Испытание газопровода: Испытания газопроводов
Испытания газопроводов
Законченные строительством или реконструкцией наружные и внутренние газопроводы следует испытывать на герметичность воздухом. Для испытания газопровод в соответствии с проектом производства работ следует разделить на отдельные участки, ограниченные заглушками или закрытые линейной арматурой и запорными устройствами перед газоиспользующим оборудованием, с учетом допускаемого перепада давления для данного типа арматуры (устройства).
Если арматура и приборы не рассчитаны на испытательное давление, то вместо них на период испытаний следует устанавливать катушки, заглушки.
Газопроводы жилых, общественных, бытовых, административных, производственных зданий и котельных следует испытывать на участке от отключающего устройства на вводе в здание до кранов газоиспользующего оборудования. Испытания газопроводов должна производить строительно-монтажная организация в присутствии представителя эксплуатационной организации. Результаты испытаний следует оформлять записью в строительном паспорте.
Перед испытанием на герметичность внутренняя полость газопровода должна быть очищена в соответствии с проектом производства работ. Очистку полости внутренних газопроводов и газопроводов ГРП (ГРУ) следует производить перед их монтажом продувкой воздухом.
Для проведения испытаний газопроводов следует применять манометры класса точности 0,15. Допускается применение манометров класса точности 0,40, а также класса точности 0,6. При испытательном давлении до 0,01 МПа следует применять К-образные жидкостные манометры (с водяным заполнением).
Испытания подземных газопроводов следует производить после их монтажа в траншее и присыпки выше верхней образующей трубы не менее чем на 0,2 м или после полной засыпки траншеи.
Сварные стыки стальных газопроводов должны быть изолированы.
До начала испытаний на герметичность газопроводы следует выдержать под испытательным давлением в течение времени, необходимого для выравнивания температуры воздуха в газопроводе с температурой фунта.
При испытании надземных и внутренних газопроводов следует соблюдать меры безопасности, предусмотренные проектом производства работ.
Испытания газопроводов на герметичность проводят путем подачи в газопровод сжатого воздуха и создания в газопроводе испытательного давления. Значения испытательного давления и время выдержки под давлением стальных подземных газопроводов принимают в соответствии с таблицей ниже.
Испытательное давление стальных подземных газопроводов
Рабочее давление газа, МПа | Вид изоляционного покрытия | Испытательное давление, МПа | Продолжительность испытаний, ч |
До 0,005 | Независимо от вида изоляционного покрытия | 0,6 | 24 |
Свыше 0,005 до 0,3 | Битумная мастика, полимерная липкая лента | 0,6 | 24 |
Экструдированный полиэтилен, стекло- эмаль | 1,5 | 24 | |
Свыше 0,3 до 0,6 | Битумная мастика, полимерная липкая лента | 0,75 | 24 |
Экструдированный полиэтилен, стекло- эмаль | 1,5 | 24 | |
Свыше 0,6 до 1,2 | Независимо от вида изоляционного покрытия | 1,5 | 24 |
Свыше 0,6 до 1,6 для СУГ | 2,0 | ||
Газовые вводы до 0,005 при их раздельном строительстве с распределительным газопроводом | Тоже | 0,3 | 2 |
Нормы испытаний полиэтиленовых газопроводов, стальных надземных газопроводов, газопроводов и оборудования ГРП, а также внутренних газопроводов следует принимать по таблице ниже. Температура наружного воздуха в период испытания полиэтиленовых газопроводов должна быть не ниже минус 15 °С.
Нормы испытаний полиэтиленовых газопроводов, стальных подземных газопроводов, газопроводов и оборудования ГРП, а также внутренних газопроводов зданий
Рабочее давление газа, МПа | Испытательное давление, МПа | П родолжительность испытаний, ч |
Полиэтиленовые газопроводы | ||
До 0,005 | 0,3 | 24 |
Свыше 0,005 до 0,3 | 0,6 | |
Свыше 0,3 до 0,6 | 0,75 | |
Надземные газопроводы | ||
До 0,005 | 0,3 | 1 |
Свыше 0,005 до 0,3 | 0,45 | |
Свыше 0,3 до 0,6 | 0,75 | |
Свыше 0,6 до 1,2 | 1,5 | |
Свыше 1,2 до 1,6 (для СУГ) | 2,0 | |
Газопроводы и оборудование ГРП | ||
До 0,005 | 0,3 | 1 |
Свыше 0,005 до 0,3 | 0,45 | |
Свыше 0,3 до 0,6 | 0,75 | |
Свыше 0,6 до 1,2 | 1,5 | |
Газопроводы внутри зданий, газопроводы и оборудование ГРУ | ||
Газопроводы жилых зданий давлением до 0,003 | 0,01 | 5 мин |
Газопроводы котельных, общественных, административных, бытовых и производственных зданий давлением | ||
До 0,005 | 0,01 | 1 |
Свыше 0,005 до 0,1 | 0,1 | |
Свыше 0,1 до 0,3 | 1,25 от рабочего, но не более 0,3 | |
Свыше 0,3 до 0,6 | 1,25 от рабочего, но не более 0,6 | |
Свыше 0,6 до 1,2 | 1,25 от рабочего, но не более 1,2 | |
Свыше 1,2 до 1,6 (для СУГ) | 1,25 от рабочего, но не более 1,6 |
Подземные газопроводы, прокладываемые в футлярах на участках переходов через искусственные и естественные преграды, следует испытывать в три стадии:
- после сварки перехода до укладки на место;
- после укладки и полной засыпки перехода;
- вместе с основным газопроводом.
Разрешается не производить испытания после полного монтажа и засыпки перехода по согласованию с эксплуатационной организацией. Испытания участков переходов разрешается производить в одну стадию вместе с основным газопроводом в случаях:
- отсутствия сварных соединений в пределах перехода;
- использования метода наклонно-направленного бурения;
- использования в пределах перехода для сварки полиэтиленовых труб деталей с закладными нагревателями или сварочного оборудования с высокой степенью автоматизации.
Результаты испытания на герметичность следует считать положительными, если за период испытания давление в газопроводе не меняется, т.е. нет видимого падения давления по манометру класса точности 0,6, а по манометрам класса точности 0,15 и 0,4, а также по жидкостному манометру падение давления фиксируется в пределах одного деления шкалы. При завершении испытаний газопровода давление следует снизить до атмосферного, установить автоматику, арматуру, оборудование, контрольно-измерительные приборы и выдержать газопровод в течение 10 мин под рабочим давлением. Герметичность разъемных соединений следует проверить мыльной эмульсией.
Дефекты, обнаруженные в процессе испытаний газопроводов, следует устранять только после снижения давления в газопроводе до атмосферного. После устранения дефектов, обнаруженных в результате испытаний газопровода на герметичность, следует повторно произвести эти испытания.
Стыки газопроводов, сваренные после испытаний, должны быть проверены физическим методом контроля. Резервуары сжиженных углеводородных газов вместе с обвязкой по жидкой и паровой фазам следует испытывать в соответствии с требованиями правил устройства и безопасной эксплуатации сосудов, работающих под давлением.
Испытания газопроводов и оборудования ГРП и ГРУ производят по нормам испытаний на стороне входного давления газа или по частям:
- до регулятора давления — по нормам испытаний на стороне входного давления газа;
- после регулятора давления — по нормам испытаний на стороне выходного давления газа.
Испытания газопроводов паровой фазы СУГ производят по нормам, предусмотренным для испытаний газопроводов природного газа. Подземные газопроводы до начала испытаний после их заполнения воздухом рекомендуется выдерживать под испытательным давлением в течение времени, необходимого для выравнивания температуры воздуха в газопроводе с температурой фунта, но не менее 24 ч.
Надземные и внутренние газопроводы, газопроводы и оборудование ГРП и ГРУ до начала испытаний после их заполнения воздухом рекомендуется выдерживать под испытательным давлением в течение времени, необходимого для выравнивания температуры воздуха внутри газопроводов с температурой окружающего воздуха, но не менее 1 ч.
Газопроводы жилых, общественных и бытовых непроизводственного назначения, административных зданий испытывают на участке от отключающего устройства на вводе в здание до кранов газовых приборов и оборудования. При установке дополнительных газовых приборов испытание новых участков газопроводов к этим приборам при их длине до 5 м допускается производить газом (рабочим давлением) с проверкой всех соединений газоиндикаторами или мыльной эмульсией.
Внутренние газопроводы котельных, общественных и бытовых зданий производственного назначения, производственных зданий следует испытывать на участке от отключающего устройства на вводе до отключающих устройств у газовых горелок.
Газопроводы обвязки резервуара СУГ при раздельном испытании их с резервуаром СУГ допускается испытывать в соответствии с требованиями СП 42-101-2003.
Герметичность арматуры, газопроводов и присоединительных рукавов индивидуальных баллонных установок СУГ, а также присоединительные рукава газоиспользующего оборудования и контрольно-измерительных приборов разрешается проверять рабочим давлением газа с применением газоиндикатора или мыльной эмульсией.
Манометры класса точности 0,15 рекомендуется применять для проведения испытаний газопроводов всех диаметров и давлений
Испытание газопроводов / КонсультантПлюс
Испытание газопроводов
1742. Межцеховые и цеховые газопроводы должны подвергаться испытанию раздельно.
Наружные цеховые газопроводы, проложенные на отдельно стоящих опорах, по стенам снаружи зданий и крышам, должны испытываться отдельно от внутрицеховых газопроводов.
1743. Величина пробного давления на прочность Pпр (гидравлическим или пневматическим способом) устанавливается проектом и должна составлять:
,
но не менее 0,2 МПа,
где P — рабочее давление трубопровода, МПа;
— допускаемое напряжение для материала трубопровода при 20 град. C;
— допускаемое напряжение для материала трубопровода при максимально положительной расчетной температуре.
Все межцеховые газопроводы низкого давления подлежат испытаниям только на плотность.
Испытания на плотность газопроводов с рабочим давлением P <= 0,015 МПа должны производиться пробным давлением Pпр = 0,02 МПа, а при P от 0,015 МПа до 0,1 МПа должны производиться Pпр = 1,25P, но не более 0,1 МПа.
1744. Испытательное давление в трубопроводе выдерживают в течение 10 мин. (испытание на прочность), после чего снижают до рабочего давления, при котором производят тщательный осмотр сварных швов (испытание на плотность). По окончании осмотра давление вновь повышают до испытательного и выдерживают еще 5 минут, после чего снова снижают давление до рабочего и вторично осматривают трубопровод.
Продолжительность испытания на плотность определяется временем осмотра газопровода и проверки герметичности разъемных соединений.
1745. Пневматическое испытание должно проводиться воздухом или инертным газом (азотом) и только в светлое время суток.
1746. Пневматическое испытание газопроводов должно проводиться по инструкции, утвержденной главным инженером предприятия, предусматривающей необходимые меры безопасности.
1747. На время проведения пневматических испытаний на прочность как внутри помещений, так и снаружи должна устанавливаться охраняемая зона. Границы охраняемой зоны должны отмечаться флажками. Минимальное расстояние от испытываемого газопровода до границ зоны должно составлять не менее 25 м, для газопроводов больших диаметров и газопроводов токсичных газов, расположенных вне помещений, — не менее 50 м.
Для газопроводов, расположенных внутри помещений, охраняемая зона должна быть установлена по согласованию с начальником соответствующего цеха (объекта), но не менее 10 м.
1748. Во время подъема давления в газопроводе и при достижении в нем испытательного давления на прочность пребывание людей в охраняемой зоне запрещается.
1749. Если пневматическому испытанию на плотность предшествовало гидравлическое испытание на прочность, установление охраняемой зоны не производится. Газопровод в этом случае следует продуть воздухом до полного удаления оставшейся воды.
1750. Окончательный осмотр газопровода разрешается лишь после того, как испытательное давление будет снижено до рабочего.
Устранение выявленных дефектов должно производиться после снижения давления в газопроводах до атмосферного.
1751. Результаты испытания на прочность и плотность признаются удовлетворительными, если во время испытания не произошло разрывов, видимых деформаций, падения давления по манометру, в основном металле, сварных швах, корпусах арматуры, разъемных соединениях и во всех врезках не обнаружено пропусков воздуха, а при гидроиспытании не обнаружены течи и запотевания.
Открыть полный текст документа
Испытание газопровода
Категория: Газоснабжение
Испытание газопровода
Газопроводы низкого давления в жилых и общественных зданиях полагается испытывать воздухом:
-на прочность —давлением 1 кгс/см2 для выявления дефектов на испытываемом участке. При испытании бытовые приборы и счетчики отключают; – на плотность — давлением 400 мм вод. ст. с установленными счетчиками и бытовыми приборами. В том случае, если нет счетчиков, а также если система снабжена сжиженным газом, испытание производят давлением 500 мм вод. ст.
Рис. 1. Малогабаритный компрессор КМ-70: 1 — электродвигатель, 2 — кривошипно-шатунный механизм, 3 — поршень,4 — цилиндр, 5 — фильтр,6 — гибкий шланг, 7 — канал, 8 — манометр, 9 — выключатель, 10 — вентилятор
Газопроводы считаются выдержавшими испытание на плотность, если падение давления в них в течение 5 мин не превышает 20 мм вод. ст.
Нормы испытания внутренних газопроводов среднего и высокого давления приведены в табл. 1.
Таблица 1
Нормы испытания внутренних газопроводов
После сборки газопровода и установки газовых приборов проверяют его герметичность. Внутреннюю сеть испытывают давлением воздуха, которое создается при помощи ручного воздушного насоса, баллона со сжатым воздухом или компрессора КМ-70.
Принцип работы малогабаритного компрессора КМ-70 (рис. 280) заключается в следующем. От электродвигателя через кривошипно-шатунный механизм движение передается поршню, находящемуся в цилиндре. Воздух забирается в цилиндр в средней его части через шесть радиальных отверстий, проходя предварительно воздушный фильтр.
От электродвигателя движение передается вентилятору, предназначенному для охлаждения компрессора. Из цилиндра воздух под давлением поступает через канал в гибкий шланг, подключенный к испытываемой системе. К каналу присоединен манометр для контроля за рабочим давлением.
Управление работой электродвигателя производится при помощи пакетного выключателя.
При падении давления места соединений смачивают мыльной водой. В местах утечки воздуха появляются мыльные пузыри.
Если в резьбовом соединении обнаружены неплотности, его подтягивают или перевертывают вновь. Трубы с трещинами и фасонные части со свищами заменяют новыми или трещины и свищи заваривают газовой или электрической сваркой. Заделка, замазка или подчеканка трещин, свищей и раковин запрещаются.
Вводы газопроводов испытывают отдельно от внутренней сети газопровода.
Дворовый газопровод низкого давления испытывают на прочность сжатым воздухом давлением 3 кгс/см2 до засыпки его землей. Соединения на плотность проверяют, смачивая их мыльной водой.
После засыпки траншей землей газопровод вторично в течение часа испытывают на плотность при давлении 1 кгс/смг. Давление не должно упасть сверх допустимого.
Газоснабжение — Испытание газопровода
Правила испытания газопроводов на прочность и плотность
ПРАВИЛА ИСПЫТАНИЯ ГАЗОПРОВОДОВ НА ПРОЧНОСТЬ И ПЛОТНОСТЬ [c.
Нормы давлений при испытаниях на прочность и плотность подземных, надземных и внутренних газопроводов и газопроводов ГРП (ГРУ), а также расчетные формулы допустимых потерь давления при испытаниях на плотность указаны в прил. 24 настоящих Правил. [c.200]
После проверки и последующей сборки газопровод должен быть подвергнут испытанию на прочность и плотность в соответствии с главой 7 настоящих Правил. [c.415]
Все газопроводы (за исключением указанных в п. 7.38), на которые распространяются настоящие Правила, в том числе все вакуумные трубопроводы, помимо обычных обязательных испытаний на прочность и плотность, должны подвергаться дополнительному испытанию на плотность с определением падения давления за время испытания. [c.408]
Как было указано выше, на газопроводах, как правило, следует устанавливать арматуру, специально предназначенную для работы в газовой среде. Однако в некоторых случаях из-за ограниченности типоразмеров и недостаточного выпуска специальной газовой арматуры приходится использовать арматуру, предназначенную для других сред. При этом арматуру следует подвергнуть в центральных заготовительных мастерских ревизии и испытаниям на прочность, плотность и герметичность затвора в соответствии с требованиями п. 4.26—4.28 СНиП П1-29—76. [c.148]
Испытание трубопроводов на прочность и плотность производят одновременно гидравлическим или пневматическим способом. Как правило, трубопроводы испытывают гидравлическим способом. Пневматическое испытание на прочность и плотность применяют только в следующих случаях для газопроводов с условным проходом от 250 мм и более, если строительные конструкции и газопровод не рассчитаны на заполнение его водой при температуре окружающего воздуха ниже 0° С когда проведение гидравлического испытания недопустимо или невозможно (наприг ер, по технологическим требованиям). [c.232]
Все газопроводы, на которые распространяется действие настоящих Правил, после окончания монтажа подвергаются наружному осмотру и испытанию на прочность и плотность, за исключением газопроводов низкого давления, работающих под давлением от 0,95 кГ1см (абс. ) до 1 кГ/см (изб.), которые подлежат только испытанию на плотность в соответствии с п. 7.38. [c.403]
После ознакомления с документацией и проверки ее члены комиссии осматривают все газопроводы, сооружения и арматуру. К моменту приема газопроводы должны быть испытаны на прочность, плотность и засыпаны, а комиссия имеет право проверить любые участки газопроводов путем вырезки стыков, повторного испытания и т. д. Прием нового объекта оформляется специальным актом, он одновременно является разрешением на ввод в эксплуатацию газопровода. [c.79]
Правило, трубопроводы испытывают гидравлическим способом.Пневматическое испытание на прочность и плотность применяют только в следующих случаях для газопроводов с Dy от 2-50 мм и более, если строительные конструкции и газопровод не рассчитаны на заполнение его водой, при температуре окружающего воздуха ниже 0°С, когда проведение гидравлического испытания недопустимо или невозможно по технологическим требованиям. [c.203]
Все участки газопровода, подвергавшиеся в процессе выборочной ревизии разборке, резке и сварке, после сборки должны быть испытаны на прочность и плотность в соответствии с главой 7 настоящих Правил, а результаты испытаний должны быть зафиксированы в паспорте газопровода (см. приложение 14). [c.414]
Испытание на прочность и плотность газопроводов, работающих под давлением Ру Ю МПа, может быть гидравлическим или пневматическим. Как правило, эти газопроводы испытывают гидравлическим методом. Замена гидравлического испытания газопроводов, работающих под давленирм ниже 10 МПа, пневматическим испытанием допускается в следующих случаях если несущие строительные конструкции не рассчитаны на заполнение этих газопроводов водой при температуре окружающего воздуха ниже О °С если применение воды недопустимо по техническим причинам. Испытания на прочность и плотность газопроводов, работающих под давлением выше 10 МПа, должно производиться только гидравлическим методом. [c.243]
Газопроводы на прочность и плотность испытываются воздухом, за исключением испытания на прочность надземных и внутрицеховых газопроводов с давлением выше 3 кПсм , которое, как правило, производится водой и лишь, как исключение, зимой допускается воздухом. Газопроводы и регуляторные установки испытываются после монтажа отключающей арматуры, регуляторов, сборников конденсата и другого оборудования, включая контрольно-измерительные приборы. Все места соединений газопровода должны быть открыты для осмотра и очищены от грязи, ржавчины, изоляции и т. п. Газопроводы и регуляторные станции при испытании на прочность должны находиться под давлением не менее 1 ч, после чего давление снижается до величины, необходимой для испытания на плотность. Во время испытания производится осмотр газопроводов и их оборудования с проверкой плотности сварных и фланцевых соединений мыльным раствором, во время которого давление в газопроводе необходимо поддерживать постоянным. Если при испытании будут выявлены дефектные места, давление воздуха в газопроводе снижают до атмосферного, после чего замеченные дефекты устраняют и газопровод снова подвергают испытанию. Все подземные и надземные (нарунчныо) газопроводы, за исключением газопроводов низкого давления диаметром до 150 мм на вводах к зданиям, цехам, предприятиям и т. д., подвергаются испытанию на давление, приведенное в табл. 1У-1. [c.72]
«Голубой поток»
Значение
Газопровод «Голубой поток» предназначен для поставок российского природного газа в Турцию через акваторию Черного моря, минуя третьи страны. «Голубой поток» дополняет газотранспортный коридор из России в Турцию, который проходит через территорию Украины, Молдавии, Румынии и Болгарии.
«Голубой поток» существенно повысил надежность поставок газа в Турцию, а также способствует развитию газового рынка и газовой инфраструктуры этой страны.
Уникальность и технические особенности
«Голубой поток» является уникальным газотранспортным сооружением, не имеющим аналогов в мире. Строительство этого газопровода открыло новую страницу в истории развития современных газотранспортных технологий.
Общая протяженность газопровода «Голубой поток» составляет 1213 км.
Учитывая, что более 60 км газопровода, расположенного на российском сухопутном участке, проходит по горной местности, а глубина залегания трубы на морской части достигает 2150 м в условиях агрессивной сероводородной среды, для повышения надежности газопровода при его строительстве применялись специальные технические решения. К ним относятся, к примеру, применение труб из высококачественной коррозионностойкой стали с внутренним и внешним полимерным покрытием; испытание газопровода методом стресс-теста; использование интеллектуальных вставок на горном и морском участках и др.
Впервые в практике российской нефтегазовой отрасли на горном участке сухопутной части газопровода были сооружены протяженные тоннели под хребтами Кобыла и Безымянный. Общая длина тоннелей составила 3260 м.
Параллельно со строительством газопровода осуществлялось проведение природоохранных мероприятий. К ним относится рекультивация земель по всей трассе строительства газопровода, сохранение более 4 гектаров реликтового леса при прохождении тоннельным методом хребтов Кобыла и Безымянный.
Сотрудничество
Основным партнером «Газпрома» при строительстве «Голубого потока» выступала итальянская компания Eni, которая имеет большой опыт строительства морских газопроводов и располагает крупнейшим в мире трубоукладочным флотом.
История
15 декабря 1997 года между Россией и Турцией было подписано межправительственное соглашение. В рамках этого соглашения «Газпром» заключил коммерческий контракт с турецкой фирмой Botas на поставку 365 млрд кубометров газа в Турцию по газопроводу «Голубой поток» в течение 25 лет.
В феврале 1999 года между «Газпромом» и итальянской компанией Eni был подписан Меморандум о взаимопонимании по совместному участию в реализации проекта «Голубой поток».
16 ноября 1999 года ОАО «Газпром» (с 17 июля 2015 года — ПАО «Газпром») и Eni зарегистрировали в Нидерландах на паритетных началах российско-итальянскую компанию специального назначения Blue Stream Pipeline Company B. V. Сейчас эта компания выступает владельцем морского участка газопровода, включая компрессорную станцию «Береговая». Владельцем и оператором сухопутного участка газопровода является ПАО «Газпром».
Сооружение морского участка «Голубого потока» длиной 396 км началось в сентябре 2001 года и полностью завершилось в мае 2002 года.
30 декабря 2002 года газопровод «Голубой поток» был сдан в эксплуатацию. Промышленные поставки газа по газопроводу начались в феврале 2003 года.
Текущее состояние
Проектная мощность газопровода составляет 16 млрд куб. м газа в год.
Стоит отметить, что по запросам турецкой стороны в отдельные периоды суточные объемы, поставляемые по газопроводу «Голубой поток», соответствуют уровню его проектной мощности. Это связано с тем, что Турция сталкивается с невыполнением обязательств по поставкам со стороны Ирана, и «Газпром», идя навстречу турецким коллегам, компенсирует эти недопоставки.
«Газпром» также в состоянии покрывать пиковый рост спроса в Турции, связанный с регулярно наблюдающимися там холодными температурами.
Технология проведения пневматических испытаний газопровода
Please use this identifier to cite or link to this item: http://earchive.
tpu.ru/handle/11683/55105
Title: | Технология проведения пневматических испытаний газопровода |
Authors: | Насекин, Евгений Игоревич |
metadata.dc.contributor.advisor: | Брусник, Олег Владимирович |
Keywords: | природные газы; пневматические испытания; газоперекачивающие агрегаты; компрессорные агрегаты; внешние нагрузки; natural gas; pneumatic tests; gas pumping unit; compressor unit; external loads |
Issue Date: | 2019 |
Citation: | Насекин Е. И. Технология проведения пневматических испытаний газопровода : бакалаврская работа / Е. И. Насекин ; Национальный исследовательский Томский политехнический университет (ТПУ), Инженерная школа природных ресурсов (ИШПР), Отделение нефтегазового дела (ОНД) ; науч. рук. О. В. Брусник. — Томск, 2019. |
Abstract: | Объектом исследования является: подводный переход через реку Томь в близи н.![]() The object of the research is: underwater crossing across the river Tom in the vicinity of the settlement. Chernaya rechka Purpose of the work: Development of technical solutions for pneumatic tests. In the process of the study were carried out: an analytical review of the methods of pneumatic tests; factors affecting the steady and uninterrupted operation of gas pipelines are presented; the ranking of the main types of loads acting on pipelines. |
URI: | http://earchive.tpu.ru/handle/11683/55105 |
Appears in Collections: | Выпускные квалификационные работы (ВКР) |
Items in DSpace are protected by copyright, with all rights reserved, unless otherwise indicated.
Что такое пневматические испытания трубопроводов?
Пневматические испытания — один из двух способов проверки на прочность магистральных трубопроводов как новых, так и отремонтированных. Пневматические испытания проводят преимущественно с помощью воздуха, в отдельных случаях могут применяться иные инертные газы, в том числе те, на которых эксплуатируется трубопровод. Для испытаний воздухом выбирают компрессоры большой производительности и давления, для инертных газов используют азотные генераторы.
Пневматические испытания проводят под давлением от 40 до 150 бар в зависимости от типа трубопровода, его диаметра и среды. Магистральные трубопроводы диаметром 1420 мм, такие как «Сила Сибири» или «Северный поток», испытывают на герметичность до давления 152 бар, если иное не прописано в техническом задании. Результаты считаются удовлетворительными, если по показаниям манометра давление осталось на заданном уровне, а в сварных швах и фланцевых соединениях не было выявлено утечки, пропусков или потения.
Зачастую в местах проведения испытаний нет возможности подключения к электрическим сетям, поэтому компрессоры должны быть оборудованы автономным приводом – в большинстве случаев – дизельным.
Мобильность – еще один важный фактор при выборе оборудования для проведения пневматических испытаний, так как трубопроводы пролегают вдали от населенных пунктов и автотрасс. Пневматическое оборудование должно иметь необходимые транспортные и прицепные узлы для быстрой разгрузки и погрузки. Дополнительным преимуществом обладают модульные станции, которые в отличие от монолитных изделий, где компрессор и бустер представляют собой единый агрегат, возможно перевозить на более проходимых транспортных средствах.
Испытания магистральных трубопроводов проходят в тяжелых условиях окружающей среды. Экстремальные температуры, пыль, грязь – всё это крайне неблагоприятно сказывается на работе оборудования. Для многих марок компрессоров и дожимных бустеров такие условия не позволяют выполнить работы в срок, что может привести как к финансовым, так и имиджевым потерям. В данном случае надежность и простота используемого оборудования является залогом успеха. Рекомендуем выбирать компрессоры, дожимные бустеры и азотные генераторы, которые имеют базовую конструкцию, устойчивую к условиям Крайнего Севера (а не модный «зимний пакет»), и минимальное количество электроники (жидкокристаллические панели при температуре ниже -26°C перестают отображать параметры работы).

PHMSA: Связь с заинтересованными сторонами — Гидростатические испытания
Обзор:
Испытания под давлением используются операторами трубопроводов в качестве средства для определения целостности трубопровода сразу после строительства и перед вводом трубопровода в эксплуатацию, а также в течение срока эксплуатации трубопровода. Испытание под давлением после строительства подтверждает соответствие материалов трубопровода и методов строительства.
Правила об управлении целостностью требуют, чтобы операторы трубопроводов периодически проводили оценку целостности определенных трубопроводов.Испытания под давлением — один из приемлемых методов проведения этих оценок. Испытание под давлением для оценки целостности предназначено для определения того, имеет ли трубопровод для опасной жидкости или газа достаточную прочность — целостность — для предотвращения утечек или разрывов при нормальной работе и в аварийных условиях.
При испытании под давлением испытательная среда (газ или жидкость) внутри трубопровода с помощью насосов или компрессоров сжимается до давления, превышающего нормальное рабочее давление трубопровода.Это испытательное давление поддерживается в течение нескольких часов, чтобы убедиться в отсутствии утечек в трубопроводе. Любые признаки утечки требуют идентификации и устранения утечки. Затем в трубопроводе снова создается давление, и испытание повторяется. Эксплуатационная целостность сварных швов и самой трубы гарантируется, если испытание под давлением успешно завершено.
Гидростатические (непроточная вода) Испытания:
Испытания гидростатическим давлением обычно используются для испытаний трубопроводов для опасных жидкостей и трубопроводов природного газа с повышенным напряжением (> 30% SMYS) после строительства.
Гидростатические испытания также широко используются для периодической оценки целостности трубопроводов для транспортировки опасных жидкостей и газа (особенно, когда использование встроенных инструментов контроля невозможно). Углеводородные продукты вытесняются из тестируемой секции или секций и заменяются водой, чтобы минимизировать ущерб окружающей среде, который может возникнуть в результате утечек или разрывов. По ряду причин, включая перебои в работе и другие факторы воздействия на систему, гидростатические испытания могут быть неосуществимы для всех трубопроводов.Когда невозможны ни встроенные инструменты проверки, ни гидростатические испытания, операторы обычно проводят оценку целостности, используя процесс, называемый «прямой оценкой».
Если трубопровод успешно проходит испытание гидростатическим давлением, можно предположить, что в испытанной трубе нет опасных дефектов. Это особенно важно при работе с участками труб, которые были изготовлены до 1970 года с использованием низкочастотной контактной сварки сопротивлением (LFERW) и сварки внахлест (LW) продольного шва. Опыт показал, что в некоторых случаях некоторые из сварных на заводе швов на этих типах труб могут выходить из строя.
Требования и ограничения по гидростатическим испытаниям трубопроводов для опасных жидкостей указаны в 49 CFR 195, подраздел E; Требования и ограничения для трубопроводов природного газа указаны в 49 CFR 192, подраздел J.
. Гидростатическое испытание трубопроводов для опасных жидкостей требует испытания не менее 125% от максимального рабочего давления (MOP) в течение не менее 4 часов непрерывной работы и дополнительных 4 часов при давлении не менее 110% от MOP, если трубопровод не работает. видимый.Если есть опасения по поводу скрытых трещин, которые могут расти из-за явления, известного как «реверсирование давления», то можно провести испытание на «скачок» при максимальном давлении 139% от MOP в течение короткого периода (~ 1/2 часа). . Пиковое испытание служит для «расчистки» любых трещин, которые в противном случае могли бы расти во время снижения давления после гидростатического испытания или в результате циклов рабочего давления. Были проведены исследования, которые демонстрируют приемлемость трубопровода для продления срока службы после испытания гидростатическим давлением, если отсутствуют факторы, которые могут ускорить рост трещин, такие как коррозия или агрессивные циклы давления.
Испытание пневматическим давлением:
Пневматическое испытание трубопроводов под давлением относится к использованию воздуха или инертного газа (например, азота) в качестве испытательной среды вместо воды. Операторы трубопроводов редко используют пневматические испытания под давлением для систем, работающих при давлении выше 100 фунтов на кв. Дюйм, из соображений безопасности. Количество энергии, хранящейся в сжатом газе, намного превышает энергию, запасенную в сжатой жидкости. Если во время испытания пневматическим давлением под высоким давлением произойдет отказ трубопровода, внезапное выделение такого большого количества энергии может быть опасным для персонала, проводящего испытания.
Гидростатические испытания: где я могу узнать больше?
Дополнительную информацию о гидростатических испытаниях и трубопроводах LFERW можно найти в следующих ссылках:
- Джон Ф.
Кейфнер, Роль гидростатических испытаний в оценке целостности трубопроводов, Представлено на семинаре Northeast Pipeline Integrity Workshop, Олбани, штат Нью-Йорк, июнь 2001 г. www.kiefner.com
- Джон Ф. Кифнер, Работа с трубами с ВПВ и трубами оплавлением, сваренными низкочастотной сваркой, в соответствии с оценкой целостности, связанной с HCA , Представлено на ETCE 2002 ASME Engineering Technology Conference on Energy, Houston Texas, Paper No.ETCE2002 / Pipe-29029, февраль 2002 г. www.kiefner.com
Дата редакции: 12012011
Все, что вам нужно знать об испытаниях газопроводов
Все, что вам нужно знать об испытаниях газопроводов
Что такое газопровод? Газопровод — это транспортировка жидкого или парообразного газа на большие расстояния по трубопроводной сети, как правило, к месту нахождения потребителя. Испытания трубопроводов в основном проводятся для улучшения и обеспечения безопасности газопроводной системы.
- Испытание трубопровода давлением: В трубопровод подается воздух / азот с рабочим давлением в 1,5 раза и поддерживается от одного часа до трех часов.
- Гидростатические испытания : Сюда входит создание давления в трубопроводе водой для обнаружения возможных уязвимостей. Гидростатические испытания — это существующий метод оценки способности газопровода работать под давлением.При проведении гидростатического испытания необходимо выполнить следующие действия:
- Тестируемый трубопровод выведен из эксплуатации. Весь газ внутри него удален, а внутренняя часть промыта механическим способом.
- Затем трубу закрывают с обоих концов и полностью заполняют водой. Вода нагнетается до испытательного давления. Давление теста сохраняется и отслеживается в течение определенного периода времени, обычно 8 часов.
- Как только обнаруживается отсутствие потери давления, из участка трубопровода сливается вода, полностью очищается и снова вводится в эксплуатацию.
- Если секция не выдерживает или не поддерживает давление, это означает, что гидростатическое испытание привело либо к утечке, либо к разрыву трубы. В этой ситуации утечка обнаруживается, устраняется и труба снова проверяется. Трубы, не прошедшие гидростатическое обследование, заменяются.
- In-Line Testing: Встроенный контроль требует использования сложных технических устройств, также называемых «умными скребками» или методами поточного контроля, которые используются внутри трубопровода.Инспекция на линии требует использования сложных технических устройств, также называемых «умными скребками» или методов поточной инспекции, которые используются внутри трубопровода. «Умные свиньи» перемещаются со скоростью около пяти миль в час и обычно используются для проверки газопроводов, работающих при более высоком давлении.
Машина записывает данные (например, толщину стенки, коррозию, вмятины и т. Д.) По мере прохождения через трубопровод. После проверки данные обрабатываются и вносятся корректировки.
- Тестирование камеры: Проверка камеры включает просверливание нескольких отверстий по длине линии передачи, чтобы можно было установить привязанную камеру для наблюдения за внутренним состоянием трубы.Видео с камеры будет передано на устройство наблюдения и записи. Затем обученные специалисты проанализируют запись и решат, требуются ли какие-либо действия.
- Трубопровод на складе: Каждые 12 месяцев .
- Гидростатический клапан: Их можно заменять каждые 10 лет новыми устройствами, работающими под давлением.
- Обычные испытания: Испытания обычно проводятся три раза в год, в зависимости от возраста и формы газовой сети и трубопровода.
Мы рекомендуем проходить тестирование два раза в год.
Газопроводы подлежат испытанию и сертификации ежегодно . Несоблюдение не только увеличивает риски инцидентов, но может привести к штрафным санкциям и прекращению деятельности властями.
Для удобного тестирования газопровода щелкните здесь.
Как безопасность трубопроводов природного газа при испытаниях под давлением
Как безопасность трубопроводов природного газа при испытаниях под давлением
Боб Шивли, президент и ведущий фасилитатор Enerdynamics
За прошедшие годы газопроводы зарекомендовали себя как безопасный вид транспорта топлива.Но иногда о прорывах трубопровода попадают в новости, а очень редко это приводит к катастрофическим авариям. Многие газовые компании отмечают, что часть их инфраструктуры находится в земле в течение многих лет и может ухудшаться. Одним из ключевых способов ограничения неожиданных событий является испытание трубопроводов и газораспределительных компаний под давлением своих трубопроводов. Вот объяснение того, что это влечет за собой.
Испытания под давлением — это практика воздействия на трубы или трубопроводные системы давления, намного превышающего рабочее давление, для подтверждения целостности труб, фитингов и соединений.Идея состоит в том, чтобы найти слабые места трубопровода, прежде чем что-то пойдет не так. В зависимости от ситуации тестирование может проводиться с использованием сжатого воздуха, газа или воды. Испытания под давлением могут проводиться либо перед вводом трубы в эксплуатацию, либо на существующих линиях, которые эксплуатируются много лет.
Опрессовка новых установок
Давайте сначала рассмотрим опрессовку новых линий. Хотя так было не всегда, в настоящее время стандартом для всех новых линий электропередачи, распределительных линий или линий обслуживания является испытание давлением перед вводом в эксплуатацию. Практика различается в зависимости от типа линии. Например, линии электропередачи часто испытываются с использованием воды под давлением, потому что любая потеря давления происходит внезапно и утечки легко обнаружить (вы просто идете по линии и ищете лужу с водой). Примером опрессовки линии передачи является заполнение ее водой (до того, как она будет подключена к остальной части системы передачи), давление воды до 1,5-кратного максимального допустимого рабочего давления (MAOP), а затем оставление линии под давлением на время восемь часов, чтобы убедиться, что давление держится.
С другой стороны, двухдюймовая рабочая линия может быть испытана с использованием газа под давлением до 90 фунтов. Если линия может удерживать давление в течение 10 минут, это считается хорошим. Путем испытания под давлением перед вводом линии в эксплуатацию можно убедиться, что прочность всей линии удовлетворительна. Конечно, в качестве последнего шага важно записать результаты теста и поместить эту информацию в систему учета газовой компании.
Опрессовка существующих линий
Опрессовка существующих линий более сложна.Клиенты обслуживаются по линиям, в линиях уже есть газ, а доступ к существующим линиям может быть затруднен. Но испытание под давлением — важный способ убедиться, что существующая в земле труба способна безопасно выдерживать номинальное давление в трубопроводе. Это особенно верно для старых линий, потому что когда-то правила разрешали установку линий без испытаний под давлением, а максимальное рабочее давление в начале 1970-х годов было установлено на основе самого высокого давления, которое линия испытывала во время реальных операций, а не путем испытаний.И даже для линий, которые были протестированы при установке, линии могли быть повреждены или испортились за прошедшие годы.
Тестирование всех существующих трубопроводов — длительный процесс, поскольку многие газовые компании могут проложить тысячи километров трубопровода под землей. Компании обычно отдают предпочтение трубам на основе самого высокого потенциального отказа трубы и давления в трубе. Обычно компании в первую очередь сосредотачиваются на напорных трубопроводах трансмиссии (более 60 фунтов на квадратный дюйм). Гидроиспытания выполняются, как описано выше, но они затруднены, поскольку сначала необходимо удалить газ из линии.Тогда:
- линия должна быть доступна и изолирована путем вырезания части трубы;
- труба испытана;
- при обнаружении неисправностей трубу необходимо заменить;
- трубу необходимо очистить перед повторной установкой и повторным вводом в эксплуатацию.
Между тем, любые потребители, находящиеся ниже по течению от испытания, не обслуживаются, если у газовой компании нет средств для обеспечения дополнительных нисходящих поставок. Иногда это делается с использованием грузовиков для сжатого природного газа (КПГ) или сжиженного природного газа (СПГ), подключенных к нисходящей трубе.Чтобы посмотреть хорошее видео процесса тестирования, проводимого SoCalGas, щелкните здесь.
Несмотря на то, что испытание существующих линий под давлением и иногда неудобно для последующих потребителей, они являются важной частью процесса управления целостностью трубопроводов. Тестирование может выявить существующие дефекты в материале трубы, выявить растрескивание или другое повреждение, которое могло произойти, указать места, где коррозия ослабила трубу, или выявить места, в которых процедуры первоначальной установки были ошибочными.Это позволяет заменить неисправный актив до возникновения инцидента.
Прицеп-цистерна для СПГ с испарителем
Газопроводы обычно безопасны, но испытания давлением делают их еще безопаснее
Хотя серьезные инциденты на трубопроводах случаются редко, газовые компании постоянно оценивают методы эксплуатации для повышения безопасности. Все трубопроводные и распределительные компании практикуют программы управления целостностью трубопроводов. Эти программы позволяют операторам оценивать состояние системы, угрозы, последствия, риски для жизни и имущества, а также оценивать превентивные и смягчающие меры.Испытания под давлением — важная часть этих общих программ.
Вернуться на главную страницу блога
Гидростатические испытания — обзор
Испытания API 614, Глава 2, Система смазки
Гидростатические испытания — первое испытание, используемое в системе смазки. Система тестируется в собранном или частично собранном виде, в зависимости от конкретной системы. Для испытания используется испытательное давление, в 1,5 раза превышающее максимально допустимое рабочее давление (минимум 20 фунтов на квадратный дюйм для масляной стороны).Для деталей, смачиваемых маслом, в качестве испытательной жидкости должно использоваться легкое масло, которое обычно рекомендуется для смазки компрессорного агрегата.
Период тестирования — это время, необходимое для проверки на утечки, или минимум 30 минут. Приемка основана на отсутствии утечек, наблюдаемых визуально, или отсутствии падения испытательного давления.
Эксплуатационное испытание смазочной системы, как следует из названия, является функциональным испытанием для проверки как можно большего числа функций в рабочих условиях.Приведенную здесь процедуру следует рассматривать как дополнительное руководство к успешному испытанию консоли смазочного масла. Первый шаг — демонстрация чистоты системы. Затем следует беговой тест продолжительностью четыре часа. Испытание должно имитировать работу компрессора в полевых условиях во всех возможных смыслах. Все оборудование, поставляемое с системой смазки, должно использоваться в испытании, включая пусковые выключатели резервного насоса и аварийные выключатели системы. Все другие инструменты следует использовать для демонстрации их работы.Перед началом четырехчасового пробега систему следует тщательно осмотреть на предмет утечек и устранить утечки. Если для паровой турбины нет пара (если она используется), можно провести четырехчасовую работу на электронасосе. Однако следует приложить все усилия для использования альтернативного источника энергии, такого как сжатый воздух, для работы паровой турбины.
Для испытания запуска резервного насоса, которое является важным испытанием для обеспечения перекачки насосов без больших перепадов давления, необходимо проверить, поднимаются ли предохранительные клапаны или давление падает до давления, составляющего половину разницы между давление запуска резервного насоса и давление отключения компрессора. Переходное давление лучше всего измерять с помощью многоформатного самописца. Скорость диаграммы должна быть достаточно высокой, чтобы полностью отображать изменение давления. Хотя он не так хорош, как самописец, его можно заменить простой испытательной установкой, изготовленной в магазине. Запасной переключатель временно подключается к тому же месту, что и другие переключатели. Этот переключатель откалиброван на включение при пороговом приемном давлении. Контакты подключаются к контрольной лампе через реле уплотнения. Назначение реле — поддерживать цепь при восстановлении давления, поэтому свет останется включенным, если переключатель достигнет своего положения.Если при передаче горит контрольная лампа, консоль не прошла проверку. Очевидно, это испытание необходимо проводить при работающих обоих насосах. То же самое верно и для реакции регулирующего клапана, хотя баланс работы регулирующего клапана может быть достигнут с помощью резервного насоса. Из-за проблем, связанных с моделированием событий, лучше всего проводить тест с основным насосом, если это вообще возможно.
Необходимо выполнить как можно больше практических шагов. Перепускные клапаны охладителей и фильтров должны работать.Давление не должно падать до уровня запуска резервного насоса в перекачке. Если подается контрольное масло, необходимо смоделировать переходный процесс регулятора, чтобы проверить уровень давления на предмет падения до уровня запуска резервного насоса. Следует проверить передаточные клапаны, чтобы продемонстрировать, что утечка меньше пропускной способности корпуса фильтра. Предпочтительна нулевая утечка.
После минимум одного часа циркуляции масла при расчетном расходе необходимо проверить чистоту системы.Следует использовать процедуру, описанную в API 614, Глава 2. Консоль считается чистой, если количество и размер частиц на ситах соответствуют критериям приемлемости, указанным в API 614, глава 2.
Система смазки считается приемлемой, если во время испытания не возникают аномальные условия. Нестабильность или чрезмерные колебания давления на одном из этапов считаются ненормальным состоянием. Потребуются исправления в системе, и система будет повторно протестирована и продемонстрирована отсутствие отклонений, прежде чем ее можно будет считать приемлемой.
Тестовый трубопровод — обзор
18.4 Предварительное планирование трубопровода внутри штата
Перед любым гидроиспытанием инженер-испытатель или руководитель эксплуатации трубопровода должен определить минимальный и максимальный диапазон испытательного давления для всего трубопровода. Это испытательное давление должно учитывать текущий и будущий статус эксплуатации трубопровода, максимальное рабочее давление, а также федеральные и государственные правила испытаний. Испытательное давление во время этого испытания на прочность должно поддерживаться на уровне не менее 125% от максимально допустимого рабочего давления (MAOP) для трубопровода. 3 Как правило, самая низкая отметка трубопровода и самый слабый участок трубопровода будут факторами, которые могут ограничить MAOP системы. Номинальное давление труб и расположение клапанов, фланцев и других компонентов трубопровода должны быть идентифицированы и записаны на верстовых столбах.
Лучший подход к изучению влияния испытательного давления по длине трубопровода — это разработка электронной таблицы для всего трубопровода с данными трубы, градиентом высоты, рабочим давлением трубопровода, испытательным давлением (в фунтах на квадратный дюйм и футы) и текучестью трубы. сила, все vs.верстовой столб. Для этого необходимо, чтобы диаметр трубы, толщина стенки, марка трубы и внутреннее расчетное давление были известны для каждого участка трубы, подлежащего испытанию. Лучшим источником этой информации могут быть диаграммы профиля трубопровода, чертежи трассы трубопровода и планы участков трубопровода.
Таблица 18.1 представляет собой хороший пример предварительного тестирования и анализа, выполненного с помощью электронной таблицы, а также представляет дизайн и производительность конвейера с разбивкой по милям. Этот анализ может быть чрезвычайно полезен перед гидростатическими испытаниями, чтобы убедиться, что ни один участок трубопровода не будет подвергаться избыточному давлению, а также обеспечивает основу для будущего планирования испытаний. Я рекомендую потратить немного времени на изучение этой таблицы, пока вы не освоитесь с методологией.
Таблица 18.1. Предварительный анализ гипотетического трубопровода с несколькими диаметрами *
Анализ гипотетического трубопровода с жидкостью с разными диаметрами и толщиной стенки, расположенного в городской зоне † | |||||||||||||
---|---|---|---|---|---|---|---|---|---|---|---|---|---|
1 | 2 | 4 | 5 | 6 | 7 | 8 | 9 | 10 | 11 | 12 | 13 | 14 | |
Труба Mile-Post | футовВысота | D. (дюймы) | WT трубы (дюймы) | Объем сегмента (баррелей) | Давление в трубе (футы) | Давление в трубе (фунты на квадратный дюйм) | Испытательное давление (футы) | Испытательное давление (фунты на квадратный дюйм) | Местный% выхода | Гидростатическое давление (футы) | Гидростатическое давление (фунт / кв.![]() | Гидро% выхода | Гидро% выхода |
0,00 | 15 | 9027 9027 6,625 9028 0,25 2076900 | 2595 | 1125 | 30.4 | 2653 | 1149 | 128 | 39 | ||||
0,44 | 15 | 8,625 | 0,322 | 83 | 2059 | 891 | 9027 267 9027 9027 9027 9027 9278 1149 | 129 | 44 | ||||
0,65 | 15 | 10,75 | 0,365 | 69 | 2055 | 890 | 2569 | 1112 372784 | 2653 | 1149 | 129 | 48 | |
1,06 | 400 | 8,625 | 0,322 | 211 | 1649 | 714 | 983 | 138 | 38 | ||||
1,08 | 780 | 10,75 | 0,365 | 7 | 1268 | 549 | 1585 | 686 9027.![]() | 1888 | 818 | 149 | 34 | |
1,74 | 860 | 8,625 | 0,322 | 340 | 1154 | 9027 9027 9027 9027 6278 | |||||||
157 | 30 | ||||||||||||
3,03 | 960 | 8,625 | 0,322 | 421 | 974 | 422 | 1218 | 527 168 | 5271 | 1708 | 740 | 175 | 28 |
6,34 | 36 | 10,75 | 0,365 | 1081 | 1815 | 787 9027 9027 9027 9027 9027 9027 9027 9027 9027 1140 | 145 | 48 | |||||
12,5 | 58 | 10,75 | 0,280 | 3172 | 1648 | 713 | 2060 | 982 9027.1 | 2610 | 1131 | 159 | 62 | |
13,1 | 40 | 6,625 | 0,280 | 298 | 1559 | 9027 9027 9027 9027 9027 9027 9027 9027 9027 9027 1139 | 169 | 38 | |||||
14,2 | 30 | 6,625 | 0,280 | 219 | 1312 | 568 | 1640 | 710.![]() | 2638 | 1143 | 201 | 39 | |
18,6 | 20 | 6,625 | 0,280 | 834 | 494 | 214 9027 267 9027 9027 267 9027 9027 267 9027 267 1147 | 536 | 39 | |||||
19,5 | 10 | 6,625 | 0,280 | 164 | 341 | 148 | 426 | 185 9027.0 | 2658 | 1152 | 778 | 39 | |
Итого = 6899 |
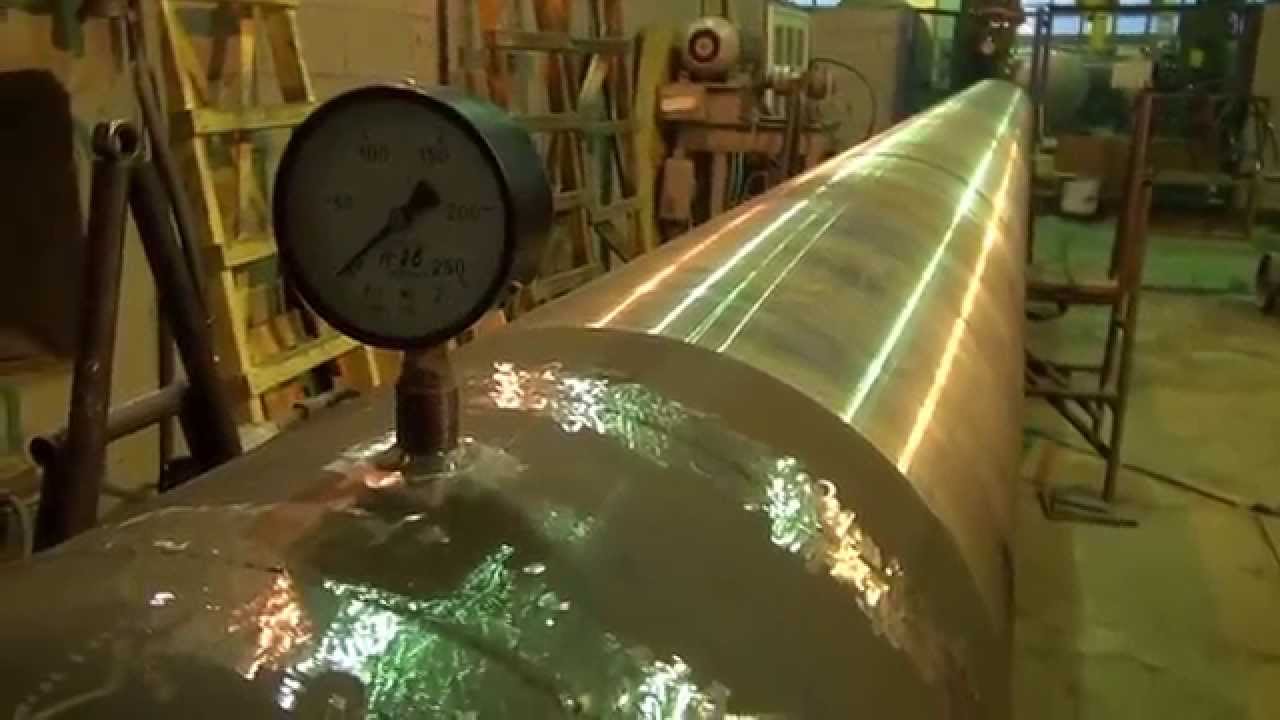
Обратите внимание, что MAOP 900 фунтов на кв. Дюйм на мильном столбе 0 (столбец 7), определенное испытанием, не близко к расчетной прочности внутренней трубы, с выходом всего 30,4%, а самый слабый участок трубопровода расположен на мильном столбике 12,5 с гидроэлектростанцией. давление при 62% предела текучести. Также рассчитывается количество удаляемого продукта из трубопровода и тестовая вода, необходимая для заполнения трубопровода в бочках. Анализ этого типа позволяет тщательно оценить трубопроводы-кандидаты перед тестированием, чтобы не произошло избыточного давления в трубопроводе.
Данные трубы и результаты расчетов могут быть нанесены на график (высота в футах по сравнению с мильными столбами) и представлены графически, как показано на рис. 18.2. На этом графике показано давление насосной станции при MAOP и минимальные испытательные давления, требуемые правилами, по всему трубопроводу, а также фактическое давление гидростатических испытаний, начиная с 1149 фунтов на кв. Дюйм (7928 кПа), но не постоянно на протяжении 19,51 мили (31,5 км). ) трубопровода, в связи с изменением отметки трубы. Этот график ясно показывает рабочий запас прочности по всей длине трубопровода и может использоваться в качестве основы для будущего расширения трубопровода.
Рисунок 18.2. Градиент гидростатических испытаний для гипотетического внутригосударственного трубопровода.
Глядя на данные по трубам, приведенные в Таблице 18.1, становится ясно, что трубопровод не подлежит очистке скребками из-за широкого диапазона диаметров труб: от 6 дюймов до 8 дюймов до 10 дюймов и обратно до 6 дюймов (150). от 200 до 250 и обратно до 150 мм). Поставщики свиней теперь производят скребков двойного диаметра (DD), которые могут выполнять приемлемую работу в трубопроводе с двумя диаметрами с очисткой и дозированием, но этот широкий диапазон диаметров превышает их возможности.Таким образом, дозирующий скребок или скребок нельзя успешно использовать для отделения продукта от тестовой воды, поскольку тестовая вода выталкивает продукт из трубопровода в резервуар для хранения. Поскольку скребки использовать нельзя, лучший подход — это нагнетать воду с турбулентной скоростью вместе с промывкой 150 стволов. Объем промывки был определен с использованием среднего трубопровода длиной 2000 футов (613 м) и диаметром 8 дюймов (200 мм).
Считается, что когда трубопровод заполняется водой для испытаний и переполняется водой, большая часть остатков продукта, воздуха и пара выталкивается в резервуары вместе со всем продуктом трубопровода.
Количество тестовой воды, включая промывочную, составляет около 7100 баррелей (1 128 900 литров). Поскольку, вероятно, на полигоне не будет воды, необходимо принять меры для ее получения. Вода может быть подана к месту проведения испытаний из ближайшего пожарного гидранта или другого источника воды, воспользовавшись услугами таких компаний, как Rain-for-Rent. Они приносят временную переносную трубу диаметром 6 дюймов или больше и натягивают ее над землей от пожарного гидранта к соединению на стороне всасывания транспортного насоса, если таковой имеется, или к переносному линейному насосу для заполнения, если необходимо. Они могут договориться с пожарными службами о разрешении на подключение к гидрантам с использованием устройств предотвращения обратного потока для защиты водоснабжения от загрязнения, фильтров для воды, когда это необходимо, и расходомеров для учета использования воды. Они доставляют переносную трубу и оборудование на полигон и проводят настройку. После завершения гидростатического испытания они снимают трубопроводы и оборудование для защиты от воды и вывозят их за пределы площадки.
Еще одна возможность получить воду на испытательном полигоне — заказать доставку чистых резервуаров на площадку компании Baker Tanks.Резервуары могут быть подсоединены к стороне всасывания транспортного насоса, как упомянуто выше, и затем будут приняты меры, чтобы грузовики с водой заполняли большие резервуары для испытаний (см. Рис. 18.3, на котором показано соединение для воды для испытаний).
Рисунок 18.3. План испытаний — трубопровод Intrastate, протяженностью 19,51 мили.
Третий вариант — временно использовать один из резервуаров для хранения нефти на насосном предприятии для хранения испытательной воды. Повторное использование испытательной воды может иметь хороший экономический смысл, если для испытаний запланировано несколько трубопроводов в этом месте, а существующая система трубопроводов достаточна для проталкивания испытательной воды после гидростатических испытаний обратно в предусмотренный резервуар для хранения.
Насосы для транспортировки по трубопроводу или переносные насосы должны обеспечивать промывку трубопровода и безопасное заполнение линии тестовой водой. Несмотря на то, что система тестовой воды подключается к всасывающей стороне насосов, следует принять меры для установки выпускного клапана высокой точки в самой высокой точке трубопровода или рядом с ней, если таковой не существует. Для этого гипотетического трубопровода (который схематически представлен на рис. 18.3) высшая точка находится на отметке 3.03. На рисунке 18.3 показано графическое представление тестируемой трубопроводной системы.Мы обсудим больше о важности удаления воздуха и пара из линии после завершения заполнения водой.
Теперь, когда уровень испытательного давления для линии определен и вода для испытаний будет доступна на месте, этот план предварительных испытаний можно завершить.
Руководство по гидростатическим испытаниям трубопроводов
Несмотря на то, что существуют различные способы транспортировки топливных ресурсов, трубопроводные системы являются одними из самых безопасных. Чтобы гарантировать его безопасность, перед вводом в эксплуатацию необходимо обеспечить общую целостность систем.Гидростатические испытания обычно используются для проверки и подтверждения этой целостности. В этой статье представлен общий обзор гидростатических испытаний трубопроводов, а также их преимущества, ограничения и требования.
Что такое гидростатические испытания?
Гидростатические испытания — это процесс, который обеспечивает безопасность и структурную целостность определенных сосудов под давлением, таких как резервуары для хранения, газовые баллоны, водопроводные системы и трубопроводы, с помощью оборудования для гидроиспытаний. Это промышленный метод испытания под давлением, который позволяет выявлять утечки в сосудах путем приложения давления, тем самым проверяя их сильные стороны.
Как работают гидростатические испытания?
Как указывалось ранее, испытание гидростатическим давлением включает испытание и проверку общей целостности сосудов под давлением. Стандартная процедура гидростатических испытаний трубопроводов включает следующие этапы:
- Заполните трубопровод жидкостью, в основном водой, если его материал не несовместим с водой.
- Подайте давление в трубопровод, чтобы довести его до допустимого испытательного давления. Это давление обычно превышает расчетное рабочее давление трубопровода.
- Удерживайте давление в течение необходимого периода времени, чтобы проверить трубопровод на предмет возможных утечек.
- Сбросьте давление в трубопроводе после подтверждения того, что испытание завершено и соответствует спецификациям и отраслевым стандартам.
Обратите внимание, что на сосуде должны быть вентиляционные отверстия, позволяющие выходить воздуху, когда он наполняется водой. Кроме того, флуоресцентные красители могут быть нанесены на испытательную жидкость для облегчения проверки и анализа. После подтверждения того, что трубопровод выдерживает допустимое испытательное давление, он может быть сертифицирован как безопасный для ввода в эксплуатацию.
Общие приложения гидростатических испытаний
Гидростатические испытания используются в промышленном секторе по-разному. Применяется для определения целостности и информирования об эффективном ремонте:
- Теплообменники
- Недавно установленные или модифицированные системы трубопроводов для газа, воды и других жидкостей
- Воздушный компрессор и системы хранения и распределения
- Системы пожаротушения
- Свинец, резервуары и реакторы, используемые в промышленных процессах
Как правило, гидростатические испытания обнаруживают разрывы, отверстия или зазоры в сосудах, которые возникают в процессе их изготовления в результате литья или сварки. Некоторые другие возможные дефекты, которые он может обнаружить, — это газовые поры, вязкие разрывы, включения песка и локальные твердые пятна. Приложения включают дефектоскопию в промышленном производстве, хранении и транспортном оборудовании.
Преимущества аутсорсинга гидростатических испытаний
Аутсорсинг услуг по гидростатическим испытаниям имеет свои преимущества. Можно воспользоваться услугами авторитетных компаний по испытанию гидростатического давления, поскольку они предлагают следующие преимущества:
- Многолетний опыт проведения испытаний гидростатическим давлением в соответствии с отраслевыми стандартами и стандартами клиентов.
- Обладая современным оборудованием для гидроиспытаний, они всегда соответствуют спецификациям Министерства транспорта (DOT).
- Устраняет потребность в рабочей силе, связанную с приобретением оборудования для гидростатических испытаний.
- Экономит время и деньги, связанные с проведением тестов самостоятельно и поддержанием актуальности сертификации оборудования.
Ограничения гидростатических испытаний трубопроводов
Хотя гидростатические испытания трубопроводов оказались наиболее надежным, безопасным и наиболее распространенным методом испытаний под давлением, он не идеален для некоторых систем и не позволяет выявить некоторые недостатки.Эти два ключевых ограничения обсуждаются ниже.
Не подходит для некоторых систем
Общеизвестно, что методы испытаний гидростатическим давлением не подходят для повторных испытаний существующих систем. Причина этого в том, что процедура испытания требует, чтобы все содержимое сосудов или систем было удалено или продувано. Это означает, что они (суда или системы) временно выводятся из эксплуатации, что приводит к простою. Это время простоя означает, что, если у вас нет резервной системы или судна, которое будет служить заменой во время теста, вы столкнетесь с неэффективной производительностью в это время.
Неспособность обнаружить некоторые недостатки
Этот метод испытания под давлением не позволяет обнаружить подкритические дефекты в системе. Эти недостатки требуют, чтобы системы подвергались воздействию более высоких диапазонов внутреннего давления, чтобы их можно было обнаружить и измерить. Поскольку гидростатические испытания зависят от визуального осмотра и иногда измерения расширения для подтверждения безопасности оборудования или системы, подкритические дефекты часто остаются незамеченными или усугубляются испытанием.
Требования к гидростатическим испытаниям
Американское общество инженеров-механиков (ASME) опубликовало ASME B31.1 и ASME B31.3 для определения требований к гидростатическим испытаниям технологических трубопроводов. В этих нормах указано, что испытательное давление должно быть не менее половины расчетного рабочего давления трубопроводной системы на протяжении всего испытания. Эта спецификация может быть изменена только в том случае, если расчетная и рабочая температура выше температуры испытания. В этом случае минимально допустимое давление может быть оценено с помощью кодов.
NiGen предлагает испытания трубопроводов гидростатическим давлением
В NiGen мы предлагаем интеллектуальные технологические решения нашим партнерам в различных производственных отраслях. Для промышленных игроков, которым нужны рентабельные услуги по испытанию трубопроводов гидростатическим давлением, лучше всего подойдет NiGen.
Чтобы узнать больше об услугах, которые мы предлагаем нашим партнерам в нефтегазовой отрасли, свяжитесь с нами через Интернет.
Гидростатические испытания | Инспекционная
Гидростатические (гидро) испытания — это процесс, при котором компоненты, такие как трубопроводы , системы , газовые баллоны, котлы и сосуды под давлением , проверяются на прочность и герметичность.После остановов и ремонтов часто требуются гидроиспытания, чтобы подтвердить, что оборудование будет работать в желаемых условиях после возвращения в эксплуатацию.
Кроме того, гидростатическое испытание не может быть выполнено во время нормальной работы и не может контролировать оборудование на предмет утечек после того, как испытание было выполнено. Целостность оборудования в процессе эксплуатации лучше всего контролируется с помощью эффективной программы для обеспечения механической целостности фиксированного оборудования .
Хотя гидростатические испытания считаются методом неразрушающего контроля , оборудование может сломаться и выйти из строя, если при проверке будет превышено заданное испытательное давление или если небольшая трещина быстро распространяется.
Как это работает? Гидростатическое испытание — это тип испытания под давлением, при котором компонент полностью заполняется водой, удаляется воздух, содержащийся внутри агрегата, и повышается давление в системе до 1,5-кратного предельного расчетного давления агрегата. Затем давление поддерживается в течение определенного времени для визуального осмотра системы на предмет утечек. Визуальный осмотр можно улучшить, нанеся на жидкость индикаторные или флуоресцентные красители, чтобы определить, где возникают трещины и утечки.
Существует три распространенных метода гидростатических испытаний, которые используются для испытаний небольших сосудов и цилиндров под давлением: метод водяной рубашки, метод прямого расширения и метод контрольных испытаний.
Метод водяной рубашкиДля проведения этого метода сосуд наполняют водой и помещают ее в герметичную камеру (называемую испытательной рубашкой), которая также заполнена водой. Затем сосуд находится под давлением внутри испытательной рубашки в течение определенного времени.Это приводит к расширению емкости внутри испытательной рубашки, в результате чего вода выталкивается в стеклянную трубку, измеряющую полное расширение. После регистрации полного расширения в сосуде сбрасывается давление, и он сжимается до своего приблизительного первоначального размера. Когда сосуд сдувается, вода течет обратно в испытательную рубашку.
Иногда судно не возвращается к своему первоначальному размеру. Это второе значение размера называется постоянным расширением. Разница между полным и постоянным расширением определяет, пригоден ли резервуар к эксплуатации.Обычно чем выше процент расширения, тем больше вероятность вывода судна из эксплуатации.
Метод прямого расширения включает наполнение емкости или цилиндра определенным количеством воды, создание давления в системе и измерение количества воды, которое вытесняется после сброса давления. Значения постоянного и полного расширения определяются путем регистрации количества воды, нагнетаемой в сосуд, испытательного давления и количества воды, вытесненной из сосуда.
Испытательный метод давления В ходе контрольного испытания под давлением применяется внутреннее давление и определяется, есть ли в резервуаре какие-либо утечки или другие слабые места, такие как утончение стенок, которые могут привести к отказу. 1 В США этот метод разрешен только в том случае, если Свод федеральных правил США не требует регистрации постоянных и общих значений расширения.
Некоторое оборудование может быть не предназначено для выдерживания нагрузок, необходимых для испытания под давлением.В этих случаях следует использовать альтернативные методы, такие как пневматические испытания. Пневматические испытания — это еще один тип испытания под давлением, при котором в сосуд создается давление в сосуде с помощью газа, такого как воздух или азот, вместо воды. Однако следует проявлять особую осторожность при проведении пневматических испытаний, поскольку газообразные среды могут сжиматься и содержаться в больших количествах по сравнению с гидростатическими испытаниями.
Примечания к гидроиспытаниямДля трубопровода гидроиспытания проводятся при неработающем трубопроводе.Вся нефть и / или природный газ обычно сбрасываются, а перед испытанием линия механически очищается.
В любом случае операторы и инспекторы должны учитывать свойства текучей среды для гидроиспытаний и то, как среда может влиять на оборудование. Например, вода является хорошей средой для возникновения коррозии. Поэтому перед началом работы оборудование необходимо тщательно высушить и очистить от загрязнений.
- Справочник по сжатым газам , Compressed Gas Association, Inc.изд. 3. С. 184, 1990. .
Связанные темы
Инструменты темы
Поделиться темой
Внести вклад в определение
Мы приветствуем обновления этого определения Integripedia от Inspectioneering сообщество.Щелкните ссылку ниже, чтобы отправить любые рекомендуемые изменения для Inspectioneering’s команда редакторов для обзора.
Способствовать определению .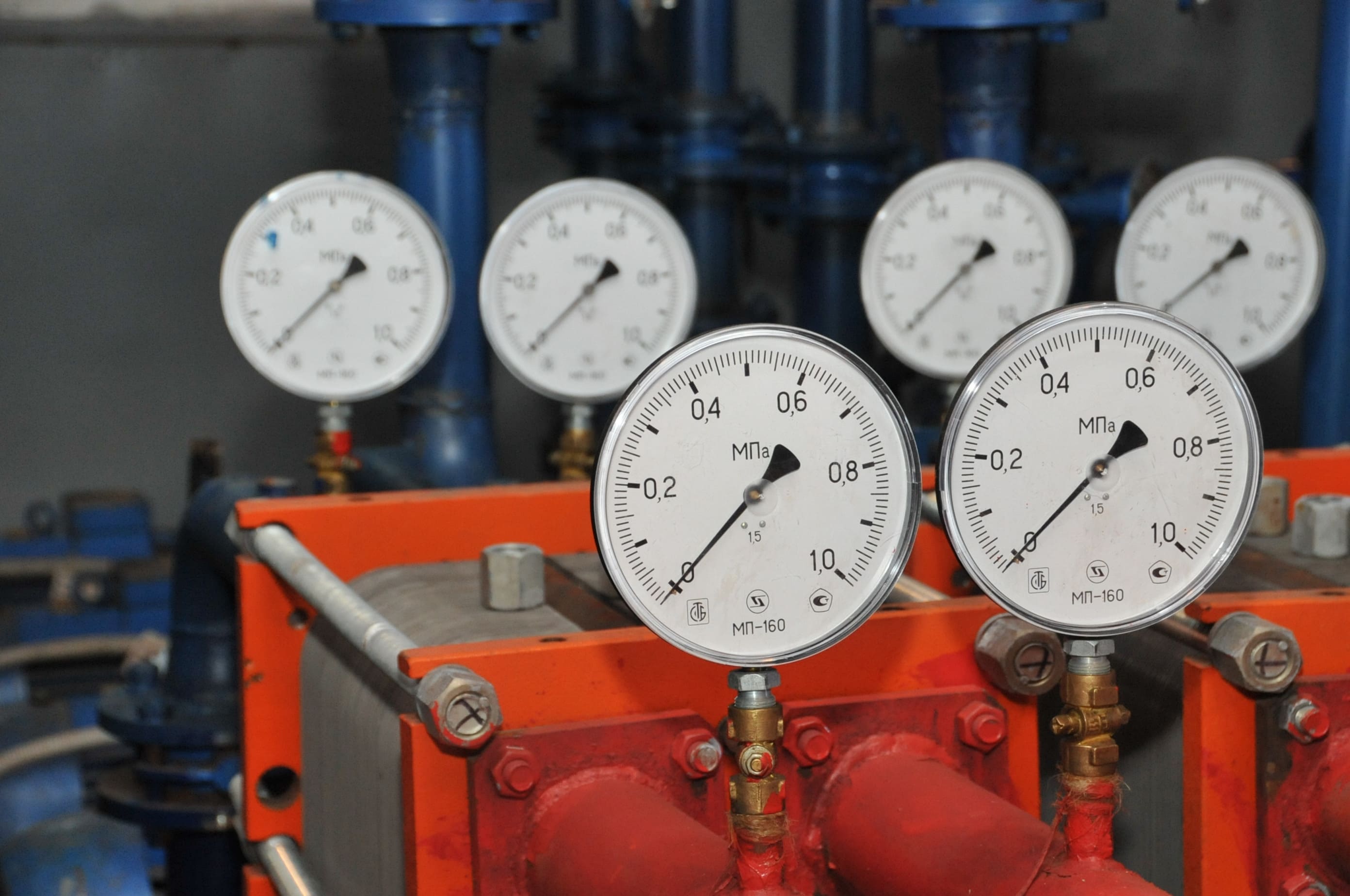