Контрольная опрессовка газопроводов: Опрессовка газа в многоквартирном доме
Контрольная опрессовка (КО) — СтудИзба
Контрольная опрессовка (КО).
Информация: ПБ в ГХ п.6.25…6.31.
Контрольная опрессовка – испытание ГП и газового оборудования низким давлением воздуха с целью обнаружения мельчайших утечек газа, т.е. проверка герметичности газового оборудования.
КО проводится воздухом или инертным газом. Она проводится перед каждым пуском газа, после ремонта, с началом отопительного сезона, при первичном пуске газа в газопроводы или оборудование. Перерыва между пуском газа и КО быть не должно. Результат контрольной опрессовки записывается в НАРЯД-ДУПУСК.
Люди также интересуются этой лекцией: Лекция 1.
Наружные ГП всех давлений подлежат КО давлением 0,02 МПа:
0,02 МПа = 0,2 кгс/см
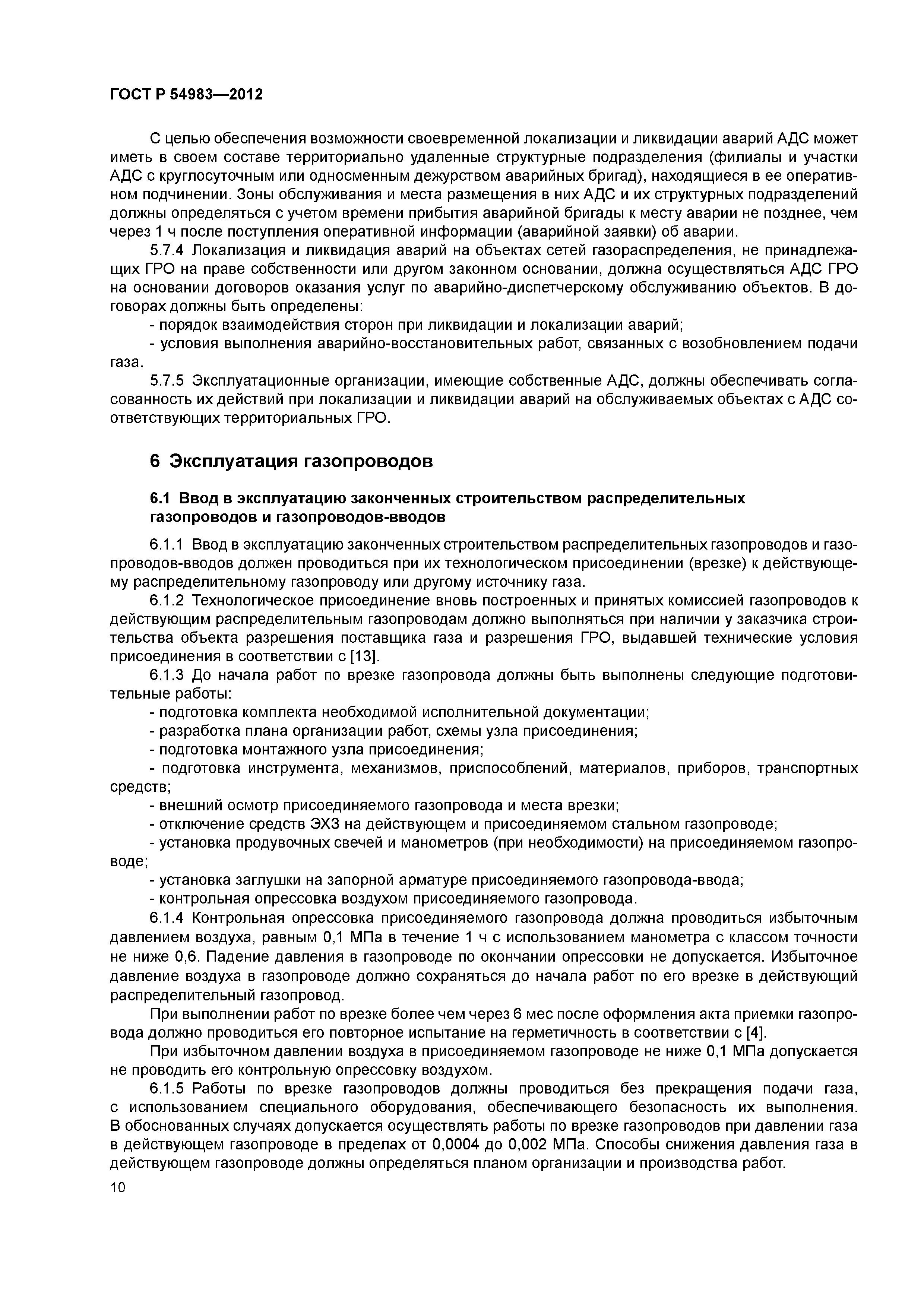
Падение давления не должно превышать 10 даПа (или 10 мм вд. ст.) за 1 час.
КО внутренних газопроводов промышленных и сельскохозяйственных производств, котельных, ГРП, ГРУ должно проводиться давлением 0,01 Мпа (1000 мм вд. ст.). Падение давления не должно превышать 60 даПа (60 мм вд. ст.) за 1 час.
КО внутренних газопроводов и газового оборудования общественных, жилых зданий, административных, должна проводиться давлением 500 даПа (500 мм вд. ст.). Падение давления не должно превышать 20 даПа (20 мм вд. ст.) за 1 час.
Опрессовка газопроводов — Энциклопедия по машиностроению XXL
После опрессовки газопровода, выявления мест неплотности и их устранения проверяют регулятор давления на герметичность, используя давление воздуха в системе газопроводов ГРУ.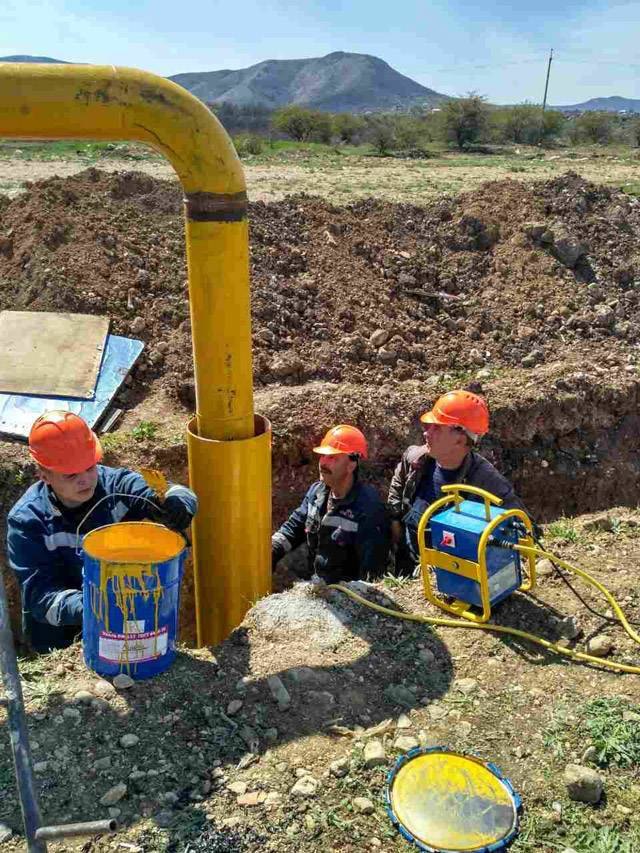
Перед растопкой котла на газе должна быть проведена контрольная опрессовка газопроводов котла воздухом и проверена герметичность закрытия запорной арматуры перед горелками в соот-в ствии с «Типовой инструкцией по эксплуатации газового хозяйства ТЭС, работающих на природном газе . [c.229]
Обход тепловых сетей 150 Ограждения 130 Окраска трубопроводов 149 Опрессовка газопроводов 25 Опробование вспомогательных механизмов 130, 179
Пуск газа без контрольной опрессовки газопровода при отсутствии ответственного руководителя указанной бригады категорически запрещается. [c.169]
Отдельные участки трубопровода соединяют между собой сваркой. После опрессовки газопровода места сварных стыков изолируют непосредственно в траншее.
[c. 454]
Приступая к продувке газопроводов котельной, ответственное лицо должно еще раз убедиться в полной технологической готовности хотя бы одного котла, проинструктировать персонал котельной, расставив его у рабочих мест. Желательно проверить плотность рабочих кранов перед горелками котлов, подготовленных к пуску, путем опрессовки их воздухом на открытые концы . [c.67]
Проверять плотность газопроводов, арматуры и приборов с по.мощью огня не разрешается. Если осмотренные и подвергшиеся контрольной опрессовке участки [c.191]
Перед врезкой в действующую сеть, независимо от давления газа, все газопроводы подвергают контрольной опрессовке воздухом на давление 2000 мм вод. ст., при этом в течение I ч допускается падение давления не более 10 мм вод. ст. [c.149]
После контрольной опрессовки на присоединяемом газопроводе закрывают все краны и задвижки, кроме [c.149]
Подземные и надземные газопроводы независимо от рабочего давления подлежат контрольной опрессовке воздухом на давление
[c. 904]
Проверяются также электрические силовйе линии к приборам автоматизации и сборкам питания, отлаживается работа оборудования котлоагрегатов. Работы по расконсервации начинаются с установки временно снятых приборов и датчиков и снятия защитных чехлов с остальных приборов. Работы ведутся в такой последовательности производится контрольная опрессовка газопроводов, газового оборудования и импульсных линий на герметичность с предварительной продувкой импульсных линий.
После опрессовки газопровода присоединяют газовые приборы. Одновре.мекно следует соединить водонагреватели с газоходами в стенах. [c.478]
Контрольная опрессовка газопроводов является обязательной операиией перед пуском газа. Газопроводы котельных подвергаются контрольной опрессовке воздухом на давление 1 ООО м.н вод. ст., падение давления за 1 ч не должно превышать 60 мм вод. ст. [c.904]
Простейшим является случай истечения в атмосферу газа через отверстие постоянного сечения из резервуара постоянного объема (V= idem).
При текущем ремонте газового оборудования и внутрицеховых газопроводов выполняют следующие работы разборку, смазку, перенабивку сальников, проверку хода и плотности закрытия (при необходимости притирку или замену) запорных и предохранительных устройств, контрольную опрессовку газового оборудования по нормам Правил безопасности в газовом хозяйстве, чистку газовых горелок, осмотр тоннелей, горелочных насадок, топок, газоходов, шиберов, проверку и настройку автоматики безопасности и регулирования. [c.170]
Проверка газопроводов производится путем их внешнего осмотра, опробования легкости хода установленной арматуры и контрольной опрессовки воз-духо. м на давление 1000 мм вод. ст. Падение давления не должно превышать 60 мм вод. ст. в течение 1 ч. Проверка газопроводов и котлоагрегата должна производиться под непосредственным руководством начальника котельной или его заместителя. Результаты проверки оформляются актом с указанием состояния проверенных узлов котлоагрегата и газопроводов. Пуск агрегатов после длительной остановки выполняется под непосредственным руководством начальника котельной или его заместителя.
[c.270]
Если объект, принятый комиссией, не был введен в эксилуата-нию в течение G мес., то при вводе его в эксплуатацию должно быть произведено повторное испытание газопроводов на плотность (помимо контрольной опрессовки непосредственно перед пуском газа). [c.904]
Для опрессовки изделие заполняют контрольным веществом под давлением, несколько превышающим рабочее, и выдерживанп-нзделие под этим давлением в течение определенного времени. Величина давления 1 время опрессовки ог. релеляются техническими условиями на изделие. Например, магистральные газопроводы испытывают на прочность в течение 6 ч при давлении, превышающем рабочее на 10%.
[c.253]
Работа по охране труда на предприятиях, связанных с переоборудованием серийных тракторов в газобаллонные, испытаниями газовой системы питания на герметичность и ее опрессовкой под давлением 20 МПа (200 кгс/см ), проверкой работоспособности двигателей осуществляется в соответствии с «Правилами безопасности при ремонте и техническом обс уживании мащин и оборудования в системе Газпрома СССР», «Правилами устройства и безопасной эксплуатации сосудов, работающих под давленфм ПБ-10-115-96», «Правилами устройства и безопасной эксплуатации стационарных компрессорных установок, воздухопроводов и газопроводов», «Требованиями пожарной безопасности для предприятий, эксплуатирующих автотранспортные средства на компримированном природном газе РД-3112199-98» и настоящими Правилами.
Полученный материал, включающий результаты контроля глубины трещин в процессе испытания дефектных труб, а также анализ вида излома, образовавшегося при разрушении плетей, однозначно показывает, что при нагружении внутренним давлением труб со стресс-коррозионными дефектами увеличение размера (глубины) существующих в дефектной трубе трещин может происходить задолго до момента разрыва трубы. По этой причине практика переиспытания ( опрессовки ) действующих газопроводов на предмет обнаружения дефектов типа продольных стресс-коррозионных трещин может увеличивать размеры докритических трещин, оставшихся невыявленными при использованном уровне испытательного давления.
[c.123]
Подготовка ГРП к пуску, останову
Подготовка ГРП к пуску включает в себя следующие мероприятия:
Проверка общего состояния ГРП: чистота помещения и территории ГРП, исправность системы освещения ГРП, наличие и исправность противопожарного инвентаря, знаков безопасности, а также работоспособность приборов, обеспечивающих непрерывный контроль содержания газа в воздухе помещения ГРП и сигнализирующих об опасной концентрации газа в этом помещении.
Контрольная опрессовка. Выполняется ремонтным персоналом перед подачей газа в газопроводы ГРП при переводе их из режима консервации или ремонта в рабочий режим. Порядок действий:
Дать заявку дежурному персоналу цеха ТАИ на сборку электрических схем дистанционного управления арматурой, расположенной на газопроводах ГРП. Опробовать дистанционное управление оперативной арматурой с контролем по дистанционным указателям положения.
Контрольная опрессовка газопроводов и оборудования ГРП проводится сжатым воздухом с давлением в газопроводе при опрессовке 0,01 МПа. Падение давления не должно превышать 600 Па за 1 час. Для контроля давления при опрессовке применяют U-образный манометр, заполненный водой.
Испытания проводятся после выравнивания температуры воздуха в газопроводах ГРП с окружающей средой.
Результаты контрольной опрессовки должны записываться в нарядах-допусках на выполнение газоопасных работ и в оперативный журнал ГРП.
Необходим периодический ремонт промышленных зданий? Вам не обойтись без бетоносмесителей, растворосмесителей — см. на http://www.bdscompany.com.ua/produktsiya/betonomesiteli-rastvorosmesiteli
Ввод в эксплуатацию газопроводов и газового оборудования предприятий
Законченные строительством наружные и внутренние газопроводы до ввода в эксплуатацию необходимо испытать на герметичность воздухом. Для испытания газопровод следует разделить на отдельные участки, ограниченные заглушками или запорными устройствами перед газоиспользующим оборудованием, с учетом допускаемого перепада давления для соответствующей арматуры. Если арматура, оборудование и приборы не рассчитаны на испытательное давление, то вместо них на время испытания следует установить заглушки.
Газопроводы производственных, общественных, жилых зданий и котельных следует испытать на участке от отключающего устройства на вводе в здание до кранов газоиспользующего оборудования.
Испытание производится строительно-монтажной организацией в присутствии представителя эксплуатационной организации. До начала испытаний на герметичность газопроводы следует выдерживать под испытательным давлением в течение времени, необходимого для выравнивания температуры грунта с температурой воздуха в газопроводе.
Испытание производится путем нагнетания в газопровод воздуха и создания в нем необходимого испытательного давления. Время выдержки под давлением и значение испытательного давления стальных подземных газопроводов принимают в соответствии с таблицей ниже.
В таблице ниже приведены нормы испытаний полиэтиленовых газопроводов, стальных газопроводов, газопроводов и оборудования ГРП, а также внутренних газопроводов зданий.
Приемка законченного строительством газопровода производится специально созданной приемочной комиссией, которая должна проверить представленную исполнительную документацию и соответствие сооруженного газопровода этой документации, требованиям СНиП и правил безопасности в газовом хозяйстве. Комиссия имеет право проверить любые участки газопровода, провести разборку, просвечивание или вырезку стыков, повторное испытание газопроводов. Если объект принимается, то оформляется акт, являющийся разрешением на ввод газопровода в эксплуатацию.
Присоединение к действующим газопроводам вновь построенных газопроводов и объектов должно производиться только перед пуском газа в эти газопроводы и объекты. До пуска газа в газопроводы необходимо осмотреть газовые сети ГРП, ГРУ и проверить исправность всего оборудования.
Все газопроводы и газовое оборудование перед их присоединением к действующим газопроводам, а также после ремонта должны подвергаться внешнему осмотру и контрольной опрессовке бригадой, которая производит пуск газа. Контрольная опрессовка производится воздухом или инертным газом давлением 0,02 МПа, при этом падение давления не должно превышать 10 даПа за 1 ч.
Контрольной опрессовке подвергаются также газопроводы и оборудование ГРП. Опрессовка производится давлением 0,01 МПа, при этом падение давления не должно превышать 60 даПа за 1 ч.
Наружные газопроводы всех давлений подлежат контрольной опрессовке давлением 0,02 МПа, падение давления не должно превышать 10 даПа за 1 ч.
Контрольная опрессовка внутренних газопроводов промышленных и сельскохозяйственных предприятий, котельных, газопроводов к оборудованию производственного характера в общественных зданиях должна производится давлением 0,01 МПа, падение давления не должно превышать 60 даПа за 1 ч.
Первоначальный пуск газа в газовые сети промышленных предприятий разрешается только после завершения испытаний и приемки газового хозяйства.
На газифицируемых предприятиях кроме акта приемки газового хозяйства должны быть:
- приказ о назначении ответственного за газовое хозяйство предприятия;
- инструкция по эксплуатации газопроводов и газового оборудования;
- инструкция по технике безопасности при эксплуатации и ремонте газопроводов и газового оборудования.
При вводе в эксплуатацию газового хозяйства предприятий присоединение их газовой сети к распределительным газопроводам и пуск газа в сеть предприятий должны производиться территориальным трестом газового хозяйства на основании заявки предприятия.
Газопроводы до пуска газа должны продуваться газом до вытеснения всего воздуха. Окончание продувки определяют путем анализа или сжигания отбираемых проб, при этом объемная доля кислорода в пробе газа не должно превышать 1 % по объему, а сгорание газа должно происходить спокойно, без хлопков.
При необходимости освобождения от газа газопроводы должны продуваться воздухом или инертным газом до полного вытеснения газа. Окончание продувки определяется путем анализа, при этом остаточная объемная доля газа в продуваемом воздухе не должна превышать 20 % от нижнего предела воспламеняемости. Во время продувки газопроводов газовоздушная смесь должна выпускаться в места, где исключена возможность попадания ее в здания, а также воспламенения от огня.
Перед пуском газа необходимо проверить состояние отключающих устройств и наличие заглушек. Подача газа в цеха и на агрегаты производится персоналом газовой службы предприятия в присутствии представителя территориального газового треста (конторы). Для пуска и наладки особо сложного газового оборудования можно привлекать специализированные пусконаладочные организации.
Объем и последовательность работ при пуске газа в котлы, печи и агрегаты предприятия отражаются в специально разработанных и утвержденных инструкциях.
В помещениях, где установлены газопотребляющие агрегаты, необходимо периодически контролировать содержание в воздухе газа и оксида углерода. При этом все обнаруженные неисправности и утечки газа должны немедленно устраняться, после чего производится повторная проверка воздушной среды.
Необходимо убедиться, что переводимые на газовое топливо печи и агрегаты надежно отключены от газовой сети. Проверка проводится путем осмотра положения отключающих устройств на подводящих газопроводах агрегатов и на продувочных свечах.
Ввод в эксплуатацию внутренних газопроводов и газоиспользу- |Ьщего оборудования производится после проведения пусконаладочных работ.
Наладку ГРУ и газоиспользующего оборудования производит специализированная организация. В состав пусконаладочных работ входят:
- наладка газоиспользующего оборудования и ГРУ, средств автоматического регулирования и безопасности;
- наладка теплоутилизационных устройств и вспомогательного оборудования, систем контроля и управления технологическими процессами;
- определение режимов работы газового оборудования с разработкой режимных карт, обеспечивающих эффективное использование газа.
При этом пусконаладочные работы на газоиспользующем оборудовании должны выполняться на газовом и на резервном топливе. Если топливным режимом предусмотрено применение резервного топлива, разрешение на пуск газа на газоиспользующее оборудование выдается только после завершения строительства резервного топливного хозяйства.
Перед пуском газа необходимо проверить:
- исправность топки и газоходов, запорных и регулирующих устройств;
- исправность КИП, питательных устройств, арматуры, дымососов и вентиляторов, наличие естественной тяги; исправность газового оборудования;
- исправность отключающих устройств, при этом необходимо убедиться, что вся запорная арматура на газопроводах закрыта, а краны на продувочных газопроводах — открыты;
- отсутствие заглушек перед и после предохранительных клапанов, на питательной, спускной и продувочной линиях;
- заполнение котла водой до отметки низшего уровня;
- отсутствие падения уровня воды в котле и пропуска воды через фланцы и арматуру.
При пуске газа необходимо продуть газопроводы газом через продувочные свечи, установленные перед горелками, постепенно открывая задвижку на ответвлении газопровода к газоиспользующей установке, до тех пор, пока газопровод заполнится газом.
По окончании продувки необходимо:
- закрыть кран на продувочной свече;
- убедиться в отсутствии утечек газа из газопроводов, газооборудования и арматуры путем обмыливания или с помощью приборов;
- проверить по манометру соответствие давления газа, а при использовании горелок с принудительной подачей воздуха на горение — дополнительно соответствие давления воздуха установленному давлению;
- отрегулировать тягу.
Перед розжигом газоиспользующей установки необходимо провентилировать топки и газоходы путем открытия дверок топки, поддувала, шиберов для регулирования подачи воздуха, заслонок естественной тяги, а при наличии дымососов и вентиляторов — путем их включения.
Включение дымососов во взрывоопасном исполнении производится только после проветривания топок естественной тягой и после проверки исправности дымососа.
Порядок включения горелок зависит от их конструкции, расположения на газоиспользующем оборудовании, типа запального устройства, типа автоматики безопасности и регулирования. Последовательность действий при розжиге горелок определяется в соответствии с требованиями производственной инструкции и ОСТ.
Розжиг горелок с помощью переносного запальника осуществляется в следующей последовательности:
- разжечь запальник и ввести его в топку к устью включаемой основной горелки;
- медленно открывая отключающее устройство перед горелкой, произвести пуск газа, следя за тем, чтобы воспламенение его произошло сразу, одновременно начать подачу воздуха;
- постепенно увеличивая подачу газа и воздуха, отрегулировать разрежение в топке и факел горелки;
- после получения устойчивого факела погасить запальник и удалить его из топки.
Розжиг горелок запально-защитным устройством осуществляется в следующей последовательности:
- повернуть ключ управления газоиспользующей установкой в положение «Розжиг».
При этом срабатывает запально-защитное устройство: включается реле времени, открывается газовый электромагнитный клапан запальника, включается устройство зажигания;
- при погасании пламени запальника контрольный электрод запально-защитного устройства дает импульс на отклонение катушки зажигания;
- если пламя запальника устойчивое, закрыть кран газопровода безопасности и полностью открыть запорное устройство перед горелкой.
Для розжига основной горелки с принудительной подачей воздуха необходимо:
- закрыть заслонку на воздухопроводе перед горелкой;
- приоткрыть запорное устройство перед горелкой и установить давление газа, соответствующее устойчивому режиму горения;
- при устойчивом пламени основной горелки приоткрыть шибер, регулирующий подачу воздуха на горение;
- отрегулировать разрежение в топке;
- постепенно увеличивать теплопроизводительность горелки, медленно повышая сначала давление газа, а затем давление воздуха, одновременно контролируя разрежение в топке.
Для розжига инжекционных горелок необходимо:
- открыть воздушный шибер и отрегулировать разрежение в топке;
- постепенно увеличивать теплопроизводительность горелки, увеличивая давление газа и контролируя разрежение в топке.
При наличии у газоиспользующей установки нескольких горелок их розжиг производится последовательно. Если при розжиге происходит отрыв, проскок или погасание пламени всех или части зажженных горелок, следует немедленно прекратить подачу газа, убрать из топки запальник и провентилировать топку и газоходы в течение времени, указываемого пусконаладочной организацией. Только после этого можно приступить к повторному розжигу горелок.
Если котлы, печи или другие установки работают на различных видах топлива и имеют общий боров, пуск котлов, печей и установок, работающих на газовом топливе, следует производить при неработающих агрегатах на других видах топлива.Гидростатические испытания — PetroWiki
Гидростатические испытания — это способ проверки сосудов под давлением, таких как трубопроводы, водопровод, газовые баллоны, котлы и топливные баки, на прочность и герметичность.
Испытания трубопроводов
Гидроиспытания труб и/или трубопроводов проводятся для выявления дефектных материалов, которые не были обнаружены ранее, чтобы гарантировать, что любые оставшиеся дефекты достаточно незначительны, чтобы можно было работать при проектном давлении, выявить возможные утечки и служить в качестве окончательной проверки целостности построенного система.
Подземные трубопроводы
Подземные нефте- и газопроводы высокого давления испытывают на прочность путем создания в них давления не менее 125% от их максимального рабочего давления (MAOP) в любой точке их длины. Поскольку многие магистральные трубопроводы рассчитаны на кольцевое напряжение стали, равное 80 % от заданного минимального предела текучести (SMYS) при MAOP, это означает, что сталь подвергается напряжению до SMYS и выше во время испытаний, и испытательные участки должны быть выбраны таким образом, чтобы обеспечить чтобы не происходило чрезмерной пластической деформации.
Проверка герметичности
Испытание на герметичность выполняется путем сопоставления изменений измеренного давления в испытательной секции с теоретическими изменениями давления, рассчитанными на основе изменений измеренной температуры испытательной секции.
Ссылки
Примечательные статьи в OnePetro
Кавахара Ю., Умехара Ю., Иидзука Х. и Кикучи К. 2006. Разработка системы гидростатических испытаний морской водой для резервуара для хранения СПГ на земле. НАСЕ Интернэшнл. OnePetro
Пауэлл, Д.Э., Меланкон, Б., и Винтерс, Р. Х. 2011. Руководство по проведению испытаний на гидростатическое давление и управление увеличенным временем выдержки при сухой/мокрой укладке. НАСЕ Интернэшнл. OnePetro
Texter, HG 1951. Испытание внутреннего гидростатического давления как мера эксплуатационных характеристик обсадных и насосно-компрессорных труб нефтяных скважин. Всемирный нефтяной конгресс. OnePetro
Заслуживающие внимания книги
Американская ассоциация водопроводных сооружений. 2010. Полевое руководство по гидростатическим испытаниям. Денвер, Колорадо: Американская ассоциация водопроводных сооружений.WorldCat
Международное общество измерений и контроля, Американское общество приборов и Американский национальный институт стандартов. 1995. Гидростатические испытания регулирующей арматуры. Research Triangle Park, Северная Каролина: Американское общество инструментов. WorldCat
Лам, Си-Тай. 1975. Гидростатические испытания линейных вязкоупругих материалов. WorldCat
Общество по стандартизации производителей арматуры и арматуры. 1961. Гидростатические испытания стальной арматуры. Нью-Йорк, штат Нью-Йорк: Общество. WorldCat
Мультимедиа
Внешние ссылки
Википедия
См. также
Скребки трубопровода
Что такое опрессовка | Промышленные ресурсы
Какова цель опрессовки?
Хотите узнать основы опрессовки? Всегда полезно начинать с самого начала, чтобы понять, что означает этот термин. Далее поясняется испытание под давлением.
Испытание под давлением или гидростатическое испытание – это испытание, которое проводится после монтажа любого трубопровода до его ввода в эксплуатацию. Целью испытаний под давлением является исследование различных пределов трубопровода, которые будут проверять такие области, как надежность, максимальная пропускная способность, утечки, соединительные фитинги и давление. Без этой информации труба не может быть введена в эксплуатацию, а владелец/оператор не знает, соответствует ли труба установленным требованиям.
Информация, полученная в результате опрессовки, помогает поддерживать стандарты безопасности и содержать трубопровод в рабочем состоянии. При выпуске нового оборудования трубопроводы проходят первоначальную аттестацию с помощью гидравлических/гидростатических испытаний и регулярно проходят повторную аттестацию через различные промежутки времени, что называется «модифицированным гидростатическим испытанием» или «проверочным испытанием давлением».
При испытаниях трубопроводов их проводят по отраслевым или техническим условиям заказчика, заполняя сосуд несжимаемой жидкостью, например водой или нефтью.Это проверяет трубу на наличие утечек или изменений формы. Обычно в воду добавляют красители для облегчения обнаружения утечек. При опрессовке давление, оказываемое на сосуд, всегда значительно превышает нормальное рабочее давление. Это необходимо для обеспечения максимальной безопасности при любых непредвиденных уровнях давления в сосуде.
Информация для тестера выбита на сосуде, она может включать серийный номер, производителя и дату изготовления. Может быть и другая информация, такая как REE (упругое расширение при отказе) и максимальное расширение, указанное производителем для обеспечения безопасности.Эта информация обычно записывается в компьютерную систему, что позволяет владельцу отслеживать, когда тесты проводились или когда их нужно запланировать.
Почему пневматические испытания более опасны, чем гидроиспытания? После того, как вы успешно проложили подземный трубопровод или выполнили все необходимые огневые работы (например, сварку или термообработку после сварки), вам необходимо провести испытание под давлением, чтобы убедиться, что механические свойства трубы не изменились. был понижен.
Однако в данном случае для испытания давлением используются два основных метода, а именно гидростатический и пневматический. В то время как первый выполняется с использованием воды в качестве испытательной среды, второй использует воздух, азот или любую другую форму нетоксичного и негорючего газа для завершения проверки.
Существуют и другие различия между этими двумя методами тестирования, которые также необходимо учитывать при выборе правильного варианта для любого конкретного приложения.
Интересно, что пневматические испытания считаются более опасными из двух вариантов, поскольку количество энергии, запасенной на единицу объема сжатого воздуха под испытательным давлением, относительно велико.
В результате пневматические испытания рекомендуются только для применений с низким давлением, в то время как все проверки должны сопровождаться подробными мерами предосторожности и проводиться под контролем старших сотрудников.
Вы также должны убедиться, что у вас есть разрешение от соответствующего органа на проведение пневматического испытания, в противном случае вы окажетесь в нарушении существующего закона. Это обеспечит наличие подходящих условий для этого типа испытаний под давлением, поскольку вы не можете проводить такую проверку, если трубопроводная система может быть заполнена водой или не может выдержать следовые количества испытательной среды.
Несмотря на то, что существует два различных метода испытания трубопроводов под давлением, в большинстве случаев вам потребуется использовать метод гидростатического испытания.
Причина этого проста; поскольку пневматическое испытание по своей природе более опасно и может использоваться только в том случае, если конструкция или функция трубопровода несовместимы с идеей использования воды в качестве испытательной среды.
При испытании трубопроводов с использованием этого метода рассматриваемый сосуд будет заполнен водой, чтобы помочь выявить любые потенциальные утечки, механические дефекты или незначительные изменения формы при погружении. Красители также могут быть добавлены в воду для немедленного обнаружения утечек, в то время как вы должны убедиться, что все сварочные работы были завершены и проверены перед проведением гидростатического испытания.
Когда дело доходит до манометрического давления, величина давления, воздействующего на сосуд, всегда должна быть значительно выше нормального рабочего уровня.
В частности, оно должно быть в пределах от 1,5 до 4 от значения, полученного при испытании давлением, чтобы учесть любые ожидаемо высокие уровни давления, которые могут быть на сосуде во время его нормальной эксплуатации.
Что такое испытание пневматических труб? Испытание под давлением всегда требуется после завершения строительства новой трубопроводной системы или в случаях, когда отдельные трубы были изменены. Для этого тоже есть веская причина; поскольку это гарантирует безопасность системы и надежность ее работы, а также определяет любые потенциальные утечки.
Обычно испытания под давлением проводятся после завершения всех огневых работ и сварки трубопроводной системы, при этом послесварочная термообработка способна снизить механические свойства отдельных труб.
Существуют различные типы испытаний под давлением, которые можно использовать, например, пневматические испытания с использованием воздуха или инертного газа, такого как азот, для повышения давления в трубопроводе до 110 % его расчетной пропускной способности.
Затем газ выдерживают в трубопроводе в течение длительного периода времени, чтобы оценить способность системы работать безопасно и эффективно при максимальной мощности.
Несмотря на то, что результаты пневматических испытаний трубопроводов очень точны, эта методология используется только в приложениях с заметно низким давлением, когда вода или масло не могут использоваться в качестве жизнеспособной испытательной среды.
Причина этого проста; поскольку инертные газы, такие как азот, способны сохранять высокие уровни энергии, когда они сжимаются во время испытаний. Это увеличивает риск отказа и повреждения системы, в то время как характер пневматических испытаний требует официального разрешения местных властей и руководства инженеров-специалистов.
Хотите получить дополнительную информацию об оборудовании для испытаний под давлением?
Groundforce — один из ведущих поставщиков в Великобритании и Ирландии для строительной отрасли, занимающийся испытаниями под давлением, заглушками для труб, опалубкой, свайным оборудованием, крепью и арендой насосов.Компания Groundforce работает уже более 20 лет, обладая богатым опытом в области строительства, и гордится своим завидным портфелем продуктов и услуг. Groundforce также предлагает комплексную службу технической поддержки для всего разнообразия своего оборудования. Чтобы узнать больше о полном спектре продуктов и услуг, предлагаемых Groundforce, позвоните по телефону 0800 000 345 или отправьте электронное письмо по адресу[email protected].
Неразрушающий контроль.
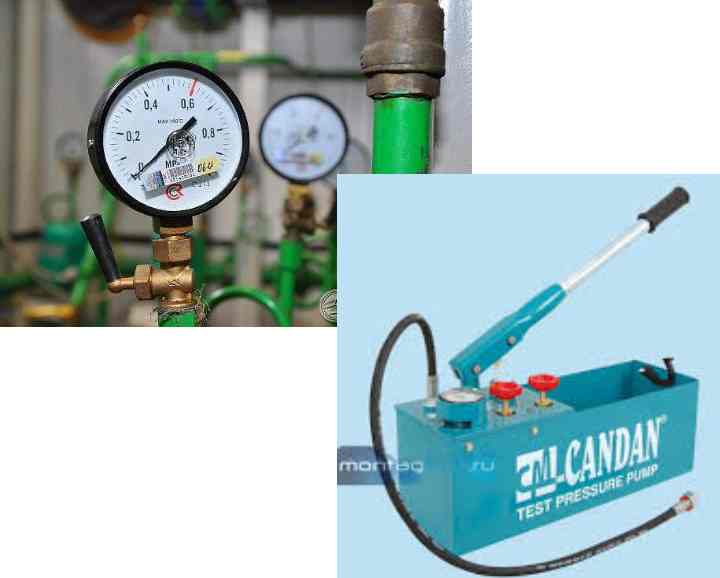
Испытания под давлением — это неразрушающие испытания, проводимые для обеспечения целостности корпуса высокого давления нового оборудования, работающего под давлением, или ранее установленного оборудования, работающего под давлением, и трубопроводного оборудования, в котором были изменены или отремонтированы его границы.
Испытания под давлением требуются большинством норм и правил для трубопроводов, чтобы убедиться, что новая, модифицированная или отремонтированная система трубопроводов способна безопасно выдерживать номинальное давление и герметична. Соблюдение правил трубопроводов может быть предписано регулирующими и правоохранительными органами, страховыми компаниями или условиями контракта на строительство системы.Испытания под давлением, независимо от того, требуются они по закону или нет, служат полезной цели защиты рабочих и населения.
Испытание под давлением может также использоваться для установления номинального давления для компонента или специальной системы, для которой невозможно установить безопасное номинальное давление расчетным путем. Прототип компонента или системы подвергается постепенно увеличивающемуся давлению до тех пор, пока не произойдет измеримая деформация или, альтернативно, до точки разрыва. Затем, используя коэффициенты снижения номинальных характеристик, указанные в коде или стандарте, соответствующем компоненту или системе, можно установить номинальное расчетное давление на основе экспериментальных данных.
Коды трубопроводов
Существует множество норм и стандартов, касающихся трубопроводных систем. Двумя стандартами, имеющими большое значение для испытаний под давлением и на наличие утечек, являются стандарт ASME B31 для трубопроводов, работающих под давлением, и стандарт ASME для котлов и сосудов под давлением. Хотя эти два кодекса применимы ко многим трубопроводным системам, могут потребоваться другие коды или стандарты, если этого требуют власти, страховые компании или владелец системы. Примерами могут служить стандарты AWWA для трубопроводов систем подачи и распределения воды.Стандарт ASME B31 для напорных трубопроводов состоит из нескольких разделов. Они..
- ASME B31.1 для силовых трубопроводов
- ASME B31.2 для трубопроводов топливного газа
- ASME B31.3 для технологических трубопроводов
- ASME B31.4 для систем транспортировки жидких углеводородов, сжиженного нефтяного газа, безводного аммиака и спиртов
- ASME B31.5 для трубопроводов охлаждения
- ASME B31.8 для трубопроводных систем передачи и распределения газа
- ASME B31.9 для инженерных сетей здания
- АСМЭ Б31.11 для трубопроводных систем транспортировки навозной жижи
Кодекс ASME по котлам и сосудам под давлением также содержит несколько разделов, которые содержат требования к испытаниям на герметичность и давление для систем трубопроводов, сосудов под давлением и других элементов, удерживающих давление. Это..
- Раздел I для энергетических котлов
- Раздел III для компонентов атомной электростанции
- Раздел V для неразрушающего контроля
- Раздел VIII для сосудов под давлением
- Раздел X для сосудов высокого давления из пластика, армированного стекловолокном
- Раздел XI по инспекции компонентов атомной электростанции в процессе эксплуатации
Существует большое сходство в отношении требований и процедур тестирования среди многих кодов. В этой главе будут обсуждаться различные методы проверки на герметичность, планирование, подготовка, выполнение, документация и приемочные стандарты для испытаний под давлением. Оборудование, полезное для опрессовки, также будет включено в обсуждение. Последующий материал не должен рассматриваться как замена полного знания или тщательного изучения конкретных требований правил, которые необходимо использовать для тестирования конкретной системы трубопроводов.
Методы проверки на герметичность
Существует множество различных методов проверки давления и герметичности в полевых условиях.Семь из них..
- Гидростатические испытания с использованием воды или другой жидкости под давлением
- Пневматические или газожидкостные испытания, в которых используется воздух или другой газ под давлением
- Комбинация пневматических и гидростатических испытаний, при которой для обнаружения утечек сначала используется воздух под низким давлением
- Первоначальные эксплуатационные испытания, которые включают проверку герметичности при первом вводе системы в эксплуатацию
- Вакуумные испытания, при которых используется отрицательное давление для проверки наличия утечки
- Испытание статического напора, которое обычно проводится для дренажного трубопровода, когда вода остается в стояке в течение установленного периода времени
- Поиск утечек галогенов и гелия
Гидростатические испытания на герметичность
Гидростатические испытания являются предпочтительным и, возможно, наиболее часто используемым методом испытаний на герметичность. Наиболее важной причиной этого является относительная безопасность гидростатических испытаний по сравнению с пневматическими испытаниями. Вода является гораздо более безопасной жидкой испытательной средой, чем воздух, поскольку она практически несжимаема. Следовательно, количество работы, необходимой для сжатия воды до заданного давления в системе трубопроводов, существенно меньше, чем работа, необходимая для сжатия воздуха или любого другого газа до того же давления. Работа сжатия сохраняется в жидкости в виде потенциальной энергии, которая может внезапно высвободиться в случае отказа во время испытания под давлением.
Расчет потенциальной энергии воздуха, сжатого до давления 1000 фунтов на кв. дюйм (6900 кПа), по сравнению с потенциальной энергией того же конечного объема воды при манометрическом давлении 1000 фунтов на кв. дюйм (6900 кПа) показывает соотношение более 2500 к 1. Следовательно, потенциальный ущерб окружающему оборудованию и персоналу в результате отказа во время испытания под давлением гораздо более серьезен при использовании газообразной испытательной среды. Это не означает, что при гидростатическом испытании на герметичность вообще нет опасности. Гидравлические испытания могут представлять значительную опасность из-за попадания воздуха в трубопровод.Даже если перед подачей давления из трубопровода стравлен весь воздух, работникам настоятельно рекомендуется проводить любые испытания высоким давлением с учетом требований безопасности.
Пневматические испытания на герметичность
Для пневматических испытаний обычно используется сжатый воздух или азот, если источником является баллонный газ. Азот не следует использовать в закрытом помещении, если существует вероятность того, что выходящий азот может вытеснить воздух в замкнутом пространстве. Известно, что в таких обстоятельствах люди теряют сознание, прежде чем понимают, что им не хватает кислорода.Из-за большей опасности травмирования газообразной испытательной средой давление, которое может использоваться для визуального осмотра на наличие утечек, для некоторых кодов трубопроводов ниже, чем в случае гидростатического испытания. Например, для пневматических испытаний ASME B31.1 позволяет снизить давление до более низкого из 100 фунтов на квадратный дюйм (690 кПа) или расчетного давления во время проверки на утечку.
Комбинированные пневматические и гидростатические испытания
Низкое давление воздуха, чаще всего 25 фунтов на кв. дюйм (175 кПа), сначала используется для выявления крупных утечек.Такое низкое давление снижает опасность травм, но позволяет быстро обнаружить крупные утечки. Ремонт, если он необходим, может быть выполнен до гидростатического испытания. Этот метод может быть очень эффективным для экономии времени, особенно если требуется много времени, чтобы заполнить систему водой только для того, чтобы обнаружить утечки с первой попытки. Если при гидростатическом испытании обнаружены утечки, потребуется больше времени, чтобы удалить воду и высушить трубопровод в достаточной степени для проведения ремонта.
Гидростатико-пневматическое испытание на герметичность отличается от двухэтапного испытания, описанного в предыдущем абзаце. В этом случае испытание под давлением проводится смесью воздуха и воды. Например, сосуд высокого давления, предназначенный для хранения технологической жидкости с паровой фазой или воздухом над жидкостью, может быть спроектирован так, чтобы выдерживать вес жидкости до определенной максимально ожидаемой высоты жидкости. Если бы сосуд не был рассчитан на то, чтобы выдерживать вес при полном заполнении жидкостью, можно было бы испытать этот сосуд только в том случае, если бы он был частично заполнен технологической жидкостью до уровня, дублирующего эффект максимально ожидаемого уровня.
Испытание на утечку при начальном обслуживании
Эта категория испытаний ограничена кодами для определенных ситуаций. Например, ASME B31.3 ограничивает использование этого метода жидкими средами категории D. Работа с жидкостями категории D определяется как неопасная для человека и должна работать при давлении ниже 150 фунтов на кв. дюйм (1035 кПа) и температуре от -20 до 366°F (от -29 до 185°C). Кодекс ASME B31.1, раздел 137.7.1, не разрешает первоначальные эксплуатационные испытания внешних трубопроводов котла. Однако тот же раздел ASME B31.1 разрешает первоначальные эксплуатационные испытания других систем трубопроводов, если другие виды испытаний на герметичность нецелесообразны. Первоначальные эксплуатационные испытания также применимы к проверке компонентов атомной электростанции в соответствии с разделом XI Кодекса ASME по котлам и сосудам под давлением. Как указано, этот тест обычно запускается при первом вводе системы в эксплуатацию. Система постепенно поднимается до нормального рабочего давления в соответствии с требованиями ASME B31.1 или расчетного давления в соответствии с требованиями ASME B31.3. Затем в нем поддерживается это давление, пока проводится проверка на наличие утечек.
Вакуумная проверка на герметичность
Вакуумная проверка на герметичность является эффективным способом определения наличия утечки в системе. Обычно это делается путем создания вакуума в системе и захвата вакуума внутри системы. Утечка определяется, если захваченный вакуум поднимается до атмосферного давления. Производитель компонентов довольно часто использует этот тип проверки на утечку в качестве проверки на производственные утечки. Однако очень сложно определить место или места утечки, если она существует.Генераторы дыма использовались для определения местоположения трубопровода, где дым втягивается в трубопровод. Это очень трудно использовать, если утечка не достаточно велика, чтобы весь или большая часть дыма попала в трубу. Если образуется значительно больше дыма, чем может быть втянуто в трубу, дым, который рассеивается в окружающем воздухе, может легко скрыть место утечки. Очевидно, что этот метод не подходит для испытания трубопровода при рабочем давлении или выше, если только трубопровод не должен эксплуатироваться при вакууме.
Испытание на герметичность статическим напором
Этот метод испытания иногда называют испытанием на падение, поскольку падение уровня воды в открытом стояке, добавляемом в систему для создания необходимого давления, является признаком утечки. После того, как система и стояк заполнены водой, измеряется и отмечается уровень стояка. После требуемого периода выдержки высота снова проверяется, и любое снижение уровня и период выдержки записываются. Место утечки определяется визуальным осмотром.
Проверка на утечку галогена и гелия
В этих методах проверки используется индикаторный газ для определения места и количества утечки. В случае обнаружения утечек галогена система заполняется газообразным галогеном. Галогенный датчик-детектор используется для обнаружения утечки индикаторного газа из любого незащищенного соединения. Галогенный течеискатель, или сниффер, состоит из трубчатого зонда, который всасывает смесь вытекшего газообразного галогена и воздуха в прибор, чувствительный к небольшим количествам газообразного галогена.
В этом приборе используется диод для определения присутствия газообразного галогена. Утечка газообразного галогена проходит над нагретым платиновым элементом (анодом). Нагретый элемент ионизирует газообразный галоген. Ионы текут к коллекторной пластине (катод). Ток, пропорциональный скорости образования ионов и, следовательно, скорости потока утечки, отображается на измерителе. Зонд галогенного детектора калибруется с использованием отверстия, пропускающего известный поток утечки. Зонд детектора проходит над отверстием с той же скоростью, которая будет использоваться для проверки системы на наличие утечек.Предпочтительным индикаторным газом является хладагент 12, но можно использовать хладагенты 11, 21, 22, 114 или метиленхлорид. Галогены не следует использовать с аустенитными нержавеющими сталями.
гелием также может проводиться в режиме анализатора, как описано выше для галогенов. Однако, кроме того, испытание на утечку гелием можно проводить двумя другими методами, более чувствительными при обнаружении утечки. Это режим трассировки и режим капота или закрытой системы. В трассирующем режиме в системе создается вакуум, и гелий распыляется на наружную поверхность соединений для проверки на наличие утечек. Вакуум системы всасывает гелий через любое негерметичное соединение и подает его в гелиевый масс-спектрометр. В режиме колпака тестируемая система окружена концентрированным гелием.
Испытание на утечку гелием в колпаке является наиболее чувствительным методом обнаружения утечек и единственным методом, принятым разделом V Кодекса ASME в качестве количественного. Производители компонентов, требующих герметичного уплотнения, будут использовать колпакный метод обнаружения утечек гелием в качестве производственного испытания на герметичность. В этих случаях компонент может быть окружен гелием в камере.Компонент подключается к гелиевому течеискателю, который пытается создать внутри компонента вакуум, близкий к абсолютному нулю.
Любая утечка гелия из окружающей камеры в компонент будет втягиваться в гелиевый течеискатель создаваемым им вакуумом. Течеискатель гелия содержит масс-спектрометр, настроенный на обнаружение присутствия молекул гелия. Этот метод испытаний в закрытой системе способен обнаруживать утечки размером до 1X10 -10 см3/с (6. 1X10 -12 кубических дюймов/с), эквивалент стандартного атмосферного воздуха. Метод закрытой системы не подходит для измерения большой утечки, которая может затопить детектор и сделать его непригодным для дальнейших измерений до тех пор, пока из детектора не будет удалена каждая молекула гелия.
Метод закрытой системы не подходит для системы трубопроводов в полевых условиях из-за больших объемов. Также он не показывает места утечки или утечек. Наконец, чувствительность обнаружения утечек с использованием закрытой системы на много порядков выше, чем обычно требуется.Анализатор гелия является наименее чувствительным методом и может дать ложные показания, если гелий из большой утечки в одном месте системы диффундирует в другие места.
Большая утечка также может затопить детектор, временно сделав его бесполезным, пока весь гелий не будет удален из масс-спектрометра. Давление гелия, используемое во всех этих методах, обычно составляет одну или две атмосферы, чего достаточно для обнаружения очень небольших утечек. Низкое давление также служит для уменьшения количества гелия, необходимого для испытания.Испытания на герметичность гелием редко, если вообще когда-либо, используются для демонстрации того, что система может безопасно выдерживать расчетное номинальное давление.
не смогут найти утечки, если компонент или система трубопроводов не будут полностью сухими. Жидкость, содержащаяся в небольшом пути утечки, из-за капиллярного действия может герметизировать утечку из-за низкого давления гелия и поверхностного натяжения жидкости. Поэтому требуется большая осторожность при использовании этого подхода в абсолютно сухих условиях.В противном случае эта система может оказаться даже менее чувствительной при обнаружении утечки, чем гидростатическое испытание под высоким давлением. Кроме того, гелиевый течеискатель легко загрязняется маслами и другими соединениями и становится неточным. Полевые условия обычно не исключают возможности загрязнения течеискателя.
Испытательное давление
Выбранный метод испытаний и жидкая испытательная среда вместе с применимым кодом также определяют правила, которым необходимо следовать при расчете требуемого испытательного давления. В большинстве случаев давление, превышающее расчетное номинальное давление, применяется в течение короткого времени, скажем, не менее 10 минут. Величина этого начального испытательного давления часто по крайней мере в 1,5 раза превышает расчетное давление для гидростатического испытания. Однако он может быть другим, в зависимости от того, какой код применим и является ли испытание гидростатическим или пневматическим.
Кроме того, испытательное давление никогда не должно превышать давление, которое может вызвать деформацию, или максимально допустимое испытательное давление какого-либо компонента, подвергаемого испытанию.В случае ASME B31, раздел 137.1.4, и норм для котлов и сосудов под давлением, максимальное испытательное давление не должно превышать 90 процентов предела текучести для любого компонента, подвергаемого испытанию. Испытательное давление необходимо для демонстрации того, что система может безопасно выдерживать номинальное давление. После этого периода давления, превышающего расчетное, часто допускается снижение давления до более низкого значения для проверки утечек. Испытательное давление поддерживается в течение времени, необходимого для проведения тщательного
Код | Тип теста |
АСМЭ Б31.1 | Гидростатический (1) |
АСМЭ Б31.1 | Пневматический |
АСМЭ Б31.1 | Начальное обслуживание |
АСМЭ Б31.3 | Гидростатический |
АСМЭ Б31.3 | Пневматический |
АСМЭ Б31.3 | Начальное обслуживание (3) |
АСМЭ I | Гидростатический |
ASME III Раздел 1 Подраздел NB | Гидростатический |
ASME III Раздел 1 Подраздел NB | Пневматический |
ASME III Раздел 1 Подраздел NC | Гидростатический |
ASME III Раздел 1 Подраздел NC | Пневматический |
ASME III Раздел 1 Подраздел ND | Гидростатический |
ASME III Раздел 1 Подраздел ND | Пневматический |
Код | Испытательное давление минимальное |
АСМЭ Б31.![]() | 1,5-кратный дизайн |
АСМЭ Б31.1 | 1,2-кратный дизайн |
АСМЭ Б31.1 | Нормальное рабочее давление |
АСМЭ Б31.3 | 1,5-кратный дизайн (2) |
АСМЭ Б31.3 | 1,1-кратный дизайн |
АСМЭ Б31.3 | Расчетное давление |
АСМЭ I | 1,5-кратное максимально допустимое рабочее давление (4) |
ASME III Раздел 1 Подраздел NB | 1.25-кратное расчетное давление в системе (5) |
ASME III Раздел 1 Подраздел NB | 1,25-кратное расчетное давление в системе (6) |
ASME III Раздел 1 Подраздел NC | 1,5-кратное расчетное давление в системе |
ASME III Раздел 1 Подраздел NC | 1,25-кратное расчетное давление в системе |
ASME III Раздел 1 Подраздел ND | 1,5-кратное расчетное давление системы для готовых компонентов, 1,25-кратное расчетное давление системы для трубопроводных систем |
ASME III Раздел 1 Подраздел ND | 1.![]() |
Код | Испытательное давление максимальное |
АСМЭ Б31.1 | Максимально допустимое испытательное давление для любого компонента или 90 % предела текучести |
АСМЭ Б31.1 | 1,5-кратное расчетное или максимально допустимое испытательное давление любой компонент |
АСМЭ Б31.1 | Нормальное рабочее давление |
АСМЭ Б31.3 | Не превышать предел текучести |
АСМЭ Б31.3 | 1,1-кратное расчетное плюс меньшее из 50 фунтов на кв. дюйм или 10 процентов испытательного давления |
АСМЭ Б31.3 | Расчетное давление |
АСМЭ I | Предел текучести не должен превышать 90 процентов |
ASME III Раздел 1 Подраздел NB | Не превышайте пределы напряжений расчетного сечения NB-3226 или максимальное испытательное давление любого компонента системы (5) |
ASME III Раздел 1 Подраздел NB | Не превышайте пределы напряжений расчетного сечения NB-3226 или максимальное испытательное давление любого компонента системы |
ASME III Раздел 1 Подраздел NC | Если минимальное испытательное давление превышено на 6 %, установите предел по наименьшему из результатов анализа всех испытательных нагрузок или максимальному испытательному давлению любого компонента |
ASME III Раздел 1 Подраздел NC | Если минимальное испытательное давление превышено на 6 %, установите предел по наименьшему из результатов анализа всех испытательных нагрузок или максимальному испытательному давлению любого компонента |
ASME III Раздел 1 Подраздел ND | Если минимальное испытательное давление превышено на 6 %, установите предел по наименьшему из результатов анализа всех испытательных нагрузок или максимальному испытательному давлению любого компонента |
ASME III Раздел 1 Подраздел ND | Если минимальное испытательное давление превышено на 6 %, установите предел по наименьшему из результатов анализа всех испытательных нагрузок или максимальному испытательному давлению любого компонента |
Код | Испытательное давление время выдержки |
АСМЭ Б31.![]() | 10 минут |
АСМЭ Б31.1 | 10 минут |
АСМЭ Б31.1 | 10 минут или время для завершения проверки герметичности |
АСМЭ Б31.3 | Время на завершение проверки герметичности, но не менее 10 минут |
АСМЭ Б31.3 | 10 минут |
АСМЭ Б31.3 | Время для завершения проверки герметичности |
АСМЭ I | Не указано, обычно 1 час |
ASME III Раздел 1 Подраздел NB | 10 минут |
ASME III Раздел 1 Подраздел NB | 10 минут |
ASME III Раздел 1 Подраздел NC | 10 или 15 минут на дюйм расчетной минимальной толщины стенки для насосов и клапанов |
ASME III Раздел 1 Подраздел NC | 10 минут |
ASME III Раздел 1 Подраздел ND | 10 минут |
ASME III Раздел 1 Подраздел ND | 10 минут |
Код | Осмотр давление |
АСМЭ Б31.![]() | Расчетное давление |
АСМЭ Б31.1 | Нижнее из 100 фунтов на кв. дюйм или расчетное давление |
АСМЭ Б31.1 | Нормальное рабочее давление |
АСМЭ Б31.3 | 1,5-кратный дизайн |
АСМЭ Б31.3 | Расчетное давление |
АСМЭ Б31.3 | Расчетное давление |
АСМЭ I | Максимально допустимое рабочее давление (4) |
ASME III Раздел 1 Подраздел NB | Больше расчетного давления или 0,75 испытательного давления |
ASME III Раздел 1 Подраздел NB | Больше расчетного давления или 0,75 испытательного давления |
ASME III Раздел 1 Подраздел NC | Больше расчетного давления или 0,75 испытательного давления |
ASME III Раздел 1 Подраздел NC | Больше расчетного давления или 0,75 испытательного давления |
ASME III Раздел 1 Подраздел ND | Больше расчетного давления или 0,75 испытательного давления |
ASME III Раздел 1 Подраздел ND | Больше расчетного давления или 0,75 испытательного давления |
Примечания. .
1. | Внешние трубопроводы котла должны пройти гидростатические испытания в соответствии с PG-99 раздела I норм ASME. |
2. | Гидростатическое давлениеASME B31.3 должно быть выше расчетного давления в 1,5 раза пропорционально пределу текучести при температуре испытания, деленному на прочность при расчетной температуре, но не должно превышать предела текучести при температуре испытания. Если речь идет о сосуде, расчетное давление которого меньше, чем в трубопроводе, и когда сосуд не может быть изолирован, трубопровод и сосуд могут быть испытаны вместе при испытательном давлении сосуда при условии, что испытательное давление сосуда составляет не менее 77 процентов от испытательного давления трубопровода. |
3. | ASME B31.3 первоначальные эксплуатационные испытания разрешены только для трубопроводов категории D. |
4. | ASME Code Section I Гидростатическое испытательное давление при температуре не ниже 70°F (21°C) и испытательное давление при температуре ниже 120°F (49°C).![]() |
5. | ASME Code Section III, Division 1, подраздел NB, пределы испытательного давления, определенные в разделе NB3226; также компоненты, содержащие паяные соединения и клапаны, перед установкой должны быть испытаны давлением, в 1,5 раза превышающим проектное значение системы. |
6. | ASME Code Section III, Division 1, подраздел NB, пневматическое испытательное давление для компонентов, частично заполненных водой, должно быть не менее 1.25-кратное расчетное давление в системе. |
Отказ оборудования, работающего под давлением
Сосуды под давлением и системы трубопроводов широко используются в промышленности и содержат очень большую концентрацию энергии. Несмотря на то, что их конструкция и установка соответствуют федеральным, государственным и местным нормам и признанным промышленным стандартам, продолжают иметь место серьезные отказы оборудования, работающего под давлением.
Существует множество причин выхода из строя оборудования, работающего под давлением. Деградация и утончение материалов в процессе эксплуатации, старение, скрытые дефекты при изготовлении и т. д.. К счастью, периодические испытания, а также внутренние и внешние проверки значительно повышают безопасность сосуда под давлением или системы трубопроводов. Хорошая программа испытаний и инспекций основана на разработке процедур для конкретных отраслей или типов судов.
Ряд несчастных случаев привлек внимание к опасностям и рискам, связанным с хранением, обращением и перекачкой жидкостей под давлением. Когда сосуды под давлением выходят из строя, это обычно происходит в результате разрушения корпуса в результате коррозии и эрозии (более 50 процентов отказов корпуса).
Сосуд новой постройки разорвался во время гидроиспытаний
Все сосуды под давлением имеют свои собственные специфические опасности, включая большую накопленную потенциальную силу, точки износа и коррозии, а также возможный отказ предохранительных устройств контроля избыточного давления и температуры.
Правительство и промышленность отреагировали на потребность в улучшении испытаний систем, работающих под давлением, путем разработки стандартов и правил, определяющих общие требования безопасности при работе под давлением (Кодекс ASME по котлам и сосудам под давлением, Руководство Министерства энергетики США по безопасности, работающее под давлением, и другие).
В этих правилах излагаются требования к реализации программы безопасности при испытаниях под давлением. Крайне важно, чтобы проектировщики и эксплуатационный персонал использовали эти стандарты в качестве эталонных критериев для написания и реализации программы безопасности при испытаниях под давлением.
Программа испытаний под давлением
Надлежащая программа безопасности при испытаниях под давлением должна выявлять производственные дефекты и износ в результате старения, растрескивания, коррозии и других факторов до того, как они приведут к отказу сосуда, и определять (1) может ли сосуд продолжать эксплуатироваться при том же давлении, (2) что могут потребоваться меры контроля и ремонта, чтобы система давления могла работать при исходном давлении, и (3) необходимо ли снижать давление для безопасной работы системы.
Все компании, работающие с оборудованием, работающим под давлением, почти все имеют расширенные технические руководства по испытаниям сосудов под давлением и трубопроводных систем. Эти инструкции подготовлены в соответствии со стандартами безопасности под давлением OSHA, DOT, ASME, местными, государственными и другими федеральными нормами и стандартами.
Документация включает определение обязанностей инженеров, руководства и персонала по технике безопасности; общие требования к оборудованию и материалам; процедуры гидростатических и пневматических испытаний для проверки целостности системы и ее компонентов; и руководства по плану испытаний под давлением, аварийным процедурам, документации и мерам контроля опасностей. Эти меры включают в себя контроль сброса давления, защиту от последствий шумового воздействия, контроль окружающей среды и персонала, а также защиту от присутствия токсичных или горючих газов и высокого давления.
Запуск вновь изготовленного резервуара во время пневматического испытания под давлением воздухом
Определения испытаний под давлением
- Переделка — Под переделкой понимается физическое изменение любого компонента, имеющее конструктивные последствия, влияющие на способность сосуда под давлением выдерживать давление, выходящее за рамки элементов, описанных в существующих отчетах с данными.
- Коррозионная прибавка — Дополнительная толщина материала, добавленная в соответствии с конструкцией, чтобы компенсировать потерю материала в результате коррозионного или эрозионного воздействия.
- Работа с коррозией — Любая работа системы давления, которая из-за химического или другого взаимодействия с конструкционными материалами контейнера, содержимым или внешней средой вызывает растрескивание контейнера под давлением, его охрупчивание, потерю более 0,01 дюйма толщины за год эксплуатации или испортиться каким-либо образом.
- Расчетное давление — давление, используемое при расчете компонента давления вместе с соответствующей расчетной температурой металла с целью определения минимально допустимой толщины или физических характеристик границы давления. Расчетное давление для сосудов указано на производственных чертежах, а для трубопроводов максимальное рабочее давление указано в ведомости. Расчетное давление для трубопровода больше, чем 110 % от максимального рабочего давления или 25 фунтов на квадратный дюйм сверх максимального рабочего давления.
- Замечание по технике безопасности (ESN) — Утвержденный руководством документ с описанием ожидаемых опасностей, связанных с оборудованием, и расчетными параметрами, которые будут использоваться.
- Высокое давление — Давление газа более 20 МПа (3000 фунтов на кв. дюйм) и жидкости более 35 МПа (5000).
- Промежуточное давление — Давление газа от 1 до 20 МПа (от 150 до 3000 фунтов на кв.
дюйм изб.) и жидкости от 10 до 35 МПа (от 1500 до 5000 фунтов на кв. дюйм).
- Испытание на утечку — Испытание давлением или вакуумом для определения наличия, скорости и/или места утечки.
- Низкое давление — Давление газа менее 1 МПа (150 фунтов на кв. дюйм изб.) или жидкости менее 10 МПа (1500 фунтов на кв. дюйм).
- Операция в пилотируемой зоне — Операция под давлением, которая может проводиться (в определенных пределах) в присутствии персонала.
- Максимально допустимое рабочее давление (МДРД) — максимально допустимое давление в верхней части сосуда в его нормальном рабочем положении при рабочей температуре, указанной для данного давления.Это наименьшее из значений, найденных для максимально допустимого рабочего давления для любой из основных частей сосуда в соответствии с принципами, установленными в Разделе VIII ASME. МДРД указан на заводской табличке судна. МДРД можно принять таким же, как расчетное давление, но по большей части МДРД основывается на изготовленной толщине за вычетом допусков на коррозию.
МДРД применяется только к сосудам под давлением.
- Максимальная расчетная температура — это максимальная температура, используемая в проекте, которая не должна быть ниже максимальной рабочей температуры.
- Максимальное рабочее давление (MOP) — максимальное давление, ожидаемое во время работы. Обычно это на 10-20% ниже МДРД.
- Минимально допустимая температура металла (MAMT) — Минимальная температура для существующего сосуда, чтобы выдерживать условия испытаний или эксплуатации с низким риском хрупкого разрушения. MAMT определяется путем оценки сосудов под давлением, построенных до 1987 года. Этот термин используется в API RP 579 для оценки хрупкого разрушения существующего оборудования.Это может быть одна температура или диапазон допустимых рабочих температур в зависимости от давления.
- Минимальная расчетная температура металла (MDMT) — Минимальная температура металла, используемая при расчете сосуда высокого давления.
MDMT является термином кода ASME и обычно указывается на заводской табличке судна или в форме U-1 для судов, спроектированных в соответствии с разделом VIII ASME, разделом 1, изданием 1987 г. или более поздним.
- МПа — Абсолютное давление в единицах СИ. 1 атмосфера (14,7 фунтов на квадратный дюйм) равна 0.1 МПа.
- Процедура безопасности при эксплуатации (OSP) — Документ, используемый для описания средств контроля, необходимых для обеспечения того, чтобы риски, связанные с потенциально опасным исследовательским проектом или уникальной деятельностью, находились на приемлемом уровне.
- Оборудование, работающее под давлением — Любое оборудование, например, сосуды, коллекторы, трубопроводы или другие компоненты, которые работают при давлении выше или ниже (в случае вакуумного оборудования) атмосферного давления.
- Сосуд под давлением — Компонент давления относительно большого объема (например, сферический или цилиндрический контейнер) с поперечным сечением, превышающим соответствующий трубопровод.
- Контрольное испытание — Испытание, при котором прототипы оборудования подвергаются воздействию давления для определения фактического предела текучести или давления разрушения (разрыва) (используется для расчета МДРД).
- Дистанционное управление — Работа под давлением, которую нельзя проводить в присутствии персонала. Оборудование должно быть установлено в испытательных камерах, за сертифицированными баррикадами или эксплуатироваться из безопасного места.
- Коэффициент запаса прочности (SF) — Отношение предельного давления (т. е. разрыва или разрушения) (измеренного или рассчитанного) к МДРД.Коэффициент безопасности, относящийся к чему-либо, отличному от давления разрушения, должен обозначаться соответствующим нижним индексом.
Коды, стандарты и ссылки
Американское общество инженеров-механиков (ASME)
- Код
- по котлам и сосудам под давлением. Раздел VIII Сосуды под давлением
- ASME B31.
3 Трубопровод химических и нефтеперерабатывающих заводов
- Трубные фланцы и фланцевые фитинги ASME B16.5
Американское общество испытаний и материалов (ASTM)
- ASTM E 1003 Стандартный метод испытаний на гидростатическую утечку
Американский институт нефти (API)
- РП 1110 Опрессовка стальных трубопроводов для транспорта газа, нефтяного газа, опасных жидкостей…
- Техническое обслуживание, проверка, оценка, ремонт и изменение API 510
- Пламенные нагреватели API 560 для общего обслуживания нефтеперерабатывающих заводов
- API 570 Проверка, ремонт, изменение и переоценка находящихся в эксплуатации трубопроводных систем
- API 579 Проект рекомендуемой практики API для пригодности к эксплуатации
Роберт Б. Адамс
- Президент и главный исполнительный директор EST Group, Inc. Харлисвилл, Пенсильвания
Интересные статьи о неудачных испытаниях под давлением
Сосуд высокого давления Отказ во время пневматического испытания
Сосуд высокого давления Отказ во время гидроиспытаний
Сосуд высокого давления Отказ во время воздушных испытаний
Примечание(я) автора. ..
Испытание под давлением ASME B31.3
Системы трубопроводовобычно проектируются и изготавливаются в соответствии с применимыми нормами. Конечно, использование ASME B31.3 может быть применимо к судам, перевозящим нефть, но вы действительно должны следовать правилам, для которых была разработана система трубопроводов. Поскольку я знаком с B31.3, а не с европейским (или другим страновым) эквивалентом, я буду основывать свой ответ на B31.3.
ASME B31.3 требует «проверки герметичности» системы трубопроводов. Это не структурный тест, это всего лишь тест, чтобы определить, есть ли в системе точки, которые негерметичны.* С другой стороны, существуют нормы, которые могут потребовать проведения структурных испытаний, таких как нормы для котлов и сосудов под давлением. В этом случае проводится гидростатическое испытание, чтобы убедиться, что сосуд и прикрепленные к нему трубопроводы являются конструктивно прочными, а не только герметичными.
ASME B31.3, пар. 345.1. 341 каждая система трубопроводов должна быть испытана на герметичность. Испытание должно представлять собой гидростатическое испытание на герметичность в соответствии с п.345.4, за исключением случаев, предусмотренных в настоящем документе.
Если владелец считает нецелесообразным гидростатическое испытание на герметичность, может быть проведено либо пневматическое испытание в соответствии с пунктом
. 345.5 или комбинированное гидростатико-пневматическое испытание в соответствии с абз. 345.6 можно заменить, признавая опасность энергии, хранящейся в сжатом газе.
Таким образом, в соответствии с правилами испытание на герметичность с использованием воздуха может быть выполнено, если владелец системы считает, что гидростатическое испытание нецелесообразно.
Важно понимать, что давление, при котором проводится испытание, зависит от расчетного давления.Расчетное давление зависит от пределов допустимых напряжений в трубопроводе, которые также зависят от рабочей температуры.
- Для гидростатических испытаний, пара. 345.4.2 требуется давление, не менее чем в 1,5 раза превышающее расчетное давление.
- Для пневматического испытания, пара. 345.5.4 требуется давление не менее 110 % расчетного давления.
Следующим шагом для инженера (предпочтительно проектировщика трубопроводной системы или специалиста по анализу напряжений) является создание процедур испытаний под давлением.Эти процедуры испытаний под давлением рассматривают возможность хрупкого разрушения при низких температурах, что может быть проблемой при температурах, о которых вы говорите. Процедуры испытаний под давлением на самом деле представляют собой набор процедур (как правило), которые включают в себя такие вещи, как метод создания давления в системе, положения клапанов, удаление предохранительных устройств, изоляция частей системы трубопроводов и т. д.
Относительно низкой температуры, пункт. 345.4.1 гласит: «Жидкостью должна быть вода, за исключением случаев, когда существует вероятность повреждения из-за замерзания или неблагоприятного воздействия воды на трубопровод или технологический процесс (см. F345.4.1). В этом случае можно использовать другую подходящую нетоксичную жидкость». Таким образом, гликоль/вода разрешены.
Если испытание должно проводиться пневматически, испытательное давление должно быть повышено до 25 фунтов на квадратный дюйм, после чего должна быть проведена предварительная проверка, включая осмотр всех соединений. Настоятельно рекомендуется использовать низкотемпературную пузырьковую жидкость.
Итак, в заключение..
- Если спецификация, которую вы получили, заключается в проведении гидроиспытаний при 16 бар, то это должно быть 1.5-кратное расчетное давление 10,67 бар. Следовательно, в соответствии с B31.3 пневматическое испытание следует проводить не при 16 бар, а при 1,1-кратном расчетном давлении или 11,7 бар. Поддерживайте пневматическое давление только до 11,7 бар.
- Возможность хрупкого разрушения должна быть проверена соответствующим инженером. В случае температуры ниже 0°C используемый материал должен быть проверен, чтобы убедиться, что его температура не ниже минимальной пригодной температуры для этой стали.
- Знающий инженер должен составить набор процедур испытаний под давлением.В этих процедурах должно быть указано, какие участки трубы испытываются, в какие положения должны быть помещены клапаны, какие предохранительные устройства необходимо снять (или установить) и т. д.
- Пневматическое испытание должно начинаться при давлении 25 фунтов на кв. дюйм, а предварительная проверка на наличие утечек должна выполняться до повышения давления.
- Самое главное, знающий инженер должен также изучить проектную спецификацию трубопровода на предмет всех требований, относящихся к испытаниям на герметичность или давление.
Хотя B31.3 описывает это как «испытание на утечку», когда оно проводится гидростатически в 1,5 раза больше, чем расчетное, оно находится в действии, структурное испытание.
Пожалуйста, прочтите статью. Министерство труда США OSHA
Безопасность газопровода | Балтиморская газовая и электрическая компания
Высшим приоритетом BGE является безопасность, и мы стремимся поддерживать безопасную и надежную систему природного газа.
Комплексная программа управления целостностью BGE выявляет области с высокими последствиями (HCA), обеспечивает анализ рисков в этих областях, включает базовые оценки целостности каждого сегмента трубопровода и определяет график проверки трубопровода. Выявленные места могут включать места скопления людей и места, где существует ограниченная подвижность лиц, находящихся в помещении.
Текущий мониторинг, техническое обслуживание и меры безопасности трубопроводной сети BGE включают:
- Мониторинг давления в режиме реального времени из нашей круглосуточной диспетчерской, которая поддерживает текущее давление в нашей системе в соответствии с инструкциями по безопасной эксплуатации.
Станции регулирования давления и устройства защиты от избыточного давления обслуживаются по всей системе.
- Обследование утечек магистральных и распределительных трубопроводов через:
- Воздушные инспекции коридоров магистральных трубопроводов отслеживают явные признаки утечек.
- Наземное патрулирование с использованием автомобильные и переносные детекторы измеряют уровень природного газа в воздухе вблизи трубопроводов.
- Команды по борьбе с коррозией измеряют и тестируют катодную защиту стальных трубопроводов. Катодная защита заключается в обеспечении устойчивости стальных трубопроводов к коррозионному воздействию окружающего грунта.
- Внешняя коррозия Прямая оценка раскопок проведена.BGE анализирует собранные данные и периодически выкапывает участки трубопровода для непосредственной оценки целостности трубопровода и проведения технического обслуживания или ремонта.
- Добавление меркаптана для обнаружения газа по запаху, что позволяет быстро обнаруживать утечки.
- Участие в системе единого звонка в Мэриленде для повышения осведомленности о предотвращении повреждений. Узнайте больше о Miss Utility и 811.
- Включение в процесс оповещения BGE о раскопках , который требует, чтобы инспектор BGE по предотвращению повреждений контролировал работы вблизи трубопроводов и оставался на участках, где работы ведутся в пределах 10 футов от трубопровода.
- Маркеры трубопроводов размещаются там, где это необходимо для обозначения местоположения трубопроводов. Однако никогда не полагайтесь на наличие или отсутствие маркеров для определения точного местоположения подземных коммуникаций. Для получения дополнительной информации посетите веб-сайт Национальной картографической системы трубопроводов.
- Управление растительностью проводится на коридорах магистральных трубопроводов, чтобы сделать трубопроводы видимыми с воздуха и открытыми для обычного и аварийного доступа.
- Испытание гидростатическим давлением испытание новых трубопроводов во время строительства. Перед вводом в эксплуатацию трубопровод заполняется водой и подвергается давлению до уровня, превышающего рабочее давление трубы.
Если вы чувствуете запах природного газа , немедленно покиньте это место и позвоните в BGE по телефону 1-877-778-7798 или 1-800-685-0123.
В случае обрыва линий электропередач держитесь подальше от этого места и позвоните в BGE по телефону 1-877-778-2222 или 1-800-685-0123.
Представители доступны 24 часа в сутки, 7 дней в неделю.
Испытания и проверки трубопроводов под давлением
Типичное испытание погрузочного рукава с водой.
Узкоспециализированная услуга, предоставляемая PPSI, – испытание трубопровода гидростатическим давлением. Испытания под давлением проверяют структурную целостность и прочность трубопровода, проверяя его способность выдерживать давление, превышающее нормальное, без деформации, повреждения или выхода из строя. Эта форма проверки целостности требуется в соответствии с отраслевыми нормами и может включать плановое соблюдение, аварийное реагирование на предполагаемую утечку в трубопроводе, квалификацию более высокого MOP или повторную квалификацию недавно отремонтированных или построенных трубопроводов.Услуги по тестированию предназначены для трубопроводов, погрузочных рукавов, эстакад для грузовиков, горячих ям, резервуаров и вторичной защитной оболочки.
Государственные нормативные акты по охране окружающей среды вынуждают объекты с нефтью или другими продуктами, опасными для окружающей среды, периодически проверять трубопроводы продукта под давлением. Морские трубопроводы, станционные трубопроводы, внутригосударственные и межгосударственные трубопроводы регулируются различными государственными органами в зависимости от юрисдикции. Наше современное оборудование для сбора данных имеет точность до .05% от полного диапазона шкалы, поддерживается в хорошем состоянии и ежегодно калибруется третьей стороной для обеспечения точного сбора данных.
В отличие от некоторых наших конкурентов, мы не ставим «количество испытаний, выполненных за день», а не «качество каждого испытания» в подходе к гидростатическим испытаниям. Наша методология испытаний включает выполнение предварительных расчетов заполнения линии, объема испытаний , %SMYS трубы и обнаружение захвата воздуха, а также выполнение полного визуального осмотра каждого компонента в испытательном участке и документирование даже незначительных дефектов, таких как коррозия, потеря металла и дефекты покрытия.Предоставляются полные и точные отчеты об испытаниях (в собственном формате) с полной документацией, включая валидационные расчеты, подтверждающие изменение объема и прирост/падение давления с температурной компенсацией, а также рекомендации по устранению недостатков предоставляются владельцу трубопровода после испытаний. Расчеты проверки принимают переменные, такие как материал трубы, местоположение трубы, продукт и погода, и используют физические характеристики каждой из них в сложном наборе расчетов для подтверждения того, что увеличение и уменьшение давления/объема находятся в допустимых пределах.Если линия не может пройти тест, мы внесем все возможные исправления для достижения удовлетворительного результата, прежде чем объявить линию «неудачной». Этот метод расчета с температурной компенсацией абсолютно необходим, когда речь идет о подземных или недоступных трубопроводах, где простой визуальный осмотр активных утечек невозможен.
Основным преимуществом использования испытаний на гидростатическую прочность по сравнению с испытаниями на обнаружение утечек, сертифицированными NWGLDE, является стоимость одного испытания. Если стандартное гидроиспытание признано неудачным, можно использовать сертифицированное третье лицо прецизионное испытание на герметичность для подтверждения отказа, что позволяет сэкономить деньги на всех испытаниях, которые были признаны успешными. Кроме того, несмотря на заявления об обратном, на все испытания по обнаружению утечек в той или иной степени влияют колебания температуры, и чувствительность испытаний снижается по мере увеличения объема испытательного участка трубопровода.
Наш персонал имеет квалификацию DOT (письменный экзамен NCCER) и знает правила и отраслевые стандарты, чтобы гарантировать, что клиент будет соблюдать их. Наши квалификации DOT OQ и записи о безопасности можно найти на веб-сайте ISNET. (www.isnetworld.com).Наши программы по наркотикам и алкоголю управляются третьей стороной, и с ними можно ознакомиться на веб-сайте NCMS. (www.nationalcompliance.com) PPSI сертифицирована в штате Калифорния для проведения испытаний трубопроводов гидростатическим давлением, и этот список можно найти на веб-сайте Государственной земельной комиссии: http://osfm.fire.ca.gov/pipeline/pipeline_hydrotest
Выполненные услуги по испытаниям и инспекциям включают:
- Гидростатические (вода) и гидравлические (топливо) испытания под давлением трубопроводов жидкого нефтепродукта, трубопроводов природного газа, водопроводов, наливных рукавов и многих других типов трубопроводных систем.
- Заполнение линии «под ключ», обезвоживание и осушка до отрицательной точки росы путем очистки скребками, включая установку временных насосов, фильтров, резервуаров для гидроразрыва и сопутствующего оборудования.
- Температурная компенсация и объемные испытания.
- Кривые испытаний при низком и высоком давлении. Пневматические испытания при сверхнизком давлении для систем вторичной защитной оболочки и резервуаров. Испытания высокого давления таких систем, как линии природного газа до 3000 фунтов на квадратный дюйм.
- Обслуживание и калибровка предохранительного клапана.
- Индикатор давления и калибровка трансмиттера.
- Испытание под давлением морских перекачивающих шлангов и погрузочных рукавов.
- Варианты контактной воды, включая очистку и сброс на месте или удаление за пределы участка.
- Обнаружение утечек гелия в резервуарах, трубопроводах и вторичных защитных пространствах. (Эта услуга может выполняться в сочетании с испытанием пневматическим давлением для обнаружения источника любых предполагаемых утечек.
)
- API-580 Оценки на основе рисков и API-570 Рекомендации и координация проверок.
- Рекомендация и координация сертифицированных NWGLDE сторонних испытаний на обнаружение утечек или трассирующих испытаний.
Наш комплексный 100% визуальный осмотр надземных участков трубопровода, который проводится при каждом гидроиспытании, выявил следующие аномалии трубопровода, некоторые из которых были обнаружены и устранены еще до проведения гидроиспытаний.
Примеры активных утечек и отказов, обнаруженных во время контролируемого гидростатического испытания. Эти утечки могли бы быть гораздо более масштабными, если бы они произошли во время нормальной эксплуатации.
Пневматические испытания под давлением | Vaetrix
Испытания пневматическим давлением — регистрация данных с помощью Vaetrix ETG
Bluetooth
Испытания под давлением — это практика воздействия на трубы или трубопроводные системы давлением, превышающим рабочее давление, для подтверждения целостности труб и фитингов, составляющих систему. Концепция состоит в том, чтобы точно определить любые слабые места, прежде чем что-то пойдет не так. Для большинства газовых линий низкого давления предпочтительной испытательной средой является сжатый воздух или азот.Например, двухдюймовая рабочая магистраль может быть испытана при давлении около 100 фунтов на квадратный дюйм в течение 10–15 минут и должна поддерживать постоянное давление. Ужесточенные правила теперь требуют, чтобы все новые линии электропередачи, распределительные линии или линии обслуживания перед вводом в эксплуатацию проходили испытания под давлением.
Получение данных о давлении с помощью приложения Data Director
Любой Vaetrix ETG, оснащенный опцией Bluetooth, будет работать с приложением Data Director.Сеансы регистрации данных можно настраивать, запускать и останавливать с помощью нашего телефона или планшета. Интерфейс очень прост в использовании, а датчик четко показывает LOG на ЖК-дисплее. Результаты должны быть зарегистрированы и сохранены в системе учета газовой компании. Таким образом, независимо от того, использует ли технический специалист регистратор графиков давления, аналоговый манометр, грузопоршневой манометр или даже цифровой регистратор данных давления, он должен убедиться, что результаты отсканированы и загружены обратно в офис.Это требует времени и может быть дорогостоящим, если результаты теста потеряны, не приняты или должны быть переделаны. Что, если бы существовал более быстрый и надежный способ просмотра, хранения и обмена результатами испытаний в полевых условиях?
Загрузить результаты одним нажатием кнопки. Просматривайте и переименовывайте сеансы на телефоне, загружайте результаты на телефон или сделайте еще один шаг и сохраните их в облаке. Учетная запись бесплатна от Google и может быть настроена для любой корпоративной или индивидуальной учетной записи Gmail. Добавьте заметки по тестированию с помощью Microsoft Excel, Google Таблиц и создайте безопасный файл . pdf, чтобы поделиться файлом. Отправьте копию теста по электронной почте или поделитесь ссылкой на файл. Все, что вам нужно, это подключение к Интернету.
Vaetrix ETG может хранить 64 000 записей или 200 сеансов в памяти датчика. Каждая точка давления записывается с отметкой даты/времени на часах реального времени внутри манометра. Данные сохраняются до тех пор, пока вы не сотрете или не удалите память в датчике. Если вы предпочитаете передавать результаты с помощью USB, просто подключите кабель и загрузите программное приложение Data Director на свой ПК.
Выберите точность 0,05 %, 0,1 % или 0,25 % от полной шкалы в соответствии с вашими требованиями к точности. Точность основана на диапазоне температур от 14°F до 122°F и остается постоянной в выбранном диапазоне давления. Все устройства ETG поставляются с сертификатом и данными NIST. Информация о серийном номере и модели манометра записывается при каждом сеансе регистрации данных для обеспечения прослеживаемости.
Опрессовка труб из ПЭНД – статьи и ресурсы
Советы SCS с места: как компенсировать влияние изменений температуры окружающей среды на изменения давления в трубе во время опрессовки трубы из ПЭНД с использованием несжимаемой жидкости
17 февраля 2016 г.
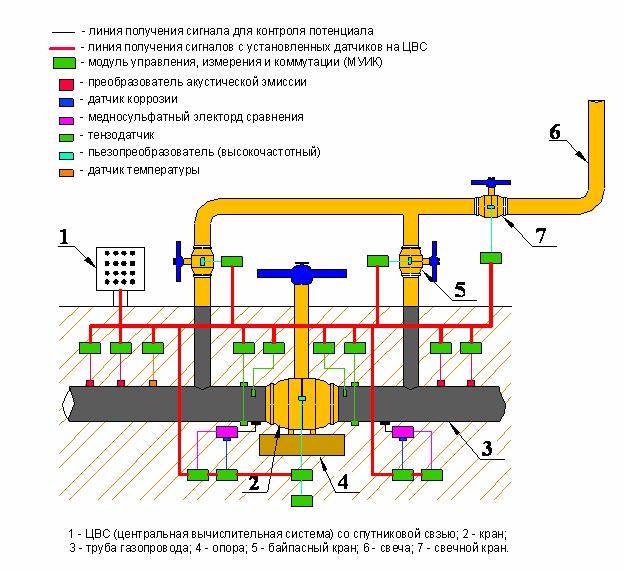
Испытание газового коллектора диаметром 18 дюймов, работающего под вакуумом.
Испытания под давлением труб из полиэтилена высокой плотности проводятся почти на всех проектах по строительству систем облицовки свалок и систем сбора свалочных газов. Трубы должны быть проверены, чтобы убедиться, что сварные швы не повреждены и не протекает. Когда инженеры задают испытание под давлением, они определяют необходимое испытательное давление, продолжительность испытания и допустимый перепад давления по завершении испытания. Испытательное давление может варьироваться от одного применения трубы к другому. Например, заданное испытательное давление может достигать 1.5-2-кратное максимальное рабочее давление в трубопроводе для магистральных трубопроводов фильтрата; тогда как для труб, используемых в системах сбора свалочного газа, где трубы находятся под вакуумом, указанное испытательное давление может быть меньше. Продолжительность испытания может варьироваться от одного часа до нескольких часов, а допустимый перепад давления может варьироваться от нуля до процента от начального давления.
Что часто отсутствует в спецификациях испытаний под давлением, так это влияние изменения температуры окружающей среды на изменения давления внутри трубы во время испытания.Если для испытания под давлением используется несжимаемая жидкость (например, вода), изменения давления из-за изменений температуры окружающей среды менее значительны, чем при использовании сжимаемой жидкости (например, воздуха).
Для несжимаемых жидкостей SCS разработала математическую модель, которая позволяет инженеру или подрядчику рассчитать изменения давления из-за изменений температуры окружающей среды во время испытания. Расчетное изменение давления следует учитывать при оценке того, являются ли результаты испытаний удовлетворительными или неудовлетворительными.Повышение температуры окружающей среды во время испытания может вызвать расширение трубы, а расширение вызывает дополнительный перепад давления, не связанный с какой-либо негерметичностью сварных швов. С другой стороны, снижение температуры окружающей среды может вызвать сжатие трубы, что приведет к увеличению давления в трубе. В этом случае падение давления из-за утечки в сварном шве может быть не обнаружено из-за более высокого давления, создаваемого внутри трубы из-за сжатия трубы. Рекомендуется, чтобы инженеры или подрядчики использовали математическую модель для расчета измененного допустимого перепада давления с учетом расчетного изменения давления (положительного для расширения трубы или отрицательного для сжатия трубы) до проведения оценки «годен/не годен».
Недавно во время полевых испытаний произошло падение давления, которое немного превышало указанное допустимое падение давления. Полевой персонал сообщил об изменении температуры окружающей среды во время двухчасового испытания. Когда модифицированный допустимый перепад давления был рассчитан с использованием модели SCS для учета изменения температуры окружающей среды, испытание было пройдено. Обратите внимание, что полевая документация чрезвычайно важна для оценки результатов «годен/не годен».Это становится еще более важным, когда указанная продолжительность испытаний составляет несколько часов, а колебания температуры окружающей среды значительны.
Вопросы? Контакт Али Хатами, доктор философии, PE, LEP, CGC, является директором проекта и вице-президентом SCS Engineers. Он также является нашим национальным экспертом по проектированию полигонов и обеспечению качества строительства. Он имеет почти 40-летний опыт исследований и профессионального опыта в области механического, структурного и гражданского строительства. Доктор Хатами приобрел обширный опыт и знания в области геологии, гидрогеологии, гидрологии, гидравлики, методов строительства, материаловедения, обеспечения качества строительства (CQA) и устойчивости грунтовых систем.Доктор Хатами применил этот опыт при размещении многочисленных свалок и при восстановлении участков, загрязненных опасными отходами.
Подробнее здесь.