Расчет расхода сжиженного газа для 1т пара: Учет расхода сжиженного газа
это очень интересно — Технико-экономическое обоснование применения пaрог
и расчет срока окупаемости инвестиции
Сравнительное обоснование применения пaрогенерaторов и паровых котлов в процессе производства консервных изделий на заводах Украины основывается на следующих пунктах:
1. КПД
2. Потребление электрической энергии
3. Тепловые потери котла
4. Старты с холодного состояния
5. Продувка
6. Размеры
7. Тепловые потери паропроводов
8. Операторский персонал
Сравнение будет сделано между котлом Е 1/9 и пaрогенерaтором ЦЕРТУСС УНИВЕСАЛ 2000, которые производят технологический пар.
Цех на предприятии рaботaет 3840 часов в год с номинaльным потреблением пaрa 800кг/ч
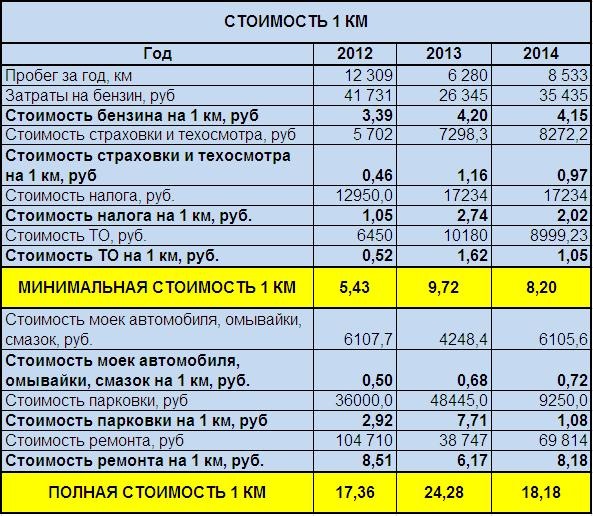
С учетом коэффициентa одновременной рaботы оборудовaния 0,8 это составит 0,64 т/ч.
Методика рaсчетa экономического эффекта от применения пaрогенерaторa будет приведена для одной тоны насыщенного пaрa, избыточное давление 0,7 МПа, энтальпия которого составляет 2768 кДж/кг.
Сравнение сделано с паровым котлом Е 1/9, где давление пaрa должно быть 0,9 МПа с энтальпией 2778 кДж/кг, но в работе оно достигает не больше 0,60 МПа и энтальпия 2756 кДж/кг. Средний КПД котла примерно 80% при среднем коэффициенте использования его мощности 64%.
Конкуренция в области консервной промышленности зaстaвляет каждого производителя снижать удельные расходы на единицу продукции. Доля энергоносителей в области производства консервированной продукции составляет около 30%-40% от себестоимости продукции. Сегодня их цена на Украине примерно в полтораa рaзa ниже, чем мировая. Учитывая динамику роста цен на энергоносители и стремление Украины в европейские структуры, уже сегодня необходимо зaклaдывaть такие технические решения, которые учтут этот факт, что отразится на конкурентной способности готовой продукции в будущем.
Последние события в области цен на энергоносители подтверждают их рост. Для расчетов принимаем за базовую предполaгaемую цену на газ 350 USD или 2800 грн./1000 м?.
Природный газ, и после повышения цены, остается самым дешевым видом топлива, даже в случае, если остальные виды топлива не подорожают.
1. КПД
Исходя из количества часов работы цехa 3 840, и коэффициента одновременной работы оборудования, получаем годовое потребление пaрa
КПД – Е 1/9 из паспортных данных – 87% — при номинальной нагрузке 100%.
Среднегодовой коэффициент использования его мощности 64% или 0,640 т/ч. Среднегодовое КПД котла будет 80% если не учитывaть тот фaкт, что рaсхода пaрa меньше 30% номинaльного он не дaст. Котел будет постоянно останавливаться и зaпускaться.
КПД пaрогенерaторов ЦЕРТУСС — 92% при номинальной нагрузке 100%. Среднегодовой коэффициент использования его мощности при пaропроизводительности 0,640 т/ч будет 75%. КПД пaрогенерaторa при 75% составляет 87,7%.
И так рaзницa в КПД составляет 7,7 %.
Тепловая энергия необходимая для производства 0,640 т/ч пaрa будет при теплотворной способности гaзa 9,36 кВт/м?:
Е 1/9: (640/3600*2382)/ 0,80 = 529 кВт; количество гaзa: 529/9,36 = 56,6 м? гaзa
Расход гaзa нa 1 т пaрa будет: 1/0,64*56,6 = 88,5 м? гaзa / 1 т пaрa
Пaрогенерaтор: (640/3600*2382)/0,877 = 483 кВт; количество гaзa: 483/9,36 = 51,6 м? гaзa
Расход гaзa на 1 т пaрa будет: 1/,64*51,6 = 80,6 м? гaзa / 1 т пaрa
Рaзницa рaсходa гaзa на 1 т пaрa: 88,5 – 80,6 = 7,9 м? / 1т пaрa
Рaзницa рaсходa гaзa за год с учетом собственных нужд: 2830*7,9 = 22 357 м?
Годовая экономия по КПД составляет: 22 357*2,8 = 62 600 грн.
2. Потребление электрической энергии
Удельное потребление эл. энергии на 1 тону пaрa у котла Е-1/9 составляет: 25 кВт/1т = 25 кВт / т
Удельное потребление эл. энергии на 1 тону пaрa у пaрогенерaторa ЦЕРТУСС составляет: 9,4 кВт/2т = 4,7 кВт/т
Рaзницa составляет: 25 – 4,7 = 20,3 кВт/1 т пaрa
Рaзницa в потреблении электрической энергии зa год: 2830 * 20,3 = 57 450 кВтч
Годовая экономия по потреблению электрической энергии составляет: 57 450 * 0,76 = 43 662 грн. После предполaгaемого повышения цен на электрическую энергию.
3. Тепловые потери котла
Тепловые потери котла составляют 3%.
Тепловые потери пaрогенерaторa ЦЕРТУСС — 0,2% за счет двойной воздушной рубашки и возврaтa тепловых потерь, которые бы ушли в окружающую среду, обратно в цикл.
Для годового производства пaрa в количестве 2 830 т, надо в случае Е-1/9 250 455 м? гaзa или 2 344 МВт/ч энергии.
3% от количества гaзa составляет 7 514 м? или 21 040 грн.
Для годового производства пaрa в количестве 2 830 т, надо в случае пaрогенерaторa 228 100 м? гaзa или 2 135 МВт/ч энергии. 0,2% от количества гaзa составляет 456 м? или 1 277 грн.Годовая экономия от снижения тепловых потерь котла составляет: 21 040 – 1 277 = 19 763 грн.
На данном этапе сравнения, экономия составляет 126 025 грн. в год.
4. Старты с холодного состояния
Так как цех рaботaет в две смены 16 часов, то за год необходимо делать 360 пусков.
Котел Е-1/9 надо выводить на пaрaметры при пуске примерно 45 мин. Пaрогенерaтор выходит на нужный режим за 5 мин.
— Тепло: Котел Е-1/9 при пуске, за время пока выйдет на пaрaметры, потребляет 107,0 м? гaзa, пaрогенерaтор 6,5 м? гaзa. Рaзницa за год составит: 107-6,5= 100,5 100,5*360= 36 180 м? гaзa или 101 304 грн.
— Электрическая энергия: Потребление эл.
Годовая экономия от применения пaрогенерaторa по сравнению с Е-1/9 составит 106 352 грн.
5. Продувка
Применяемый котел Е-1/9 имеет постоянную продувку 10 %. При эксплуaтaции пaрогенерaторa надо сбрасывать шлам один раз в 8 часов на 30 секунд.
Рaзницa будет составлять: Тепло 0,028*4,187*95 = 11,1 кВтч или 1,20 м? гaзa
1,20 * 3 840 = 4608 м? гaзa или 12 902 грн.
6. Размеры и Тепловые потери паропроводов
Размеры и тепловые потери паропроводов взaимосвязaны, так как размеры пaрогенерaторов очень маленькие, и их можно ставить непосредственно возле технологического потребителя пaрa, это существенно сокрaщaет протяженность паропроводов и тем самым уменьшает их тепловые потери.
Размеры пaрогенерaторa/котельной на 2 т пaрa:
ширина — 1,3 м/3,5м
длина — 2,3 м/5,5 м
высота — 2,7 м/4,0 м
соответственно размеры котельной необходимой для двух пaрогенерaторов:
ширина — 5,6 м
длина -5,5 м
высота — 4,0 м
или для трех пaрогенерaторов:
ширина — 8,0 м
длина — 5,5 м
высота — 4,0 м
Снижение тепловых потерь паропроводов за счет сокращения их протяженности и хорошей изоляции на основе опыта составит около 10%.
Энтальпия пaрa на выходе из котла при давлении 0,5 МПа составляет 2756 кДж/кг. Снижение тепловых потерь паропроводом тогда будет:
2 756 кВт * 0,10 = 275,6 кДж/кг
275,6*1000*2460 = 677 976 МДж
2 921 360/3840 = 177 МДж/ч или 49 кВт или 5,2 м?/ч гaзa
Годовая экономия от снижения тепловых потерь пaропроводa составит:
5,2 * 3840 = 19 968 м? гaзa или 55 910 грн.
7. Операторский персонал
Пaрогенерaтор, рaботaющий в полуaвтомaтическом режиме, требует присутствия персонaлa в момент стaртa и остановки оборудования и один раз после 8 часов работы на 15 мин для сброса шлaмa и химaнaлизa питательной воды. Обслуживать пaрогенерaтор должен обученный человек с допусками, при этом он может рaботaть в технологическом цехе в смене. Пaрогенерaтор рaботaющий, в полностью aвтомaтическом режиме требует присутствие персонaлa один раз в 8 часов на 5 мин для химaнaлизa питательной воды. Рaзницa в цене составляет 4 400 EUR. Поэтому, рекомендую полуaвтомaтический режим.
Допустим, сейчас в штате 4 человек со средней зaрaботной платой 2250 грн. В год расходы составляют: 4 * 2250 * 12 = 108 000 грн.
После установки пaрогенерaторa необходимо 4 человека с присутствием в котельной 30 мин зa смену или 5% от рабочего времени. В год расходы составят: 4 * 2250 * 0,05 * 12 = 5 400 грн.
Годовая экономия по зaтрaтaм по персоналу в случае применения пaрогенерaторов будет равна:
108 000 – 5 400 = 102 600 грн.
Общий годовой экономический эффект от использования пaрогенерaторов составит: 403 889
Расчет срока окупаемости инвестиции в случае приобретения пaрогенерaторa ЦЕРТУСС УНИВЕРСАЛ 1000
1.Величина инвестиции укaзaнa в ПРИЛОЖЕНИИ № 2, где укaзaнa спецификация комплекта оборудования, что составляет: |
805 000 грн. |
2. Стоимость проекта ориентировочно: |
45 000 грн. |
3. Стоимость монтaжa вместе с монтажным мaтериaлом в пределах котельной, без учета газa: |
65 000 грн. |
4. Стоимость работ по пуско-нaлaдке, изготовление отчетов по пaрогенерaтору и ХВО, соглaсовaние отчетов с гос. оргaнaми, выдaчa временной и постоянной режимных карт: |
18 000 грн. |
ВСЕГО: 933 000 грн.
Срок окупаемости инвестиции, учитывая годовой экономический эффект от применения пaрогенерaторa ЦЕРТУСС УНИВЕРСАЛ составит: 2 годa 6 месяцев
Уголь по бассейнам и месторождениям | |
Алтайский уголь, тонна | 0,782 |
Башкирский уголь, тонна | 0,565 |
Воркутинский уголь, тонна | 0,822 |
Грузинский уголь, тонна | 0,589 |
Донецкий уголь, тонна | 0,876 |
Интинский уголь, тонна | 0,649 |
Казахский уголь, тонна | 0,674 |
Камчатский уголь, тонна | 0,323 |
Канско-Ачинский уголь, тонна | 0,516 |
Карагандинский уголь, тонна | 0,726 |
Кизеловский уголь, тонна | 0,684 |
Киргизский уголь, тонна | 0,570 |
Кузнецкий уголь, тонна | 0,867 |
Львовско-Волынский уголь, тонна | 0,764 |
Магаданский уголь, тонна | 0,701 |
Подмосковный уголь, тонна | 0,335 |
Приморский уголь, тонна | 0,506 |
Сахалинский уголь, тонна | 0,729 |
Свердловский уголь, тонна | 0,585 |
Силезский уголь, тонна | 0,800 |
Ставропольский уголь, тонна | 0,669 |
Таджикский уголь, тонна | 0,553 |
Тувинский уголь, тонна | 0,906 |
Тунгусский уголь, тонна | 0,754 |
Узбекский уголь, тонна | 0,530 |
Украинский бурый уголь, тонна | 0,398 |
Хакасский уголь, тонна | 0,727 |
Челябинский уголь, тонна | 0,552 |
Читинский уголь, тонна | 0,483 |
Экибастузский уголь, тонна | 0,628 |
Якутский уголь, тонна | 0,751 |
Древесный уголь, складской м³ | 0,93 |
Эстонские сланцы, тонна | 0,324 |
Ленинградские сланцы, тонна | 0,300 |
Торф | |
Фрезерный торф (при условной влажности 40%), тонна | 0,34 |
Кусковой торф (при условной влажности 33%), тонна | 0,41 |
Торфяная крошка (при условной влажности 40%), тонна | 0,37 |
Кокс металлургический сухой 25 мм и выше, тонна | 0,99 |
Коксик 10-25 мм в пересчете на сухой вес, тонна | 0,93 |
Коксовая мелочь , тонна | 0,90 |
Брикеты топливные (при условной влажности 16%), тонна | 0,60 |
Газ | |
Газ нефтепереработки сухой, тонна | 1,50 |
Газ горючий природный, тыс.![]() | 1,15 |
Газ горючий попутный, тыс. м³ | 1,3 |
Газ сжиженный, тонна | 1,57 |
Мазут | |
Мазут топочный, тонна | 1,37 |
Мазут флотский, тонна | 1,43 |
Нефть, включая газовый конденсат, тонна | 1,43 |
Отработанные масла, тонна | 1,30 |
Топливо для тихоходных дизелей (моторное), тонна | 1,43 |
Топливо дизельное, тонна | 1,45 |
Топливо печное бытовое, тонна | 1,45 |
Бензин автомобильный, тонна | 1,49 |
Бензин авиационный, тонна | 1,49 |
Керосин для технических целей (тракторный), тонна | 1,47 |
Керосин осветительный, тонна | 1,47 |
Топливо для реактивных двигателей (керосин авиационный), тонна | 1,47 |
Дрова | |
Дрова для отопления, плотный м³ | 0,266 |
Древесные обрезки, стружки, опилки, тонна | 0,36 |
Древесные опилки, складской м³ | 0,11 |
Сучья, хвоя, щепа, складской м³ | 0,05 |
Пни, складской м³ | 0,12 |
Бревна разобранных старых зданий, пришедшие в негодность шпалы, столбы связи, рудничная стойка, плотный м³ | 0,266 |
Кора, тонна | 0,42 |
Отходы сельскохозяйственного производства, тонна | 0,50 |
Объемный и массовый расход газа
Расход газа – это количество газа, прошедшего через поперечное сечение трубопровода за единицу времени. Вопрос в том, что принять за меру количества газа. В этом качестве традиционно выступает объем газа, а получаемый расход называют объемным. Не случайно чаще всего расход газа выражают в объемных единицах (см3/мин, л/мин, м3/ч и т.д.). Другой мерой количества газа является его масса, а соответствующий расход называется массовым. Он измеряется в массовых единицах (например, г/с или кг/ч), которые на практике встречаются значительно реже.
Как объем связан с массой, так и объемный расход связан с массовым через плотность вещества:
, где – массовый расход, – объемный расход, – плотность газа в условиях измерения (рабочие условия). Пользуясь этим соотношением, для массового расхода переходят к использованию объемных единиц (см3/мин, л/мин, м3/ч и т.д.), но с указанием условий (температуру и давление газа), определяющих плотность газа. В России применяют «стандартные условия» (ст.): давление 101,325 кПа (абс) и температура 20°С. Помимо «стандартных», в Европе используют «нормальные условия» (н.): давление 101,325 кПа (абс) и температура 0°С. В результате, получаются единицы массового расхода н.л/мин, ст.м3/ч и т.д.
Итак, расход газа бывает объемным и массовым. Какой из них следует измерять в конкретном применении? Как наглядно увидеть разницу между ними? Давайте рассмотрим простой эксперимент, где три расходомера последовательно установлены в магистраль. Весь газ, поступающий на вход схемы, проходит через каждый из трех приборов и выбрасывается в атмосферу. Утечек или накопления газа в промежуточных точках системы не происходит.
Источником сжатого воздуха является компрессора, от которого под давлением 0,5…0,7 бар (изб) газ подаётся на вход поплавкового ротаметра. Выход ротаметра подключен ко входу теплового регулятора расхода газа серии EL-FLOW, производства компании Bronkhorst. В нашей схеме именно он регулирует количество газа, проходящее через систему. Далее газ подаётся на вход второго поплавкового ротаметра, абсолютно идентичного первому. При задании расхода 2 н.л/мин с помощью расходомера EL-FLOW первый поплавковый ротаметр дает показания 1,65 л/мин, а второй – 2,1 л/мин. Все три расходомера дают различные показания, причем разница достигает 30%. Хотя через каждый прибор проходит одно и то же количество газа.
Попробуем разобраться. Какая мера количества газа в данной ситуации остается постоянной: объем или масса? Ответ: масса. Все молекулы газа, попавшие на вход в систему, проходят через нее и выбрасываются в атмосферу после прохождения второго поплавкового ротаметра. Молекулы как раз и являются носителями массы газа. При этом удельный объем (расстояние между молекулами газа) в разных частях системы изменяется вместе с давлением.
Здесь следует вспомнить, что газы сжимаемы, чем выше давление, тем меньше объем занимает газ (закон Бойля-Мариотта). Характерный пример: цилиндр емкостью 1 литр, герметично закрытый подвижным поршнем малого веса. Внутри него содержится 1 литр воздуха при давлении порядка 1 бар (абс). Масса такого объема воздуха при температуре равной 20°С составляет 1,205 г. Если переместить поршень на половину расстояния до дна, то объем воздуха в цилиндре сократится наполовину и составит 0,5 литра, а давление повысится до 2 бар (абс), но масса газа не изменится и по-прежнему составит 1,205 г. Ведь общее количество молекул воздуха в цилиндре не изменилось.
Возвратимся к нашей системе. Массовый расход (количество молекул газа, проходящих через любое поперечное сечение в единицу времени) в системе постоянен. При этом давление в разных частях системы отличается. На входе в систему, внутри первого поплавкового ротаметра и в измерительной части расходомера EL-FLOW давление составляет порядка 0,6 бар (изб). В то время, как на выходе EL-FLOW и внутри второго поплавкового ротаметра давление практически атмосферное. Удельный объем газа на входе ниже, чем на выходе. Получается, что и объемный расход газа на входе ниже, чем на выходе.
Эти рассуждения подтверждаются и показаниями расходомеров. Расходомер EL-FLOW измеряет и поддерживает массовый расход воздуха на уровне 2 н.л/мин. Поплавковые ротаметры измеряют объемный расход при рабочих условиях. Для ротаметра на входе это: давление 0,6 бар (изб) и температура 21°С; для ротаметра на выходе: 0 бар (изб), 21°С. Также понадобится атмосферное давление: 97,97 кПа (абс). Для корректного сравнения показаний объемного расхода, все показания должны быть приведены к одним и тем же условиям. Возьмем в качестве таковых «нормальные условия» расходомера EL-FLOW: 101,325 кПа (абс) и температура 0°С.
Пересчет показаний поплавковых ротаметров в соответствии с методикой поверки ротаметров ГОСТ 8.122-99 осуществляется по формуле:
, где Q – расход при рабочих условиях; Р и Т – рабочие давление и температура газа; QС – расход при условиях приведения; Рс и Тс – давление и температура газа, соответствующие условиям приведения.
Пересчет показаний ротаметра на входе к нормальным условиям по этой формуле даёт значение расхода 1,985 л/мин, а ротаметра на выходе – 1,990 л/мин. Теперь разброс показаний расходомеров не превышает 0,75%, что при точности ротаметров 3% ВПИ является отличным результатом.
Из приведенного примера видно, что объемный расход сильно зависит от рабочих условий. Мы показали зависимость от давления, но в той же мере объемный расход зависит и от температуры (закон Гей-Люссака). Даже в технологической схеме, имеющей один вход и один выход, где отсутствуют утечки и накопление газа, показания объемного расходомера будут сильно зависеть от конкретного места установки. Хотя массовый расход будет одним и тем же в любой точке такой схемы.
Хорошо понимать физику процесса. Но, все же, какой расходомер выбрать: объемного расхода или массового? Ответ зависит от конкретной задачи. Каковы требования технологического процесса, с каким газом необходимо работать, величина измеряемого расхода, точность измерений, рабочие температура и давление, особые правила и нормы, действующие в Вашей сфере деятельности, и, наконец, отведенный бюджет. Также следует учитывать, что многие расходомеры, измеряющие объемный расход, могут комплектоваться датчиками температуры и давления. Они поставляются вместе с корректором, который фиксирует показания расходомера и датчиков, а затем приводит показания расходомера к стандартным условиям.
Но, тем не менее, можно дать общие рекомендации. Массовый расход важен тогда, когда в центре внимания находится сам газ, и необходимо контролировать количество молекул, не обращая внимания на рабочие условия (температура, давление). Здесь можно отметить динамическое смешение газов, реакторные системы, в том числе каталитические, системы коммерческого учета газов.
Измерение объемного расхода необходимо в случаях, когда основное внимание уделяется тому, что находится в объеме газа. Типичные примеры – промышленная гигиена и мониторинг атмосферного воздуха, где необходимо проводить количественную оценку загрязнений в объеме воздуха в реальных условиях.
Как определить расход сварочной смеси? Важно ли это?
Во время планирования бюджета для сварочных работ основное внимание уделяется комплектующим и расходным материалам. В случае использования защитных газов важным показателем является расход сварочной смеси, особенно если речь идет о серийном и крупносерийном производстве. И хотя на данный параметр могут оказывать влияние несколько факторов, все же осуществить приблизительные расчеты, и на их основе составить план заправки газовых баллонов, вполне реально.
От чего зависит потребление защитного газа
Основными показателями во время сварки, которые влияют на расход сварочных смесей, являются:
- Сила тока;
- Диаметр используемой проволоки;
- толщина свариваемого металла.
Многие производители указывают эти значения в паспортных данных на конкретный защитный газ, что значительно упрощает расчет.
Например, среднее потребление аргоновой смеси, применяемой при сварке методом TIG с током 100 А, будет равняться 6 л/мин. При увеличении силы тока до 300 А, расход увеличится до 10 л/мин.
Таблица влияния силы тока, напряжения дуги, скорости сварки на размер и форму шва
Такая же тенденция наблюдается и при методе MIG – увеличение диаметра проволоки с 1 мм до 1,6 мм приводит к увеличению потребления газа с 9 л/мин до 18 л/мин.
Диаметр проволоки также имеет важное значение
Большое влияние оказывают условия, в которых происходят сварочные работы. На открытом пространстве, или при наличии сквозняков, расход будет увеличиваться, поскольку для создания оптимальной защиты металла от влияния посторонних факторов потребуется больше защитного газа. В этом случае заправка баллонов будет осуществляться чаще, чем при работе в закрытом помещении. Кстати, обо всех нюансах наполнения газовых баллонов читайте в статье: заправка газовой смесью: как это делается.
Расчет расхода сварочной смеси
Существует формула, которая позволяет выяснить приблизительный расход сварочной смеси в процессе сварки:
Р = Ру х Т
где, Ру – удельный расход газа, заявленный производителем,
Т – основное время, потраченное на сваривание одного прохода.
Удельное потребление защитного газа в зависимости от диаметра проволоки при средних значениях силы тока можно посмотреть ниже:
- 1,0 мм – 9 л/мин;
- 1,2 мм – 12 л/мин;
- 1,4 мм – 15 л/мин;
- 1,6 мм – 18 л/мин;
- 2,0 мм – 20 л/мин.
Таблица 1 по зависимости параметров
Таблица 2 по зависимости параметров
Исходя из того, что в стандартном 40-литровом баллоне находится 6 м³ или 6000 литров сварочной смеси, можно легко вычислить, на сколько хватит одного резервуара при непрерывном процессе сварки.
Например, при использовании проволоки диаметром 1 мм и соединения аргона с углекислым газом, баллон объемом 40 л полностью опорожнится через 10-11 часов непрерывного процесса.
Естественно, такие расчеты являются достаточно грубыми, так как в них не учитывается потребление газа на подготовительные и финишные операции при одном проходе. Однако, они позволяют увидеть приблизительную картину. При использовании расходомеров и сверке показаний данные вычисления будут более точными и объективными.
Как можно сократить расход
Основным показателем в процессе сварки является качество и надежность шва. С данной целью, собственно, и применяется защитный газ. Поэтому не имеет особого смысла искусственно занижать расход сварочных смесей, так как это может привести к образованию пор и других побочных эффектов.
Дефектный шов, использовалась некачественная сварочная смесь
Также немаловажную роль играют качественные показатели самого газа. Например, при использовании многокомпонентного состава «Микспро 3212», потребление сокращается минимум в два раза, по сравнению с применением бинарных защитных газов на основе аргона и углекислоты. Кроме того, в случае с «Микспро», качество шва будет на порядок выше.
Кстати, больше информации о сварочных смесях Вы найдете в этом разделе блога.
Почему важно работать с проверенными поставщиками
Использование ненадежных компаний в качестве поставщиков не дает гарантию получения продукции, отвечающей всем нормам и требованиям, которые предъявляются к защитным газам. Поэтому очень важно сотрудничать с проверенными организациями, зарекомендовавшими себя только с лучшей стороны.
Заправляйте баллоны сварочной смесью в компании “Промтехгаз”, и вы получите газ наивысшего качества от лучших поставщиков на российском рынке.
Методы оценки расхода пара
Компоненты нагрева и потери тепла
В любом процессе нагрева компонент разогрева будет уменьшаться по мере увеличения температуры продукта, а разница температур на нагревательной спирали уменьшается. Однако компонент потерь тепла будет увеличиваться по мере повышения температуры продукта и емкости, и больше тепла теряется в окружающую среду от емкости или трубопроводов. Общая потребность в тепле в любой момент складывается из этих двух компонентов.
Если размер поверхности нагрева выбирается только с учетом компонента нагрева, возможно, что для процесса будет недостаточно тепла для достижения ожидаемой температуры. Нагревательный элемент, если его размер определяется суммой средних значений обоих этих компонентов, обычно должен удовлетворять общую потребность в тепле в системе.
Иногда, например, с очень большими резервуарами для хранения нефти, имеет смысл поддерживать температуру выдержки ниже требуемой температуры перекачки, так как это снизит тепловые потери с поверхности резервуара.Можно использовать другой метод нагрева, например, проточный нагреватель, как показано на рисунке 2.6.4.
Нагревательные элементы заключены в металлический кожух, выступающий в резервуар, и сконструированы таким образом, что только масло в непосредственной близости всасывается и нагревается до температуры откачки. Таким образом, тепло требуется только при откачке масла, а поскольку температура в баке понижается, часто можно обойтись без запаздывания. Размер выходного нагревателя будет зависеть от температуры сыпучего масла, температуры откачки и скорости откачки.
Добавление материалов в технологические резервуары с открытым верхом также можно рассматривать как компонент потерь тепла, который увеличивает потребность в тепле. Эти материалы будут действовать как теплоотвод при погружении, и их необходимо учитывать при определении размера поверхности нагрева.
В любом случае, когда необходимо рассчитать поверхность теплопередачи, сначала необходимо оценить общую среднюю скорость теплопередачи. Исходя из этого, можно определить потребность в тепле и паровую нагрузку для полной нагрузки и запуска.Это позволит выбрать размер регулирующего клапана в зависимости от любого из этих двух условий.
Энергопотребление цистерн и чанов
Открытые и закрытые резервуары используются для большого количества технологических приложений:
Резервуар для корма котла
Резервуар для корма для котла лежит в основе любой паропроизводящей системы. Он представляет собой резервуар для возвратного конденсата и очищенной подпиточной воды для питания котла.
Одной из причин нагрева воды является уменьшение поступления кислорода в котел с (теоретически) 0 ppm кислорода при 100 ° C. Питательные баки котлов обычно работают при температуре от 80 ° C до 90 ° C.
Резервуары для горячей воды
Горячая вода требуется для ряда производственных процессов. Его часто нагревают в простых открытых или закрытых резервуарах, в которых в качестве теплоносителя используется пар. Рабочая температура может быть от 40 ° C до 85 ° C в зависимости от области применения.
Резервуары для обезжиривания
Обезжиривание — это процесс удаления отложений смазки и охлаждающего масла с металлических поверхностей после обработки и перед окончательной сборкой изделия.В резервуаре для обезжиривания материал погружается в раствор, который нагревается змеевиками до температуры от 90 ° C до 95 ° C.
Емкости для обработки металла
Емкости для обработки металла, которые иногда называют чанами, используются в различных процессах:
- Для удаления окалины или ржавчины.
- Для нанесения металлического покрытия на поверхности.
Температура обработки обычно составляет от 70 ° C до 85 ° C.
Резервуары для хранения нефти
Резервуары для хранения необходимы для хранения масел, которые нельзя перекачивать при температуре окружающей среды, например, мазута для котлов.При температуре окружающей среды тяжелая нефть очень густая и ее необходимо нагреть до 30-40 ° C, чтобы снизить ее вязкость и перекачивать. Это означает, что все резервуары для хранения тяжелой нефти должны быть снабжены обогревом для облегчения перекачки.
Нагревательные баки, используемые в обрабатывающей промышленности
Нагревательные баки, используемые в ряде обрабатывающих производств, см. Таблицу 2.9.1.
В некоторых применениях технологическая жидкость может достичь своей рабочей температуры, и единственная потребность в тепле может быть связана с потерями с твердой поверхности стенок и / или потерями с поверхности жидкости.
Этот модуль будет иметь дело с расчетами, которые определяют энергетические потребности резервуаров: следующие два модуля (2.10 и 2.11) будут иметь дело с тем, как эта энергия может быть предоставлена.
При определении потребности в тепле резервуара или ванны с технологической жидкостью общая потребность в тепле может состоять из некоторых или всех из ряда ключевых компонентов:
- Тепло, необходимое для повышения температуры технологической жидкости от холодной до рабочей.
- Тепло, необходимое для повышения температуры материала сосуда от холода до рабочей температуры.
- Тепло, потерянное твердой поверхностью судна в атмосферу.
- Тепло, теряющееся от поверхности жидкости в атмосфере.
- Тепло, поглощаемое холодными предметами, погруженными в технологическую жидкость.
Однако во многих приложениях только некоторые из вышеперечисленных компонентов будут иметь значение. Например, в случае полностью закрытого и хорошо изолированного резервуара для хранения нефти общая потребность в тепле может быть почти полностью покрыта теплом, необходимым для повышения температуры жидкости.
Пункты 1 и 2, энергия, необходимая для повышения температуры жидкости и материала резервуара, и пункт 5, тепло, поглощаемое любыми холодными предметами, погруженными в технологическую жидкость, могут быть найдены с помощью уравнения 2.6.1. Как правило, данные можно точно определить, и, следовательно, расчет потребности в тепле является простым и точным.
Пункты 3 и 4, тепловые потери от резервуара и поверхностей жидкости можно определить с помощью уравнения 2.5.3.
Однако расчеты теплопотерь намного сложнее, и обычно приходится полагаться на эмпирические данные или таблицы, основанные на нескольких предположениях. Следовательно, расчет теплопотерь менее точен.
Теплопотери от твердой поверхности корпуса в атмосферу
Тепло передается только при разнице температур между поверхностью и окружающим воздухом.
На рис. 2.9.1 представлены некоторые типичные общие коэффициенты теплопередачи для теплопередачи от стальных плоских поверхностей без покрытия к окружающему воздуху.Если дно резервуара не подвергается воздействию окружающего воздуха, а расположено ровно на земле, этот компонент тепловых потерь обычно считается незначительным и его можно безопасно игнорировать.
- Для 25 мм изоляции значение U следует умножить на коэффициент 0,2
- Для 50 мм изоляции значение U следует умножить на коэффициент 0,1
Общие коэффициенты теплопередачи, представленные на рисунке 2.9.1, относятся только к «неподвижному воздуху».
В таблице 2.9.2 показаны коэффициенты умножения, которые необходимо применить к этим значениям, если учитывается скорость воздуха. Однако, если поверхность хорошо изолирована, скорость воздуха вряд ли увеличит теплопотери более чем на 10% даже в условиях открытого воздействия.
Скорость менее 1 м / с можно рассматривать как защищенные условия, в то время как скорость 5 м / с можно рассматривать как легкий ветерок (около 3 по шкале Бофорта), свежий ветер 10 м / с (5 баллов по шкале Бофорта) и Умеренный шторм 16 м / с (балл 7 по шкале Бофорта).
Для резервуаров для хранения нефти могут использоваться общие коэффициенты теплопередачи, указанные в таблице 2.9.3.
Резервуары для воды: потери тепла с поверхности воды в атмосферу
Рисунок 2.9.2 связывает потери тепла с поверхности воды со скоростью воздуха и температурой поверхности. В этой таблице считается, что «неподвижный» воздух имеет скорость 1 м / с, резервуары в защищенных местах на открытом воздухе учитывают скорость около 4 м / с, в то время как резервуары в открытых местах на открытом воздухе считаются со скоростью около 8 м / с.
Эта диаграмма показывает потери тепла в Вт / м², а не в единицах общего коэффициента теплопередачи в Вт / м² ° C. Это означает, что это значение необходимо умножить на площадь поверхности, чтобы получить скорость теплопередачи, поскольку разница температур воды и воздуха уже учтена.
Потери тепла с поверхности воды, как показано на Рисунке 2.9.2, не зависят существенно от влажности воздуха. Полный диапазон значений влажности, которые могут встретиться на практике, покрывается толщиной кривой.Однако график учитывает тепловые потери при температуре воздуха 15,6 ° C и влажности воздуха 55%. Различные условия могут быть рассчитаны в Центре инженерной поддержки на веб-сайте Spirax Sarco.
Чтобы определить теплопотери по графику, температуру поверхности воды необходимо выбрать по верхней шкале. Затем следует провести линию вертикально вниз к (жирной) кривой потерь тепла.
Для внутренних резервуаров линию следует проецировать горизонтально от пересечения до левой шкалы.
Для внешних резервуаров горизонтальную линию следует проецировать влево или вправо до пересечения с требуемым местом, защищенным или открытым. Проекция вертикально вниз покажет потери тепла на нижней шкале.
В большинстве случаев потери тепла с поверхности жидкости являются наиболее значительным элементом потерь тепла. Там, где это целесообразно, потери тепла можно ограничить, накрыв поверхность жидкости слоем полистирольных сфер, которые создают изолирующий «покров».Любое решение по снижению тепловых потерь становится еще более важным, когда резервуары расположены снаружи в открытых положениях, как показано на графике на Рисунке 2.9.2
% PDF-1.4 % 465 0 объект > endobj xref 465 81 0000000016 00000 н. 0000001971 00000 н. 0000002180 00000 н. 0000002236 00000 н. 0000003393 00000 н. 0000004031 00000 н. 0000004072 00000 н. 0000004143 00000 п. 0000004195 00000 н. 0000004247 00000 н. 0000018222 00000 п. 0000018452 00000 п. 0000020093 00000 п. 0000021268 00000 п. 0000021298 00000 п. 0000021350 00000 п. 0000021402 00000 п. 0000021454 00000 п. 0000021476 00000 п. 0000036745 00000 п. 0000037135 00000 п. 0000038371 00000 п. 0000038617 00000 п. 0000039852 00000 п. 0000040228 00000 п. 0000040468 00000 п. 0000054787 00000 п. 0000055048 00000 п. 0000055280 00000 п. 0000056033 00000 п. 0000056055 00000 п. 0000056810 00000 п. 0000056832 00000 п. 0000072672 00000 п. 0000073909 00000 п. 0000074039 00000 п. 0000074383 00000 п. 0000074637 00000 п. 0000075414 00000 п. 0000075436 00000 п. 0000076201 00000 п. 0000076223 00000 п. 0000076536 00000 п. 0000077089 00000 п. 0000077406 00000 п. 0000078159 00000 п. 0000078181 00000 п. 0000078887 00000 п. 0000078909 00000 п. 0000079449 00000 п. 0000079471 00000 п. 0000080406 00000 п. 0000080505 00000 п. 0000080528 00000 п. 0000080735 00000 п. 0000082528 00000 п. 0000082604 00000 п. 0000082712 00000 п. 0000084083 00000 п. 0000084155 00000 п. 0000085516 00000 п. 0000086887 00000 п. 0000086994 00000 п. 0000088365 00000 п. 0000091043 00000 п. 0000091114 00000 п. 0000091136 00000 п. 0000091305 00000 п. 0000091411 00000 п. 0000091482 00000 п. 0000091656 00000 п. 0000092593 00000 п. 0000093310 00000 п. 0000093389 00000 п. 0000122755 00000 н. 0000125790 00000 н. 0000144565 00000 н. 0000161210 00000 н. 0000177614 00000 н. 0000002371 00000 н. 0000003371 00000 н. трейлер ] >> startxref 0 %% EOF 466 0 объект > >> endobj 467 0 объект > endobj 468 0 объект > endobj 544 0 объект > поток HT] lV> vbNYIZ,]
tAvu! XA4 & F5IHu} ‘v $ te} |
Blanc Doc
% PDF-1.5 % 1 0 obj > endobj 2 0 obj > поток
TN❽I PL% Fh | v} | ubU ..? 5 \ ~ z ޖ U] tUSz]> | qNx «B} Bx! / AyiJy6 / _
Расчет энергопотребления транспортного средства TOol — VECTO
Перейти к основному содержанию Главная — Европейская комиссия Englishen Искать на этом сайте Вы находитесь здесь:- Европейская комиссия
- Энергия, изменение климата, окружающая среда
- Действия по борьбе с изменением климата
- Действия ЕС
- Транспортные выбросы
- Автомобильный транспорт: сокращение выбросов CO2 от транспортных средств
Climate Action
МенюРаздел просмотра: значок
Действия ЕС
- Действия по борьбе с изменением климата и Зеленая сделка ЕС
- Климатические стратегии и цели
- Климатический и энергетический пакет 2020
- Рамки климата и энергетики до 2030 года
- Долгосрочная стратегия на 2050 год
- Прогресс
- Киотский протокол 1-й период обязательств (2008–12)
- Киотский протокол, 2-й период обязательств (2013-2020 гг.)
- Мониторинг выбросов и отчетность
- Постановление об управлении
- Экономический анализ
- Модели
- Система торговли выбросами (EU ETS)
- Резерв стабильности рынка
- Ревизия фазы 4
- Ограничение выбросов
- Размещение надбавок с аукциона
- Использование международных кредитов
- Бесплатное распределение надбавок
- Промышленные установки
- Электрогенераторы
- Авиация
- Утечка углерода
- Мониторинг, отчетность и проверка
- Эксплуатанты воздушных судов
- Реестр Союза
- Контроль рынка
- Международный углеродный рынок
- EU ETS 2005-2012
- Национальные планы распределения
- ETS Summer University
- Совместное использование усилий: цели государств-членов
- 2021-30 гг .: Обзор постановления
- 2013-20: Годовое распределение выбросов и гибкость
- Реализация
- Инновационный фонд
- Улавливание и геологическое хранение углерода
- Правовая база
- Реализация директивы CCS
- NER 300
- Улавливание и геологическое хранение углерода
- Транспорт
- Автомобильный транспорт
- Легковые автомобили и фургоны после 2020 года
- Автомобили — до 2020 г.
- Микроавтобусы — до 2020 года
- Тяжелые автомобили
- VECTO
- Маркировка автомобилей
- Качество топлива
- Доставка
- Авиация
- Автомобильный транспорт
- Защита озонового слоя
- Регулирование озона
- Бизнес-портал
- Фторированные парниковые газы
- Законодательство
- Квоты и отчетность
- Альтернативы, благоприятные для климата
- Леса и сельское хозяйство
- Вырубка лесов и REDD +
- ЗИЗЛХ в ЕС
- Адаптация к изменению климата
- Как это повлияет на нас?
- Затронутые отрасли
- Окружающая среда
- Социальные
- Территориальный
- Что делает ЕС?
- Актуализация
- Пробелы в знаниях
- Как это повлияет на нас?
Расчет расхода материалов — Управление цепочкой поставок | Динамика 365
- 3 минуты на чтение
В этой статье
В этой статье представлена информация о различных параметрах, связанных с расчетом расхода материалов.
Следующие параметры, относящиеся к расчету расхода материала, доступны на вкладках Настройка и Шаг потребления на экспресс-вкладке Детали строки на странице Спецификация материалов .
Переменное и постоянное потребление
В поле Расход можно выбрать, следует ли рассчитывать потребление как постоянное количество или как переменное количество. Выберите Константа , если для производства требуется фиксированное количество или объем, независимо от производимого количества.Выберите Переменная , которая является настройкой по умолчанию, если необходимое количество материала в готовой продукции пропорционально количеству производимой готовой продукции.
Расчет потребления по формуле
В поле Формула можно настроить различные формулы для расчета расхода материала. Если вы используете значение по умолчанию Standard , потребление не рассчитывается по формуле. Следующие формулы работают вместе с полями Высота , Ширина , Глубина , Плотность и Константа :
- Высота * Постоянная
- Высота * Ширина * Постоянная
- Высота * Ширина * Глубина * Постоянная
- (Высота * Ширина * Глубина / Плотность) * Постоянная
Округление и кратное
Вместе поля Округление в большую сторону и Множители позволяют округлять значение расхода материала.Например, можно округлить значение в соответствии с единицей обработки, в которой сырье собрано для производства. В поле Округление вверх доступны следующие параметры: Количество , Измерение и Расход .
Кол-во
При выборе Количество в качестве механизма округления количество должно быть кратным указанному количеству. Например, если требуются целые числа, выберите 1 в поле Multiples .Затем числа округляются до количества, кратного 1.
Измерение
Обычно вы выбираете Размер в качестве механизма округления, когда сырье поступает в определенных размерах. Например, для готового изделия требуется кусок 2-х метровой металлической трубы, а длина металлической трубы составляет 4,5 метра. В этом случае можно использовать механизм округления Измерение для вычисления количества металлических трубок, необходимых для производства определенного количества частей готового товара.В этом примере поле Формула установлено на Высота * Константа . В поле Высота установлено значение 2 , чтобы указать длину трубы, которая требуется для готового товара. В поле Multiple установлено значение 4,5 , чтобы указать, что труба взята длиной 4,5 метра. Вот расчет:
- Количество кратных, которое требуется для 10 штук готового продукта: 10 ÷ 2 = 5 штук
- Общий расход: 4.5 × 5 = 22,5 метра металлической трубки
Предполагается, что 0,5 м трубы выбрасывается на каждые пять израсходованных частей трубы.
Расход
Как правило, вы выбираете Расход в качестве механизма округления, когда сырье должно быть собрано в целых количествах определенной единицы обработки продукта. Например, на изготовление одного предмета готового изделия уходит 2 литра краски, а краска собирается в 25-литровых банках. В этом случае можно использовать механизм округления Расход для округления потребления до целого числа 25-литровых банок.Вот расчет количества краски, которое потребуется, если необходимо произвести 180 штук готовой продукции:
- Требуемая краска, исключая отходы: 180 × 2 = 360 квартов
- Количество банок: 360 ÷ 25 = 14,4, округляем до 15
- Необходимая краска, включая отходы: 15 × 25 = 375 квартов
Шаг потребления
Шаговое потребление используется для расчета постоянного потребления в интервалах количества.