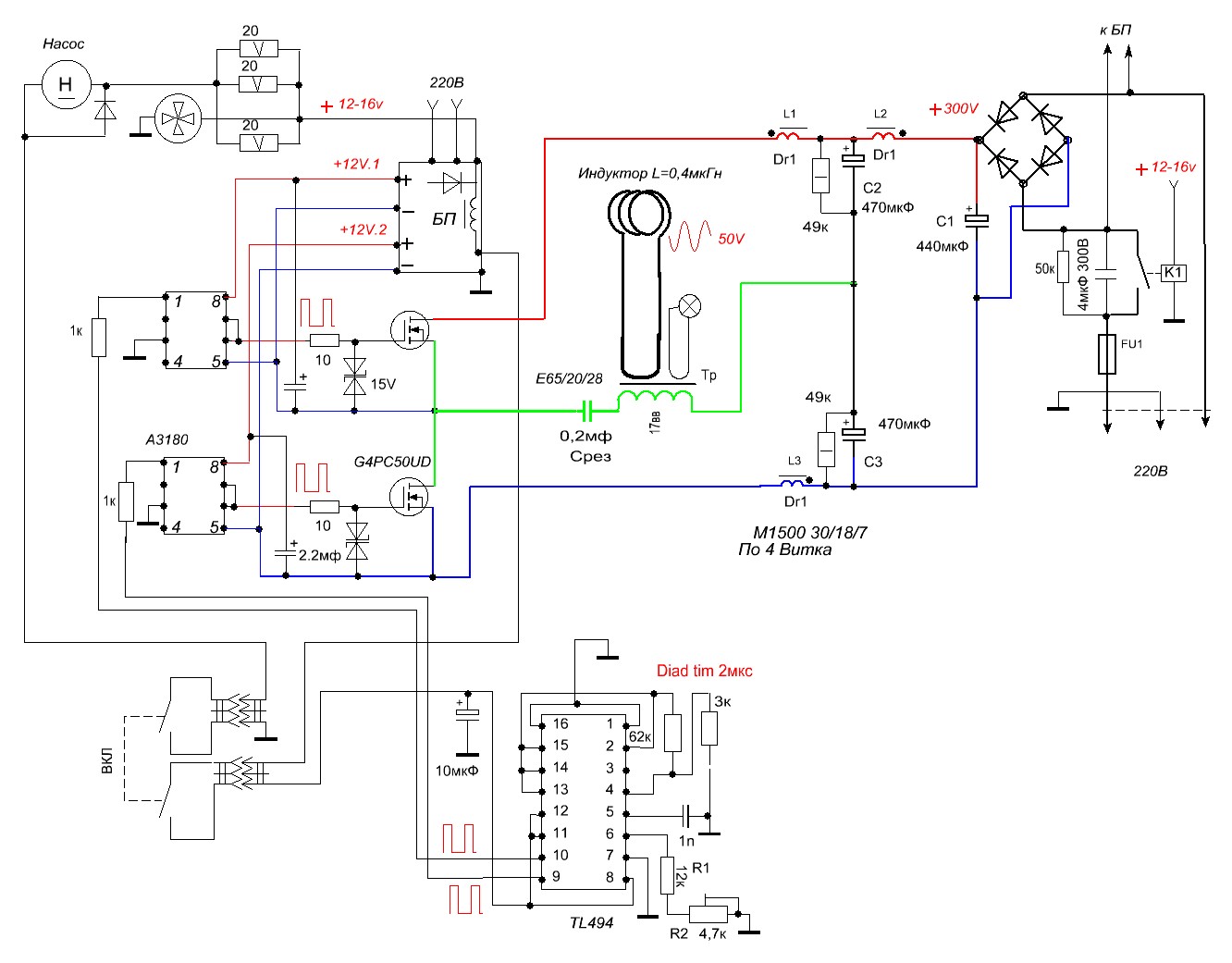
Колебательный контур C1 L2, пожалуй, самая важная часть схемы — именно эти элементы задают частоту колебания схемы. Катушка L2 — непосредственно сам индуктор, катушка большого размера из толстого медного провода, внутрь которой помещается нагреваемый предмет. Её диаметр может составлять от 1 до 5 см, в зависимости от размеров предмета, который нужно будет разогревать. Следует также учитывать, что чем больше будет размер катушки относительно размера нагреваемого объекта — тем менее эффективной будет работа данной схемы. В идеальном случае объект должен помещаться в катушку, не оставляя больших зазоров по краям, до витков.

Через конденсатор С1 в данной схеме будут протекать довольно значительные токи, а потому необходимо использовать неполярные плёночные конденсаторы и низким внутренним сопротивлением (ESR). Ёмкость С1 может варьироваться в пределах 0,68 — 1 мкФ, её можно будет подбирать для достижения наилучшей эффективности работы схемы, оценивая скорость нагрева. Для того, чтобы снизить внутреннее сопротивление С1, можно включить параллельно несколько конденсаторов — это наиболее предпочтительный вариант. Например, 6-10 конденсаторов по 0,1 мкФ каждый дадут как раз нужную ёмкость, а внутреннее сопротивление такой батареи конденсаторов будет значительно меньше, чем у одного конденсатора.
Ниже представлены осциллограммы в разных частях схемы.
На затворе транзистора:
Сток-исток транзистора:
На самой катушке индуктора:
Можно увидеть, что амплитура на катушке индуктора составляет около 70 вольт, и это при том, что напряжение питания схемы составляет всего 11В.
Преимуществом данной схемы является её простота — для сборки даже не обязательно изготавливать печатную плату. Смонтировать все элементы можно прямо на выводах индуктора, если он выполнен из жёсткого провода, то и конструкция будет обладать нужной жёсткостью и надёжностью. Батарея конденсаторов припаивается прямо на толстые выводы.
Ещё одним преимуществом данной схемы является её большой КПД — практически вся мощность, потребляемая от источника, уходит в нагрев объекта, а потому транзисторы нагреваются лишь слегка и не требуют массивных радиаторов. Тестовый запуск схемы можно проводить и вовсе без радиаторов, но для долговременной работы они обязательны. Также следует заметить, что ток потребления в этой схеме большой лишь во время нагрева — когда внутрь катушки-индуктора помещён металлический объект. На холостом же ходе схема потребляет небольшой ток, максимум несколько сотен миллиампер. Ниже представлено несколько фотографий раскалённого лезвия ножа, нагретого таким индукционным нагревателем. Удачной сборки!
Источник (Source) Становитесь автором сайта, публикуйте собственные статьи, описания самоделок с оплатой за текст. Подробнее здесь.
Индукционная печь своими руками, принцип работы и сборка
Очень сложно бывает найти подходящую работу и дело, которое будет вам по душе, подобрать подходящие вакансии в море можно перейдя по ссылке.
Как собирается индукционная печь своими руками. Устройство и принцип работы. Важные параметры индукционных печей.
Расплавить небольшой кусок железа можно в самостоятельно собранной индукционной печи. Это самое эффективное устройство, которое работает от домашней розетки 220В. Печь пригодится в гараже или мастерской, где она может размещаться просто на рабочем столе. Нет смысла покупать ее, так как индукционная печь своими руками собирается за пару часов, если человек умеет читать электрические схемы. Без схемы обходиться нежелательно, ведь она дает полное представление об устройстве и позволяет избежать ошибок при подключении.
Принцип работы индукционной печи
Самодельная индукционная печь для плавки небольшого количества металла не требует больших габаритов и такого сложного устройства, как промышленные агрегаты. Ее работа основана на выработке тока переменным магнитным полем. Металл расплавляется в специальной заготовке, называемой тигелем и помещаемой в индуктор. Он представляет собой спираль с небольшим количеством витков из проводника, например, медной трубки. Если устройство используется в течение короткого времени, проводник не будет перегреваться. В таких случаях достаточно использовать медную проволоку.
Специальный генератор запускает в эту спираль (индуктор) мощные токи, а вокруг нее создается электромагнитное поле. Это поле в тигле и в помещенном в него металле создает вихревые токи. Именно они разогревают тигель и расплавляют металл за счет того, что он поглощает их. Следует отметить, что процессы происходят очень быстро, если использовать тигель из неметалла, например, шамота, графита, кварцита. Самодельная печь для плавки предусматривает выемную конструкцию тигеля, то есть, в него помещают металл, а после нагрева или плавки его вытаскивают из индуктора.
Схема индукционной печи
Генератор высокой частоты собирают из 4-х электронных ламп (тетродов), которые соединяются между собой параллельно. Скорость нагрева индуктора регулируется конденсатором переменной емкости. Его ручка выводится наружу и позволяет регулировать емкость конденсатора. Максимальное значение обеспечит нагрев куска металла в катушке всего за несколько секунд до красного состояния.
Параметры индукционной печи
Эффективная работа данного устройства зависит от следующих параметров:
- мощность и частота генератора,
- количество потерь в вихревых токах,
- скорость потерь тепла и количество этих потерь в окружающий воздух.
Как подобрать составляющие детали схемы, чтобы получить для плавки в мастерской достаточные условия? Частота генератора задана заранее: она должна составить 27,12 МГц, если устройство собирают своими руками для использования в домашней мастерской. Катушку делают из тонкой медной трубки или провода, ПЭВ 0,8. Достаточно сделать не более 10 витков.
Электронные лампы следует использовать большой мощности, например, марки 6п3с. Также схема предусматривает установку дополнительной неоновой лампы. Она будет служить индикатором готовности устройства. Схема также предусматривает применение керамических конденсаторов (от 1500В) и дросселей. Подключение к домашней розетке осуществляется через выпрямитель.
Внешне самодельная индукционная печь выглядит так: к небольшой подставке на ножках прикрепляется генератор со всеми деталями схемы. К нему подключается индуктор (спираль). Следует отметить, что данный вариант сборки самодельного устройства для плавки применим для работы с небольшим объемом металла. Индуктор в виде спирали изготавливается проще всего, поэтому для самодельного устройства он используется именно в таком виде.
Особенности эксплуатации индуктора
Однако существует много разных модификаций индуктора. Например, он может изготавливаться в форме восьмерки, трилистника или иметь любую другую форму. Она должна быть удобной для размещения материала для термообработки. Например, плоскую поверхность легче всего нагреть виткам, расположенными в виде змейки.
Кроме этого ему свойственно прожигаться, и чтобы продлить время службы индуктора, его можно изолировать жаропрочным материалом. Используют, например, заливку огнеупорной смесью. Следует отметить, что данное устройство не ограничивается лишь медным материалом провода. Также можно применить стальной провод или из михрома. При работе с индукционной печью следует учесть ее термическую опасность. При случайном касании кожа получает сильный ожог.
требуемая схема и принцип работы,
В настоящее время в быту стали использоваться печи, работающие по индукционному принципу, которые обычно применяются в промышленности.
Принцип работы индукционной печи
Работа такой печи основана на принципе индукционного нагрева. Другими словами, тепловая энергия получается от электрического тока, вырабатываемого электромагнитным полем. Благодаря такой особенности этот прибор отличается от обыкновенных электрообогревателей.Конструкция индуктора довольно проста. Его центром является графитовая или металлическая электропроводящая заготовка, вокруг которой следует намотать провод. При помощи мощности генератора в индуктор начинают запускать токи разной частоты, создавая вокруг индуктора мощное электромагнитное поле. Благодаря воздействию такого поля на заготовку и создания в ней вихревых токов, графит или металл начинает очень сильно разогреваться и отдавать тепло окружающему воздуху.
В быту индукторы стали использоваться сравнительно недавно.
Виды индукционных устройств
По своему предназначению такие приборы бывают бытовыми и промышленными. Однако такая классификация считается неполной. Существует еще несколько разновидностей печей:
- Тигельные. Самый распространенный вид агрегатов, используемых в металлургии. Такая конструкция не содержит сердечник. Эти устройства в основном используются для обработки и плавки любых металлов. Замечательно зарекомендовали себя они и в других областях.
- Канальные. Их конструкция имеет сходство с трансформатором.
- Вакуумные. Применяются тогда, когда необходимо удалить примеси из металла.
Бытовые печи делятся на две группы:
- Агрегаты, которые используют для отопления. Представляют собой индукционные котельные установки небольшого размера, которые монтируются в системах автономного отопления.
- Индукционные плиты, на которых готовят пищу.
Основное отличие от обыкновенной электроплиты – экономное расходование электроэнергии.
Можно ли изготовить индукционную печь, предназначенную для плавки металлов, своими руками? Хотя она и является, с одной стороны, сложным оборудованием, а с другой – благодаря относительной простоте и понятности принципа работы появляется возможность сделать индукционный нагревательный прибор своими руками. Кроме того, многие специалисты, обладающие необходимыми знаниями и навыками, способны создать качественные агрегаты из обычных материалов. Чтобы сделать индукционную печь своими руками, будет нужна схема и хорошее знание физики.
Индукционные печи своими руками в основном используются для обогрева помещений. Тигельные конструкции небольшого размера лучше всего подойдут для плавки металлов в небольших объемах, например, при изготовлении бижутерии или ювелирных украшений. Индукционные плиты считаются замечательным решением для дачных домиков. А в городской квартире их используют как дополнительный обогреватель, если произошел какой-либо сбой в центральной системе отопления.
Схема индукционной печи
Схема такого простого индукционного нагревателя необходима будет для выполнения работ. Можно работать и без нее, но нежелательно, так как такой нагреватель является сложным электрооборудованием. Его конструкция и внутреннее содержимое разрабатывается заранее. Схема объединяет все задумки мастера в единое целое. Если потребуется спроектировать плиту, а не простой нагреватель, без схемы вообще не получится обойтись.Конструкция индукционной печи своими руками достаточно проста: нагревательный элемент, общий корпус, индуктор. Если агрегат потребуется для обработки материалов, следует дополнительно спроектировать плавильную камеру. Сердцем индукционной печи является заготовка, проводящая ток, способная разогреваться до высоких температур. С такой задачей замечательно справляются нихромовая спираль или графитовые щетки. Выбирая между ними, следует ориентироваться на те задачи, которые стоят перед нагревателем. Для плавильной печи лучшим вариантом будет использование графитовых щеток, для нагревательного прибора – нихромовой спирали. Использование нихрома дает возможность подключить агрегат к обычной электросети.
Как сделать индукционную печь своими руками
Для создания эффективного агрегата необходимо учитывать следующие параметры:
- частота и мощность генератора;
- скорость, с которой теряется тепло;
- количество потерь в вихревых токах.
Сначала необходимо правильно подобрать все необходимые детали схемы для получения достаточных условий для плавки в мастерской. Если агрегат собирают своими руками, частота генератора должна составлять 27,12 МГц. Катушку следует делать из провода или тонкой медной трубки, при этом не должно быть больше 10 витков.
Мощность электронных ламп должна быть большая. Схема предусматривает установку неоновой лампы, которая будет использоваться в качестве индикатора готовности устройства. В схеме также предусмотрено применение дросселей и керамических конденсаторов. К домашней розетке подключение осуществляется через выпрямитель.
Индукционная печь, изготовленная своими руками, выглядит следующим образом: небольшая подставка на ножках, к которой крепится генератор со всеми необходимыми деталями схемы. А уже к генератору подключается индуктор.
Преимущества и недостатки индукционных печей
Индукционные агрегаты могут иметь различную мощность и зависит это от особенностей конструкции. Своими руками собрать устройство промышленной частоты очень непросто, да и в этом нет необходимости. Лучше стоит их купить.
Индукционные печи могут иметь как плюсы, так и минусы:
- они очень надежные;
- гораздо экономичнее обыкновенных электронагревателей;
- их используют не только для обогрева, но и подключают к водяному контуру;
- устанавливать их можно в квартире или доме, не оборудуя для этого специальное помещение;
- такую печь используют не только в качестве основного котла в автономной сети отопления, но и в сочетании с другими тепловыми источниками;
- такие устройства очень просто эксплуатировать, при этом не требуется периодическое сервисное обслуживание;
- основным недостатком индукционной печи является ее высокая пожароопасность, поэтому это качество следует учитывать при установке ее в жилом помещении.
Безопасность
Работая с печью, следует опасаться получения термических ожогов. Кроме того, такое устройство имеет высокую пожарную опасность. Во время работы эти агрегаты ни в коем случае нельзя перемещать. Нужно быть очень внимательным, когда такие печи устанавливают в квартире.
Переменное электромагнитное поле начинает разогревать окружающее его помещение, и такая особенность находится в прямой зависимости от мощности и частоты излучения устройства. Мощные промышленные печи могут оказывать воздействие на предметы, находящиеся в карманах одежды, на близлежащие детали из металла, на ткани людей.
Заключение
Индукционную печь можно изготовить самостоятельно, но это не всегда целесообразно. Лучше не браться за такую работу, если нет совершенно никаких знаний в области электрооборудования и физики. Перед тем как приступить к конструированию даже самого простого устройства, его следует разработать, спроектировать и составить схему. Если нет никакого опыта в изготовлении электроприборов, лучше всего приобрести такой агрегат заводского изготовления.
Индукционная печь своими руками: схема, как собрать?
Домашняя индукционная печь справляется с плавкой относительно небольших порций металла. Однако такой горн не нуждается ни в дымоходе, ни в мехах, подкачивающих воздух в зону плавки. А всю конструкцию подобной печи можно разместить на письменном столе. Поэтому разогрев с помощью электрической индукции является оптимальным способом плавки металлов в домашних условиях. И в этой статье мы рассмотрим конструкции и схемы сборки подобных печей.
1 Как устроена индукционная печь – генератор, индуктор и тигель
В заводских цехах можно встретить канальные индукционные печи для плавки цветных и черных металлов. У этих установок очень высокая мощность, задаваемая внутренним магнитопроводом, который повышает плотность электромагнитного поля и температуру в тигле печи.
В промышленных масштабах производятся канальные индукционные печи для плавки цветных и черных металлов
Однако канальные конструкции расходуют большие порции энергии и занимают много места, поэтому в домашних условиях и небольших мастерских применяется установка без магнитопровода – тигельная печь для плавки цветного/черного металла. Такую конструкцию можно собрать даже своими руками, ведь тигельная установка состоит из трех основных узлов:
- Генератора, выдающего переменный ток с высокими частотами, которые необходимы для повышения плотности электромагнитного поля в тигле. Причем, если диаметр тигля можно будет сопоставить с длинной волны частоты переменного тока, то такая конструкция позволит трансформировать в тепловую энергию до 75 процентов электричества, потребляемого установкой.
- Индуктора – медной спирали, созданной на основе точного просчета не только диаметра и количества витков, но и геометрии проволоки, используемой в этом процессе. Контур индуктора должен быть настроен на усиление мощности в результате возникновения резонанса с генератором, а точнее с частотой питающего тока.
- Тигля – тугоплавкого контейнера, в котором и происходит вся плавильная работа, инициируемая за счет возникновения в структуре металла вихревых токов. При этом диаметр тигля и прочие габариты этого контейнера определяются строго по характеристикам генератора и индуктора.
Такую печь может собрать любой радиолюбитель. Для этого ему нужно найти правильную схему и запастить материалами и деталями. Перечень всего этого вы сможете найти ниже по тексту.
2 Из чего собирают печи – подбираем материалы и детали
В основе конструкции самодельной тигельной печи лежит простейший лабораторный инвертор Кухтецкого. Схема этой установки на транзисторах имеет следующий вид:
Схема установки на транзисторах
На основе этого рисунка-схемы вы сможете собрать индукционную печь, используя следующие компоненты:
- два транзистора – желательно полевого типа и марки IRFZ44V;
- медный провод диаметром 2 миллиметра;
- два диода марки UF4001, еще лучше — UF4007;
- два дроссельных кольца – их можно извлечь из старого блока питания от десктопа;
- три конденсатора емкостью по 1 мкФ каждый;
- четыре конденсатора емкостью по 220нФ каждый;
- один конденсатор с емкостью 470 нФ;
- один конденсатор с емкостью 330 нФ;
- один резистор на 1 ватт (или 2 резистора по 0,5 ватта каждый), рассчитанный на сопротивление 470 Ом;
- медный провод диаметром 1,2 миллиметра.
Кроме того, вам понадобится пара радиаторов – их можно снять со старых материнских плат или кулеров для процессоров, и аккумуляторная батарея емкостью не менее 7200 мАч от старого источника бесперебойного питания на 12 В. Ну а емкость-тигель в данном случае фактически не нужна – в печи будет плавиться прутковый металл, который можно удерживать за холодный торец.
3 Пошаговая инструкция для сборки – несложные операции
Распечатайте и повесьте над рабочим столом чертеж лабораторного инвертора Кухтецкого. После этого разложите все радиодетали по сортам и маркам и разогрейте паяльник. Закрепите два транзистора на радиаторах. А если вы будете работать с печью дольше 10-15 минут подряд, закрепите на радиаторах кулеры от компьютера, подключив их к рабочему блоку питания. Схема распиновки транзисторов из серии IRFZ44V выглядит следующим образом:
Схема распиновки транзисторов
Возьмите медную проволоку на 1,2 миллиметра и намотайте на ее на ферритовые кольца, сделав по 9-10 витков. В итоге у вас получатся дроссели. Расстояние между витками определяется диаметром кольца, исходя из равномерности шага. В принципе все можно сделать «на глаз», варьируя число витков в пределах от 7 до 15 оборотов. Соберите батарею из конденсаторов, соединяя все детали параллельно. В итоге у вас должна получиться батарея на 4,7 мкФ.
Теперь сделайте индуктор из медной 2-миллиметровой проволоки. Диаметр витков в этом случае может равняться диаметру фарфорового тигля или 8-10 сантиметрам. Число витков не должно превышать 7-8 штук. Если в процессе испытаний мощность печи покажется вам недостаточной – переделайте конструкцию индуктора, меняя диаметр и число витков. Поэтому на первых парах контакты индуктора лучше сделать не паянными, а разъемными. Далее соберите все элементы на плате из текстолита, опираясь на чертеж лабораторного инвертора Кухтецкого. И подключите к контактам питания аккумулятор на 7200 мАч. Вот и все.
Теперь вы можете проводить испытания печи, подбирая правильные параметры индуктора для каждой разновидности металла или тигля. Однако во время испытаний или плавки нужно помнить о мерах безопасности при работе с электропечами.
4 Меры безопасности при плавке металла
Индукционная установка генерирует очень высокую температуру, достаточную для расплавления металла массой до 10-20 грамм. Поэтому при работе с тиглем нужно использовать фартук из плотного материала и такие же рукавицы. Они уберегут вас от ожогов при случайном пролитии металла из емкости.
Собранную конструкцию печи лучше упрятать в изолированный корпус, оставив за его стенами только индуктор. Это убережет и пользователя, и хрупкие радиодетали. А для вентиляции в корпусе необходимо нарезать или насверлить несколько отверстий, обеспечив приток и отток воздуха.
Остаточное магнитное поле может нагреть металлические детали на одежде пользователя, которые обожгут кожу. Поэтому к тиглю лучше подходить в простой одежде, без молний или металлических пуговиц. Кроме того, все электроприборы лучше удалить от индуктора, как минимум, на метровое расстояние.
Простой лабораторный инвертор для индукционного нагрева. Часть 1.
Кухтецкий С.В., [email protected]
В статье подробно описана схема, конструкция и приведены советы по изготовлению лабораторного инвертора, предназначенного для индукционного нагрева и плавки. Инвертор может быть легко интегрирован в существующее оборудование лабораторных установок (трубчатые печи, прогреваемые трубопроводы, нагрев электропроводных тиглей и т.п.). Он может также использоваться автономно для закалки и плавки (в том числе — во взвешенном состоянии) небольших образцов металлов и сплавов (несколько грамм). Мощность инвертора регулируется от 0 до 2 кВт, диапазон рабочих частот – от 60 кГц до 300 кГц, питание – от сети 220В.
Введение
Инверторами называют устройства, обратные выпрямителям, т.е. — преобразователи постоянного напряжения в переменное. Обычно термин «инвертор» используется более узко: генератор переменного напряжения, используемый в качестве источника питания. Выходное напряжение инвертора может быть как промышленной частоты (50 Гц), так и повышенной (десятки, сотни кГц и выше). Одно из важнейших преимуществ источников питания повышенной частоты это резкое уменьшение массогабаритных параметров трансформаторов. Другой положительный момент связан с тем, что переключающие силовые элементы инверторов работают в ключевом режиме, т.е. основная часть потерь энергии происходит лишь в моменты переключения. Таким образом, современные быстродействующие полупроводниковые ключи позволяют существенно увеличить кпд преобразователей, приближая его для некоторых конструкций к 100%.
Быстрое развитие и удешевление элементной базы силовой электроники привело к тому, что некоторые классы инверторов прочно заняли свои ниши уже даже в быту. Это мощные импульсные блоки питания современных персональных компьютеров, электронные балласты для люминесцентных ламп, сварочные инверторы и бытовые индукционные электроплитки. Доступность и умеренная цена транзисторных инверторов также могли бы способствовать более широкому их внедрению и в практику физико-химического эксперимента. Вот далеко не полный список возможных приложений инверторов в экспериментальной лаборатории.
- 1. Источники питания для печей с низкоомными трубчатыми нагревателями.
2. Источники питания дуговых разрядов (плазмохимические реакторы с дуговым разрядом, электродуговая плавка).
3. Источники питания высоковольтных неравновесных разрядов (импульсные разряды, высокочастотные коронные и дуговые разряды, барьерные разряды (озонаторы)).
4. Индукционный нагрев (индукционные печи, закалка, плавка).
К сожалению, приобрести за разумную цену универсальный инвертор мощностью несколько киловатт с регулируемой частотой преобразования до двух-трех сотен килогерц – задача практически неразрешимая. Таких просто нет в продаже по вполне понятным причинам. Во-первых, очень непроста разработка такого универсального инвертора, пригодного к серийному производству. Во-вторых, у таких унифицированных инверторов нет непосредственного применения в быту. Поэтому производителям бытовой техники проще и дешевле использовать специализированные решения для каждого класса задач (сварка, электропитание, балласты и т.д.).
С другой стороны, для исследовательской лаборатории универсальность и гибкость оборудования – обычно один из самых важнейших критериев, часто перевешивающий остальные. Это несколько смещает акценты в сторону универсальных решений. Конечно, в ряде случаев можно попытаться приспособить некоторые бытовые решения для исследовательских задач. Например, можно приобрести и модифицировать готовый сварочный инвертор для питания низковольтной дуги. Это может оказаться дешевле, чем изготавливать инвертор в непрофильной лаборатории. Или можно переоборудовать компьютерный блок питания для получения среднечастотного инвертора на пару сотен ватт. Но грамотное выполнение таких задач потребует от экспериментатора квалификации не меньше, чем изготовление собственного инвертора, а гибкость и универсальность полученного решения будет весьма невелика.
Приведем еще несколько соображений, почему изготовление самодельного лабораторного инвертора может оказаться неплохим решением.
- 1. Во-первых, «нагрузка» на лабораторный инвертор обычно существенно меньше, чем на бытовые или промышленные образцы. Поэтому лабораторный инвертор может представлять собой скорее макет (прототип), чем промышленный образец, готовый к серийному производству.
2. Во-вторых, в условиях обычной исследовательской экспериментальной лаборатории нет таких жестких требований к надежности и экономичности устройства, как в промышленности или в быту. Это существенно «облегчает обвязку», связанную с автоматическим контролем функционирования устройства, защитой от внештатных ситуаций и перегрузок. Этот фактор становится еще более весомым, если учесть, что работа с этим оборудованием будет вестись достаточно квалифицированным персоналом.
3. В-третьих, поскольку речь не идет о серийном выпуске отработанного прототипа, то силовые комплектующие можно взять с большим избыточным «запасом прочности». Одновременно можно упростить и схемотехнические решения, повышающие надежность устройства.
4. Ну и, наконец, универсальный лабораторный инвертор может (как «конструктор») представлять собой набор отдельных модулей, часть из которых может быть выполнена в виде макетов с навесным монтажом, упрощающих их модификацию, анализ и ремонт. Модернизация и развитие этих модулей («обвязка» защитными и диагностическими цепями, автоматизация защиты и контроля) в условиях ограниченного бюджета может проводиться постепенно, лишь по мере необходимости.
С учетом этих соображений в лаборатории плазмохимии ИХХТ СО РАН был разработан и изготовлен прототип лабораторного инвертора, описанию которого посвящена данная статья. Инвертор может работать в диапазоне частот 60-300 кГц, мощность (для полумоста) – до 2 кВт. Все модули и основные технические детали рассмотрены с детализацией, достаточной для воспроизводства устройства любым квалифицированным экспериментатором, не имеющим специальной подготовки в области силовой электроники. В конце статьи приводятся примеры практического использования макета для нагрева и плавки.
Принцип работы полумостового инвертора
Различные варианты инверторов подробно описаны литературе [1, 2]. В данной статье речь пойдет о так называемом двухтактном «полумостовом» инверторе. Блок-схема полумостового инвертора представлена на рис.1.
Рис.1. Блок-схема полумостового инвертора.
Принцип его работы очень прост. Сетевое напряжение выпрямляется и подается на конденсатор C, к которому подключен силовой модуль. Силовой модуль содержит два полупроводниковых ключа (K1 и K2) и конденсаторный делитель (C1 и C2). Нагрузка подключается к общим точкам ключей и конденсаторов делителя. При помощи модуля управления ключи K1 и K2 включаются/выключаются попеременно с заданной частотой, подключая связанный с ними конец нагрузки то к верхней (по схеме), то к нижней шине питания. В результате на нагрузке получается переменное напряжение с амплитудой, равной половине напряжения питания.
Работа такого идеального инвертора, состоящего из идеальных ключей, действительно выглядит довольно просто. Проблемы начинаются тогда, когда мы приступаем к изготовлению реального инвертора из реальных компонентов. Эти проблемы приводят не только к усложнению схемотехнических решений, но и формируют вполне определенные требования к типу используемых компонентов, качеству монтажа, правилам компоновки, запуска и отладки. Без учета большинства этих требований сделать работоспособный инвертор не удается. Дорогие силовые транзисторы будут сгорать либо сразу при включении питания, либо в первые секунды работы.
Рассмотрим вкратце некоторые из этих требований. Более подробно они будут обсуждаться при описании конкретных модулей.
Первое требование — к модулю управления. Оно заключается в том, что работа ключей K1 и K2 должна быть согласованной, т.е. они должны открываться/закрываться попеременно и никогда не должны быть полностью открыты одновременно. Это необходимо для устранения так называемых «сквозных токов», текущих через оба открытых ключа, минуя нагрузку. Обычно это приводит к разрушению ключей. Кроме этого, поскольку реальные ключи имеют конечное (ненулевое) время открытия/закрытия, то открывающие сигналы модуля управления должны подаваться с некоторой задержкой после сигнала закрытия другого ключа. Эти задержки называются «мертвым временем» (dead-time) и должны быть предусмотрены в любом варианте модуля управления.
Другая проблема связана с тем, что все реальные элементы и соединения имеют конечную индуктивность. Поэтому даже при работе на чисто активную нагрузку при закрытии ключей возникают «выбросы» напряжения. Естественно, эти эффекты существенно возрастают при работе на индуктивную нагрузку, которая и нужна для данной задачи. Для решения этой проблемы обычно используют так называемые «возвратные диоды», включенные параллельно ключам. Кроме этого, необходимо выбирать ключи с некоторым запасом по рабочему напряжению (как минимум, вольт на 200).
Еще одна группа проблем связана с паразитными индуктивностями монтажа. Дело в том, что при очень быстром коммутировании больших токов заметные «наводки» появляются даже на очень небольших индуктивностях. С первого взгляда – просто «на пустом месте». Для того, чтобы «почувствовать» эти эффекты, сделаем простую оценку. Пусть мы коммутируем ток ΔJ ~ 10A за время Δt ~ 10нс (10-8 с). Напряжение U, возникающее на индуктивности L, можно оценить как U ~ L ΔJ/Δt. Индуктивность одного дюйма (2.54 см (!)) провода диаметром 1 мм порядка 10 нГн (10-8 Гн). В результате получаем наводку на этом дюйме провода U ~ 10-8*10/10-8 = 10 В (!). Это напряжение сравнимо с напряжением питания микросхем драйверов для управления ключами! Такая наводка вполне может открыть ключ в самый неподходящий момент (например, когда уже открыт второй ключ) со всеми вытекающими печальными последствиями. Поэтому правильная компоновка и монтаж играют особую роль в быстродействующей силовой электронике.
Единого рецепта здесь нет, но нужно придерживаться нескольких простых правил, уменьшающих паразитные индуктивности (либо эффекты от их наличия). Суть этих правил в следующем.
- 1. Силовые проводники, по которым текут коммутируемые токи, нужно делать как можно короче, прямее и толще.
Стараться избегать петель таких проводников.
2. По-возможности, необходимо разделять силовые и управляющие цепи, а сами силовые элементы располагать как можно ближе друг к другу.
3. При разводке земляных цепей придерживаться правила «одной точки». Всегда нужно помнить о том, что на любом проводнике, по которому течет большой ток, есть разность потенциалов, которая сопоставима с уровнем управляющих сигналов. Поэтому не стоит, например, заземлять различные элементы управляющих цепей в разных точках земляной шины, по которой течет большой импульсный ток. Это чревато непредсказуемой работой управляющего модуля.
На самом деле все не так уж страшно. Более того, многие разработчики указывают правила монтажа для критических узлов в документации к ним. Главное – не делать грубых ошибок. Тогда можно изготовить, пусть не идеальный, но вполне работающий прибор.
Предупреждение об опасности
Цепи выпрямителя и силового модуля находятся под высоким напряжением без гальванической развязки от питающей сети. Поэтому при работе с инвертором нужно соблюдать предельную осторожность. ВСЕ МАНИПУЛЯЦИИ с этими модулями можно проводить ТОЛЬКО ПОСЛЕ ВЫКЛЮЧЕНИЯ ПИТАНИЯ И ПОЛНОГО ОТКЛЮЧЕНИЯ ПРИБОРА ОТ СЕТИ!
Описание макета лабораторного инвертора
Перейдем теперь к описанию отдельных узлов лабораторного инвертора. Начнем с выпрямителя.
Выпрямитель
В данной реализации инвертора это самый простой, но и самый громоздкий узел. Он содержит большой и тяжелый ЛАТР (лабораторный автотрансформатор) для регулирования выходного напряжения выпрямителя и один громоздкий низкочастотный развязывающий трансформатор. Выбор такого решения обусловлен следующими причинами.
- 1. На стадии первоначального знакомства с силовой электроникой и отладки желательно иметь возможность плавно регулировать постоянное напряжение, подаваемое на ключи. Самый простой способ, доступный практически в любой экспериментальной лаборатории – это ЛАТР.
2. Если взять за правило начинать и заканчивать работу инвертора при «нулевом» положении ЛАТРа, то можно избежать необходимости создания специальных цепей для первоначальной зарядки больших электролитических конденсаторов фильтра.
3. ЛАТР обладает большой индуктивностью, поэтому на первых порах можно убрать высокочастотные фильтры по цепи питания.
4. На стадии знакомства с силовой электроникой возникает много вопросов, ответы на которые проще найти экспериментально, путем осциллографирования сигналов в различных точках схемы. Поскольку силовые узлы инвертора не имеют гальванической развязки с питающей сетью, то на первых порах ее лучше сделать. Хотя бы для процесса отладки, при работе на малых мощностях. Самый эффективный способ – запитать весь инвертор через развязывающий трансформатор подходящей мощности. Естественно, коэффициент трансформации его должен быть близок к единице. Такая развязка желательна также и для дополнительной безопасности самого экспериментатора при отладке инвертора.
С учетом этих соображений первый вариант регулируемого выпрямителя для лабораторного инвертора получается простым. Его схема представлена на рис.2. Выпрямитель не содержит каких-нибудь дефицитных деталей и узлов, надежен и весьма удобен в работе.
Рис.2. Схема выпрямителя.
Рассмотрим некоторые детали реализации выпрямителя. В качестве выключателя и предохранителей можно взять обычный бытовой сдвоенный автомат на 10-16 ампер. Подходящий 8-амперный ЛАТР можно найти в любой экспериментальной лаборатории «со стажем». При отсутствии ЛАТРа на стадии отладки (при работе на малых мощностях – 200-300 Вт) можно использовать электронный аналог ЛАТРа на биполярных транзисторах (см., например, [3]). При больших мощностях придется делать импульсный регулятор, естественно, со всеми вытекающими последствиями. Поэтому на начальных стадиях лучше все-таки приобрести ЛАТР, хотя стоят они сейчас недешево. Как, впрочем, и другие низкочастотные трансформаторы. Это, кстати, еще один аргумент в пользу перевода лабораторного хозяйства на импульсные преобразователи.
Развязывающий трансформатор TR можно заказать отдельно или же сделать из старого ЛАТРа подходящей мощности. В последнем случае, если использовать уже существующую обмотку ЛАТРа в качестве первичной, нужно обратить особое внимание на межвитковую изоляцию. Желательно хорошенько очистить обмотку от угольной пыли и залить лаком дорожку, где изоляция обмотки снята. В качестве развязывающего трансформатора можно также взять пару силовых (или небольших сварочных) трансформаторов, подходящей мощности и включить их встречно. Например, у трансформаторов 220 на 36 вольт соединить 36-вольтовые обмотки, и использовать 220-вольтовые обмотки как обмотки развязывающего трансформатора. После отладки инвертора развязывающий трансформатор желательно убрать (особенно, если он маломощный).
Диодный мост VD1 лучше выбрать с запасом, ампер на 20-30 и рабочим напряжением 1000 В. Например, KBPC3510, KBU25M и т.п.. Их лучше установить на небольшую металлическую пластину в качестве радиатора, хотя при мощности инвертора 1-2 кВт они практически не греются.
Кнопка S3 и резистор R2 предназначены для разряда конденсатора C1 в случае аварии. Например, при выгорании силовых ключей, на этом конденсаторе может остаться высокое напряжение опасное для жизни. В начале работы с силовой электроникой вероятности аварий достаточно велики, поэтому желательно предусмотреть такой разрядник.
Сам конденсатор C1 – электролитический, с рабочим напряжением не менее 400 В. Он может быть составным. В случае последовательного соединения конденсаторов обязательно нужно поставить выравнивающие резисторы на 150-200 кОм, подключенные параллельно каждому конденсатору. Конденсатор C2 – пленочный, с рабочим напряжением не менее 400 В.
И, наконец, 10-амперный измеритель переменного тока на входе инвертора и вольтметр постоянного напряжения на выходе выпрямителя предназначены для контроля полного тока, потребляемого инвертором из сети, и напряжения, подаваемого на полумост силового модуля. Этот контроль особенно актуален при ручной регулировке мощности инвертора. В качестве вольтметра очень удобно использовать недорогой китайский цифровой мультиметр. К сожалению, такие мультиметры не рассчитаны на длительное измерение больших токов (например, 10-амперный режим – не дольше 10 сек с перерывами 15 мин), поэтому в качестве амперметра проще использовать обычный стрелочный амперметр переменного тока.
Никаких особых требований к компоновке выпрямителя нет. Поскольку по цепям выпрямителя текут довольно большие токи (до 10 А в данном инверторе), то монтаж необходимо выполнять короткими и толстыми проводами сечением не менее 1.5 – 2 мм2. Общий вид одного из вариантов выпрямителя представлен на рис.3 (без развязывающего трансформатора).
Рис.3. Общий вид выпрямителя.
Конечно же, в перспективе желательно заменить такой регулятор с громоздким ЛАТРом на подходящий импульсный регулятор. Во-первых, он гораздо компактнее и, во-вторых, он мог бы обеспечить некоторый запас по мощности (до 6-10 кВт). Однако в данном проекте главная цель – получить реально работающий инвертор для физико-химических экспериментов максимально простым способом. Поэтому остановимся на этом варианте, а импульсный регулятор оставим на будущее.
Перейдем теперь к модулю управления.
Модуль управления
Естественно, схемотехника модуля управления определяется тем, какими ключами он будет управлять. В данном инверторе в качестве ключей используются мощные полевые транзисторы с изолированным затвором, известные под аббревиатурой MOSFET (Metal Oxide Semiconductor Field Effect Transistor) или по-русски — полевые МОП-транзисторы (Метал-Оксид-Полупроводник). Популярно о таких транзисторах можно почитать, например, в [1]. Однако, для данного раздела достаточно просто представлять MOSFET как некий электронный выключатель, который управляется напряжением на затворе (относительно истока). В открытом состоянии сопротивление между истоком и стоком мало (в зависимости от типа транзистора — от нескольких Ом до сотых долей Ома), а в закрытом – велико (десятки МОм и выше). Для большинства транзисторов напряжение на затворе может изменяться в пределах от -20 до + 20 Вольт. Если напряжение на затворе выше порогового (порог обычно от +2 до +4 В) транзистор открывается, если ниже – закрывается.
Таким образом, для управления ключами мы должны подавать на затворы транзистора положительные импульсы с напряжением 12-18 В. Это должны быть две последовательности импульсов, передаваемые по двум отдельным управляющим шинам, сдвинутые по времени относительно друг друга (рис.4). Как уже отмечалось выше, для устранения сквозных токов должны быть предусмотрены паузы (dead-time).
Рис.4. Диаграммы управляющих импульсов.
Существует множество вариантов таких генераторов управляющих импульсов. В данном проекте применено одно из простейших решений на основе распространенной и недорогой микросхемы IR2153. Эта микросхема представляет собой законченный автоколебательный драйвер полумоста для электронных балластов люминесцентных ламп. Драйвер имеет фиксированную длительность dead-time (1.2 мкс). Максимальное время нарастания и спада импульсов 150 и 100 нс, соответственно. Поэтому максимальная частота управляющих импульсов ограничена значением 300-350 кГц.
К сожалению, мощность выходных каскадов этого драйвера (Io+- = 200 мА/400 мА) не позволяет его использовать непосредственно в качестве драйвера затворов полевых транзисторов нашего инвертора. Причина в том, что затворы мощных MOSFET-ов имеют довольно большую емкость (доходящую до нескольких тысяч пикофарад), т.е. драйверы вынуждены работать на большую емкостную нагрузку. Поэтому драйверы должны выдавать большие токи. Иначе время переключения (и, следовательно, тепловые потери) транзисторов будут велики. Оценим эти токи.
В данном проекте в качестве ключей используются транзисторы IXFh40N50. Производитель декларирует суммарную емкость затвор-исток и затвор-сток Ciss = 5200-5700 пФ. Однако, в действительности реальная (эффективная) емкость затвора гораздо больше. Здесь для оценки нужно брать полный заряд, который необходимо передать затвору для того, чтобы транзистор полностью открылся. Обычно эта величина тоже приводится в datasheet. Для IXFh40N50 Qg(on) ~ 200-300 нКл. Таким образом, для напряжения затвор-исток 10 В получаем Cэфф ~ 20-30 нФ. Это в 4-6 раз больше, чем Ciss! Для того, чтобы время включения транзистора было порядка 100 нс, драйвер должен заряжать емкость затвора током порядка (2-3)*10-7 Кл / 10-7 сек ~ 2-3 A. Такой ток драйвер IR2153 выдать не может. Поэтому в данном проекте IR2153 используется только как задающий генератор, сигналы которого затем будут усиливаться. Схема генератора представлена на рис.5.
Рис.5. Генератор управляющих импульсов на IR2153.
С выводов 5 (LO) и 7 (HO) мы получим сигналы, точно совпадающие с сигналами, представленными на рис.4. Резисторы R3 и R4 и конденсатор C3 определяют частоту генерирования импульсов. Для указанных номиналов при помощи резистора R3 эту частоту можно изменять в пределах приблизительно от 60 до 300 кГц.
Для усиления сигналов генератора управляющих импульсов существует множество схемотехнических решений, как на дискретных элементах, так и специализированные интегральные микросхемы (см., например, [4, 5]). В данном инверторе был применен не самый дешевый, но зато очень простой вариант. Были использованы 6-амперные быстрые драйверы MAX4420. Естественно, вместо этих драйверов можно поставить продукты других производителей или собрать их на комплементарных парах транзисторов (полевых или биполярных). Главное условие – они должны быть быстродействующими (фронты и спады – до сотни наносекунд) и обеспечивать токи несколько ампер. Однако проще и экономичнее – готовые интегральные драйверы. Схема включения драйверов MAX4420 показана на рис.6.
Рис.6. Фрагмент модуля управления.
С выходов L и H мы получим усиленные управляющие импульсы, по форме совпадающие с сигналами на рис.4.
Теперь осталось рассмотреть очень важный и непростой вопрос — согласование уровней управляющих сигналов. Поскольку в основу силового модуля у нас положен полумост, то возникает известная проблема управления верхним плечом полумоста. Нам необходимо, чтобы драйвер верхнего плеча выдавал управляющие импульсы не относительно земли (как на рис.6), а относительно уровня истока верхнего транзистора (т.е. US1, рис.7). Это уровень может изменяться в течение рабочего цикла приблизительно от 0 (нижний ключ открыт, верхний закрыт) до напряжения питания (нижний ключ закрыт, верхний открыт).
Рис.7. К согласованию уровней управляющих импульсов полумоста.
Существуют несколько схемотехнических решений для сдвига уровня сигнала верхнего плеча. Они делятся на два класса: с гальванической развязкой и без. К первому классу относятся системы с оптической развязкой и на импульсных трансформаторах. Ко второму классу относятся, в частности, бутстрепные (bootstrap) схемы. Не вдаваясь в детали, отметим, что бутстрепные схемы удобны при реализации хорошо отлаженных решений. Однако на стадии освоения силовой электроники они доставляют немало огорчений. Из-за отсутствия гальванической развязки при тепловом пробое силовых транзисторов часто выгорает также и весь модуль управления (вплоть до задающего генератора). Поэтому в данной работе использован вариант с гальванической развязкой в виде импульсного трансформатора. На частотах десятки-сотни килогерц изготовление импульсных трансформаторов на ферритовом кольце не представляет никаких трудностей. При наличии осциллографа нет проблем ни с корректировкой количества витков, ни с подгонкой параметров снабберов, гасящих паразитные выбросы и осцилляции. Полная схема модуля управления с трансформаторной развязкой представлена на рис.8.
Рис.8. Полная схема модуля управления с трансформаторной развязкой.
Поскольку драйверы MAX4420 работают на индуктивную нагрузку, на их выходы нужно поставить диоды VD6-VD9. Можно использовать любые быстрые диоды SF, HER, UF и т.п. Снаббер C7-R5 предназначен для подавления выбросов напряжения при работе на индуктивную нагрузку. Кроме этого, C7 удаляет постоянную составляющую.
Импульсный трансформатор можно рассчитать, а можно просто подобрать экспериментально по качеству сигналов на нагрузке, моделирующей затворы MOSFET. При подборе количества витков можно руководствоваться простым правилом: количество витков должно быть максимально возможным, но при этом сердечник трансформатора не должен уходить в насыщение. При слишком малом количестве витков импульсы на вторичных обмотках имеют спадающий характер (т.е. у прямоугольных импульсов нет «полочки»), при слишком большом – наоборот. Сердечник насыщается, магнитная проницаемость падает и всплески получаются в конце импульсов. Во всем рабочем диапазоне импульсы должны иметь плоские вершины. Параметры трансформатора, использованного в данном инверторе, указаны на схеме. Размеры сердечника несколько избыточны, но для данной конструкции это не важно. Мотать обмотки лучше сразу в три провода, параллельно или перевив их, равномерно распределяя витки по сердечнику. На рис.9 представлен вид модуля управления, собранного на макетной плате.
Рис.9. Общий вид макета модуля управления.
Особых требований к монтажу здесь нет, кроме обычных правил для импульсных схем. Нужно стараться располагать компоненты поближе к друг другу, соединительные провода должны быть покороче и попрямее. Конденсаторы C4, C5 и C6 необходимо располагать непосредственно у корпусов соответствующих микросхем у ножек питания. В данном инверторе модуль управления неплохо работает и просто на макетной плате (как на рис.9).
Питание модуля управления осуществляется от единого нестабилизированного источника постоянного напряжения (20В, 8А), представляющего собой накальный трансформатор, выпрямительный мост и электролитический конденсатор на 1000 мкф в качестве фильтра. Для получения стабилизированных напряжений 12В и 15В используются микросхемы стабилизаторов LM7812 и LM7815, включенных согласно datasheet. В принципе, драйвер IR2153 содержит внутри стабилитрон, поэтому его можно просто запитать через резистор от тех же стабилизированных 15В. Но для повышения помехоустойчивости лучше его запитать через отдельный стабилизатор. От этого же общего нестабилизированного источника питается и вентилятор силового модуля (через еще одну LM7812 с небольшим радиатором). На рис.9 эти стабилизаторы находятся в левой части платы.
На рис.10 представлена осциллограмма сигнала на выходе блока управления (на конденсаторах Cэфф = 3300 пФ, на щупе осциллографа – делитель 1:10).
Рис.10. Осциллограммы управляющих сигналов на эквивалентах затворов (нижнее плечо слева и верхнее — справа).
Фронты и спады на емкостную нагрузку порядка 130-160 нс, «полочки» хорошо выражены, выбросы не превышают 0.5В. Необходимо учесть, что эффективная емкость реальных транзисторов гораздо больше (как правило, в 4 и более раз), поэтому при работе на реальные затворы фронты будут положе.
Подобная форма импульсов и длительности переходов сохраняются во всем рабочем диапазоне 60-300 кГц (см. рис.11). На этом рисунке представлены осциллограммы на границах диапазона. Видно, что спад вершины импульса при низких частотах (правая осциллограмма) несущественный.
Рис.11. Форма сигналов на высоких (306 кГц) и низких (62 кГц) частотах.
В заключение этого раздела отметим еще один положительный момент, связанный с применением трансформаторной развязки. Такое включение трансформатора, как на рис.8, превращает наш однополярный драйвер в двухполярный. Т.е. в полупериод, когда транзистор силового модуля должен быть закрыт, на его затвор подается отрицательный импульс (а не ноль, как в однополярном). Для приборов с изолированным затвором это допускается. Подача отрицательного сигнала на затвор позволяет существенно повысить помехоустойчивость силового модуля от наводок, избежать ложных срабатываний (открытий) транзисторов без дополнительных «обвязок» их затворов.
Силовой модуль
Как уже отмечалось выше, в данном инверторе силовой модуль представляет собой полумост. Его полная схема представлена на рис.12.
Рис.12. Схема силового модуля.
В качестве ключей использованы транзисторы IXFh40N50 фирмы IXYS. Они почему-то гораздо дешевле аналогичных приборов других производителей. Эти транзисторы рассчитаны на ток до 30 А и рабочее напряжение до 500 В. Сопротивление «исток-сток» в открытом состоянии – 0.16 Ом. Можно было бы поставить и менее мощные транзисторы, но экономия будет несущественной, а запас мощности никогда не помешает. Единственной веской причиной для использования транзисторов попроще было бы уменьшение емкости затвора и заряда, необходимого для открытия транзистора. Но в данной разработке мы используем драйверы достаточно мощные и для этих транзисторов.
В цепях затворов мы используем только резисторы R7 и R8, которые ограничивают токи зарядки емкостей затворов и гасят высокочастотный «звон». В данном варианте силового модуля никаких дополнительных элементов в цепях затворов нет.
Силовые транзисторы шунтированы возвратными диодами VD10 и VD11. В принципе, их можно не ставить, так как используемые транзисторы (IXFh40N50) сами содержат не такие уж плохие внутренние диоды (trr <250 нс). Однако, если работать на повышенных частотах (сотни килогерц), лучше поставить сверхбыстрые диоды. Под рукой оказались MUR860 с trr <60 нс, ток 8 А и напряжение 600 В. Вместо них можно использовать другие сверхбыстрые диоды (например, HER или SF), сопоставимые по параметрам. Можно взять и менее мощные (по току) диоды, но тогда их желательно разместить в зоне обдува радиаторов транзисторов.
Снабберы R9-C8 и R10-C9 также шунтируют ключи. Они служат для подавления выбросов и особенно желательны при работе на индуктивную нагрузку. Резисторы R9 и R10 заметно греются, поэтому их лучше разместить в зоне обдува, либо использовать более мощные резисторы (5 – 10 Вт). Конденсаторы C8 и C9 должны быть рассчитаны на напряжение не менее 600-800 В.
Конденсаторы C10 и C11 тоже должны быть высоковольтными (не менее 400 В) и пленочными. Если они будут монтироваться вне зоны обдува, то лучше их собрать из нескольких (3-4) конденсаторов меньшей емкости, включенных параллельно. В данной работе каждый конденсатор собран из трех по 0.47 мкФ. Их нагрев был незначительным даже без обдува.
Теперь немного о конструкции силового модуля.
Несмотря на то, что мы взяли довольно мощные транзисторы, нагрев их в процессе работы будет все-таки ощутимым. Высоковольтные MOSFET имеют, к сожалению, все-таки достаточно высокое сопротивление открытого канала. Действительно, даже в полностью открытом состоянии на транзисторе будет выделяться порядка 10-16 Вт тепла (0.16 Ом * (10 А)2 = 16 Вт). Плюс еще потери при переключении и еще при повышенных частотах. Поэтому ключи обязательно необходимо размещать на радиаторах. Разумные размеры радиаторов получаются при условии их принудительного обдува. Очень удобно использовать для этой цели кулеры (теплосъемники) мощных компьютерных процессоров. Они содержат радиатор и вентилятор, объединенные в одну конструкцию. В последние годы ассортимент кулеров сильно расширился, и они заметно упали в цене. Цена бывшего в употреблении кулера, даже с медным радиатором и сносно работающим вентилятором, гораздо ниже стоимости большого дюралюминиевого радиатора. Такой кулер и был положен в основу конструкции силового модуля, представленного на рис.13.
Рис.13. Силовой модуль.
Транзисторы VT1 и VT2 размещены на изолирующих прокладках из слюды непосредственно на подошве радиатора. Остальные компоненты припаяны к выводам этих транзисторов и, по сути дела, на них и держатся. Термопара для контроля температуры транзисторов размещена сверху и прижата к медному основанию радиатора тоже через изолирующую прокладку. Прокладка необходима для устранения наводок на термопару, так как радиатор не заземлен и находится под плавающим потенциалом.
Ну вот, по сути дела, и весь инвертор. Осталось соединить все модули вместе и приступить к испытаниям.
Первое включение инвертора
Для первого включения необходимо подключить развязывающий трансформатор и небольшую активную нагрузку. В качестве нагрузки возьмем лампу накаливания на 100 Вт. Вид собранного для испытаний инвертора представлен на рис.14.
Рис.14. Готовый к испытаниям инвертор.
Первое испытание инвертора проводим по шагам.
Шаг 1. Еще раз проверяем правильность монтажа и сборки инвертора. Полезно убрать все лишнее со стола.
Шаг 2. Включаем питание блока управления. Только блока управления! Высокое напряжение пока не включаем. Смотрим на экране осциллографа сигналы на затворах ключей. Земляной разъем щупа осциллографа подключаем к истоку соответствующего транзистора. Сигналы должны быть похожи на сигналы, представленные на рис.10. В зависимости от используемых транзисторов и драйверов фронты могут быть более пологие. Обязательно проверяем фазировку сигналов. Для этой цели, конечно, лучше двухлучевой осциллограф, но можно и однолучевым. В последнем случае запуск развертки осциллографа необходимо выполнять от отдельного сигнала синхронизации. В качестве такого сигнала удобно использовать один из выходов IR2153 (см. рис.8). Осторожнее с земляными разъемами щупов! В данном случае мы используем трансформаторную развязку, поэтому земляной разъем щупа в силовом блоке можно спокойно подключать к истокам обоих транзисторов полумоста. В противном случае для сигнала синхронизации нужно сделать развязку. Иначе могут быть большие искры.
Шаг 3. Если шаг 2 пройден успешно, подключаем щупы осциллографа параллельно нагрузке. Проверяем положение ручки ЛАТРа. Она должна быть на нуле! После этого включаем высокое напряжение. ЛАТРом плавно поднимаем напряжение до 15-20 В. Контролируем это напряжение по вольтметру выпрямителя. На экране осциллографа мы должны увидеть импульсы напряжения на нагрузке, симметричные относительно нуля (как на рис.15 слева).
Рис.15. Осциллограммы сигналов на активных нагрузках. Высокоомная (лампочка 100 Вт, 40 Ом) слева, низкоомная (лампочка 500 Вт, 8 Ом) справа. Щуп с делителем 1:10.
На самом деле это осциллограммы с шага 5. Но на этом шаге сигналы должны быть точно такие же, только меньшей амплитуды. Я их привел здесь для того, чтобы обсудить их форму. Мы видим медленно спадающие в течение dead-time «хвосты» на высокоомной нагрузке (рис.15 слева). Это связано с тем, что в течении dead-time оба транзистора закрыты. Поэтому чисто активная нагрузка вместе со щупом осциллографа просто, как говорят, «висит в воздухе». При отсутствии нагрузки (бесконечное сопротивление) потенциал средней точки (между ключами) вообще не изменяется в течение dead-time. Поэтому не нужно обращать внимание на эти хвосты. При уменьшении сопротивления нагрузки форма сигнала будет приближаться к классической (с «плечиками» dead-time). Чтобы убедиться в этом можно взять более мощную лампочку с меньшим сопротивлением нити накала или вообще другую нагрузку с сопротивлением 10-20 Ом. Осциллограммы для лампочки на 500 Вт приведены на рис.15 справа. Мы видим, что все работает правильно.
Продолжим работу с лампочкой на 100 Вт.
Шаг 4. Изменяем частоту инвертора от минимума да максимума. Форма импульсов не должна радикально меняться. По крайней мере они должны оставаться симметричными относительно нуля.
Шаг 5. Если на шаге 3-4 все нормально, постепенно увеличиваем напряжение до 100-120 вольт. Спираль лампочки начнет светиться. Первая мощность от инвертора получена! «Погоняем» его так минут 30-40. Температура радиатора не должна заметно уходить от комнатной.
Шаг 6. Если осциллограф не позволяет работать при высоких напряжения, то отключим щуп и плавно выведем напряжение на уровень 300-310 В. Лампочка ярко светится. Следим за температурой радиаторов. Если нагрев существенный – придется все-таки возиться с разрядкой затворов MOSFET. В моих экспериментах в течение часа температура радиаторов превысила комнатную лишь на 2-3 градуса. Не таким уж страшным оказалось наше «недозакрывание» транзисторов. Спокойно работаем дальше. Общий вид инвертора во время этого шага представлен на рис.16.
Рис.16. Общий вид инвертора в процессе испытаний (через час работы на шаге 6).
Шаг 7. Быстро выводим ЛАТР в 0 и быстро выключаем все питание (сначала высокое, затем — питание модуля управления с вентилятором). Внешней стороной пальца проверим температуру резисторов снабберов и конденсаторов делителя (R9, R10 и C10, C11). Они не должны быть горячими. Заодно проверим и радиатор. Так, на всякий случай. Вдруг у термопары – плохой тепловой контакт.
Все. Первые испытания инвертора закончены. Теперь можно переходить к индукционному нагреву.
Индукционный нагрев
Индукционный нагрев это технология, связанная с возбуждением вихревых токов в проводящих образцах для их нагрева. В настоящее время индукционный нагрев широко используется в различных отраслях промышленности и даже в быту (например, бытовые индукционные плитки). Однако, в исследовательской лаборатории индукционный нагрев – пока еще экзотика. Может быть лабораторный инвертор, о котором идет речь в данной статье, облегчит внедрение технологий индукционного нагрева в практику физико-химического эксперимента. Мы продемонстрируем замечательные возможности высокочастотных инверторов на одном красивом примере. Это – плавка металла (алюминия) во взвешенном состоянии. Иногда этот процесс называют плавкой в электромагнитном тигле или просто «левитационной плавкой» (с англоязычного термина «levitation melting»). Здесь высокочастотное электромагнитное поле не только греет и плавит металл, но и удерживает его в пространстве без каких-нибудь тиглей или ограничивающих стенок. Для того, чтобы осуществить такую плавку, нам необходимо изготовить водоохлаждаемую нагрузку с индуктором специальной формы и предусмотреть в системе некоторую дополнительную диагностику. Начнем с нагрузки.
Нагрузка
Эквивалентная схема нагрузки для индукционного нагрева и плавки представлена на рис.17.
Рис.17. Эквивалентная схема нагрузки для индукционного нагрева.
Трансформатор TR2 изготовлен из двух колец К 45х28х12. Марка феррита М 2000 НМ. Первичная обмотка – 26 витков провода МГТФ 0.75. Эта обмотка подсоединяется непосредственно к выходу инвертора. Роль вторичной обмотки, состоящей из одного витка, выполняет одна из отводных трубок индуктора (медь, диаметр 6 мм), проходящая через центр кольца трансформатора. Индуктор представляет собой катушку, содержащую несколько витков (медная трубка диаметром 4 мм). Индуктор вместе с конденсатором C образует последовательный колебательный контур, на резонансную частоту которого должен быть настроен инвертор. Нагреваемый образец, помещенный в индуктор на эквивалентной схеме можно представить как активное сопротивление, индуктивно связанное с индуктором.
Конструкция собранной нагрузки со специальным индуктором для плавки во взвешенном состоянии показана на рис.18 слева.
Рис.18. Общий вид нагрузки и дополнительной диагностики.
Поскольку данная статья посвящена, в основном, инвертору, а не тонкостям индукционного нагрева, отметим только самые важные моменты, касающиеся конструкции нагрузки.
Во-первых, в нашем колебательном контуре проходят весьма большие токи (сотни ампер). Поэтому медные трубки, образующие индуктор и подводы к нему, при больших мощностях довольно сильно нагреваются. Их нужно обязательно охлаждать. Проще всего использовать водяное охлаждение непосредственно из водопровода. Поскольку в контуре имеется высокое напряжение, необходимо предусмотреть электрическую развязку индуктора от водопровода. Для этого подвод воды делаем тонкими длинными диэлектрическими трубами. Длина этих труб зависит от проводимости водопроводной воды. Проводимость воды в лаборатории автора составляет величину порядка 100 мкСм/см, поэтому развязка в виде трубок диаметром около 6 мм и длиной 5-6 м имеет достаточное для электрической развязки сопротивление (около 50 Мом). Желательно также контролировать и температуру охлаждающей воды. Это легко сделать при помощи металлической вставки в сливной тракт. К ней можно прикрепить термопару, подключенную к недорогому китайскому тестеру, в котором есть режим измерения температуры (рис. 18 в левом верхнем углу). Очень удобно — сразу видно, если забыл включить воду для охлаждения.
Во-вторых, конденсатор C колебательного контура должен быть рассчитан на довольно большую реактивную мощность. Необходимо использовать либо специальные конденсаторы для индукционного нагрева, либо набирать батарею из достаточно большого количества пленочных конденсатором меньшей емкости, включенных параллельно. В данном контуре конденсаторная батарея содержит 40 полипропиленовых высоковольтных конденсаторов CBB81. Емкость каждого конденсатора — 0.033 мкФ, рабочее напряжение 2 кВ. Общая емкость батареи – 1.32 мкФ. Тангенс угла потерь их составляет 0.0008. Поэтому на каждом конденсаторе выделяются в виде тепла лишь десятые доли ватта. Конденсаторы смонтированы свободно и хорошо охлаждаются конвективными потоками воздуха. Поэтому, даже после получаса работы на максимальной мощности они нагреваются незначительно (на 10-20 градусов).
И, в-третьих. Для устойчивой левитационной плавки, конструкция катушки индуктора должна иметь специальную форму. В данном случае индуктор выполнен из медной трубки диаметром 4 мм в виде конуса. Угол между образующей и горизонталью равен 65°. Индуктор содержит четыре витка в прямом направлении и один – в обратном (противовиток). Это нужно для того, чтобы внутри индуктора была область, в которой поле меньше, чем вокруг нее. Проводник, помещенный в переменное электромагнитное поле, выталкивается в область меньших полей. Поэтому без области с минимальным полем положение образца внутри индуктора будет неустойчивым. Для левитационной плавки небольших образцов коническая конструкция индуктора с противовитком – одна из самых простых, но эффективных. Подробнее о плавке во взвешенном состоянии и сравнительный анализ различных конструкций индукторов см. в [5, 6].
Дополнительная диагностика
Для «ручной» настройки инвертора на резонанс при работе с резонансной нагрузкой и оптимизации процесса нагрева полезно добавить к установке еще пару измерителей, связанных с током, потребляемым нагрузкой.
Первый измеритель предназначен для контроля среднеквадратичного тока. Это трансформатор тока с двухполупериодным выпрямителем. Первичная обмотка представлена проводом, идущим от инвертора к нагрузке и проходящим через центр небольшого ферритового кольца. На этом кольце намотана вторичная обмотка (20 – 30 витков провода с выводом от середины обмотки). Далее при помощи двух диодов сигнал выпрямляется, фильтруется и измеряется при помощи обычного китайского мультиметра.
Второй измеритель также представляет собой трансформатор тока, идущего в нагрузку, но служит для контроля осциллограммы сигнала. Он устроен практически так же, как и в предыдущем случае, но вторичная обмотка не содержит вывода из центра и нагружена на резистор в несколько сотен Ом. С этого резистора сигнал подается на осциллограф. Очень удобно при настройке на резонанс и контроле нештатных ситуаций.
Проверка работоспособности установки индукционного нагрева
Включаем воду охлаждения и все измерители, необходимые для контроля процесса. Далее, сначала включается питание модуля управления и вентилятора, а затем – источник высокого напряжения (выпрямитель). Плавно при помощи ЛАТРа увеличиваем напряжение до 30-50 В. Затем, медленно изменяя частоту инвертора (резистор R3 на рис. 8), пытаемся настроить инвертор на резонанс. Резонанс настраиваем по максимуму тока, потребляемого нагрузкой, контролируя его амплитуду по осциллографу. После настройки на резонанс увеличиваем при помощи ЛАТРа напряжения на силовом модуле до нужного уровня. Установка для индукционного нагрева готова к работе.
Выключение производится в обратном порядке. Сбрасываем высокое напряжение (выводим ЛАТР в 0), затем выключаем его. После этого выключается источник питания модуля управления. Дальше – в произвольном порядке.
Настройку на резонанс приходится выполнять не так уж часто. Опыт показал, что при внесении в индуктор небольших ферромагнитных образцов, расстройка контура не приводит к фатальному уменьшению поглощаемой образцом мощности и он греется достаточно хорошо даже без дополнительной подстройки частоты. При работе с немагнитными материалами резонансная частота вообще практически не «уходит».
На рис. 19 и рис. 20 представлены два примера, иллюстрирующие работу инвертора в качестве индукционного нагревателя. Первый вариант – ферромагнетик (просто — ручка надфиля), второй – немагнитный (кусок нержавеющей трубки). По ссылкам ниже можно загрузить видео, показывающие весь процесс. Ни в том, ни в другом случае никакой дополнительной подстройки частоты не производилось.
Рис.19. Нагрев ферромагнитного материала.
Рис.20. Нагрев немагнитного материала.
При помощи пирометра ПД-4-02 была оценена температура графитового образца, помещенного в индуктор, на воздухе, без теплоизоляции. При максимальной мощности она была около 1300-1350°С. Так что для небольших трубчатых печей с графитовым нагревателем наш инвертор вполне подходит. Перейдем теперь к плавке.
Левитационная плавка
Плавка во взвешенном состоянии – довольно увлекательное занятие. В качестве образца для плавки выбран кусочек алюминия весом 2.6 гр. Отдельные кадры, иллюстрирующие процесс плавки, приведены на рис.21. Полное видео плавки можно загрузить по ссылке ниже.
Рис.21. Процесс плавки во взвешенном состоянии.
Во взвешенном состоянии образец может находиться неограниченно долго. Положение его довольно устойчивое. Оценка температуры верхушки образца (в расплавленном состоянии при максимальной мощности) была сделана тем же пирометром ПД-4-02 без поправки на излучательную способность перегретого алюминия. Она равна 1150-1200°С.
Заключение и выводы
Двухнедельная работа с описанным в данной статье лабораторным инвертором показала, что эта конструкция вполне может «трудиться» в исследовательской лаборатории в качестве устройства для индукционного нагрева и плавки. За это время было расплавлено более полусотни образцов алюминия, около десятка образцов стали и несколько образцов меди. Большинство плавок алюминия были выполнены во взвешенном состоянии. Масса образцов 2-3 гр. Масса стальных и медных образцов тоже составляла несколько грамм. Плавки проводились как в графитовых тиглях, так и без них.
Инвертор работал стабильно. Во всех этих экспериментах не случилось никаких нештатных или аварийных ситуаций. Никаких перегревов или взрывов транзисторов и других компонентов также не произошло. По сути дела, работа с инвертором ничем не отличалась от работы с любым другим несложным лабораторным прибором.
Так что можно считать, что цель создания простого лабораторного инвертора для индукционного нагрева и плавки небольших образцов металлов достигнута.
Естественно, в процессе разработки и практической работы с инвертором накопился список необходимых модернизаций и улучшений, которые желательно провести в ближайшем будущем. Первые в очереди из них перечислены ниже.
- 1. Выпрямитель. Хотелось бы убрать громоздкий регулятор напряжения на ЛАТРе и поставить что-нибудь более современное, компактное и главное – с запасом по мощности.
2. Модуль управления. Желательно удешевить «оконечники» (усилители) и выбрать более доступные компоненты. В принципе, здесь ничего сложного нет. Нужно просто проанализировать существующие в большом количестве решения и выбрать наилучшее.
3. Трансформаторные развязки. В данной конструкции мы использовали самые простые решения. Мы «заплатили» за эту простоту качеством сигналов и сравнительно пологими фронтами импульсов. В принципе, работать можно, транзисторы греются приемлемо. Однако, лучше поработать в этом направлении дополнительно.
4. Силовой модуль. Желательно увеличить мощность инвертора до 4-5 кВт. В принципе, можно увеличить мощность в два раза, практически ничего не меняя в схемотехнике. Для этого достаточно перейти с полумоста на полный мост. Добавится еще один кулер с парой транзисторов с «обвязкой» и пара дополнительных обмоток на импульсном трансформаторе блока управления.
Поскольку лабораторный инвертор имеет модульную структуру, то все эти модификации легко делать параллельно, не выводя инвертор надолго из работы. Возможно, в результате этих модификаций удастся создать действительно «бюджетный» вариант лабораторного инвертора. Это способствовало бы более широкому внедрению технологий индукционного нагрева в лабораторную практику.
Литература
- Семенов Б.Ю. Силовая электроника: от простого к сложному. – М.: СОЛОН-Пресс, 2005. – 416 с.
- Мелешин В.И. Транзисторная преобразовательная техника. М. Техносфера, 2005. – 632 с.
- Шандренко Д.А. Транзисторный регулятор напряжения.
http://electroscheme.org/2007/08/13/tranzistornyjj_reguljator_naprjazhenija.html
или
http://www.radiolub.orsk.info/Shems/Shems2/tr_reg.htm - Design Tips DT92-2A: High Current Buffer for Control IC’s.
http://www.irf.com/technical-info/designtp/dt92-2.pdf
См. русский перевод: Мощный буфер тока для управления затворами МОП-транзисторов
http://vcoder.flyback.org.ru/electronics/power_buffer/Power%20buffer.pdf - Фогель А.А. Индукционный метод удержания жидких металлов во взвешенном состоянии. Л. Машиностроение, 1979. – 104 с.
- Глебовский В.Г., Бурцев В.Т. Плавка металлов и сплавов во взвешенном состоянии. М. Металлургия, 1974. – 176 с.
Благодарности
Работа выполнена при частичной финансовой поддержке ОХНМ РАН (проект №5.5.3) и ГК № 02.740.11.0269.
Приложение
Рис.22. Общая схема инвертора.
Самодельный индукционный нагреватель Схема DIY
Схема индукционного нагревателяКак работают эти индукционные нагреватели? Мы рассмотрим схему и шаг за шагом объясним, как создается колебательный сигнал, как индуцируется ток и как нагревается металл. Наконец, мы используем эту схему и устанавливаем самодельную версию и смотрим, работает ли она на нагрев некоторых металлов. Так что посмотрим …
ЧАСТЬ 1 — Коммерческий модуль
Во-первых, чтобы узнать и сопоставить сигналы, я купил один из этих коммерческих модулей индукционного нагревателя.Этот рекламируется как 1000Вт mdoule. Мы видим огромные конденсаторы, несколько катушек и еще несколько компонентов, а на выходе — огромную катушку из толстой медной проволоки. Эта выходная катушка создаст мощное колеблющееся магнитное поле, которое будет нагревать металлы, и мы увидим, как это сделать. Я делаю еще одну катушку из медного провода и помещаю ее рядом с катушкой индукционного нагревателя, и, как вы можете видеть на осциллографе, у нас есть колебательный сигнал около 100 МГц.
Чтобы понять, как этот модуль нагревает металлы, нам нужно понять 3 вещи.Во-первых, как магнитные поля могут индуцировать токи внутри металлов и обратный процесс, как токопроводящие провода будут создавать магнитные поля. Затем нам нужно увидеть, как резонанс этих катушек и конденсаторов будет создавать высокочастотные сигналы и, наконец, как ток будет нагревать металлы. Как вы можете видеть ниже, после включения модуля эти высокочастотные и мощные колебания нагревают металл до ярко-красного цвета всего за несколько секунд.
ЧАСТЬ 2 — Закон Фарадея
Закон индукции Фарадея — это основной закон электромагнетизма, предсказывающий, как магнитное поле будет взаимодействовать с электрической цепью, создавая явление электродвижущей силы, называемое электромагнитной индукцией.Это основной принцип работы трансформаторов, индукторов и многих типов электродвигателей, генераторов и соленоидов. Таким образом, движущийся магнит будет создавать изменения магнитного потока внутри катушки, и тем самым мы можем индуцировать ток внутри катушки. Но что еще может формировать кореатирование магнитных полей?
Что ж, еще один компонент, помимо amgnet, который также создает магнитные поля, — это катушка. Да, катушка может производить обратный процесс индукции тока. Если мы подаем ток через катушку, будет создано магнитное поле, поэтому нам не нужны магниты.Катушка могла создавать магнитное поле и наводить ток во второй катушке, как трансформаторы. Итак, теперь мы знаем, как индуцировать ток, и этот ток будет нагревать наш металл. Ниже вы можете увидеть, как я передаю сигнал от одной катушки к другой.
ЧАСТЬ 3 — Частота резонанса
В этом примере мы будем использовать параллельно катушку и конденсатор. Это называется резервуаром LC, и если мы ударим по нему электроникой, он будет резонировать на своей резонансной частоте.Итак, если я приложу небольшой импульс напряжения, и они отключат соединение, это создаст быстро колеблющийся сигнал. Я подключаю конденсатор и катушку параллельно и очень быстро прикасаюсь к одному кабелю с напряжением 12 В к этому резервуару LC. Посмотрите ниже, что происходит. После прикосновения к резервуару LC я получаю на осциллографе первый осциллирующий сигнал, который медленно затухает. Итак, теперь мы получаем наши высокочастотные и мощные колебания, которые позже индуцируют ток внутри металла. Но наша схема работает немного иначе.Для этого давайте взглянем на схему базового и простого модуля индукционного нагревателя.
ЧАСТЬ 4 — Схема
В этом примере мы будем использовать параллельно катушку и конденсатор. Это называется резервуаром LC, и если мы ударим по нему электроникой, он будет резонировать на своей резонансной частоте. Итак, если я приложу небольшой импульс напряжения, и они отключат соединение, это создаст быстро колеблющийся сигнал. Я подключаю конденсатор и катушку параллельно и очень быстро прикасаюсь к одному кабелю с напряжением 12 В к этому резервуару LC.Посмотрите ниже, что происходит. После прикосновения к резервуару LC я получаю на осциллографе первый осциллирующий сигнал, который медленно затухает. Итак, теперь мы получаем наши высокочастотные и мощные колебания, которые позже индуцируют ток внутри металла. Но наша схема работает немного иначе. Для этого давайте взглянем на схему базового и простого модуля индукционного нагревателя.
Итак, как вы можете видеть на схеме выше, у нас на выходе 3 катушки. Пока не обращайте внимания на катушку L3, потому что это будет выходная катушка, которая будет создавать магнитное поле.У нас есть 2 катушки, L1 и L2, и один конденсатор, C1. У нас будет резонанс, как и раньше, но на этот раз он будет другим и никогда не прекратится. Как вы можете видеть, у нас также есть два диода, D1 и D2, которые подключены к затвору двух транзисторов, T1 и T2. Когда сигнал сначала колеблется на C1, на одной стороне C1 будет положительное напряжение, а на другой стороне C1 — отрицательное напряжение. Таким образом, один диод будет пропускать ток, а другой — нет. Таким образом, один транзистор будет включен, а другой выключен.Но буквально через мгновение из-за этого процесса полярность на C1 изменится, и это активирует второй транзистор и выключит другой. И этот процесс будет повторяться снова и снова, и это изменит поток тока внутри катушки L3, потому что, как вы можете видеть, один enf этой катушки подключен к 15 В, а другой конец будет подключен к отрицательному или положительному, и тем самым будет создаваться колебательный ток. Это создаст колеблющееся магнитное поле.
Помогите мне, поделившись этим постом
Проектирование и изготовление индукторов для индукционной термообработки
Информация
Авторы: Р.Гольдштейн, В. Штур и М. Блэк
Публикация: ASM International, 2014 г.
Купить Справочник ASM Том 4C
ДЛЯ ИНДУКЦИОННОЙ ПЛАВКИ И МАССОВОГО НАГРЕВА первые индукционные змеевики изготавливались из медных трубок, намотанных на оправку в несколько витков. Первые катушки индукционной термообработки были разработаны для закалки коленчатого вала в 1930-х годах (рис. 1, 2) (ссылки 1–4).В отличие от катушек плавления и нагрева массы, индукционные катушки для термообработки подвергались механической обработке. Эти индукторы состояли из двух частей с шарниром на одной стороне, который открывался и закрывался вокруг шейки коленчатого вала. На внутреннем диаметре индукционной катушки просверливались закалочные отверстия для закалки детали после нагрева. Такое развитие новаторского стала кульминацией многих лет напряженной работы большого коллектива и четко продемонстрировали различные требования к индукционной термообработке по сравнению с плавлением и массовым нагревом.
На начальном этапе разработки катушек для индукционной термообработки, особенности индукционной катушки в основном определялись с помощью аналитических, экспериментальных и экспериментальных методов. Концепции индукционных катушек были созданы физиками. Расчеты параметров катушки определялись путем ручного решения сложных уравнений.Конструкции индукционных катушек изначально создавались чертежниками по чертежам. Большинство индукторов были изготовлены мастерами с использованием комбинации медных трубок, компонентов, обработанных вручную, и медных пластин, спаянных вместе. Оптимизация катушки была произведена на основе экспериментальных результатов методом проб и ошибок, поскольку испытания и модификации заняли гораздо меньше времени, чем расчеты (ссылки 1, 5).
Хотя многие катушки для индукционной термообработки по-прежнему производятся таким образом, инструменты для проектирования и изготовления сложных индукторов для индукционной термообработки с годами претерпели значительные изменения.Для многих типов приложений предпочтительный тип индукционной катушки уже известен на основе многолетних эмпирических данных. Во многих случаях сравнения с известными результатами могут даже определить размеры индукционной катушки, которые приведут к успешной схеме термообработки, значительно ограничивая время экспериментальных испытаний и сокращая циклы разработки (ссылки 1, 5–9).
Для новых приложений или оптимизации существующих, инструменты компьютерного моделирования включаются в процедуру проектирования индукционной катушки.Сложное программное обеспечение, работающее на персональных компьютерах, способно производить расчеты за секунды, минуты или часы, на выполнение которых вручную потребовались бы дни, недели или месяцы. Во многих случаях аналитических формул для сложных катушек не существует, и единственный способ произвести расчеты перед испытаниями — это использовать программу компьютерного моделирования. Конструкции индукционной катушки и технологические рецепты проходят «виртуальное» тестирование для определения результирующих тепловых характеристик. Сегодня (2013 г.) во многих случаях виртуальные тесты и оценки можно проводить быстрее и с меньшими затратами, чем физические (ссылки 10–12).
Процесс конструирования механической индукционной катушки также развивался с годами. В то время как первоначальные чертежи были сделаны вручную, индукционные катушки теперь нарисованы и детализированы с использованием пакетов автоматизированного проектирования (САПР). За последние несколько лет интерактивность пакетов CAD увеличилась с пакетами программного обеспечения для автоматизированного производства (CAM). Во многих случаях чертежи индукционной катушки могут быть перенесены из чертежа САПР в программу САМ в машину с числовым программным управлением.Это создает возможность для большей повторяемости сложных индукционных катушек (см. Ссылки 13, 14).
Методы индукционной термообработки
Сегодня (2014 г.) существует множество различных типов индукционных теплообменников. Тип катушки индукционной термообработки зависит от процесса индукционной термообработки. Все процессы индукционной термообработки можно разделить на две категории: однократная обработка и сканирование, в зависимости от того, движется ли индукционная катушка (за исключением вращения) относительно детали во время процесса нагрева.Ниже приводится краткое описание, поскольку более подробная информация об оборудовании для индукционной термообработки обсуждается в других разделах этой статьи.
При однократной индукционной термообработке (рис. 3) положение индукционной катушки относительно нагреваемой длины детали не изменяется. Во многих случаях однократного нагрева деталь вращается во время нагрева и закалки, чтобы обеспечить однородность рисунка. В семействе приложений для однократной термообработки существует несколько разновидностей конфигураций индукционных катушек в зависимости от механизма закалки.
Механически обработанные установки интегральной закалки (MIQ) имеют закалку, встроенную прямо в саму индукционную катушку. Наиболее распространенный метод заключается в том, чтобы закалка проводилась через саму медную катушку. Эти индукторы обычно имеют отдельные карманы для водяного охлаждения и закалки. В некоторых других случаях закалка может подаваться через концентратор магнитного потока.
Другой тип установки для однократной термообработки — закалка на месте (рис.4). Закалка на месте аналогична MIQ, потому что закалочное кольцо является частью сборки индукционной катушки. Что отличает гашение на месте от установок MIQ, так это то, что гаситель не предназначен для использования в качестве активного компонента индукционной цепи.
Конечная разновидность катушки индукционной термообработки с однократной обработкой — это отдельная закалка (рис. 5). В этих установках гаситель не является частью сборки индукционной катушки. В установках с раздельной закалкой закалка часто осуществляется на другой станции или в другом месте в машине.Эти системы распространены, когда желательна задержка между нагревом и закалкой для пропитывания тепла.
Помимо одиночного выстрела, другим типом индукционной машины является сканирование (рис. 6) (см. 5, 9). При закалке сканированием индукционная катушка перемещается относительно детали. Подобно одноконтурным индукторам, сканирующие индукторы могут быть как MIQ, так и гасящие на месте. Также могут быть раздельные закалки, но это встречается реже.
Соображения при проектировании индуктора
Змеевики для индукционной термообработки доступны во многих формах и размерах и должны выполнять множество задач в данной области применения индукционной термообработки.В зависимости от области применения требования к конструкции индукционной катушки включают:
- Соответствие спецификациям термообработки при желаемой производительности
- Быть достаточно прочным, чтобы выдерживать производственные изменения
- Установить в индукционную машину
- Имеют электрические параметры, соответствующие индукционному источнику питания.
- Доставить закалку
- Иметь удовлетворительную жизнь
- Имеют удовлетворительную эффективность
- Быть повторяемым от индуктора к индуктору
При разработке новой катушки индукционной термообработки и процесса первый вопрос заключается в том, будет ли компонент производиться на существующей системе или должна быть построена новая машина.Во многих случаях производитель запчастей хочет разработать новую оснастку для существующей машины с резервной мощностью. Это снижает степень свободы и может усложнить процедуру проектирования индукционной катушки, поскольку для существующей машины потребуется неоптимальная частота или тип катушки (ссылка 16).
Чтобы определить возможность использования существующего оборудования, необходимо провести анализ детали, подлежащей термообработке. Материал детали, предварительная обработка, геометрия, производительность и характеристики термообработки — все это играет важную роль.Материал детали и предшествующая обработка определяют минимальную температуру термообработки, а также время, необходимое для охлаждения. Геометрия детали и спецификации термообработки указывают, сколько энергии требуется, каковы предпочтительные диапазоны частот и какой тип индукционного метода (например, одиночный выстрел, сканирование) лучше всего подходит для применения. Наконец, производительность определяет, сколько мощности и / или сколько шпинделей или станций требуется.
Более подробная информация по этой теме представлена далее в этой и других статьях этого тома.Обсуждение в этой статье ограничивается взаимосвязью между этими факторами и конструкцией индукционной катушки.
Текущий поток в детали
Вихревые токи являются основным источником рассеяния мощности в большинстве приложений индукционной термообработки. Вихревые токи, как и все другие электрические токи, должны образовывать замкнутый контур. В большинстве случаев ток в заготовке повторяет форму катушки индукционного нагрева из-за эффекта близости.Плотность мощности в данном сечении заготовки зависит от плотности тока. На плотность тока могут влиять электромагнитные эффекты (конечный эффект, краевой эффект и т. Д.), Наличие концентраторов магнитного потока, ширина меди, геометрия детали и расстояние между катушкой и заготовкой (сцепление зазор).
Следующим шагом в процессе проектирования катушки является определение того, как будет протекать ток в детали. Это очень важно, особенно в случаях, когда изменяется геометрия.Некоторые общие геометрические изменения, встречающиеся при индукционной термообработке, — это галтели, поднутрения, углы, уступы, фаски, шлицы, шпоночные пазы и отверстия для масла. Нагрев этих критических областей по сравнению с соседними сильно зависит от типа индукционной катушки и частоты нагрева.
Здесь обсуждаются первые основные варианты протекания тока, будь то в плоскости изменения геометрии или перпендикулярно изменению геометрии. Когда ток перпендикулярен направлению изменения геометрии, естественная тенденция заключается в том, что ток концентрируется на поверхности детали, которая находится ближе к индукционной катушке, из-за эффекта близости.Дополнительное соображение заключается в том, что вблизи концов более близкой секции к тому месту, где расстояние увеличивается, происходит либо уменьшение, либо увеличение нагрева, в зависимости от того, является ли часть магнитной или немагнитной из-за электромагнитного концевого эффекта. Для закалочных работ есть некоторое увеличение, а для отпуска — уменьшение. Величина изменения зависит от частоты (рис. 7) (см. 12).
Когда ток идет в направлении изменения геометрии, ток протекает под индуктором по ширине, приблизительно равной ширине индукционной катушки.Когда происходит изменение размеров, текущий поток следует за контуром детали через это изменение размеров. В точке изменения размера изменение нагрева определяется электромагнитным краевым эффектом. Краевой эффект обычно меньше, чем краевой эффект, что означает меньшую разницу температур в этой области. По мере увеличения расстояния между катушкой и деталью величина тока остается почти такой же, но ток начинает течь по большей длине. Менее концентрированный нагрев приводит к снижению удельной мощности (рис.8). Разница между плотностями мощности обычно меньше, чем когда ток идет в направлении изменения геометрии, чем когда он перпендикулярен.
Чтобы проиллюстрировать эту концепцию, рассмотрим случай простого шпинделя с одной обоймой подшипника и заплечиком (рис. 9). Рисунок термообработки — это светло-серая область. Эта часть могла нагреваться либо сканированием, либо одиночным выстрелом. Сканирующий индуктор почти наверняка будет окружающим индуктором, длина которого меньше длины рисунка.В рамках одного цикла его также можно упрочнить с помощью механически обработанного окружающего индуктора или так называемого окружающего / нециркулирующего индуктора.
Для окружая индуктор (сканирование или одного выстрела), электрический ток в катушке и частях, как правило, принимает кратчайший путь и поток вдоль внутреннего диаметра индуктора диаметра и опорной поверхности. Чтобы компенсировать эту тенденцию, необходимо изменять зазор между катушкой и деталью, чтобы использовать эффект близости, чтобы компенсировать меньшую длину тока.В области радиуса происходит переход от меньших зазоров на фланце к большим зазорам по диаметру. Для индуктора с однооборотной механической обработкой конструкция катушки в этой области предполагает тонкий баланс для достижения достаточной глубины галтели без слишком глубокого нагрева в зоне подшипника непосредственно над галтелем. Для корпусов глубиной, которые велики по сравнению с поперечным сечением, это становится более трудным, поскольку температура ядра увеличивается, что приводит к уменьшению кондуктивного отвода тепла.Для более короткой сканирующей катушки эта задача упрощается за счет использования концентратора магнитного потока, который направляет ток вниз от вала в радиус детали (рис. 10).
Индукторы с кольцевым / невымканием состоят из нескольких частичных контуров, соединенных медными шинами, которые примыкают к поверхности детали (рис. 11). Для этих индукторов деталь должна вращаться, чтобы обеспечить равномерный нагрев.Для такой простой детали, как эта, вероятно, потребуется только одна верхняя и одна нижняя частичные петли. В этом случае ток протекает под витками катушки и повторяет контур катушки в детали. Таким образом, верх и низ рисунка контролируются концевыми петлями, а рельсы определяют рисунок в центральной области. Следуя по рельсам по поверхности детали, ток течет по радиусу.
Это упрощает получение более однородного контура с помощью линейного индуктора, чем с помощью кольцевого индуктора для данного типа деталей (рис.12).
Влияние частоты
Частота тока индукционного нагрева оказывает сильное влияние на индукционную катушку и конструкцию процесса. Это влияет на требуемую мощность, время нагрева, потери в катушке, локальное распределение мощности в детали и требуемую опору конструкции. В этом разделе дается краткий обзор влияния частоты, поскольку он более подробно рассматривается в других статьях этого тома.
Часто такая же глубина корпуса может быть достигнута в широком диапазоне частот. Для больших деталей либо в полностью магнитном (холодная сталь), либо в немагнитном (горячая сталь) состоянии, плотность тока максимальна у поверхности и экспоненциально спадает по глубине. Специалисты по индукционному нагреву используют значение, называемое эталоном или глубиной кожи, связанное с этим поведением. Формула для эталонной глубины является:
где d — эталонная глубина, k — постоянная, зависящая от единиц измерения, r — удельное электрическое сопротивление, µ — магнитная проницаемость, f — частота.
В больших телах 63% тока и 86% мощности приходится на первую контрольную глубину (рис. 13) (см. Ссылки 6, 17). Это приводит к предположению, которое обычно делается при оценке параметров, что вся мощность генерируется в d-слое.
В приложениях для индукционной закалки распределение тока и плотности мощности отличается от предсказываемой по эталонной глубине, потому что магнитная сталь ниже точки Кюри все еще взаимодействует с магнитным полем за немагнитным горячим поверхностным слоем (см. 17).Чтобы добиться такой же глубины корпуса на деталях с более низкими частотами, можно ожидать более высоких уровней мощности, более короткого времени нагрева и более низких температур поверхности. По мере увеличения частоты уровни мощности должны быть уменьшены, а время нагрева увеличено для достижения той же глубины корпуса без перегрева поверхности. Количество требуемой энергии зависит от баланса между тепловыми потерями (поглощение тепла), КПД змеевика и мощностью, индуцированной в материале на глубине корпуса.
Помимо процесса, частота также влияет на то, как ток течет в самой индукционной катушке.На практике наиболее эффективная толщина проводящей части стенки трубы (d1) принимается равной d1 ≈ 1,6d1. Это соотношение основано на решении одномерной задачи. Стенка трубки индукционного змеевика меньше 1,6d1 приводит к снижению эффективности змеевика; кроме того, в некоторых случаях стенка трубы может быть намного толще по сравнению с вышеупомянутым соотношением. Это связано с тем, что использование толщины стенки трубки 0,25 мм (0,01 дюйма) с механической точки зрения может оказаться непрактичным. Некоторые рекомендации по толщине стенок приведены в Таблице 1 (Ссылка 9).
Частота также влияет на электродинамические силы, которые влияют на механическую конструкцию индукционной катушки. Электродинамические силы при индукционном нагреве имеют две составляющие: статическую и динамическую. Статический компонент сначала притягивает индуктор к детали в холодном магнитном состоянии, а затем отталкивает его от детали, когда она немагнитна. Динамическая составляющая колеблется вокруг статической составляющей с удвоенной частотой электрического тока (рис. 14).Уровень силы в системе пропорционален квадрату тока катушки; то есть силы прямо пропорциональны мощности (см. 17).
Когда деталь электрически толстая (то есть диаметр или толщина намного больше, чем эталонная глубина), ток, необходимый для той же мощности, пропорционален обратному корню четвертой степени отношения частот (уравнение 2).Из этого уравнения видно, что ток, необходимый для того же количества мощности, уменьшается с увеличением частоты:
Таблица 1 Стандартная толщина стенки медных трубТолщина медной стенки | ||
---|---|---|
мм | в | Частота, кГц |
0,75–1 | 0,032–0,048 | 450–50 |
1-2 | 0.048–0.090 | 25–8,3 |
1,5–4 | 0,062–0,156 | 10–3 |
4–6,5 | 0,156–0,250 | 3–1 |
Из-за этого электродинамические силы выше на более низких частотах. Кроме того, уровни мощности обычно имеют тенденцию быть выше на более низких частотах, что еще больше увеличивает электродинамические силы.Следовательно, чем ниже частота, тем более прочной должна быть механическая конструкция индукционной катушки. Помимо большей толщины медных стенок, поддерживающая конструкция змеевика также должна быть более прочной, чтобы выдерживать механическую нагрузку, которой подвергается змеевик. Особенно это касается однозарядных катушек.
Контроль нагрева в различных областях детали
Во многих случаях индукционной термообработки требуется выборочная закалка одних участков детали и не закалка других.В других случаях желательна разная глубина корпуса в разных областях детали. Часто бывает необходимо достичь этих различных целей в одной и той же операции индукционной термообработки.
В приложениях для закалки при сканировании эти отклонения обычно компенсируются регулировкой мощности и скорости сканирования при прохождении детали через индукционную катушку. Для однозарядных индукционных катушек необходимо учесть эти изменения в конструкции катушек. Существует три основных инструмента для настройки конструкции катушки: зазор муфты, медный профиль катушки и контроллеры магнитного потока.
Муфтовый зазор — это наиболее простой способ управления тепловым рисунком. Чем ближе змеевик к детали, тем больше интенсивность нагрева в этой области по сравнению с другими участками. Это связано с тем, что ток в детали протекает в более узкой полосе, более близкой к таковой в катушке индукционного нагрева. С увеличением зазора связи ток распространяется на большую длину, что приводит к снижению плотности тока и плотности мощности.
Другой метод управления тепловым рисунком — это изменение профиля поперечного сечения медной катушки.Участок витка катушки, обращенный к детали и пропускающий большую часть тока, называется тепловой поверхностью катушки. Для индукционных катушек с одной поверхностью нагрева профилирование мощности достигается за счет изменения геометрии поверхности нагрева (рис. 15). Например, чтобы сократить переходные зоны на концах катушки, обычно в середине катушки имеют больший зазор, чем на концах. Этот метод обычно используется для управления концом тепловой обработки рисунка, где желательно сохранить этот рисунок из поднутрения или защелки кольцевой канавки.Это помогает компенсировать расхождение магнитного потока и дополнительные тепловые потери около конца катушки.
Примером этого является упрочнение подшипника коленчатого вала с помощью кольцевой катушки (технология «грейфер» или «Sharp-C», ссылка 9). Используя программу компьютерного моделирования Flux 2D, можно провести сравнение, чтобы увидеть влияние профилирования меди на распределение температуры.На рисунке 16 показан упрощенный пример катушки для этой технологии. Линии на детали обозначают минимальную и максимальную глубину корпуса. Частота для этого сравнения 50 кГц. Зазор муфты составляет 2 мм (0,08 дюйма), а змеевик имеет тонкие пластины концентратора Fluxtrol 50 с обеих сторон для предотвращения сцепления с боковыми стенками. На расстоянии 2,5 мм (0,10 дюйма) от каждого конца катушки медь утоплена на 1 мм (0,04 дюйма). Эту катушку сравнивают с катушкой с точно такой же геометрией, за исключением того, что центральная часть индуктора не утоплена.Время нагрева для обоих случаев составляет 4 с.
Распределение температуры в змеевике без профилирования показано на рис. 17. Область высокой температуры начинает сужаться задолго до окончания нагреваемой поверхности и минимальной необходимой длины рисунка. Температура поверхности уже высока, поэтому невозможно увеличить нагрев для удлинения рисунка.
На рисунке 18 показано распределение температуры для змеевика с профилированной поверхностью. Из этого изображения видно, что зона высокой температуры простирается значительно дольше, чем для змеевика без профилирования. Минимальная ширина термообработки соответствует более низкой максимальной температуре поверхности. Для лучшего сравнения двух случаев на рис. 19 сравнивается температура поверхности по длине.
Для змеевиков с несколькими нагревательными поверхностями или секциями, помимо зазора муфты, тепловую структуру также можно контролировать, изменяя ширину тепловой поверхности от секции к секции. Плотность мощности в детали пропорциональна квадрату плотности тока.Если предположить, что весь ток в катушке передается на деталь и протекает непосредственно под поверхностью нагрева индукционной катушки, то плотность тока будет обратно пропорциональна ширине поверхности нагрева. Это означает, что плотность мощности будет пропорциональна обратному квадрату ширины тепловой поверхности. Реальный эффект значительно меньше, потому что не весь ток проходит на поверхности нагрева, а часть потока вне катушки соединяется с деталью.
При нагреве круглой детали линейным змеевиком эффект не такой сильный из-за неравномерного зазора между прямоугольным змеевиком и круглой частью.
Чтобы продемонстрировать влияние ширины поверхности нагрева, проводится сравнение для нагрева пластины толщиной 12,7 мм (0,5 дюйма) с трубкой 9,5 на 12,7 мм (на 0,5 дюйма) и квадратным диаметром 12,7 мм (0,5 дюйма). медная труба. Программа компьютерного моделирования Flux 2D используется для расчета электромагнитной задачи. Верхняя половина пластины имеет свойства стали выше точки Кюри, а нижняя половина — свойства холодной стали. Частота 10 кГц, зазор связи установлен на 3.2 мм (⅛ дюйма). Для обеих катушек используется одинаковый ток 3000 А. Распределение магнитного поля и плотности мощности для обоих случаев показано на рис. 20. В идеале плотность мощности должна быть на 78% выше для поверхности нагрева 9,5 мм (⅜ дюйма) по сравнению с поверхностью 12,7 мм (0,5 дюйма). В действительности разница в максимальной плотности мощности составляет всего около 17%. Это происходит из-за большого количества тока, протекающего в части за пределами тепловой поверхности катушки.
Более эффективный способ контролировать распределение тепла по длине индуктора — использовать регуляторы магнитного потока. Для индукционной термообработки наиболее распространенными материалами, используемыми в качестве регуляторов магнитного потока, являются листы кремнистой стали и магнитомягкие композитные материалы. Концентраторы магнитного потока обеспечивают прохождение магнитного поля по пути с низким сопротивлением.В результате магнитное поле перестает быть широко распределенным в пространстве и концентрируется вокруг катушки. Это приводит к тому, что почти весь ток, протекающий по боковым стенкам медной катушки, проталкивается вниз к нагревательной поверхности. Это приводит к тому, что ток в детали более сильно концентрируется под поверхностью нагрева катушки.
Чтобы продемонстрировать эффект концентратора, сравнивается нагрев пластины толщиной 12,7 мм (0,5 дюйма) с помощью пластины 12.Квадратная медная трубка 7 мм (0,5 дюйма) с применяемым С-образным концентратором и без него. В качестве материала, концентрирующего флюс, используется Fluxtrol A. Остальные условия такие же, как и в случае исследования изменения поверхности нагрева. Распределение магнитного поля и плотности мощности для катушки с концентратором показано на рис.21.
Магнитное поле и плотность мощности намного более сконцентрированы, когда применяется контроллер магнитного потока.Кривые поверхностной плотности мощности слева направо от детали показаны на рис. 22 для всех трех случаев. Понятно, что применение регулятора магнитного потока является более сильным методом управления тепловым рисунком по длине катушки, чем использование профилирования меди. Также можно более плавно распределить рисунок между различными областями, профилируя полюса концентратора, вместо того, чтобы иметь ступеньки в индукционной катушке. Для линейных катушек, нагревающих круглую деталь, влияние как ширины поверхности нагрева, так и регулятора магнитного потока менее драматично, чем в случае плоской пластины, из-за отклонения части от катушки.Более подробная информация о выборе и использовании контроллера магнитного потока содержится в статье «Контроллеры магнитного потока в индукционном нагреве и плавлении» в этом томе.
Представление детали к индуктору
При первоначальной конструкции индуктора необходимо рассмотреть способ удержания детали и подачи ее к индуктору.Некоторые соображения:
- Какой размер и вес детали?
- Что такое процесс закалки или отпуска?
- Это будет сканирование или одиночный снимок?
- Нужно ли вращать деталь во время обработки?
- Какая скорость производства?
- Какое подъемно-транспортное оборудование необходимо?
- Как и где его можно провести?
- Каковы требования в киловаттах и частота электросети?
- Как его загрузить в индуктор: вручную или механически?
- Какой метод закалки: распыление, окунание, ванна с мешалкой, неподвижный воздух или продувка воздухом?
- Какие типы удерживающих устройств следует использовать: центры, патрон или специальные захваты?
В зависимости от процесса может быть несколько механических методов захвата и подачи детали к индуктору.В высокопроизводительных приложениях вся машина может быть спроектирована и построена для конкретного процесса обработки материалов. Однако в условиях ограниченного производства можно использовать простое подъемно-поворотное устройство внутри охлаждающего резервуара. В любом случае необходимо принять решение о том, как удерживать деталь.
Удержание и демонстрация детали могут быть такими же простыми, как зажим детали, или сложными, например, необходимость удерживать и вращать деталь, пока она полностью нагрета. В любом случае электромагнитные поля от индукционной катушки следует учитывать при проектировании удерживающего устройства и его влиянии на деталь.Магнитная сталь в непосредственной близости от индуктора нагревается; поэтому разумно оставлять достаточное воздушное пространство вокруг индуктора. Обычные немагнитные удерживающие детали материалы, такие как нержавеющая сталь серии 300, алюминий и латунь, могут нагреваться в непосредственной близости от индуктора, но с менее значительным эффектом. Определенные виды керамики, разработанные специально для конкретного применения, также являются отличными запорными приспособлениями.
Например, типичным для индукционной закалки является метод подъема и вращения в закалочной ванне.Деталь разумного размера и формы, такая как шпиндель автомобильного колеса, устанавливается на держатель детали из немагнитной нержавеющей стали. Верхний центр из того же материала используется для стабилизации детали во время вращения. Индуктор предназначен для термической обработки колеса шпинделя установлен на монтажной ногу питания внутри резервуара. Распылительная закалка является неотъемлемой частью индуктора. Шпиндель колеса загружается в держатель и поднимается к индуктору. Начинается вращение, подается индукционная мощность, шпиндель круга нагревается, а затем сразу же гасится, и шпиндель опускается и разгружается.Весь этот процесс занимает менее 30 с. В высокопроизводительном приложении производительность может быть увеличена за счет дополнительных тепловых пунктов, использующих различные системы транспортировки материалов.
Хотя многие примеры термообработки являются типичными, когда детали большие и / или геометрически сложные, представление индуктора может потребовать инженерных решений. Для многих деталей, закаленных индукционным нагревом, вращение во время нагрева выравнивает схему термообработки. Некоторые детали, такие как рулевые тяги грузовика в форме буквы «J», не могут быть повернуты на 360 градусов из-за того, что J-образный крюк мешает индуктору; тем не менее, для выравнивания закаленного рисунка требуется некоторая форма вращения, чтобы равномерно нагреть шейку подшипника на конце J-образного крюка.Для этого держатель детали соединяется с кривошипом и заставляется колебаться на 210 во время цикла закалки, точно имитируя полное вращение.
Большие и тяжелые детали могут быть связаны с конкретным применением в том, что касается их представления в индукторе, что требует продуманной конструкции, выбора материалов и испытаний для проверки результатов нагрева. В некоторых установках к детали необходимо поднести индуктор. Сложные конструкции включают в себя роботов, перемещающих индуктор по пути, который необходимо упрочнить.Катушка индуктивности и трансформатор иногда перемещаются вместе с помощью роботов, а в других случаях, в зависимости от мощности и частоты, можно использовать гибкий кабель, соединенный с индуктором. В других приложениях для нагрева можно использовать переносное устройство для индукционного нагрева. Все приложения зависят от требуемой мощности, размера детали и нагреваемых участков.
Структура индуктора
Для низкочастотного и / или высокой плотности мощности индукции термообработки приложений, электродинамические силы сильны и индукционная катушка требует дополнительной механической опорной конструкции.Механическая опорная конструкция также требуется, если индукционная катушка тяжелая или изготовлена из тонкостенных медных трубок. Некоторые распространенные типы индукторов, в которых используются механические опоры, включают однозарядные индукторы для нагрева валов или штоков, многооборотные индукционные катушки, индукционные катушки без вращательной симметрии и приложения, в которых индуктор нагревает поверхность, перпендикулярную монтажным пластинам шины.
Для катушек индукционной термообработки компоненты механической опоры включают в себя стойки со стойками, стопорные кольца, монтажные пластины и компоненты для соединения катушки с закалочными кольцами.В подавляющем большинстве случаев материалы, используемые для конструкции индуктора, изготовлены из высокотемпературных пластиковых компонентов, армированных волокном. В некоторых крайних случаях, например, при использовании длинных однозарядных катушек для упрочнения полуоси, усиленная волокном опорная плита может дополнительно поддерживаться алюминиевым корпусом или каналом. В этом случае, следует соблюдать осторожность, чтобы изолировать индуктор и любые шпильки из проводящего корпуса опоры.
Одним из наиболее сложных приложений индукции, требующим прочной системы механической поддержки, является закалка вращающегося коленчатого вала с помощью U-образных индукторов (рис.23). Расстояние от выхода трансформатора до зоны нагрева катушки должно быть относительно большим, чтобы противовесы коленчатого вала не задели трансформатор. Это проблема, потому что в катушке этого типа электродинамические силы велики и действуют в нескольких направлениях. На индукционную катушку также действует механическая нагрузка, поскольку узел индуктора контактирует с деталью во время вращения.
Когда коленчатый вал холодный, витки тянутся к шейке подшипника и боковым стенкам коленчатого вала.Когда деталь находится выше точки Кюри, силы меняются на противоположные, и индуктор отталкивается от боковых стенок и от диаметра подшипника.
Из-за этих многочисленных проблем конструкция состоит из нескольких частей. Снаружи индуктора обычно есть две латунные или алюминиевые боковые пластины. Все компоненты прикреплены к боковым пластинам, включая индукционную катушку. Чтобы предотвратить контакт индуктора с деталью, керамические или твердосплавные направляющие башмаки размещаются в трех местах (сразу после концов петель и между двумя петлями) по периметру с обеих сторон индуктора.Керамические направляющие башмаки обычно устанавливаются на латунные или алюминиевые боковые пластины.
Помимо направляющих башмаков, боковые пластины также помогают удерживать индукционную катушку на месте. Индуктор обычно удерживается по крайней мере в трех местах: на концах каждой петли с помощью шпильки и компонента G-11, а в области выводов — с помощью компонента G-11. Другие компоненты, которые могут быть частью конструкции катушек коленчатого вала, включают направляющие для облегчения нагрузки катушки, закалочные головки и композитные боковые опоры для увеличения жесткости сборки.
Выводы катушки / Схема и контакты
В индукционных катушках имеется промежуточный корпус между головкой катушки (часть, где выполняется процесс индукционной термообработки) и тепловой станцией, источником питания или быстросменным адаптером. Эта часть индуктора называется выводами катушки или шиной. Роль выводов катушки или шины заключается в механическом и электрическом подключении головки индукционной катушки к источнику питания.Часто охлаждающая вода для головки змеевика также подается через провода.
Хорошая практика проектирования заключается в том, что выводы должны быть близко друг к другу, между ними должен быть кусок синтетической фторсодержащей смолы, чтобы электрически отделить два вывода друг от друга. Также рекомендуется делать высоту шины значительно больше, чем длина нагреваемой поверхности индукционной катушки.
В большинстве случаев выводы катушки или шина должны пропускать тот же ток, что и в самой головке индукционной катушки.Поскольку по выводам катушки / шине протекает высокочастотный ток, выводы катушки выделяют тепло от вихревых токов. Ток притягивается к стороне шины, которая обращена к противоположной шины, за счет эффекта близости. Плотность тока в выводах обратно пропорциональна длине границы раздела, и, следовательно, потери примерно пропорциональны квадрату длины. Близость двух выводов друг к другу в первую очередь влияет на падение напряжения в выводах. Чем ближе выводы, тем меньше их индуктивность и, следовательно, меньше падение напряжения.
Контакты катушки варьируются от простых расширяющихся или обжимных фитингов до механически обработанных блоков со шпонками для обеспечения правильного расположения в зависимости от сопрягаемой поверхности. Для условий термообработки обрабатываемые блоки со шпонками предпочтительны для сред с высокой удельной мощностью и низко- или среднечастотными средами. Компрессионные или развальцованные фитинги следует использовать только в случае высокочастотных применений с низкой удельной мощностью или длинных соленоидов с большим числом витков и низкими токами.
Для механически обработанных блочных контактов эти системы можно разделить на два класса: стандартные болтовые соединения и быстросменные переходники. Для стандартных болтовых соединений существует два основных типа контактов: рыбий хвост или тип Джексона и плоская пластина. Рыбные хвосты состоят из медной планки с прорезями для регулировки вертикальной высоты и внутреннего ключа на задней стороне для фиксации горизонтального положения (рис. 24а). Этот тип контакта является обычным для диапазона частот от 1 до 30 кГц при термообработке, когда катушка устанавливается на трансформатор.Для этого типа вода обычно подается из отдельных водяных линий к индукционной катушке, а не через электрические контакты тепловой станции, потому что вертикальная высота катушки не всегда находится в одном и том же месте.
Контакты с плоской пластиной обычно состоят из плоской пластины с двумя отверстиями для болтов и отверстием между двумя болтами для воды (рис. 24b). Отверстие для водяного охлаждения обычно немного утоплено для размещения уплотнительного кольца. Контакты с плоской пластиной обычно используются для подключения к источникам питания или выходам тепловых станций на более высокие частоты (от 50 до 450 кГц).
Помимо болтовых контактов, в промышленности используются несколько типов быстросменных адаптеров (рис. 25). Все эти системы включают использование механических клавиш и рычага для прижатия контактов заподлицо и фиксации положения катушки быстрым движением. Водяное охлаждение змеевика может быть или не быть встроено в быстросменный адаптер. Отдельное водяное охлаждение обычно обеспечивается индукционной катушке в случае высокой плотности мощности или когда быстросменный адаптер позволяет изменять вертикальное положение.
Рекомендации по закалке при проектировании индукционной катушки
Во многих случаях закалка проводится для завершения процесса закалки стальных компонентов и обычно выполняется с использованием воды, которая имеет небольшой процент закалочной среды. Это вторая половина термообработки; этот этап так же важен, как и нагрев.После того, как поверхность детали будет поднята выше температуры аустенизации, ее следует закалить (или быстро охладить). В большинстве случаев это следует делать сразу после достижения температуры аустенизации. Время до закалки может варьироваться в зависимости от состава стали. Конструкция закалки должна не только быстро, но и равномерно отводить тепло. Результатами неравномерной или медленной закалки являются неоднородная твердость и возможные общие деформации детали (или заготовки). Неоднородная твердость может привести к преждевременному выходу детали из строя или растрескиванию.Из-за важности однородности при закалке круглые или симметричные детали почти всегда поворачиваются во время закалки. Другими важными соображениями при проектировании закалки являются геометрия детали и то, как деталь представлена при закалке (т. Е. Горизонтально, вертикально и т. Д.). В некоторых деталях неправильной формы вращение невозможно или скорость вращения снижена, чтобы помочь контролировать закалку. При закалке на твердость поверхности обычно требуется сильная или интенсивная закалка. По этой причине закалка обычно выполняется с помощью ряда относительно небольших отверстий.Эти отверстия обычно имеют шахматный рисунок. Небольшие отверстия и ступенчатый рисунок приводят к интенсивной закалке, которая помогает избежать образования паровых карманов. Если используется закалка погружением (или замочением), на поверхности обычно образуется тонкий слой пара; этот пар может действовать как барьер или изолятор, вызывая более медленное охлаждение. Размер отдельных закалочных отверстий может варьироваться от 1,5 до 5 мм (от 1/16 до 3/16 дюйма) в диаметре, в зависимости от размера и геометрии детали. Обычно желательно, чтобы эти отверстия были как можно меньше, чтобы поддерживать более высокое давление закалки, что помогает уменьшить паровой карман, описанный ранее.Это также помогает зафиксировать твердость за счет полного преобразования мартенсита. Одним из недостатков небольших закалочных отверстий является то, что они с большей вероятностью заполнятся мусором или остатками после закалки; по этой причине многие конструкции закалки для термообработки имеют закалочные отверстия диаметром от 2,5 до 3,2 мм (3/32 и ⅛ дюйма).
На рисунке 26 показано типичное расположение закалочных отверстий при сканировании. Размер отверстия зависит от диаметра вала или заготовки, а также от площади закалки и воздушного зазора между закалочным блоком и поверхностью заготовки (Таблица 2) (Ссылка 9).
Диаметр вала | Размер отверстия | ||
---|---|---|---|
мм | дюйм | мм | дюйм |
6.5–13 | 0,25–0,50 | 1–1,5 | 0,046–0,063 |
13–38 | 0,50–1,50 | 1,5–2,5 | 0,063–0,094 |
> 38 | > 1,50 | 3,5–4 | 0,125–0,156 |
Конструкция гашения, как и конструкция индуктора, должна соответствовать детали.В некоторых случаях гаситель может быть включен в конструкцию индуктора; в других случаях он находится в отдельном закалочном кольце или закалочном блоке. Более подробно это обсуждается в разделе «Стили индукторов для термообработки» данной статьи. Что касается продолжительности времени закалки, закалка обычно занимает больше времени, чем нагрев; эмпирическое правило гласит, что время закалки должно быть в 1,5 раза больше времени нагрева. При статическом или однократном нагреве это можно контролировать с помощью таймера либо на станции нагрева, либо на станции закалки.Чтобы сэкономить время цикла, у некоторого оборудования есть короткая закалка на станции нагрева, за которой следует другая станция, чтобы завершить процесс закалки. Что касается сканирующего нагрева, закалка должна быть спроектирована так, чтобы иметь прямое столкновение на расстоянии не менее 1,5 расстояния от поверхности нагрева индуктора. При сканировании закалочные отверстия расположены под углом от катушки в том же направлении, в котором движется деталь. Это помогает предотвратить попадание воды обратно в индуктор и позволяет воде оставаться на детали как можно дольше.В любом случае (статический нагрев или сканирование) закалка должна выполняться до того, как поверхность детали упадет ниже температуры затвердевания, чтобы обеспечить полное преобразование материала.
Охлаждение индукционной катушки
Как обсуждалось ранее, в индукционном нагреве используются большие токи и высокие уровни мощности. По этой причине большинство индукторов для термообработки имеют водяное охлаждение. Некоторые индукторы состоят из медных трубок, по которым течет вода.Индукторы других типов изготавливаются из обработанных медных деталей с интегрированными в них охлаждающими каналами. В любом случае проходы должны быть рассчитаны на предполагаемые уровни мощности и иметь максимальный поток воды с минимальными ограничениями.
Термическая деградация вызвана локальным или полным перегревом головки катушки из-за потерь на вихревые токи в меди, магнитных потерь в концентраторе потока и передачи тепла от горячей поверхности детали за счет конвекции и излучения.Перегрев может привести к растрескиванию или деформации меди, а также к деградации материала концентратора. Растрескивание меди обычно происходит в змеевиках термообработки с коротким циклом из-за термомеханических напряжений, в то время как постепенная деформация змеевика более характерна для непрерывных процессов (ссылки 13, 14, 18, 19). Тепловые эффекты могут сильно усилить действие электромагнитных сил и ускорить старение электрической изоляции.
Перегрев меди — основная причина выхода из строя высоконагруженных индукторов термообработки; в этом разделе основное внимание уделяется этому типу отказа.Для катушек индуктивности, производимых последовательно, медные трещины возникают почти в одном и том же месте на индукторе каждый раз в определенном диапазоне производимых деталей. Есть несколько подходов к увеличению срока службы змеевика: обеспечить дополнительное охлаждение, уменьшить плотность источников тепла или полностью изменить конструкцию змеевика.
Дополнительное охлаждение может быть получено за счет увеличения расхода воды, снижения температуры водяного охлаждения, регулировки водяного кармана или введения дополнительных контуров охлаждения.Расход воды — это первый шаг, и он увеличивается до тех пор, пока не будет достигнут предел производительности насоса. Производители индукторов обычно имеют внутренние руководящие принципы, относящиеся к лучшим методам проектирования водяных карманов и контуров охлаждения, которые разрабатывались годами (Таблица 1). Эти рекомендации обычно основаны на частоте и плотности мощности. После того, как эти стандартные возможности исчерпаны, следующим шагом будет замена существующего насоса на более крупный или введение в систему подкачивающего насоса.
Иногда на змеевиках с очень высокой удельной мощностью достигается предел, когда даже при наилучшей конструкции охлаждающего контура и очень больших насосах срок службы змеевика остается неудовлетворительным. На этом этапе необходимо попытаться минимизировать локализованную плотность мощности в слабом месте индуктора. Это часто является сложной задачей для сложных индукторов, потому что изменение этого сечения может в некоторой степени повлиять на тепловую структуру в этой области детали, а также на остальной части.
Чтобы определить, что такое высокая удельная мощность, важно рассмотреть причину отказа. Режим отказа, который может быть устранен с помощью водяного охлаждения в змеевиках для индукционной термообработки большой мощности, — это механическая усталость, вызванная термоциклированием. Во время каждого цикла термообработки температура меди повышается при включении питания, в основном из-за тока в индукционной катушке. При повышении температуры меди медь расширяется. При отключении питания медь быстро остывает и сжимается.
Поскольку вихревые токи распределены в поперечном сечении меди неравномерно, распределение температуры в медной катушке также неоднородно. Вода в индукционной катушке отводит тепло за счет принудительной конвекции. Это означает, что скорость отвода тепла прямо пропорциональна коэффициенту теплопередачи и разнице температур между медью и основной водой. Коэффициент теплопередачи зависит от скорости воды, давления воды (в дополнение к влиянию давления на поток воды) и температуры воды.
В последние годы компьютерное моделирование оказалось эффективным инструментом для оценки тепловых циклов в индукционных катушках во время процесса термообработки (ссылки 19–21). Эти недавние исследования были выполнены с использованием некоторой комбинации электромагнитных, тепловых и гидродинамических кодов или корреляций. С помощью этого метода прогнозируются температуры, которые являются источником размерного перемещения и напряжения. Для обеспечения длительного срока службы используются определенные рекомендации по максимально допустимым температурам.Предполагается, что в будущем эти коды могут быть объединены с моделированием структур, напряжений и искажений.
Пример использования: Прогнозирование температуры меди в рулонах за один проход
В этом разделе обсуждается тематическое исследование с использованием компьютерного моделирования для демонстрации типичных распределений температуры в катушке индукционной закалки с однократной закалкой. Flux 2D используется для электромагнитного и теплового моделирования, а также для аналитических расчетов коэффициентов теплопередачи.Влияние давления (высокого и низкого), толщины стенки (1, 1,5 и 3 мм или 0,048, 0,062 и 0,125 дюйма), тока в катушке (5000, 7500 и 10000 А) и частоты (1 , 3 и 10 кГц). Корреляция для коэффициента теплопередачи сохраняется только до приблизительно 250 ° C (480 ° F) на границе медной стенки с охлаждающей водой, поэтому, если это соображение не будет соблюдено, температура в змеевике будет менее точной.
Геометрия для исследования — 19 мм (3/4 дюйма.) квадратная медная трубка с концентратором магнитного потока Fluxtrol A для нагрева вала диаметром 38 мм (1,5 дюйма). Зазор муфты, использованный для исследования, составляет 3,2 мм (⅛ дюйма). Чтобы ограничить количество переменных, деталь не моделируется во время исследования. Деталь аппроксимируется немагнитным слоем толщиной 6,3 мм (дюйма) со свойствами стали выше точки Кюри и сердечником диаметром 25 мм (1 дюйм), который имеет свойства холодной низкоуглеродистой стали.
На рисунке 27 показано распределение температуры в поперечном сечении катушки при токе 5000 А на частоте 10 кГц при низком давлении и толщине стенки 1 мм (0.048 дюймов) после 10 с нагрева. Температура наиболее высока в углах лицевой поверхности и несколько ниже в центре витка. Концентратор имеет значительно более низкую температуру, а локализованные более высокотемпературные области возникают из-за проводимости через клей к концентратору. Максимальная температура составляет 117 ° C (243 ° F). На рисунке 28 показаны зависимости температуры в углу и центре трубки от времени для этого случая. Практически весь рост температуры в меди происходит за первые 2 с.
Если давление увеличено вдвое, распределение температуры будет таким, как показано на рис.29 (а). Максимальная температура в углу снижена до 99 ° C (210 ° F). Разница между температурой в углу котла и в центре лицевой поверхности значительно выше. На рисунке 29 (b) показано распределение температуры при увеличении толщины стенки до 1,5 мм (0,062 дюйма). Максимальная температура меди немного выше — 102 ° C (216 ° F). Если толщину стенки увеличить до 3 мм (0,125 дюйма), максимальная температура возрастет примерно до 111 ° C (232 ° F) (рис. 29c).
Все эти температуры можно считать разумными, и в зависимости от температуры можно ожидать длительного срока службы меди. Если увеличить ток до 7500 А, разница между результатами станет более очевидной. На рис. 30 показаны распределения температуры для тех же случаев, показанных на рис. 27 и 29, с более высоким током. Теперь температура медной стенки, контактирующей с водой для стенки низкого давления толщиной 1 мм (0,048 дюйма) (рис.30a) выше порога, при котором корреляции сохраняются. Это означает, что существует опасность образования паровой подушки и очень короткий срок службы змеевика. Также важно отметить, что максимальная температура смещается к центру трубы, а не к углам. Это признак того, что охлаждение недостаточно, а увеличение давления воды может значительно увеличить срок службы змеевика.
При повышении давления температура на внутренних стенках медных трубок падает до приемлемого уровня (рис. 30b). Максимальная температура опять же в углах медной трубки, а не в центре. Однако уровень температуры меди в углах остается повышенным (225 ° C, или 437 ° F). Для более толстых стенок температура составляет 230 и 263 ° C (446 и 505 ° F) соответственно (рис.30в, г).
Это означает, что в каждом цикле медь в углах трубки расширяется более чем в два раза больше, чем в случае более низкого тока. Когда питание отключается, трубка сжимается до своей первоначальной формы. При таких температурах существует вероятность того, что срок службы катушки может быть неудовлетворительным.
Если частота уменьшается, но ток остается 7500 А, температура катушки значительно снижается (рис. 31). Для стенки толщиной 1 мм (0,048 дюйма) с низким давлением максимальная температура снижается до 178 ° C (352 ° F) (рис.31а). Температура в углах значительно ниже, чем в центре. Если давление увеличивается, температура меди снижается до 133 ° C (271 ° F) (рис. 31b). Однако максимальная температура по-прежнему сохраняется в центральных частях меди, а не в углах. Это связано с тем, что толщина стенки меди меньше оптимальной (1,6d). Малая толщина меди увеличивает сопротивление и потери в центральной части катушки.
При увеличении толщины стенки до 1.5 мм (0,062 дюйма) температура меди снижается до 114 ° C (237 ° F) (рис. 31c). Центральная температура обмотки также снижается по сравнению с углами. Максимум температуры находится прямо у края водяного охлаждения, что означает немного меньшую, чем оптимальная, толщина стенки. В случае стенки толщиной 3 мм (0,125 дюйма) максимальная температура снова повышается до 125 ° C (257 ° F) (рис. 31d). Максимум сейчас явно в углах. Фактически температура в центре трубки в этом случае ниже.Повышение максимальной температуры связано с удалением от водяного охлаждения.
Потери в медных трубках почти одинаковы для этих двух случаев (3 кГц; 1,5 и 3 мм, или 0,062 и 0,125 дюйма, толщина стенки) и чуть менее 20% ниже, чем для стенки 1 мм (0,048 дюйма). толщина. Оптимальная толщина стенки и, следовательно, максимальная допустимая нагрузка по току для 3 кГц будут находиться между этими двумя значениями толщины.
На 1 кГц для сравнения использовалось 10000 А, потому что на более низких частотах естественно иметь более высокие токи (рис.32). При толщине стенки 1 мм (0,048 дюйма) и низком давлении температура в меди явно чрезмерна, и имеется значительный градиент от центра к углам (рис. 32a). По мере увеличения давления температура становится предельной (230 ° C или 446 ° F, температура стенки), и все еще существует значительный градиент от центра к краю (рис. 32b). Это связано с тем, что толщина стенок значительно меньше оптимальной.
Для толщины стенки 1,5 мм (0,062 дюйма) максимальная температура снижается примерно до 144 ° C (291 ° F) (рис.32c). Потери в меди почти на 40% ниже, чем при толщине стенки 1 мм (0,048 дюйма). Распределение температуры по поверхности почти ровное, что означает, что толщина стенки меньше оптимальной. Для толщины стенки 3 мм (0,125 дюйма) максимальная температура составляет всего 100 ° C (212 ° F), а расположение — углы (рис. 32d). Потери при толщине стенки 3 мм (0,125 дюйма) примерно на 30% ниже, чем при толщине стенки 1,5 мм (0,062 дюйма).
Еще одним фактором, связанным с водяным охлаждением индукционных катушек, является температура воды.Температура воды влияет на температуру индукционной катушки двояко. Понятно, что чем ниже температура воды, тем холоднее индукционная катушка, потому что метод охлаждения — конвекционный. Если бы температуру воды понизили на 10 ° C (18 ° F), то можно было бы ожидать, что максимальная температура в меди также будет на 10 ° C (18 ° F) ниже.
Поскольку изменение температуры (∆T) меди будет таким же, можно ожидать, что величина движения меди будет такой же, как и срок службы катушки.Однако это неверно, поскольку коэффициент теплового расширения меди не зависит от температуры (рис. 33). При повышении температуры коэффициент теплового расширения меди продолжает расти (см. 22). Это означает, что чем выше температура, тем больше перемещение при том же ∆T.
На самом деле ∆T меди не то же самое.На самом деле это немного меньше, потому что удельное электрическое сопротивление меди повышается с температурой. Следовательно, потери в меди меньше, а результирующая величина ∆T меньше. Это отменяет тот факт, что коэффициент теплопередачи воды немного ниже при более низкой температуре (ссылка 23).
Последний фактор, который следует учитывать при водяном охлаждении индукторов, — это качество воды. Лучшей жидкостью для охлаждения индукционных катушек при термообработке является чистая деминерализованная вода.Чистая вода имеет естественный высокий коэффициент теплопередачи. Практически все добавки отрицательно влияют на теплопередачу.
Особенно плохи минералы. Со временем они выпадают из раствора и накапливаются на стенках медных трубок. Это имеет два отрицательных эффекта. Во-первых, минеральный слой уменьшает поперечное сечение потока воды. Минеральный слой также создает барьер для передачи тепла, вызывая повышение температуры меди.Если используется вода, содержащая минералы, со временем температура меди продолжает расти и достигает критического уровня, что приводит к выходу из строя индуктора. При использовании этого типа охлаждающей жидкости индукционную катушку необходимо регулярно чистить и промывать.
Типы индукторов для термообработки
Как указывалось ранее, катушки для индукционной термообработки бывают разных форм и размеров. Отличным источником фотографий змеевиков для индукционной термообработки является книга Ричарда Хаймбо «Практическая индукционная термообработка» (ссылка 5).Эти фотографии включены в «Основы и процессы термообработки стали», том 4A Справочника ASM, 2013 г., поэтому здесь они не повторяются.
Навыки для изготовления индукторов для термообработки
Медь — уникальный металл, связанный с древним ремеслом — медным делом. Обучаясь на ремесленника или ремесленника, студент-медник поступал в подмастерья у подмастерья, чтобы изучить характер и способы обращения с этим металлом.Хотя Соединенные Штаты ассимилировали медников с другими квалифицированными профессиями, медное дело по-прежнему признано во всем промышленно развитом мире.
Инструменты и навыки медника идеально подходят к металлу; однако нужен ли медник по специальности для изготовления медного индуктора? Ответ — нет; Тем не менее, навыки медника должны быть приобретены в процессе создания индукторов для термообработки, а также должны быть знакомы с электрическими цепями большой мощности.
Базовые навыки
Поскольку медь легко превращается в сложные формы, мастер, владеющий инструментами, паяльником и пропановой горелкой, может построить хороший базовый индуктор. В процессе формовки медь затвердевает; тем не менее, когда он нагревается до тускло-красного цвета и закаливается в воде, он снова легко образуется. Базовые индукторы изготовлены из доступных медных трубок, намотанных на формовочную оправку.Медная трубка обеспечивает удобный путь, необходимый для охлаждения меди. В зависимости от конфигурации индукционного источника питания простыми электрическими соединениями могут быть латунные трубные фитинги — либо тонкие, либо сжатые, хотя предпочтительнее тонкие, — или медные выступы, которые припаяны к трубке, как упоминалось ранее. Электрический мягкий припой достаточен при потребляемой мощности 10 кВт или меньше.
Продвинутые навыки
Машинист с классическим образованием — это обычный мастер, нанимаемый для создания индукторов для термообработки.Подходящий кандидат обладает способностями, ловкостью и терпением к созданию моделей. Большинство из них столкнутся с трудностями при обработке меди, если не будут предоставлены инструкции по использованию специальных режущих инструментов, скоростей, подач и СОЖ, специфичных для этого металла. Большая часть работы по созданию сложных индукторов включает в себя множество мелких деталей и различных материалов, которые требуют механической обработки, формовки, пайки серебром и сборки. Индукторы для термообработки обычно строятся по одному, и всю работу может выполнять один машинист.Простая механическая мастерская, состоящая из напольного фрезерного станка, токарного станка, настольной ленточной пилы, вентилируемого стола для пайки с горелками и сборочного стенда с различными ручными инструментами, составляет подходящую рабочую зону.
Большинство индукторов лучше всего строить по дизайнерским принтам. Хорошая упаковка для печати включает в себя спецификацию материалов, подробную информацию обо всех компонентах, а также форму сборки и проверки. В некоторых случаях индуктор может быть построен путем обратного проектирования оригинала. При конструировании индукторов для термообработки следует учитывать следующее:
- Обработка: Большая часть сырья в типичном индукторе для термообработки имеет форму листа, пластины или круглой электролитической меди.Из-за липкой природы металла для фрезерных, сверлильных и токарных операций рекомендуются фрезы, подачи, скорости и СОЖ, специально разработанные для меди.
- Изготовление: Для завершения сборки индуктора термообработки может потребоваться множество деталей. Некоторые из этих деталей подходят для использования в качестве крышек для охлаждающих камер и вспомогательных соединений, которые включают охлаждение или закалку, или и то, и другое. Для обеспечения герметичности и качества электрических соединений необходима целостность монтажа.
- Серебряная пайка: хотя некоторые топливные газы лучше всего подходят для серебряной пайки, выбор подходящего топлива, такого как метилацетиленпропадиеновый газ, для смешивания со сжатым кислородом может быть ограниченным. Нагрев горелки должен быть достаточным для поддержания температуры пайки серебра во всей медной массе. Требуются различные наконечники горелки, а также флюс и серебряный пруток диаметром 1,5 мм (0,06 дюйма). Содержание серебра в прутке для пайки, лучше всего подходящей для конструкции индуктора, составляет от 5 до 45%.Серебряная пайка — это трудный навык; однако с практикой, терпением и настойчивостью эту технику можно освоить.
Навыки ремонта
Медные индукторы иногда подвергаются экстремальным условиям индукционной термообработки: электромагнитному напряжению, сильному нагреву, масляному дыму, пару, грязи и сажи. Воздействие на медь может быть серьезным, приводя к износу и усталости индуктора и, в конечном итоге, к процессу термообработки.Обслуживание индуктора имеет важное значение. Очистка индуктора водой с мылом и мягкой пластиковой щеткой, а также регулярный осмотр меди и компонентов предупреждают оператора индукционной печи об ухудшении характеристик и проблемах с производительностью.
Навыки ремонта продвинуты. Индуктор очищается, разбирается и проверяется на предмет износа меди, а также утечек и трещин. Косметический ремонт, такой как выпрямление изогнутых деталей, обычно можно производить без отжига меди.Вспомогательные компоненты, такие как усилители потока, кронштейны, направляющие и устройства закалки, очищаются и проверяются на предмет повреждений, а также ремонтируются или заменяются.
Трещины в медном индукторе могут возникать в результате любого из следующих факторов: циклической усталости, дифференциального охлаждения меди, резистивных паяных соединений и неправильного обращения. Трещины часто заделывают серебряной пайкой. Хотя этот патч может быть экономически эффективным ремонтом, он редко бывает постоянным. В надежном процессе медный индуктор следует заменять через соответствующее время / срок службы.
Насадка для регуляторов магнитного потока
Было объяснено, что регуляторы потока необходимы для направления потока тока для конкретных приложений индукционного нагрева. Прикрепление их к индуктору требует осторожного обращения, чтобы они были правильно размещены и надежно закреплены. Неправильная установка или потеря любой части контроллера магнитного потока может привести к несоответствующей обрабатываемой части. Контроллеры магнитного потока зависят от частоты и изготавливаются из кремнистой стали, магнитомягкого феррита или магнитомягкого композита.Прикрепление этих материалов к индуктору может стать проблемой для проектировщика / строителя. Ниже приведены несколько примеров.
Пластины из кремнистой стали
Этот материал поставляется в различных сортах, толщинах и отделках. Его обычная форма — тонкий лист с изоляционным слоем с обеих сторон. Сначала он конструируется определенной формы, затем штампуется или подвергается механической обработке и подходит для индуктора. Самая распространенная форма — это прямоугольная или квадратная форма буквы «C».Пластины укладываются на индуктор рядом друг с другом таким образом, чтобы обнажить эту часть меди для нагреваемой части. Медные выступы той же формы припаяны серебром к индуктору через различные промежутки времени, чтобы поддерживать стопку. Крепление стопки достигается приклеиванием высокотемпературной эпоксидной смолы или механическим зажимом ее на индукторе. Используются различные методы зажима. Наиболее распространенным является использование для печатных плат полужесткого материала из эпоксидной смолы, такого как G-10, который разрезается и подходит к задней части стопки и закрепляется с обоих концов.Практично укладывать ламинат вокруг внешней или внутренней стороны индукционной петли. При установке на круглые индукторы, пластинки исходят из центральной точки, оставляя заметные зазоры, особенно на маленьких круглых индукторах; тем не менее, при тщательном проектировании это можно свести к минимуму.
Мягкие магнитные композиты и спеченные ферриты
Эти продукты разработаны и изготовлены для специальных индукционных применений.Поскольку спеченные ферриты хрупкие и их трудно обрабатывать, их использование в основном ограничивалось трансформаторами. Однако мягкие магнитные композиты были разработаны специально для индустрии индукционного нагрева. Эти продукты разработаны для использования на обычных частотах энергоснабжения. Они изготавливаются в виде блоков различных размеров, легко обрабатываются и подходят к индуктору. И ферриты железа, и магнитомягкие композиты прикрепляются к индуктору механически с помощью болтов и винтов или с помощью клея.В документации по продукту описано их использование в системах индукционного нагрева (ссылка 13).
Процедуры целостности перед производством
В этом разделе обсуждаются вопросы удаления флюса и оксидов, проверки утечки и потока, серебряного покрытия и измерения электрических параметров.
Удаление флюса и оксидов
После пайки медь индукционной катушки имеет флюс около паяных соединений, а также окисление в результате процесса высокотемпературной пайки.Перед сборкой следует удалить флюс и оксиды. Первым шагом в этом процессе является помещение индукционной катушки под горячую (от 70 до 80 ° C или от 150 до 180 ° F) проточную воду. Горячая вода помогает удалить большую часть флюса, оставшегося от процесса пайки. Также рекомендуется пропускать горячую воду через каналы для водяного охлаждения индуктора, чтобы удалить флюс, который может накапливаться внутри трубки и блокировать проход.
Следующим шагом после очистки горячей водой является пескоструйная очистка индуктора для удаления оксидов.Процесс пескоструйной обработки также удаляет остатки флюса из индуктора. После пескоструйной обработки следует использовать процесс тонкой обработки стеклом, чтобы улучшить состояние поверхности индуктора.
После бисероплетения медь чистая. Если оставить это так, индуктор окисляется на воздухе и меняет цвет. Рекомендуется покрыть поверхность индукционной катушки (за исключением электрических контактов) прозрачным лаком. Лак препятствует окислению меди.
В некоторых случаях с сильно нагруженными индукторами термообработки выполняется низкотемпературный отпуск при 200 ° C (400 ° F) в течение нескольких часов или процесс отжига при более высокой температуре на воздухе. Этот процесс отпуска снимает напряжение при производстве и окисляет медь до темно-оранжевого цвета (отпуск) или темно-коричневого цвета (отжиг). Из этого состояния медь больше не окисляется, и нет необходимости наносить прозрачный лак.
Проверка утечки и расхода
После очистки индукционной катушки необходимо убедиться, что она герметична и не засорены водопроводные каналы.Проверка герметичности индукционной катушки обычно выполняется путем погружения индукционной катушки в резервуар с водой и подачи рабочего воздуха под высоким давлением. Тест следует проводить в течение нескольких минут. Если появляются пузыри, змеевик необходимо отправить обратно изготовителю змеевика для устранения утечки. В некоторых случаях термической обработки в специальной атмосфере утечка воды особенно опасна. В этих случаях следует выполнить проверку на утечку гелия.
После проверки на герметичность индукционную катушку следует подключить к водопроводной сети.При определенном давлении следует измерить расход воды через индукционную катушку. Для каждой индукционной катушки должен быть определен минимальный расход. Если скорость потока не соответствует этому минимальному уровню, это означает, что канал охлаждения засорен. Перед отправкой индукционной катушки необходимо удалить препятствие; поэтому индукционную катушку следует отправить обратно изготовителю катушки.
Серебряное покрытие
Посеребрение контактов индукционной катушки обычно выполняется после очистки.Основная роль серебряного покрытия — действовать как ингибитор коррозии электрических контактов. Коррозия увеличивает контактное сопротивление и может привести к преждевременному выходу из строя индукционной катушки.
Материалы для серебряного покрытия могут быть жидкими, пастообразными или порошкообразными. В торговле чаще всего используется жидкий раствор для серебряного покрытия от HM Products Inc. Раствор наносится щеткой или втирается в контактную поверхность. После нанесения контактная площадка промывается водой.Если поверхность не промыть водой вскоре после нанесения, серебряный носитель разъедает контакты и образуется зеленый оксид. При использовании материалов для серебряного покрытия следует соблюдать осторожность, поскольку большинство из них содержат цианид натрия, который является токсичным материалом.
Измерение электрических параметров
На некоторых индукционных катушках, таких как литые или герметизированные индукторы, невозможно физически увидеть или механически проверить все критические размеры индукционной катушки.Кроме того, на индукционных катушках с регуляторами магнитного потока непрактично подсчитывать количество слоев или может быть трудно определить, был ли использован правильный сорт магнитомягкого композитного материала.
Чтобы гарантировать, что рабочие характеристики индукционной катушки соответствуют характеристикам других индукционных катушек, построенных для этой печати, перед отправкой необходимо провести измерения электрических параметров катушки. Лучший метод проверки включает измерение индуктивности или импеданса и сопротивления индукционной катушки с компонентом, который она предназначена для нагрева с частотой нагрева.Если это невозможно, ценную информацию о стабильности катушки можно получить путем измерения индуктивности без детали.
Устройства, способные измерять индуктивность или импеданс и сопротивление катушек (измерители LCR) на выбираемой частоте, обычно стоят несколько тысяч долларов и доступны у ряда производителей. Доступны менее дорогие устройства только для измерения индуктивности. На момент написания этой статьи одно из таких устройств, которое хорошо работает, L / C Meter IIB, произведено почти All Digital Electronics и стоит менее 200 долларов (ссылка 24).Со временем на рынке появятся новые устройства с еще лучшими характеристиками для контроля качества индукционных катушек.
Список литературы
[1] А. Мюльбауэр, История индукционного нагрева и плавления, Vulcan Verlag GmbH, Huyssenallee, Essen, Германия, 2008 г.
[2] Х. Осборн младший, Индукционный нагрев и закалка, Часть A, Американское общество металлов, Парк металлов, штат Огайо, 1977
[3] В.П. Вологдин, Б. Романов, Устройство для упрочнения коленчатых валов высокочастотными токами, Патент СССР 48416, подана 16 декабря 1935 г., выдан в 1936 г.
[4] В.П. Вологдин, Индукционная поверхностная закалка, Оборонгиз, М., 1947.
[5] Р.Э. Хаймбо, Практическая индукционная термообработка, ASM International, Materials Park, Огайо, 2001
[6] К.А. Тадбери, Основы индукционного нагрева, Том 1, Джон Ф. Райдер, Нью-Йорк, Нью-Йорк, 1960.
[7] С.Л. Семятин, Д.Э. Штутц, Индукционная термообработка стали, Американское общество металлов, Metals Park, Огайо, 1986
[8] М.Г. Лозинский, Промышленные применения индукционного нагрева, Pergamon Press, Oxford, London, New York, 1969.
[9] В. Руднев и др., Справочник по индукционному нагреву, Марсель Деккер, Нью-Йорк, штат Нью-Йорк, 2003 г.
[10] R.C. Голдштейн и др., «Виртуальный прототип индукционной термообработки», 25-я конференция Общества термической обработки ASM, 14–17 сентября 2009 г. (Индианаполис, Индиана)
[11] Дж.Цай и др., Интеграция моделирования индукционной термообработки в производственный цикл, J. Heat Treat. Прог., Том 3 (№ 2), 2003 г.
[12] В.С. Немков, Моделирование процессов индукционного упрочнения, Справочник по моделированию термических процессов в стали, C.H. Гур и Дж. Пэн, изд., CRC Press, 2009.
[13] W.I. Stuehr и D. Lynch, «Как увеличить срок службы индуктора», 23-я конференция Общества термической обработки ASM, 25–28 сентября 2005 г. (Питтсбург, Пенсильвания).
[14] В.И. Штур и Д. Линч, «Как увеличить срок службы индуктора, часть II», 24-я конференция Общества термической обработки ASM, 17–19 сентября 2007 г. (Детройт, Мичиган)
[15] Ajax Tocco Magnethermic, http://www.ajaxtocco.com/default.asp?ID=134
[16] В.С. Немков и Р. Гольдштейн, Принципы проектирования для индукционного нагрева и закалки, гл. 15, Справочник по проектированию металлургических процессов, Г. Тоттен, К. Фунатани и Л. Се, ред. Марсель Деккер, Нью-Йорк, штат Нью-Йорк, 2004 г.
[17] В.С. Немков, Справочник ресурсов для индукционного нагрева, CD-R, Fluxtrol Inc., 2006 г.
[18] В.И. Руднев, Систематический анализ отказов индукционной катушки, части 1–11, Термическая обработка. Прог. Mag., Август 2005 г. — сентябрь / октябрь 2007 г.
[19] Х. Свендсен, С.Т. Хаген, «Оценка термомеханической усталостной долговечности индукционных катушек», Международный научный коллоквиум по моделированию электромагнитной обработки, 27–29 октября 2008 г. (Ганновер, Германия)
[20] Р.К. Гольдштейн, В.С. Немков, «Влияние условий охлаждения на температуру индукционной катушки», Международный симпозиум по нагреву внутренними источниками (Падуя, Италия), 2007 г.
[21] Х. Свендсен, С.Т. Хаген, «Распределение температуры в отдельных поперечных сечениях змеевиков индукционного нагрева», Международный симпозиум по нагреву внутренними источниками (Падуя, Италия), 2007 г.
[22] Примеры моделирования процессов, Справочник по инженерной статистике, NIST / SEMATECH, http: // www.itl.nist.gov/div898/handbook/pmd/section6/pmd6.htm
[23] Внутренние документы Fluxtrol, Inc.
[24] L / C Meter IIB, Почти вся цифровая электроника, http://aade.com/lcmeter.htm
Если у вас есть дополнительные вопросы, вам требуется обслуживание или просто нужна общая информация, мы здесь, чтобы помочь.
Наша компетентная команда по обслуживанию клиентов доступна в рабочее время, чтобы ответить на ваши вопросы относительно продукта Fluxtrol, цен, заказа и другой информации.Если у вас есть технические вопросы об индукционном нагреве, свойствах материалов, наших инженерных и образовательных услугах, свяжитесь с нашими специалистами по телефону, электронной или обычной почте.
Fluxtrol Inc.
1388 Атлантический бульвар,
Оберн-Хиллз, Мичиган 48326
Телефон: + 1-800-224-5522
За пределами США: 1-248-393-2000
ФАКС: + 1-248-393-0277
— индукторы, соленоиды, тороиды, сердечники горшков, анализ сигналов индукторов, применение индукторов
В предыдущем руководстве мы обсуждали магнетизм, электромагнетизм и индуктивность.Индуктивность может быть полезна в схемах. Электронные компоненты, которые предназначены для обеспечения индуктивности в цепи, называются индукторами.
Катушки индуктивности
Большинство проводящих материалов (металлов) являются парамагнитными или ферромагнитными, в то время как большинство непроводящих материалов (неметаллы) являются диамагнитными. Любой проводник показывает некоторую индуктивность в ответ на изменение величины или направления тока. Даже простой прямой провод показывает некоторую индуктивность, хотя она достаточно мала, чтобы ею можно было пренебречь в схеме.Если этот же провод намотан в петлю, его индуктивность увеличивается. Чем больше количество витков для одинаковой длины провода, тем большую индуктивность он показывает. Индуктивность контура или катушки с проволокой можно многократно увеличить, используя подходящий ферромагнитный сердечник.
Самыми простыми катушками индуктивности являются катушки с воздушным сердечником. Они состоят из обмотки проволоки вокруг пластмассового, деревянного или любого неферромагнитного сердечника. Индуктивность катушки зависит от количества витков, радиуса катушки и общей формы катушки.Индуктивность пропорциональна количеству витков, а также диаметру катушки. Оно обратно пропорционально длине провода для данного диаметра и количества витков катушки. Значит, чем ближе будут витки, тем больше будет индуктивность. Допустимая нагрузка по току индуктора зависит от материала и толщины провода. Рабочие потери (в виде тепла) от индуктора во многом зависят от материала, используемого в качестве сердечника в индукторе.
Пример индуктора с воздушным сердечником (Изображение: Wurth Electronics)
Катушки с воздушным сердечником имеют небольшую индуктивность, которая может составлять максимум 1 мГн.Катушки с воздушным сердечником могут быть сконструированы таким образом, чтобы иметь неограниченную допустимую нагрузку по току за счет использования проволоки большого сечения с большим радиусом. Эти индукторы практически без потерь, так как воздух не рассеивает много энергии в виде тепла. Чем выше частота переменного тока, тем меньше индуктивность, необходимая для получения значительных эффектов. Таким образом, индукторы с воздушным сердечником вполне подходят для высокочастотных цепей переменного тока благодаря работе без потерь, высокой токовой нагрузке и достаточным значениям индуктивности.
Используя железные или ферритовые сердечники с питанием, можно значительно увеличить индуктивность.Однако порошкообразный железный или ферритовый сердечник также имеет значительные потери электрической энергии в виде тепла. Использование ферромагнитных сердечников также ограничивает допустимую нагрузку на индуктор. В ферромагнитных сердечниках индуктивность насыщается при критическом значении тока. При увеличении тока сверх критического значения индуктивность может вместо этого начать уменьшаться. При высоких токах ферромагнитные сердечники могут нагреться настолько, что они могут сломаться и навсегда изменить номинальную индуктивность индуктора.
Соленоид и индукторы
Соленоиды часто путают с индукторами. Соленоиды представляют собой катушки проводов, которые предназначены для использования в качестве электромагнитов. Многие индукторы также представляют собой катушки из проводов, но они предназначены для обеспечения индуктивности в цепи. Индукторы, использующие цилиндрические катушки, также называются соленоидными катушками только из-за их конструкции, подобной соленоидам. Однако они не предназначены для использования в качестве электромагнита в цепи. Соленоиды специально используются в качестве электромагнитов и обычно имеют подвижный или статический сердечник.Обычно соленоиды используются в качестве электромагнитов в электрических звонках, двигателях постоянного тока и реле.
Соленоидные катушки как индукторы
Самыми простыми и распространенными индукторами являются соленоидные катушки. Эти индукторы представляют собой цилиндрические катушки, намотанные на воздушный сердечник или ферромагнитный сердечник. Эти индукторы проще всего сконструировать.
Соленоидную или цилиндрическую катушку можно легко сконструировать для изменения индуктивности за счет включения механизма, позволяющего вставлять и выдвигать ферромагнитный сердечник катушки.Перемещая сердечник внутрь и из катушки, можно изменять эффективную магнитную проницаемость катушки и, следовательно, индуктивность катушки. Это называется настройкой проницаемости. Это используется для регулировки частот в радиосхемах.
Сердечник можно сделать подвижным, прикрепив его к валу винта и закрепив гайкой на другом конце катушки. Когда винтовой вал вращается по часовой стрелке, сердечник движется внутри катушки, увеличивая эффективную проницаемость и, следовательно, индуктивность. Когда винтовой вал вращается против часовой стрелки, сердечник выдвигается, уменьшая эффективную проницаемость и, следовательно, индуктивность.
Тороид в качестве индукторов
Тороид — еще одна наиболее распространенная форма индукторов в наши дни. Тороиды имеют ферромагнитный сердечник в форме пончика, на который намотана катушка. Тороидам требуется меньше витков, и они физически меньше при той же индуктивности и допустимой нагрузке по току по сравнению с соленоидными катушками. Еще одно важное преимущество тороидов состоит в том, что магнитный поток находится внутри сердечника, что позволяет избежать нежелательной взаимной индуктивности.
Сильноточные тороидальные проводники.(Изображение: Signal Transformer, Bel Group)
Однако намотать катушку в тороид сложно. Настроить проницаемость тороида даже очень сложно. Создание переменных индукторов на тороиде требует сложной и громоздкой конструкции. В цепях, где требуется взаимная индуктивность, разные катушки должны быть намотаны на один и тот же сердечник в случае, если тороид используется в качестве индуктора.
Сердечники в качестве индукторов
В типичных индукторах — соленоидных катушках и тороидах — катушка намотана вокруг ферромагнитного сердечника.Сердечник горшка — это еще один тип индуктора, в котором обмотка катушки находится внутри ферромагнитного сердечника. В сердечнике электролизера ферромагнитный сердечник имеет форму двух половин. Катушка наматывается и наматывается одной из половинок. Между двумя половинками есть отверстия, из которых вынимается провод катушки. Вся сборка скрепляется болтом и гайкой.
Сердечники потенциометров, такие как тороиды, обладают большой индуктивностью и допустимой нагрузкой по току при небольшом размере с меньшим количеством витков. Флюс, как и в тороидах, остается внутри сборки.Таким образом, нет нежелательной взаимной индуктивности с сердечниками потенциометра. Опять же, как и в тороидах, индуктивность сердечников потенциометров изменить сложно. Изменять индуктивность сердечников электролита можно только путем изменения количества витков, а также путем использования отводов в разных точках катушки.
Линия передачи в качестве индуктора
Катушки индуктивности используются в основном в цепях переменного тока. Для постоянного тока катушки индуктивности почти ведут себя как проводящий провод, предлагая незначительное сопротивление и ничего больше. В переменном токе индукторы находят свое реальное применение.В цепях звуковой частоты в качестве индукторов обычно используются тороиды, сердечники электролизеров или звуковые трансформаторы. В аудиосхемах обычно используются индукторы номиналом от нескольких Милли-Генри до 1 Генри. Катушки индуктивности вместе с конденсаторами использовались в аудиосхемах для настройки. В настоящее время активные ИС практически заменили катушки индуктивности и конденсаторы в аудиосхемах и приложениях.
При увеличении частоты используются индукторы с сердечниками с меньшей магнитной проницаемостью. На нижнем уровне радиочастот используются те же катушки индуктивности, которые используются в аудиоприложениях.На радиочастотах до нескольких МГц довольно часто встречаются тороиды. Для радиочастот от 30 до 100 МГц предпочтительны катушки с воздушным сердечником.
Для радиочастот выше 100 МГц полезны индукторы линии передачи. Линии передачи короткой длины (четверть длины волны или меньше длины волны сигнала) могут использоваться в качестве индуктора для настройки высокочастотных радиосигналов. Линия передачи, используемая в качестве индуктора, обычно представляет собой коаксиальный кабель.
Катушка индуктивности в цепи постоянного тока
На практике катушки индуктивности бесполезны в цепях постоянного тока, поскольку они не показывают индуктивности для постоянных токов.Однако предположение, что индуктор подключен к цепи постоянного тока, может быть полезным для понимания принципа его работы и его поведения при пульсирующих напряжениях постоянного тока. Предположим, что чистый индуктор подключен к источнику напряжения через переключатель. Когда переключатель замкнут, напряжение подается на катушку индуктивности, вызывая быстрое изменение тока через нее. Когда приложенное напряжение увеличивается от нуля до пикового значения (за короткое время), индуктор противодействует протеканию через него изменяющегося тока, создавая напряжение, противоположное по полярности приложенному напряжению.Индуцированное напряжение во время включения индуктора называется обратной ЭДС и определяется следующим уравнением —
В L = — L * (di / dt)
Где
В L — это напряжение (обратная ЭДС), индуцированное в катушке индуктивности.
L — индуктивность, обеспечиваемая катушкой индуктивности.
di / dt — это скорость изменения тока во времени.
Внезапное изменение тока через катушку индуктивности дает бесконечное напряжение, что невозможно. Таким образом, ток через катушку индуктивности не может резко измениться.Ток сталкивается с влиянием индуктивности при каждом небольшом изменении величины и медленно повышается до своего пикового постоянного значения. Таким образом, первоначально индуктор действует как разомкнутая цепь, когда переключатель замкнут. Обратная ЭДС остается на катушке индуктивности до тех пор, пока через нее не изменится ток. Индуцированная обратная ЭДС всегда остается равной и противоположной возрастающему приложенному напряжению. Когда напряжение и ток от источника приближаются к постоянному значению, обратная ЭДС падает до нуля, и индуктор действует как короткое замыкание, как соединительный провод.При подаче питания мощность, запасаемая индуктором, определяется следующим уравнением —
P = V * I = L * i * di / dt
Где
P — электрическая мощность, запасаемая индуктором.
В — пиковое напряжение на катушке индуктивности.
I — пиковый ток через катушку индуктивности.
Энергия, запасаемая индуктором при включении, определяется следующим уравнением —
Вт = ∫P.dt = L * i * (di / dt) dt = (1/2) LI 2
Где,
Вт это электрическая энергия, запасенная индуктором в виде магнитного поля.
I — это максимальный ток через него.
При отключении источника напряжения (размыканием переключателя) напряжение на катушке индуктивности падает с пикового постоянного значения до нуля. В отличие от конденсаторов, при отключении источника напряжения напряжение на катушке индуктивности не сохраняется. Фактически, он уже упал до нуля, когда ток через него стал постоянным. Теперь, когда приложенное напряжение падает с постоянного пикового значения до нуля, ток через катушку индуктивности также падает с постоянного пикового значения до нуля.Теперь индуктор противодействует падению тока, индуцируя прямую ЭДС в направлении приложенного напряжения. Из-за наведенной прямой ЭДС ток через катушку индуктивности падает до нуля медленнее. Когда ток уменьшается до нуля, прямая ЭДС также падает до нуля.
Итак, во время подачи питания электрическая энергия преобразовывалась в магнитное поле в индукторе, о чем свидетельствовала наведенная на нем обратная ЭДС. При отключении питания такая же электрическая энергия возвращается индуктором в цепь в виде прямой ЭДС.Когда напряжение на катушке индуктивности увеличивается, возникает обратная ЭДС, а всякий раз, когда напряжение на катушке индуктивности уменьшается, возникает прямая ЭДС.
На практике обратная или прямая ЭДС, возникающая на катушке индуктивности, во много раз превышает приложенное напряжение. Если только индуктор подключен к источнику напряжения или индуктор подключен к цепи постоянного тока без какой-либо защиты, электрическая энергия, возвращаемая при размыкании переключателя, высвобождается в виде всплеска напряжения или искры на контакте переключателя.Если индуктивность велика или ток в цепи велик, энергия, выделяемая в форме дуги или искры на контакте переключателя, может даже сжечь или расплавить его. Этого можно избежать, если последовательно подключить резистор и конденсатор (RC) к переключающему контакту. Эта RC-сеть называется демпфирующей сетью . Он позволяет электрической энергии, выделяемой индуктором, заряжать и разряжать конденсатор, поэтому он не повреждает другие компоненты. Во многих схемах защитные диоды используются для защиты других компонентов схемы от обратной или прямой ЭДС катушки индуктивности или соленоида.
Катушка индуктивности в цепи переменного тока
Поскольку катушка индуктивности препятствует любому изменению тока, переменный ток отстает на 90 ° от напряжения переменного тока через катушку индуктивности. Первоначально, когда напряжение от источника подается на катушку индуктивности, ток через катушку индуктивности является максимальным и в противоположном направлении. При приложении напряжения ток течет через катушку индуктивности из-за индуцированной обратной ЭДС, противоположной приложенному напряжению. Индуцированное напряжение на катушке индуктивности всегда равно и противоположно приложенному напряжению в каждый момент времени.Когда приложенное напряжение возрастает от нуля до пикового значения, противодействующий ток через катушку индуктивности падает с максимума до нуля.
Когда приложенное напряжение падает с пикового значения до нуля, прямая ЭДС индуцируется на катушке индуктивности, заставляя ток через нее повышаться от нуля до пикового значения в противоположном направлении. Когда приложенный сигнал меняет полярность и достигает пикового значения в противоположном направлении, в катушке индуктивности снова индуцируется обратная ЭДС, вызывая падение противоположного тока с пикового значения до нуля.Когда приложенное напряжение снова падает до нуля в обратном направлении, в катушке индуктивности индуцируется прямая ЭДС, заставляя ток снова повышаться от нуля до своего пикового значения в противоположном направлении. Это продолжается для каждого цикла сигнала переменного тока.
Индуктивное реактивное сопротивление
Противодействие току из-за индуктивности отображается индуктивным реактивным сопротивлением. Амплитуда тока через катушку индуктивности обратно пропорциональна частоте приложенного сигнала напряжения.Поскольку напряжение на катушке индуктивности (обратная или прямая ЭДС) пропорционально индуктивности, амплитуда тока также обратно пропорциональна индуктивности. Таким образом, противодействие току из-за индуктивности в виде индуктивного реактивного сопротивления определяется следующим уравнением:
X L = 2πfL
= ωL
Соответственно, пиковая амплитуда тока через катушку индуктивности определяется следующим уравнением:
I пик = V пик / X L
= V пик / ωL
Где
I пик — пиковое значение переменного тока через катушку индуктивности.
В пик — пиковое значение переменного напряжения, приложенного к катушке индуктивности.
X L — индуктивное реактивное сопротивление.
Как и сопротивление и емкостное реактивное сопротивление, единицей измерения индуктивного реактивного сопротивления также является ом. Следует отметить, что в цепи нет потерь энергии из-за емкостного или индуктивного реактивного сопротивления, в отличие от сопротивления. Однако реактивное сопротивление может ограничивать уровни тока через конденсатор или катушку индуктивности.
Применение индукторов
Катушки индуктивности используются в цепях переменного тока.Они обычно используются в схемах аналоговой обработки и обработки сигналов в телекоммуникациях. Они также используются вместе с конденсаторами для проектирования схем фильтров. В телекоммуникациях индукторы также используются для снижения системных напряжений или токов короткого замыкания в линиях электропередачи. Благодаря соединению катушек индуктивности конструируются трансформаторы, которые используются для повышения или понижения напряжения переменного тока. Индукторы также используются для временного хранения электроэнергии в цепях SMPS и UPS. В цепях питания индукторы (где их называют фильтрующими дросселями) используются для сглаживания пульсирующих токов.
Поведение сигнала катушки индуктивности можно резюмировать следующим образом:
- Всякий раз, когда напряжение, подаваемое на катушку индуктивности, увеличивается, она генерирует обратную ЭДС, в результате чего ток через нее падает с максимального значения до нуля или ниже. Всякий раз, когда подаваемое напряжение уменьшается, индуктор создает прямую ЭДС, заставляя ток через него повышаться от нуля или уровня тока до максимального значения или более высокого уровня.
- Обратная ЭДС или прямая ЭДС остается на катушке индуктивности до тех пор, пока не будет приложено напряжение, и поэтому ток через нее не изменится.Когда приложенное напряжение достигает постоянного значения, обратная или прямая ЭДС падает до нуля, и постоянный ток течет через катушку индуктивности без какого-либо сопротивления, как в соединительном проводе.
- Из-за индуктивности скорость изменения тока в цепи замедляется. Если сигнал является переменным, ток всегда будет отставать от напряжения на 90 ° из-за индуктивности.
- Из-за индуктивного или емкостного реактивного сопротивления потери энергии отсутствуют. Энергия, запасенная индуктором в виде магнитного поля или конденсатором в виде электростатического поля, возвращается обратно в цепь при падении приложенного напряжения или в обратном направлении.Однако из-за реактивного сопротивления максимальный уровень тока (амплитуда токового сигнала) ограничен.
В следующей статье мы обсудим различные неидеальные характеристики и ключевые показатели эффективности катушек индуктивности.
Материал сердечника индуктора: сердце индуктора
Катушки индуктивности обманчиво просты. Однако при более внимательном рассмотрении обнаруживается основная сложность. Как еще вы можете объяснить множество типов материалов сердечника, типов обмоток, размеров, геометрии и широкого спектра применений? В этой статье будут рассмотрены три примера различных типов материалов: кремнистая сталь, порошок мягкого железа и ферриты.Мы также сосредоточимся на понимании свойств материала сердечника индуктора — его сердца.
Что такое магнитное ядро?
Магнитопровод индуктора изготовлен из специально сформированного материала с «мягкими» магнитными свойствами. Хотя магнитный сердечник физически твердый, он считается «мягким», если он не сохраняет значительного магнетизма. Магнитопровод обычно окружен аккуратно расположенными витками проволоки. Комбинация магнитного сердечника и обмоток дает измеримое свойство, называемое индуктивностью.Существуют различные типы «мягких» магнитных материалов, а также различные типы и формы магнитных сердечников. Магнитные сердечники и их обмотки можно рассматривать как миниатюрные электромагниты.
Существует множество возможных геометрических форм сердечника индуктора. Геометрия ядра зависит от различных факторов, в том числе от приложения; доступная монтажная площадь и объем; допустимое излучение; ограничения на обмотки; рабочая температура; и как будет монтироваться индуктор. Следовательно, геометрическая форма сердечника может иметь форму цилиндра, бобины, тороида или нескольких других сложных форм.
Кроме того, магнитный сердечник индуктора не обязательно должен быть цельным. Составные сердечники, каждая часть из которых изготовлена из одного и того же магнитного материала, иногда используются для чрезвычайно сложных форм или больших индукторов.
Ядра должны быть сконструированы и закончены с пониманием того, как будут установлены обмотки. Иногда обмотки наматываются непосредственно на сердечник. В других случаях обмотки могут быть намотаны на втулку, которую надевают на сердечник. Обратите внимание, что провод, используемый для обмоток индуктора, обычно изолирован, потому что при плотной намотке соседние витки могут закоротить.Однако тонкий утеплитель хрупок. При намотке непосредственно на сердечник магнитный материал не должен подвергать тонко изолированный провод грубым поверхностям или острым краям, которые могут прорезать изоляцию. Для размещения прямых обмоток хорошо спроектированный магнитопровод будет иметь гладкую поверхность намотки. При необходимости сердечник обеспечит радиус закругления.
Примеры материалов сердечника для индукторов включают кремнистую сталь, железный порошок и ферриты. Каждый из этих различных материалов имеет разные свойства при разных частотах, температурах и уровнях мощности.Стержни могут быть изготовлены методом литья, механической обработки или прессования. Стоимость материалов может стать существенным фактором для больших ядер с большей мощностью. Таблица 1 иллюстрирует разнообразие материалов сердечника.
Что делает магнитный сердечник?
Функционально магнитный сердечник индуктора хранит рекуперированную энергию. Разработчики схем определяют катушки индуктивности, способные принимать и возвращать энергию через определенные промежутки времени. С механической точки зрения сердечник индуктора служит опорой для его обмоток.В магнитном отношении сердечник индуктора обеспечивает среду для концентрации и сдерживания магнитного потока. Комбинация витков обмотки и объема магнитного материала устанавливает верхний предел максимально допустимого магнитного потока, который может выдержать сердечник. Плотность потока важна, потому что она связана с энергией. Более высокая плотность потока означает большее количество запасенной энергии. Магнитный поток аналогичен электрическому току в чисто резистивной электрической цепи. Магнитное сопротивление аналогично сопротивлению. Сердечник с низким сопротивлением может поддерживать относительно высокую плотность потока.Сердечник того же размера с высоким сопротивлением может поддерживать более низкую плотность потока.
Другой важный параметр керна — проницаемость. Проницаемость обратно пропорциональна сопротивлению. Керн с высоким сопротивлением имеет низкую проницаемость, и наоборот. Проницаемость — важный параметр, потому что его можно рассматривать как множитель потока. Для справки, считайте, что множитель потока свободного пространства равен единице (система cgs). Проницаемость керна всегда зависит от проницаемости свободного пространства.Таким образом, относительная магнитная проницаемость полезных магнитных материалов составляет от 10 до 10 000. Более практические значения относительной проницаемости находятся в диапазоне от 100 до 1000.
Катушка индуктивности преобразует электрическую энергию в магнитную. Эта магнитная энергия хранится в магнитном поле индуктора. Следовательно, энергия, накопленная в один момент времени, может оставаться в активной зоне до тех пор, пока она не понадобится позже. Контролируя скорость, с которой энергия накапливается и удаляется из магнитного поля, разработчики могут реализовать импульсные источники питания.Например, импульсные источники питания могут работать в диапазоне от десятков килогерц до нескольких мегагерц. Источники питания с более медленным переключением должны накапливать больше энергии за цикл, чем переключатели с более высокой частотой. В результате размер ядра больше для более низких частот переключения и меньше для более высоких частот переключения.
Для данной конфигурации обмотки и размера сердечника значение индуктивности индуктора будет выше для сердечника с более высокой магнитной проницаемостью. При тех же электрических условиях индуктор с более высоким значением индуктивности может хранить больше энергии, чем индуктор с более низким значением индуктивности. Таблица 2 иллюстрирует несколько приложений, в которых требуются магнитные сердечники.
Поведение различных материалов сердечника
В этом разделе мы рассмотрим поведение кремнистой стали, железного порошка и ферритовых материалов. Эти магнитомягкие материалы обладают свойствами проницаемости и удельного сопротивления. Несоответствие этих свойств делает разные материалы подходящими для разных дизайнерских приложений. Это еще один способ сказать, что не существует «лучшего» материала для всех приложений.
Кремниевая стальотносительно недорога и проста в формовании. Кроме того, кремнистая сталь — это металл с низким удельным сопротивлением. Низкое удельное сопротивление сердечника означает, что кремнистая сталь легко проводит электрический ток. В результате в материале сердечника могут протекать нежелательные вихревые токи. Вихревые токи способствуют нагреву и потерям в сердечнике. Кроме того, сердечник из кремнистой стали довольно легко достигает точки насыщения. В насыщенном состоянии сердечник не может накапливать дополнительную магнитную энергию. Быстрое насыщение приводит к сокращению рабочего диапазона.
Решением проблемы быстрого насыщения является создание воздушного зазора на пути магнитного потока. Воздушный зазор увеличивает сопротивление пути потока, что снижает проницаемость и индуктивность. Следовательно, сила тока, которую может выдержать ядро, увеличивается.
Порошок мягкого железа имеет более высокое удельное сопротивление, чем кремнистая сталь. Путем специальной обработки частицы железа изолированы друг от друга. Частицы смешиваются со связующим (например, фенольным или эпоксидным).Затем стержни придают окончательную форму. Затем для отверждения сердцевин используется процесс запекания. После отверждения множество крошечных воздушных зазоров объединяются, чтобы обеспечить эффект распределенного воздушного зазора. Другими словами, воздушный зазор распределен по сердечнику. Сердечники из железного порошка нашли широкое применение, когда необходимо учитывать потери в сердечнике.
По сравнению с другими магнитными материалами, такими как ферриты, распределенный воздушный зазор позволяет порошковым сердечникам сохранять более высокие уровни магнитного потока. Распределенный воздушный зазор также допускает более высокие уровни постоянного тока до наступления насыщения.
Феррит — это кристаллический магнитный материал, состоящий из оксида железа и других элементов. Смесь обрабатывается при высокой температуре и превращается в кристаллическую молекулярную структуру. В отличие от других ферриты — это керамические материалы с магнитными свойствами. Ферриты обладают высокой магнитной проницаемостью и высоким удельным электрическим сопротивлением. Следовательно, нежелательные вихревые токи значительно уменьшаются за счет ферритовых сердечников. Благодаря высокому удельному сопротивлению ферриты идеально подходят для использования в качестве индукторов. Например, ферритовые шарики часто используются для уменьшения паразитных колебаний и для общей фильтрации на уровне выводов компонентов.Для этого типа широкополосного компонента требуется широкополосный низкодобротный компонент, чтобы обеспечить высокий импеданс в широком диапазоне частот. Таблица 3 суммирует некоторые важные свойства этих магнитных сердечников.
Магнитные домены или почему материалы разные
Различные материалы имеют разные магнитные характеристики. Интуитивно понятно, что должен существовать какой-то основной механизм, который отличается для разных материалов. Ответ находится в том, что мы называем «магнитными доменами».«Магнитные домены — это намного больше, чем модель простых стержневых магнитов, которые выровнены или не выровнены. Хотя модель стержневого магнита полезна на макроуровне, она неадекватна на микроуровне. Магнитный домен — это объемное пространство внутри материала. У этого тома есть определенные элементарные свойства. Однако в одном магнитопроводе имеется множество магнитных доменов разных размеров и форм. Кроме того, различиям способствуют загрязнения и дефекты материала.
Требуется работа, чтобы изменить энергетическое состояние каждого (отдельного) домена.Поскольку домены имеют разную форму и размер, для разных доменов требуется разный объем работы. Конечно, на макроуровне мы можем игнорировать микроструктуры. Однако именно эти свойства определяют особенности каждого материала. Таким образом, мы можем понять, почему практически невозможно предоставить два ядра с одинаковыми свойствами.
Рассмотрим магнитный поток, действующий на магнитные области и внутри них. Магнитные домены расширяются и сжимаются, как пузыри.Магнитные домены сливаются и извиваются, как реки. Иногда домены текут внутри установленных каналов, а иногда расходятся, как при наводнении. Размеры различных доменов, близость других доменов и различные топологические соображения гарантируют отсутствие единообразия. Неудивительно, что разные магнитные материалы имеют разные характеристики.
Основные материалы
Воздух |
Сплавы |
Аморфный |
Железный порошок |
Марганцево-цинковый феррит |
Молибденовый порошок пермаллоя |
Никель-цинковый феррит |
Сендуст |
Кремниевая сталь |
Приложения с использованием магнитных сердечников
Регулятор переключения наддува |
Понижающий импульсный регулятор |
Регулятор переключения понижения-повышения |
Фильтр синфазных помех |
Фильтр EMI / RFI |
Прямой преобразователь |
Обратный преобразователь |
Резонансный преобразователь |
Важные магнитные параметры
Коэрцитивная сила |
Температура Кюри |
Плотность потока |
Проходимость |
Нежелание |
Удельное сопротивление |
Насыщенность |
Для получения дополнительной информации об этой статье, CIRCLE 343 на сервисной карте считывателя
Индукционный нагреватель
Индукционный нагреватель — интересное устройство, позволяющее быстро нагревать металлический предмет.При достаточной мощности можно даже расплавить металл. Индукционный нагреватель работает без ископаемого топлива и может отжигать и нагревать предметы различной формы. Я решил сделать индукционный нагреватель, способный плавить сталь и алюминий, поэтому я собрал устройство, которое выдает около 3 киловатт! Затем я построил блок мощностью 10 кВт, который мог самостоятельно фиксировать резонансную частоту. Оба агрегата были способны левитировать металлы. В этом руководстве много страниц, заполненных практической и теоретической информацией, которая поможет вам в моих усилиях.Просто продолжайте нажимать «Далее», и в конце концов вы попадете на схемы. У меня их несколько для инверторов меньшего и большего размера.
*****
Я собрал несколько плейлистов на Youtube, в которых объясняются более тонкие детали создания надежного индукционного нагревателя. На моем канале есть видеоролики, показывающие, как это работает, и видеоролики, объясняющие, как проектировать и делать различные части. Мой хороший плейлист —-> здесь, но на YouTube-канале Imsmoother есть еще больше видео.
*****
В первой части этого руководства я расскажу о моей разработке инвертора мощностью 3 кВт. Моей первоначальной целью было быстрое нагревание металлов. Моей следующей целью было левитировать металлы. Мне это удалось, но я понял, что не могу левитировать из твердой меди и стали. Их плотность была слишком велика для магнитного поля. Это была моя конечная цель: левитировать и удерживать расплавленную медь и сталь. В конце этого урока я перейду к разработке блока мощностью 10 кВт, в котором реализована эта цель.Я также остановлюсь на проблемах, которые пришлось преодолеть, чтобы этого добиться.
Начнем.
Мой индукционный нагреватель — инвертор. Инвертор использует источник постоянного тока и преобразует его в переменный ток. Электропитание переменного тока приводит в действие трансформатор, который соединен с последовательным баком LC. Частота инвертора устанавливается равной резонансной частоте резервуара, что позволяет генерировать очень высокие токи внутри катушки резервуара. Катушка соединена с заготовкой и создает вихревые токи.2. Заготовка похожа на однооборотную катушку; рабочая катушка имеет несколько витков. Таким образом, у нас есть понижающий трансформатор, поэтому в заготовке генерируются еще более высокие токи.
Я хотел бы поблагодарить Джона Дирмонда, Тима Уильямса, Ричи Бернетта и других участников форума 4hv за неоценимую помощь за то, что они помогли мне разобраться в этой теме. А теперь, прежде чем мы поговорим подробнее, давайте посмотрим на несколько изображений того, на что он способен:
Позже дам ссылку на видео, где он работает.Вот инвертор:
Теперь я перейду к каждой части. Затем я дам схемы, расскажу о том, как вы можете построить это устройство.
ДрайверZVS — Адам Мюнхен
«Драйвер ZVS» — это очень простая схема, которая может генерировать большое количество энергии с эффективностью около 90%. Справа находится упрощенная версия генератора, известная как «преобразователь Баксандалла».
При подаче питания на + V ток начинает течь через обе стороны первичной обмотки и попадает на стоки МОП-транзисторов.Одновременно это напряжение появляется на воротах обоих МОП-транзисторов и начинает их включать. Поскольку нет двух абсолютно одинаковых компонентов, один МОП-транзистор включается немного быстрее, чем другой, и через него может протекать больший ток. Дополнительный ток, протекающий на этой стороне первичной обмотки, отбирает ток затвора у другого блока и начинает его выключать. Конденсатор образует резервуар LC с первичной обмоткой, и напряжение продолжает расти и падать синусоидально. Если бы не этот конденсатор, ток продолжал бы увеличиваться, пока сердечник трансформатора не насыщался и не взорвались МОП-транзисторы.
Представьте, что Q1 включился первым. Напряжение в точке Y будет близко к земле, в то время как напряжение в Z поднимается до пика и падает обратно, когда резервуар LC проходит один полупериод. Когда напряжение на Z проходит через ноль, ток затвора на Q1 снимается, и МОП-транзистор выключается. Напряжение в точке Y теперь начинает расти, и Q2 включается. Этот МОП-транзистор зажимает напряжение в точке Z на землю; что-то, что гарантирует, что Q1 остается выключенным. Этот же процесс повторяется для Q2, завершая другой полупериод, и генератор продолжает цикл.Чтобы генератор не потреблял огромные пиковые токи и не взорвался, L1 добавлен последовательно с + V в качестве дросселя. Импеданс LC — это то, что ограничивает фактический ток (дроссель просто смягчает пики тока).
Внимательный взгляд заметит, что этот генератор работает при нулевом напряжении (ZVS), что означает, что МОП-транзисторы переключаются, когда на них имеется нулевое напряжение. Это хорошо, потому что позволяет МОП переключаться, когда они несут наименьшую мощность; то, что по большей части устраняет коммутационные потери, которые выделяют огромное количество тепла.Это означает, что нужны только небольшие радиаторы, даже при генерации 1000 Вт!
Поскольку мазилли является резонансным генератором, частота определяется индуктивностью первичной обмотки трансформатора и конденсатора. Вы можете использовать следующую формулу, чтобы выяснить это:
f = 1 / (2π * √ [ L * C] )
f — частота в герцах
L — индуктивность первичной обмотки по Генри
C — емкость конденсатора в фарадах
Сейчас на самом деле МОП-транзисторы являются довольно хрупкими компонентами, и если затворы находятся на +/- более 30 В от источника, МОП-транзисторы будут разрушены или, по крайней мере, значительно ухудшены.Чтобы предотвратить возникновение этого сценария, нам понадобится защита ворот; что-то легко добавляемое с помощью нескольких дополнительных компонентов. См. Схему справа.
• Резисторы на 470 Ом ограничивают ток, который заряжает затворы, поскольку слишком большой ток затвора может вызвать повреждение.
• Резисторы 10 кОм опускают ворота на землю для предотвращения защелкивания; процесс, при котором МОП-транзистор застревает.
• Стабилитроны предотвращают превышение напряжения затвора 12, 15 или 18 В в зависимости от используемых стабилитронов.
• Диоды UF4007 опускают ворота на землю, когда напряжение на противоположной стороне резервуара равно заземлению.
Можно заметить, что вместо зарядки ворот с помощью резервуара LC мы вместо этого используем + V для их зарядки и мы используем резервуар LC для их разрядки через сверхбыстрые диоды. Это улучшает общую производительность схемы.
Следующая схема сделана очень простой для понимания, я надеюсь, она вам понравится.
Из-за небольшой доли черной магии, известной как резонансное повышение, напряжение в резервуаре LC будет около pi * vcc, поэтому вам необходимо убедиться, что ваши МОП-транзисторы могут выдерживать это напряжение.Хорошее практическое правило — использовать МОП-транзисторы, рассчитанные на 4-кратное превышение напряжения, которое вы планируете подавать на генератор, и IRFP250 или лучше IRFP260 является хорошим МОП-транзистором для этой задачи. Вам понадобятся радиаторы для МОП-транзисторов, но они не должны быть большими. Их нельзя ставить на один и тот же радиатор, если не используются изолирующие прокладки, поскольку металлическая задняя часть МОП-транзистора электрически не изолирована (она подключена к стоку). Также не забудьте использовать термопрокладку при установке радиатора, иначе термотрансферная передача будет плохой.
Конденсатор должен быть исправным, колпачок из MKP, слюды или майлара — хороший вариант. Не используйте электролитический колпачок, он, несомненно, взорвется. Две первичные обмотки также должны быть намотаны в одном направлении, иначе генератор не будет работать. Генератор также не сможет работать, если в сердечнике трансформатора нет воздушного зазора, поэтому всегда проверяйте его наличие.
Ниже приведено видео на YouTube, на котором генератор питает обратный трансформатор при напряжении 12, затем 24, затем 36 В.Если вы нетерпеливы, перейдите к 0:47 для 36 В.
Проблемы со схемой
Генератор имеет один фатальный недостаток: он любит взрываться выше 70 В. 60В, делает хорошо, 70 это мэх… 80 КАБЛУЕЙ. Проблема в том, что напряжение выше 70 В, как правило, настолько велико, что диоды, отвечающие за отключение вентилей, не могут полностью этого сделать, и колебания прекращаются, когда остается включенным один МОП-транзистор. По сути, это короткое замыкание, поэтому мосфет реагирует самоубийством. Всем, кто читает эту статью, я предлагаю вам задачу: исправить эту проблему.Тот, кто сделает это первым, получит подарок. Не знаю что, но что-то будет. Неон Джон попытался исправить это, но это все еще ненадежно…
ОБНОВЛЕНИЕ: Я частично решил проблему, разместив проволочный резистор на 0,5 Ом последовательно с катушкой индуктивности фильтра. Теперь ничего не произойдет, если индуктивность нагрузки резко упадет. Тем не менее, все еще взрывается, когда VCC> 70 В. ∎
Hack A Year — DIY Inductive Charger
Описание схемы:
В левом верхнем углу вы можете увидеть вход источника питания постоянного тока 18 В и + 5 В, +3.Регуляторы на 6 В. + 5 В требуется для управления МОП-транзисторами силового инвертора и операционных усилителей аналоговой обработки; + 3,6 В требуется для MCU. Я разделил цифровую и аналоговую секции резисторами на 1 Ом, чтобы минимизировать цифровую шумовую связь с аналоговыми секциями. Выбран MCU MSP430F2274. Он имеет следующие аппаратные характеристики:
Два модуля захвата / управления. Один используется для генерации ШИМ с регулируемой частотой и рабочим циклом.
Я планирую использовать второй модуль таймера для определения синхронизации импульсов связи.
Интегрированные программируемые операционные усилители: я использую один в качестве усилителя с программируемым усилением для обработки сообщений.
10-битный АЦП SAR с 15 мультиплексированными каналами: используется для измерения входного напряжения / тока, обнаружения резонанса и температуры катушки передатчика.
Много ввода / вывода: полезно для отладки
Последовательный порт (UART) Используется для отладки / связи с компьютером
Аналоговая обработка:
Входное напряжение и ток на преобразователе, инверторе и катушке измеряются так, система знает входную мощность.Сила тока измеряется датчиком тока высокого напряжения LT6105. Это очень полезная ИС, потому что она имеет очень широкий диапазон синфазных помех (0 В — ~ 40 В). Выходной сигнал является током, и его можно использовать для создания выходного напряжения, пропорционального опорным сигналам, отличным от земли; это полезно в цепях с раздельным питанием. Коэффициент усиления можно регулировать одним резистором R17. Операционный усилитель буферизует схему для управления АЦП. На входах АЦП рекомендуется минимальная емкость из-за архитектуры SAR. Резистор на 200 Ом полезен для стабилизации выходного драйвера операционного усилителя при управлении емкостными нагрузками.Для измерения входного напряжения используется простой резисторный делитель (буферизованный операционным усилителем).
Я создал монитор резонанса, измеряя напряжение в узле резонанса, создаваемое катушкой Tx и резонансными конденсаторами. Напряжение делится и выпрямляется полуволной. Конденсатор C22 и резистор R21 образуют фильтр нижних частот, который фильтрует переменный ток до уровня постоянного тока. На выходе этого резонансного детектора присутствует постоянное напряжение, пропорциональное переменному напряжению, присутствующему на резонансном узле. Я предполагаю, что это будет использоваться для калибровки и / или определения фактической резонансной частоты катушки tx.