Изготовление колодок для обуви: Классификация колодок для обуви
Классификация колодок для обуви
В каталогах и описаниях обуви в нашем магазине вы можете увидеть информацию о неких колодках — иногда они обозначаются цифрами (например, 026), а иногда обладают именами собственными (скажем, Capital или Pennine). В этой статье мы расскажем о том, что представляют собой эти колодки, почему их так много, и какими они бывают.
Что такое обувные колодки?
Колодками называются шаблоны, выточенные из дерева или пластика и обладающие формой человеческих стоп. Именно на колодки в процессе производства туфель или ботинок натягивается заранее сшитый верх обуви — для того, чтобы он в итоге приобрёл необходимую форму. Так как стопы различаются не только по длине, но и по форме, подъёму и полноте, то и обувные колодки тоже бывают разными. У одного производителя классической обуви обычно есть несколько вариантов, а иногда их число даже достигает пары десятков.
Изготовление туфель с помощью обувной колодкиРазрабатывая обувные колодки, производители, с одной стороны, учитывают особенности различных типов стоп, а с другой — соблюдают свой собственный фирменный силуэт и стиль. Следует иметь в виду, что колодка, разработанная для стоп одного типа, может быть совершенно неудобной для стопы другого типа. На практике это означает, что если одна модель производителя А вам не подошла, то из этого не следует, что все остальные модели этого производителя вам тоже не подойдут. Не исключено, что другая модель того же бренда в том же самом, например, английском размере окажется впору.
Как можно отличить высококачественную, грамотно проработанную колодку от более примитивной масс-маркетной?
Чтобы оценить качество колодки, сначала посмотрите на ботинок сверху: если его наружный край изогнут, а внутренний почти прямой и по боковым сторонам не видно краев подошвы, переверните ботинок. Если и со стороны подошвы его контуры выглядят примерно так же, как сверху, но внутренний край сильно вогнутый у перехвата (самой узкой части ступни), тогда есть вероятность, что ботинок сшит на хорошей колодке.
Майкл Антон, автор книги «Костюм»
Готовые и индивидуальные колодки
Туфли, которые можно купить в магазинах, шьются на заранее изготовленных колодках, в то время как обувь на заказ (bespoke) создаётся на колодках, сделанных по меркам, которые снимаются со стоп клиента. Автор энциклопедии мужского стиля «Джентльмен» Бернхард Рётцель указывает, что «именно индивидуальные колодки отделяют туфли, сделанные на заказ, от фабричных готовых туфель». Далее он добавляет, что «колодка, на которой изготавливаются фабричные туфли, может отвечать только средним критериям, хотя, не исключено, с очень близким соответствием. Например, Church’s выпускает до шести вариантов полноты на одну модель, и большинство мужчин найдут одну из них полностью удовлетворяющей их потребности».
Изготовление индивидуальных обувных колодок
Фабричные обувные колодки на производстве John Lobb
Какими бывают колодки?
Обувные колодки отличаются друг от друга по форме, а также по ширине («полноте»). Есть очень изящные варианты, есть более консервативные, есть так называемые country колодки, которые используются для моделей в загородном стиле — и порой они чуть больше обычных, так как эту обувь предполагается носить с более толстыми носками, чем те, что вы надеваете со строгими оксфордами.
По полноте можно выделить как минимум четыре вида колодок: E (узкие), F (стандартные), G (широкие), H (очень широкие). У некоторых американских фирм, однако, вариантов по полноте ещё больше — вплоть до девяти (от чрезвычайно узкого ААА до очень широкого ЕЕЕ).
Промаркированная обувная колодка стандартной полноты F Классифицировать колодки можно и по форме мысков. Есть колодки с квадратными, острыми, округлыми носами, а также с зауженными мысками с прямым передним краем. Первые два варианта рекомендовать сложно, а вот округлые мыски — это так называемая вечная классика.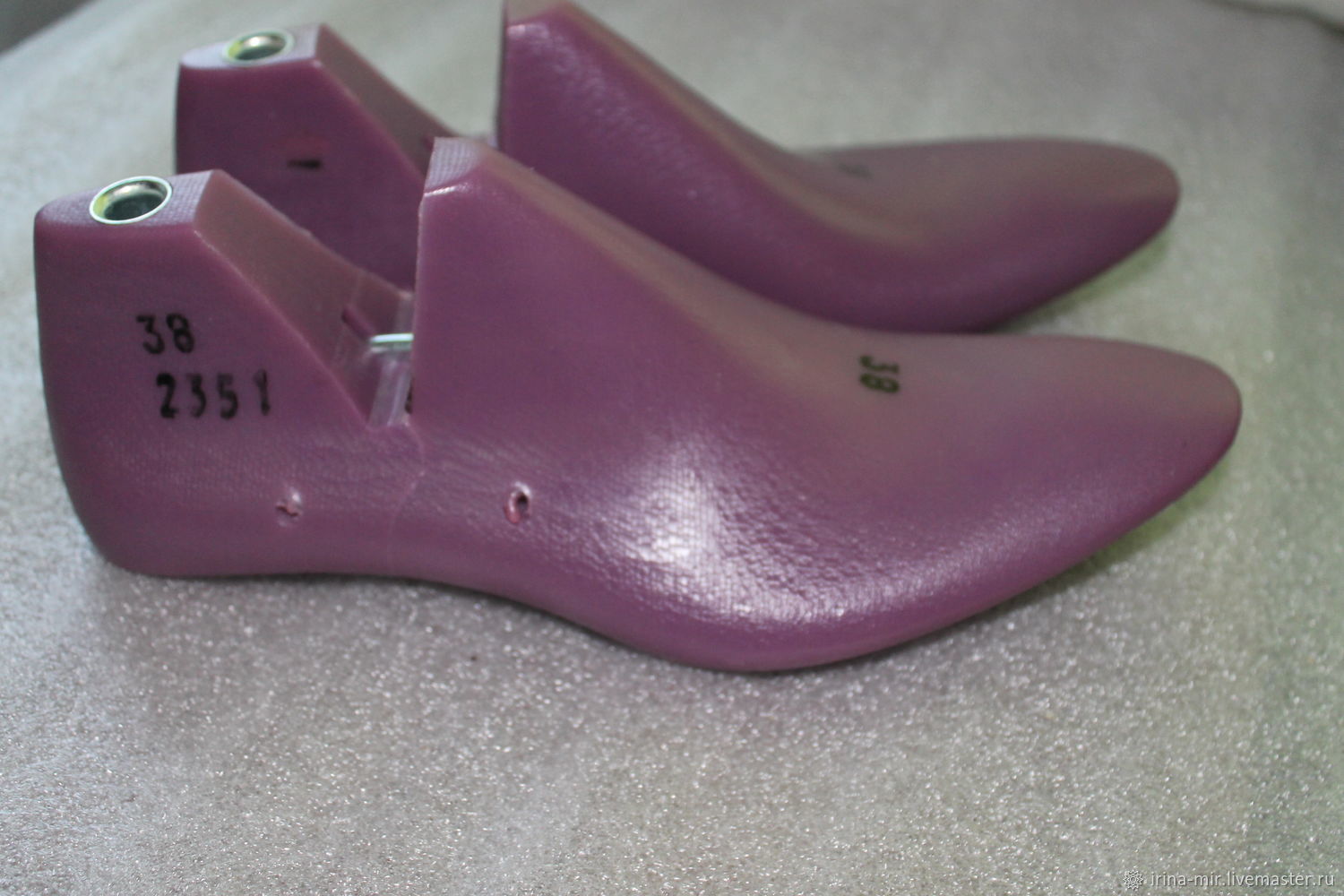
Зауженные мыски с более или менее прямым передним краем выглядят менее консервативно, чем закруглённые, но при этом они порой имеют весьма изящный и элегантный вид. Такие мыски, в отличие от совершенно квадратных или очень заострённых, вполне могут присутствовать на классических туфлях и ботинках.
Колодки для обуви с зауженным мыскомИзготовление деревянных колодок для обуви самостоятельно
Алексей Гринев из Красноярска задает вопрос:
Решил заняться пошивом тапочек. Как и из чего можно сделать колодки для изготовления обуви, которые могли бы прослужить довольно длительное время?
Ответ эксперта:
Оптимальный материал для приготовления обувных болванок – дерево, обладающее твердостью, устойчивостью к воздействию влаги, хорошо поддающееся шлифовке. Такими свойствами обладает береза, бук, клен. В качестве заготовок лучше взять отрезки бруса 12х12 см. Для выбора длины можно использовать старую обувь подходящего размера и по ней отмерить необходимое расстояние.
Для работы понадобятся следующие инструменты:
- ножовка по дереву;
- киянка;
- набор стамесок, в том числе с закругленными резцами;
- топорик;
- рашпиль плоский и полукруглый.
Еще понадобится пара старой обуви, желательно спортивной (кроссовки), которая хорошо облегает ноги.
Схема изготовления обувной колодки
Пошаговая инструкция по вытесыванию колодок для изготовления обуви своими руками:
- На одной из сторон бруса карандашом обводится подошва кроссовка, а на боковых его сторонах вырисовывается профиль будущей обуви.
- Посередине нижней и верхней части проводятся центровые линии. Просверливаются два сквозных отверстия, которые помогут восстановить центровку в процессе обработки древесины резцами.
- С помощью ножовки и топорика удаляются излишки дерева на заготовке. При этом соблюдается осторожность, чтобы не срубить лишнего. Сначала выпиливаются крупные участки, потом скалываются более мелкие.
- Далее заготовка обрабатывается стамесками до придания формы, наиболее схожей по размерам с ногой. Во время работы необходимо постоянно сверять удаление оттачиваемых поверхностей от центра, чтобы не допустить изъяна на колодке.
- Окончательная шлифовка производится с помощью рашпилей и наждачной бумаги.
Если планируется использование каблука, то пяточная часть заготовки должна иметь соответственное углубление.
В таком же порядке изготавливается колодка для второй ноги. Процесс может показаться излишне трудоемким, но на выходе пользователь получит пару колодок, которые можно использовать на протяжении длительного времени и не только для изготовления тапочек. Каждая болванка может использоваться для пошива обуви только одного размера и одного фасона. Для других моделей понадобятся иные колодки, которые можно изготовить по такой же предложенной схеме с внесением соответствующих корректировок.
Видео: Станок для изготовления обувных колодок
Екатеринбуржец, ставший мастером–обувщиком о том, как и зачем делать ботинки своими руками
Уютное помещение освещают солнечные лучи. Заходя в мастерскую, чувствуешь слегка уловимые ароматы кожи и воска. В окружении старинных инструментов, шуршащей кальки и кожаных лоскутов мастер вручную собирает уникальную пару обуви. Иван Белов – владелец мастерской, по профессии юрист, но это никак не мешает ему заниматься тем, что нравится. Он рассказал It’s My City, как создается обувь ручной работы.
Как появилась идея открыть мастерскую?
Случилось это два с половиной года назад: я смотрел видео-ролики в интернете, и в них процесс создания обуви показался мне не только интересным, но и «простым». После детального изучения технологии решил заняться этим более углубленно. На деле же оказалось, что это не так просто. Я искал различные курсы, но по тем или иным причинам они не подходили, приходилось учиться по роликам в интернете и книгам.
В итоге мне удалось выйти на специалиста в Москве. Договорился и поехал к нему на несколько дней. Ехал целенаправленно и с неким «чемоданом» теоретических знаний, не подкрепленных практикой. Именно там, в процессе построения первой пары и пришло понимание, что это то ремесло, которое действительно мне интересно.
В день отъезда из Москвы не было ничего необычного, кроме того факта, что я шагал в ботинках сделанных своими руками
После возвращения стал задумываться о покупке необходимых материалов. Первой и серьезной статьей расходов стала покупка швейной машинки, а вот с инструментами возникли трудности. Основная часть закупалась в Германии, потому что у нас найти хороший инструмент практически невозможно. Кожу тоже нужно закупать заграницей, поскольку все известные дубильни (производители качественных кож) находятся именно там.
Мастерская в ее сегодняшнем виде, со знаниями и философией, появилась год назад. Весь процесс изготовления обуви происходит именно здесь, в Екатеринбурге.
С чего начинают делать обувь?
Все начинается с замеров. Человек приходит, с каждой ноги я снимаю мерки. Для этого изготавливаются индивидуальные колодки. Колодка – самая важная деталь в процессе изготовления обуви, в индивидуальном изготовлении она максимально повторяет форму стопы и влияет на внешний вид будущей пары. Так что в следующий раз заказчик может мне позвонить из любой точки земного шара и заказать ботинки, просто прислав рисунок.
Следующий этап – лекала будущего ботинка, затем из них вырезаются все из кожи и натягивается на колодку с помощью затяжных клещей, после приколачивается гвоздями и прошивается. Затем идут подошва, стельки, каблук. Это тоже делается из кожи. Прежде чем сделать основную пару, я делаю пробную и как минимум три раза мы встречаемся с заказчиком. Весь процесс создания обуви делается вручную, без использования промышленных мощностей.
Чтобы делать обувь, не нужно каких-то исключительных инструментов. Все инструменты обычные. Например, гвозди – расходный, но необходимый материал. Помню, когда я был маленьким, то помогал деду что-то колотить, и одной из моих задач было выпрямлять гвозди для будущих работ. Сейчас я, конечно, этого не делаю, но бережное отношение к инструменту осталось с детства.
Ваш самый любимый этап в создании обуви?
Я пытался понять, что мне больше всего нравится в этом ремесле, но здесь все по-своему интересно. Мне нравится рисовать, моделировать, работать с кожей. Единственное – не нравится ждать, когда я сниму ботинок с колодки. В старые времена нужно было выдерживать ботинок два–три месяца. Сейчас все быстрее, у меня с момента замеров до готовой пары проходит примерно 35-40 дней.
А вообще, здорово прикоснуться к ремеслу, которое когда–то определило сегодняшний уровень производства обуви. Сейчас традиции сапожного мастерства не утеряны, но про них забывают. Раньше же все делали вручную и у нас, и заграницей.
А зачем в современной жизни необходимо делать обувь вручную?
Здорово стать сопричастным к одному из древнейших ремесел. Сегодня ручной труд востребован у тех людей, которые его понимают. Не составляет проблемы прийти в магазин и купить обувь, но там вы не можете повлиять на нее.
В мастерской вы не найдете готовую коллекцию обуви и не купите готовые ботинки, выбрав их из каталога
Здесь можно полностью влиять на все: от материала до ширины стежков, любой человек может стать дизайнером и конструктором. И тут важен не только конечный результат, но и сам процесс. Ручное производство обуви основано на индивидуальном отношении.
Какие у вас планы на будущее?
В ближайшее время буду я принимать участие в чемпионате мира по изготовлению обуви, который пройдет в Лондоне. За два с половиной месяца нужно изготовить ботинок определенной модели и отправить на оценку жюри. Там соберутся судьи-мастера обувного ремесла, которые несколько десятков лет делают обувь. И даже просто поучаствовать и представить на обзор ботинки, которые создаются в Екатеринбурге – уже большое достижение.
А вообще я хочу развивать это искусство и ремесло, привлекать и вовлекать в него как можно больше людей. История знает много имен мастеров сапожного дела, а тайны ремесла передавались из поколения в поколение. Все тонкости, нюансы, мельчайшие детали, которые отличают ручную обувь от изделий массового производства, по книгам не узнаешь. Это можно узнать, только наблюдая за работой мастера, постепенно проникая в его секреты. Я готов делиться теми знаниями, которые наработал в течение нескольких лет. Двери моей мастерской открыты для всех желающих: кто хочет просто посмотреть или узнать об истории сапожного дела, или научиться этому ремеслу. Особых знаний и навыков, для того чтобы начать, не требуется, главное – желание.
Фотографии предоставлены Иваном Беловым
Мы работаем в интересах наших читателей. Если вам важно наличие такого СМИ, поддержите нас донатом.Колодка
Специалисты высочайшей квалификации безукоризненно воплощают дизайнерские идеи и конструкторские разработки любой сложности
Сегодня предприятие JB-PLAST выделяется из ряда производителей осознанием современных и будущих тенденций, уникальными технологиями и индивидуальным творческим подходом к воплощению идей заказчиков. Предприятие работает на оборудовании лучших европейских производителей, основываясь на новейших мировых разработках.
В производстве используются современные, отлично зарекомендовавшие себя материалы – как основные, так и вспомогательные, которые гарантируют удобство в эксплуатации и длительный срок службы изделий.
Техническое оснащение предприятие JB-PLAST проходит регулярную модернизацию.
Важный момент – экологическая составляющая. На современном этапе развития любого производства именно экологичность продукции является непременным атрибутом качественного и безопасного товара.
Предприятие JB-PLAST использует в производстве системы очистки воды и воздуха, применение компонентов и химикатов с минимальным содержанием веществ, воздействующих на окружающую среду.
Свою цель JB-PLAST видит в том, чтобы создавать продукцию, придерживаясь самых высоких стандартов. И уже в течение двадцати лет предприятие успешно справляется с этой задачей.
JB-Plast специализируется на выпуске полиэтиленовых обувных колодок для всех видов обуви.
Производство колодок ведется на импортном оборудовании из качественного сырья с итальянской фурнитурой. Цех по производству обувных колодок оснащён копировально-фрезерным оборудованием, обеспечивающим высокую точность линейных и объёмных параметров изготавливаемых изделий.
По конструкции колодки выпускаются с клиновидным замком, с «французским» замком (тендо) или без замка, с различными видами металлических пластин.
Каждая пара колодок проходит контроль качества на всех этапах производства, начиная с отлива стандартной заготовки и заканчивая высокоточной обработкой уже готовой модели.
На производстве работают высококвалифицированные специалисты, способные разработать любые фасоны колодок, произвести их тиражирование по размерам и полноте.
Колодка может быть разработана по Вашему эскизу, по подошве в кратчайшие сроки. Традиционно изготовление новых фасонов делается вручную. В настоящее время современная технология, применяемая на нашем производстве, включает электронное сканирование образца, создание цифровой модели, компьютерное моделирование и дальнейшее изготовление на копировально-фрезерном оборудовании, обеспечивающем высокую точность линейных и объемных параметров. Одним из преимуществ цифровой модели является ее способность сохранять параметры колодки и копировать ее максимально точно необходимое количество раз.
JB-Plast предлагает своим партнерам качественную продукцию, изготовленную по новым технологиям, высококвалифицированными специалистами и приглашаем представителей обувного бизнеса к сотрудничеству. Цены на продукцию конкурентоспособны, действует гибкая система скидок. Индивидуальный подход к каждому клиенту, обеспечивает оперативность,целостность и качество заказа.
Ручное изготовление колодки из дерева мастером Курокио
2016-01-06
Мастер-класс по производству обувных колодок из дерева от мастера Курокио (Япония)
Для производства колодок используют такие сорта дерева, которые позволяют колодке быть одновременно прочной, легко впускать в себя гвозди, а также не менять существенно свой размер при попадании на них влаги. Всем вышеперечисленным требованиям удовлетворяют такие сорта дерева как бук, граб, береза, липа и клен.
Мастер Курокио не говорит какой сорт дерева он использовал, но, возможно это как раз один из вышеперечисленных сортов.
Курокиосан не комментирует свой видеоурок, но мы попытаемся по шагам разобраться в последовательности ручного изготовления обувных колодок.
1. Прежде всего для изготовления пары деревянных обувных колодок потребуется два куска дерева, предпочтительно квадратного сечения размером примерно 15х15см. Опять же необходимо понимать какого типа колодка должна получиться – если сапожная, то горловина должна быть повыше примерно на 3 см по сравнению с туфельной колодкой. Т.е. для туфельной колодки и первоначальное сечение бруса могло быть и поменьше, например 12х12см.
2. На боковые грани заготовки необходимо нанести первоначальные грубые зарисовки бокового профиля и профиля подошвы. Для этого необходима первичная подготовка поверхности с помощью рубанка по дереву.
Для нанесения перпендикулярных характерных линий хорошо использовать металлический угольник, а рисовать можно тонким маркером или гелиевой ручкой (как у мастера Курокио) темных цветов.
3. И вот профили боков и подошвы нанесены. Что же будет далее? А далее Курокио-сан берет ту же самую пилу, которой пилил исходный брус и спиливает большой кусок дерева, в носочной области. Колодку при этом неплохо бы зажать в большие столярные или слесарные тиски, чтобы обеспечить безопасность работы.
4. Какие инструменты использует мастер-колодочник? В основном это инструменты для резьбы по дереву – топорик, стамески, рубанки, рашпили. Обратите внимание, что мастер Курокио большую часть работы будет делать круглыми резцами, т.к. в некоторых местах колодка не только бывает выпукла, но и вогнута как-бы внутрь. Вот там-то и придут на помощь круглые резцы, т.к. плоский резец просто срезал бы много нужного материала.
И вот, работа резцами пошла. Сначала можно срезать самым большим плоским резцом-стамеской. Работа стамеской в большинстве случаев сопровождается легкими ударами молотком по торцу стамески.
Вот так выглядит заготовка с выбранной носовой частью.
5. Переворачиваем колодку и, согласно боковому профилю формируем пяточный подъем, который необходим, для установки каблука заранее рассчитанной высоты. Работать в этом месте удобней плоской стамеской. В завершение этого этапа угловой переход можно скруглить на шлифовальном станке, что и показывает нам мастер Курокио. После шлифовки необходимо повторно нанести профиль подошвы, т.к. предыдущий профиль был стесан вместе с деревом.
6. Далее необходимо убрать много лишнего материала с боков, особенно ближе к пяточной части колодки, поэтому Курокио-сан решил использовать для этого небольшой японский тамагавк.
7. Аналогично, мастер-колодочник срезает дерево и с боков в носочной части заготовки колодки.
После этого этапа колодка приобретает очертания, напоминающие валенок.
8. Пришла пора поработать как раз в той области, где колодка имеет вогнутости. В этих местах никак не получится работать плоскими стамесками, т.к. необходимо делать рез только в узкой области вдоль траектории резца. Приходится использовать круглый большой резец. Им мастер обрабатывает места в районе подъема колодки и в пяточной области в районе лодыжек.
Вот так причудливо выглядит колодка после того как по ней прошлась круглая стамеска.
9. Очень важно при ручной обработке обувной колодки не потерять линию симметрии. Для этого всякий раз, когда возникает возможность срезать или сошлифовать линию середины колодки, можно заранее поставить центровочные шпильки, которые в дальнейшем позволят восстановить утерянные линии.
10. Опять обращаемся к шлифовальному станку, чтобы подравнять ненужную рифленость.
11. По мере того как очертания колодки приближаются к заданным размерам нужно переходить к более точным инструментам. В данном случае – это рашпили с различным рисунком рабочей части. Опять же видно, что понадобятся не только плоские но и рашпили с полукруглым профилем.
Вот видно, как Курокио-сан обрабатывает пяточную часть подошвы рашпилем.
12. Настала пора позаботиться о выпуклости подошвы. Посмотрите какой инструмент для этого использует Курокио – обычный остро заточенный сапожный нож. Японский иероглиф обозначает верхнюю точку выпуклости.
13. А вот выпуклость в носочной области мастер делает уже небольшим закругленным рубанком. Здесь нет жестких правил каким делать инструментом ту или иную обработку. Каждый мастер вправе выбирать тот инструмент, который для него наиболее удобен.
14. Итак до заданного профиля подошвы остались считанные миллиметры. Теперь нужно быть предельно осторожным и внимательным. Посмотрим, справится ли мастер Курокио с этим ответственным этапом.
Да, он опять пошел на хитрость – обратился к шлифовальной машине, т. к. она обеспечивает хоть и не такой быстрый съем материала как стамеска, зато более контролируемый. Мастер четко представляет в какой момент какой инструмент нужно применять. После обработке на шлифовальном станке колодка уже начинает походить на колодку.
15. А теперь повторяются некоторые операции, но уже резцами меньших размеров, а значит мастер более точно и медленно приближается к нужным размерам. Можно позавидовать терпению мастера Курокио-сан, когда ему снова и снова приходится делать похожие операции но с более «точным» инструментом.
После обработки на шлифстанке колодка уже готова. Но что это? На подошве обнаружился по всей носовой части один лишний миллиметр! Опытная рука мастера удаляет его круглым рубанком. Несколько плавных движений руки с мелкой наждачной бумагой, чтобы устранить микроскопические неровности. И это был последний, завершающий, победный штрих!
Ура!!! Колодка на 1000 долларов готова! Вот она держите, господин заказчик! Таких колодок, точно под Вашу ногу нигде и никто так классно не сделает! Хотите заказать еще? Жене и детям? Запишитесь пожалуйста в список – Ваш номер 374. Приходите через 4 месяца.
Вот так и живет и работает профессионал-колодочник из Японии Курокио-сан.
Пожелаем ему успехов, удачи, любви, здоровья и пусть хоть иногда устраивает себе выходные, а то это японское трудолюбие может съесть самые интересные жизненные впечатления.
Давайте посмотрим два видеоролика, которые мастер выложил для гостей своего канала на Ютубе.
Часть 1.
Часть 2.
com/embed/bTqdmZ1SCHc»>
Изготовление стелек и колодок
Сегодня мы расскажем о современных методах изготовления индивидуальных ортопедических стелек.
В рамках основы изготовления индивидуальных ортопедических стелек мы подготовили комплексное решение из специализированного 3D сканера для стопы, CAD/CAM решения — проектирование стелек на основе сканированных данных и подготовка управляющих программ. Завершающим этапом является изготовление стелек на фрезерных станках серии Charly 4U/2U.
Разберем подробнее каждый этап изготовления:
01. Сканирование стопы
Для сканирования стопы необходимо использовать специальный аппарат, мы сделали выбор на сканере RS SCAN iQube. Данные сканеры имеют 3 модификации:
- сканер iQube mini — компактный, легкий, быстрый и точный сканер с 1 камерой, созданный специально для мобильного использования. Он имеет точность сканирования 1 мм.
- сканер iQube — портативный, с интегрированной платформой, быстрый и точный. Он имеет точность сканирования 0,4 мм.
- сканер Tiger — высокоточный сканер, разработанный для ортопедов, производителей ортопедической обуви и стелек, а также для дизайнеров обуви. Может
- сканировать колодку, стопу, отпечаток и слепок стопы, стельки и обувь. Тако сканер имеет точность сканирования 0,5 мм.
Сканеры iQube, максимально просты в работе, а время сканирование стопы или слепка не превышает нескольких секунд, при высоком разрешении. Сканер, как и все элементы этого CAD/CAM комплекса обладает открытой архитектурой, и позволяет экспортировать данные в формате STL.
02. Моделирование стельки
03. Изготовление ортопедических стелек на фрезерном станке.
04. Завершает процесс изготовления стелек настольные станки серии Charly 4U/ 2U.
Эти станки имеют компактные размеры, закрытую область обработки с обзором 360*, что в свою очередь снижает уровень шума станка при обработке, обеспечивает безопасность. Предустановленная система аспирации позволяет производить отсос стружки из зоны реза, тем самым обеспечивая чистоту в рабочем процессе. Весь процесс изготовления стельки проходит в автоматическом режиме с использованием 1 или 2 инструментов. Изготовление пары индивидуальных ортопедических стелек на станке в занимает в интервале 5-15 минут и зависит от сложности профиля и размера самых стелек.
Кроме изготовления стелек, весь этот комплекс позволяет производить изготовление ортопедических колодок. Подготовка данных аналогична, но станок для этого необходимо доукомплектовать поворотной горизонтальной осью. После этого на нем можно выполнять полноценную 4-х осевую обработку изготавливая индивидуальные обувные колодки любых форм и размеров.
Мы тщательно следим за тенденциями и новыми современными технологиями. Подписывайтесь на наши новости и узнавайте первыми о новинках, интересных новостях, применениях и тенденциях рынка.
Колодки для обуви за сутки
Необходимые материалы:
- Скотч узкий — для изготовления формы под заливку
- Пленка (например, пищевая) — подложка для формы
(для альтернативного варианта изготовления колодки вместо скотча и пленки — силиконовый герметик + растительное масло и пластиковый нож/лопаточка)
- Гипс — собственно для изготовления (отливки) самой колодки
- Палочки (деревянные или пластмассовые) — для удобства держания готовой колодки (можно использовать что-то другое)
- Ножницы (нож) — подручный материал
- Фломастер (маркер) — для разметки
- Клей — для крепления подошвы и держателя
- Калька (бумага) — для выкройки подошвы
- Картон — для формирования подошвы
- Выравнивающая шпатлевка «Аква»- для доводки колодки
- Шкурка (на бруске или листовая) — для доводки
- Шпатлевка по дереву (или акриловые краски) — для покрытия готовой колодки, чтобы не пачкалась.
- Лак — для окончательного покрытия.
- Вспомогательные материалы — тряпки, емкость для разведения гипса, подставка (поднос) и т.п.
Примерное время для создания колодок: 1-2 Недели
Этап 1 — Изготовление формы для заливки:
1. Поскольку ботинки редко кто одевает на голые ноги, то имеет смысл одеть на ножки куклы носочки. НО! этот вариант имеет один большой недостаток: при разрезании скотча можно разрезать и носки!!! (честно скажу: лично пару носочков испортила, но — зашила!) Так что кто за себя не ручается, может обматывать голую ногу (объём потом при доводке добавим!)
2. Оборачиваем ногу куклы пленкой, стараясь, чтобы складок было поменьше
3. Потом начинаем скотчем обклеивать обёрнутую ногу в самых разных направлениях. Наша задача — не должно остаться мест, не заклеенных скотчем, порядок обклеивания — любой, можно обрезать скотч (правда, этим очень не увлекайтесь!). Так бинтуем, бинтуем, бинтуем…Толщина готовой обклейки минимум 1.5 мм Могу сказать про себя: на три «скотчевых» ботиночка» у меня ушёл один моточек скотча целиком.
Так делаем обе ноги.
4. Затем фломастером проводим линию по центру «скотчевого ботиночка» сзади
5. Аккуратно разрезаем «сапожок» по намеченной линии. Вот тут главная засада — не разрезать носки, если вы их одели…
Вот фотографии варианта без носочка (все те же этапы)
Пленка:
Разметка разреза:
Сам разрез:
6. Потом аккуратно стягиваем «сапожок» с ноги и пытаемся удалить излишки пленки. Всю пленку, скорее всего, вы удалить не сможете, а образовавшиеся складочки на щиколотке и торчащие концы — запросто! Потом заклеиваем (постарайтесь потщательнее!) скотчем разрез. Мой совет: сначала пару маленьких поперечных кусочков, а потом кусочками подлиннее и изнутри, и снаружи, и вокруг щиколотки
Если удача была с нами, у нас должно получиться два вот таких «ботиночка»
Альтернативный вариант изготовления основы для колодки
Силиконовая форма для отливки. Отливка получается абсолютно точной. Этот способ, наверное, неплох для изготовления колодок модельных туфелек, одеваемых на голую ногу или тонкий чулок.
Процесс изготовления:
1. Ногу куклы (я надеюсь, вы понимаете, что отрывать ногу не надо! Я это делала только потому, во-первых, что она обратно легко ставится, а во-вторых, для наглядности!) лишаем обезжиренности. Что имею в виду? Вы знаете, что обычно в инструкциях к различным составам с хорошими адгезирующими свойствами пишут «поверхность обезжирить», так сказать, для лучшего схватывания. Но поскольку нам-то надо форму с ноги снять, то (на всякий случай!) я решила подстраховаться. Просто немного «смочила» палец растительным маслом и протерла кукольную ногу, излишки масла промокнула полотенцем (нога должна быть лишь ЧУТЬ-ЧУТЬ жирная!)
2. Затем наносим силиконовый герметик.
3. Буквально пять минут спустя, также «намасливаем» одноразовый пластмассовый ножик и разравниваем поверхность силикона (чтобы покрытие было одинаковым по толщине)
4. Минут через 40 (силикон немного схватился с внешней стороны) пальцами аккуратно обминаем форму
5. Теперь оставляем всё это для окончательной сушки дня на 3 или даже 4!!! Поскольку я делала сначала одну ногу для эксперимента, а сейчас для фотографирования и рассказа делаю вторую, то сведения эти уже проверены!
6. Когда форма высохла, также, как и скотчевую форму разрезаем силиконовую форму сзади, аккуратно стягиваем силиконовый сапожок.
Вот что должно получиться
Обращение к людям, трепетно относящимся к чистоте. Если вы ОЧЕНЬ щепетильны, подстелите что-нибудь на стол возле мойки. Но по своему опыту могу сказать, никакой такой особой грязи нет.
1. Разводим гипс в пропорции 1:1 Должен получиться такой качественный кефирчик или дешевая сметана, короче раствор должен тягуче литься. У меня мерный кувшинчик на 0.5 литра, так вот, я развожу половину кувшинчика — этого хватает за глаза!
2. Наливаем гипс в «ботиночки»
3. Пару минут ждём, можно как-бы чуть пальчиками пообминать ботиночки
4. И вставляем в центр приготовленные заранее палочки
Палочки нужны для последующей работы с колодками: поскольку ботиночки небольшие, так удобнее манипулировать. Сразу хочу сказать, что после полного высыхания гипса палочки могут выпасть, но останутся отверстия! Мы капнем туда клея «Момент» и вклеим палочки назад, так они будут стоять намертво!
Внимание Не выливаем оставшийся гипс в раковину! Ждём немного и вытряхиваем в помойное ведро!
5. Минут через 40 — через 1 час (вы увидите, что гипс хорошо схватился) аккуратно освобождаете отливки от скотчевого чехла
А потом… потом главное не потерять самообладания от того, что вы увидите!
Должно получиться что-то вроде этого
6. И теперь самое главное — положить ЭТО подальше до следующего вечера (или утра, если вы делали отливки утром). Короче — спрятать ото всех (и от себя тоже!) на 24 часа (время окончательного застывания гипса).
При альтернативном изготовлении силиконовой формы для ко лодки наши действия аналогичны уже описанным:
1. разводим гипс
2. заливаем форму
3. НЕ ЗАБЫВАЕМ вставить палочку!
4. Также через час снимаем форму с отливки
5. и оставляем для окончательной сушки.
Вот готовая отливка
Как видите отливка АБСОЛЮТНО идентична ноге. Несомненное преимущество — точность отливки, тут вам никаких складочек!
Теперь начинается самый долгий (и чего греха таить — нудноватый!) этап изготовления колодок.
Этап 3 — Доводка :
1. Берете выравнивающую шпатлевку (у меня «Аква» — это удобней в использовании: и водой можно смыть, да и безвредная она) и начинаете ПОСТЕПЕННО замазывать неровности. Я советую начать с подошв, когда мы с ними разберёмся, сможем ставить колодки как положено, а не пристраивать (увидев фото поймёте, о чём я!)
Кто когда-нибудь имел дело с краской или шпатлёвкой, знает, что лучше сделать три тонких слоя, чем один толстый! Поэтому — не бежим вперёд паровоза и делаем первый тонкий слой! Смачивая палец начинаем заполнять получившиеся при отливке неровности.
2. Потом самое главное — найти место, где никто из любопытствующих домашних не будет проверять «высохло» или «нет». Оставляем до завтра. Сохнуть.
3. Если вчера вы сделали, как я советовала, то есть подшпатлевали подошву, то сегодня надо как следует её отшкурить, всё время ставя на горизонтальную поверхность для того, чтобы убедиться, что колодочки стоят ровно, не заваливаются на какой-нибудь бок, что нет никаких «горбылей».
4. Потом обведите ногу куклы сначала на бумагу, вырежьте (дав небольшой (0.5 мм) припуск на свободу облегания). Примеряете, смотрите… Если надо, вносите исправления.
Момент довольно ответственный: сейчас мы закладываем основы нашего дальнейшего успеха, а именно — насколько хорошо будут сидеть потом наши ботинки!
5. Если вас все устраивает, обводите бумажную выкройку на картон. Картон должен быть не толстым, но достаточно прочным, не хлипким.
6. Намазываете картонную подошву клеем (я уже писала, я использую «Момент-кристалл») и приклеиваете к колодкам.
Дальнейшую доводку будем делать, уже учитывая нашу новую подошву, реально соответствующую кукольной ноге.
7. На сегодня — всё, оставляем колодки до завтра сохнуть!
8. Картонная подошва отлично приклеилась, и нужно немного долепить недостающие местечки (на предыдущей фотографии вы видели, что картонный край выступает за гипсовую отливку). На следующий день шпатлевка даст небольшую усадку, вот как это выглядит
9. Если есть небольшие трещинки, замазываем их и продолжаем доводить колодки.
10. Ещё чуть-чуть пошкурить, ещё чуть-чуть подмазать! И мы уже близки к завершению «доводки»! (тьфу-тьфу-тьфу, чтобы не сглазить!)
11. Когда получившийся результат нас устроит, обмазываем колодки шпаклёвкой по дереву. После «деревянной» шпатлёвки колодочки перестают пачкаться, как покрашенные. Вот, что у меня вышло
НО! Это делать совсем необязательно! Можно просто покрасить готовые колодочки, например, акрилом.
Этап 4 — Окончание работы:
Итак, доводка завершена. Осматриваем внимательно, что получилось: сбоку, сверху, сзади. Если всё более-менее симметрично,
1. покрываем первым слоем лака
2. Ждём, когда высохнет
3. Покрываем вторым слоем, если захочется — то и третьим.
4. Теперь самое главное — высушить как следует! Оставляем на несколько дней до полного высыхания лака.
А пока можно подготовиться к следующему мастер-классу по созданию выкройки и собственно самих ботиночек и рассмотреть мою коробочку со всем необходимым для изготовления обуви, пока лак сохнет у нас есть время дособирать всё необходимое!
5. В результате у меня (надеюсь, что и у вас тоже!) получились вот такие колодки
Алексей Гринев из Красноярска задает вопрос:
Решил заняться пошивом тапочек. Как и из чего можно сделать колодки для изготовления обуви, которые могли бы прослужить довольно длительное время?
Ответ эксперта:
Оптимальный материал для приготовления обувных болванок – дерево, обладающее твердостью, устойчивостью к воздействию влаги, хорошо поддающееся шлифовке. Такими свойствами обладает береза, бук, клен. В качестве заготовок лучше взять отрезки бруса 12х12 см. Для выбора длины можно использовать старую обувь подходящего размера и по ней отмерить необходимое расстояние.
Для работы понадобятся следующие инструменты:
- ножовка по дереву;
- киянка;
- набор стамесок, в том числе с закругленными резцами;
- топорик;
- рашпиль плоский и полукруглый.
Еще понадобится пара старой обуви, желательно спортивной (кроссовки), которая хорошо облегает ноги.
Пошаговая инструкция по вытесыванию колодок для изготовления обуви своими руками:
- На одной из сторон бруса карандашом обводится подошва кроссовка, а на боковых его сторонах вырисовывается профиль будущей обуви.
- Посередине нижней и верхней части проводятся центровые линии. Просверливаются два сквозных отверстия, которые помогут восстановить центровку в процессе обработки древесины резцами.
- С помощью ножовки и топорика удаляются излишки дерева на заготовке. При этом соблюдается осторожность, чтобы не срубить лишнего. Сначала выпиливаются крупные участки, потом скалываются более мелкие.
- Далее заготовка обрабатывается стамесками до придания формы, наиболее схожей по размерам с ногой. Во время работы необходимо постоянно сверять удаление оттачиваемых поверхностей от центра, чтобы не допустить изъяна на колодке.
- Окончательная шлифовка производится с помощью рашпилей и наждачной бумаги.
Если планируется использование каблука, то пяточная часть заготовки должна иметь соответственное углубление.
В таком же порядке изготавливается колодка для второй ноги. Процесс может показаться излишне трудоемким, но на выходе пользователь получит пару колодок, которые можно использовать на протяжении длительного времени и не только для изготовления тапочек. Каждая болванка может использоваться для пошива обуви только одного размера и одного фасона. Для других моделей понадобятся иные колодки, которые можно изготовить по такой же предложенной схеме с внесением соответствующих корректировок.
Видео: Станок для изготовления обувных колодок
Мастер-класс по производству обувных колодок из дерева от мастера Курокио (Япония)
Для производства колодок используют такие сорта дерева, которые позволяют колодке быть одновременно прочной, легко впускать в себя гвозди, а также не менять существенно свой размер при попадании на них влаги. Всем вышеперечисленным требованиям удовлетворяют такие сорта дерева как бук, граб, береза, липа и клен.
Мастер Курокио не говорит какой сорт дерева он использовал, но, возможно это как раз один из вышеперечисленных сортов.
Курокиосан не комментирует свой видеоурок, но мы попытаемся по шагам разобраться в последовательности ручного изготовления обувных колодок.
1.
Прежде всего для изготовления пары деревянных обувных
колодок потребуется два куска дерева, предпочтительно квадратного сечения размером примерно 15х15см . Опять же необходимо понимать какого типа колодка должна получиться — если сапожная, то горловина должна быть повыше примерно на 3 см по сравнению с туфельной колодкой. Т.е. для туфельной колодки и первоначальное сечение бруса могло быть и поменьше, например 12х12см .
2.
На боковые грани
заготовки необходимо нанести первоначальные грубые зарисовки бокового профиля и профиля подошвы. Для этого необходима первичная подготовка поверхности с помощью рубанка по дереву.
Для нанесения
перпендикулярных характерных линий хорошо использовать металлический угольник, а рисовать можно тонким маркером или гелиевой ручкой (как у мастера Курокио) темных цветов.
3.
И вот профили боков
и подошвы нанесены. Что же будет далее? А далее Курокио-сан берет ту же самую пилу, которой пилил исходный брус и спиливает большой кусок дерева, в носочной области. Колодку при этом неплохо бы зажать в большие столярные или слесарные тиски, чтобы обеспечить безопасность работы.
4.
Какие инструменты использует мастер-колодочник?
В основном это инструменты
для резьбы по дереву — топорик, стамески, рубанки, рашпили. Обратите внимание, что мастер Курокио большую часть работы будет делать круглыми резцами, т.к. в некоторых местах колодка не только бывает выпукла, но и вогнута как-бы внутрь. Вот там-то и придут на помощь круглые резцы, т.к. плоский резец просто срезал бы много нужного материала.
И вот, работа резцами пошла.
Сначала можно
срезать самым большим плоским резцом-стамеской. Работа стамеской в большинстве случаев сопровождается легкими ударами молотком по торцу стамески.
Вот так выглядит заготовка с выбранной носовой частью.
5.
Переворачиваем колодку и, согласно боковому профилю
формируем пяточный
подъем, который необходим, для установки каблука заранее рассчитанной высоты. Работать в этом месте удобней плоской стамеской. В завершение этого этапа угловой переход можно скруглить на шлифовальном станке, что и показывает нам мастер Курокио. После шлифовки необходимо повторно нанести профиль подошвы, т.к. предыдущий профиль был стесан вместе с деревом.
6.
Далее необходимо убрать много лишнего
материала с боков, особенно ближе к пяточной части
колодки, поэтому Курокио-сан решил использовать для этого небольшой японский тамагавк.
7.
Аналогично, мастер-колодочник срезает дерево и с боков в
носочной части заготовки колодки.
После этого этапа колодка приобретает очертания, напоминающие валенок.
8.
Пришла пора поработать как раз в той области, где колодка имеет
вогнутости. В этих местах никак не получится работать плоскими стамесками, т.к. необходимо делать рез только в узкой
области вдоль траектории резца. Приходится использовать круглый большой резец. Им мастер обрабатывает места в районе подъема колодки и в пяточной области в районе лодыжек.
Вот так причудливо выглядит колодка после того как по ней прошлась круглая стамеска.
9.
Очень важно при ручной
обработке обувной колодки не потерять линию симметрии. Для этого всякий раз, когда возникает возможность срезать или сошлифовать линию середины колодки, можно заранее поставить центровочные шпильки, которые в дальнейшем позволят восстановить утерянные линии.
10.
Опять обращаемся к шлифовальному станку, чтобы подравнять ненужную рифленость.
11.
По мере того как очертания колодки приближаются к заданным размерам нужно переходить к более точным инструментам. В данном случае — это рашпили с различным рисунком рабочей части. Опять же видно, что понадобятся не только плоские но и рашпили с полукруглым профилем.
Вот видно, как Курокио-сан обрабатывает пяточную часть подошвы рашпилем.
12.
Настала пора позаботиться о выпуклости подошвы. Посмотрите какой инструмент для этого использует Курокио — обычный остро заточенный сапожный нож. Японский иероглиф обозначает
верхнюю точку выпуклости.
13.
А вот выпуклость в носочной области мастер делает уже небольшим закругленным рубанком. Здесь нет жестких правил каким делать
инструментом ту или иную обработку. Каждый мастер вправе выбирать тот инструмент, который для него наиболее удобен.
14.
Итак до заданного профиля подошвы остались
считанные миллиметры. Теперь нужно быть предельно осторожным и внимательным. Посмотрим, справится ли мастер Курокио с этим ответственным этапом.
Да, он опять пошел на хитрость — обратился к шлифовальной машине, т.к. она обеспечивает хоть и не такой быстрый съем материала как стамеска, зато более контролируемый. Мастер четко представляет в какой момент какой инструмент нужно применять. После обработке на шлифовальном станке колодка уже начинает походить на колодку.
15.
А теперь повторяются некоторые операции, но уже резцами меньших размеров, а значит мастер
более точно и медленно приближается к нужным размерам. Можно позавидовать терпению мастера Курокио-сан, когда ему снова и снова приходится делать похожие операции но с более «точным» инструментом.
После обработки на шлифстанке колодка уже готова. Но что это? На подошве обнаружился по всей носовой части один лишний миллиметр! Опытная рука мастера удаляет его круглым рубанком. Несколько плавных движений руки с мелкой наждачной бумагой,
чтобы устранить микроскопические неровности. И это был последний, завершающий, победный штрих!
Ура!!! Колодка на 1000 долларов готова! Вот она держите, господин заказчик! Таких колодок, точно под Вашу ногу нигде и никто так классно не сделает! Хотите заказать еще? Жене и детям? Запишитесь пожалуйста в список — Ваш номер 374. Приходите через 4 месяца.
Вот так и живет и работает профессионал-колодочник из Японии Курокио-сан.
Пожелаем ему успехов, удачи, любви, здоровья и пусть хоть иногда устраивает себе выходные, а то это японское трудолюбие может съесть самые интересные жизненные впечатления.
Давайте посмотрим два видеоролика, которые мастер выложил для гостей своего канала на Ютубе.
Часть 1.
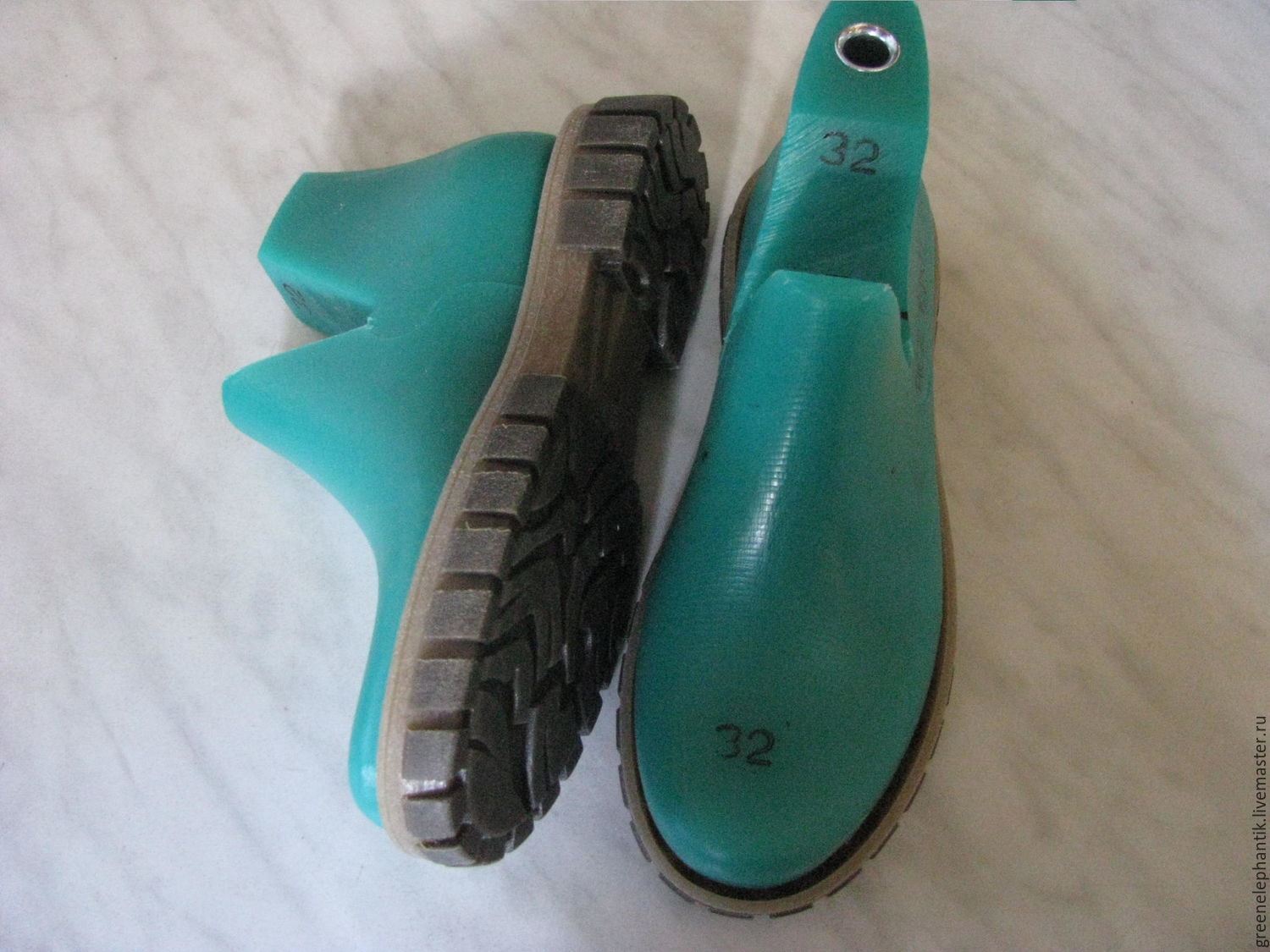
Часть 2.
Что мы делаем, когда нам нужна обувь? Многие, покрутив у виска, посчитают это глупым вопросом. Ведь сколько существует магазинов, палаток и торговых точек с обувью, и есть они практически в каждом городке.
А как на счет самостоятельного изготовления туфлей, ботинок, тапочек? Здесь вряд ли останется много героев, способных пройти весь трудный путь по созданию обуви своими руками. Даже несмотря на существование фото и видео мастер-классов, этот вопрос требует особого щепетильного отношения. Хотя не всегда для того, чтобы пошить такую вещь, нужен богатейший опыт, достаточно простой усидчивости и большого желания.
Посмотрим, какую обувь можно сделать в домашних условиях.
Вязаные тапочки
Самый простой и удобный вид уютных и комфортных тапочек. Для этого необходимо лишь пару листов плотного картона, ткань, нитки и умение связывать петли. Причем необязательно использовать спицы, можно орудовать и обыкновенным крючком.
Лучше, конечно, использовать фотосхемы, по которым удобно вязать, но с другой стороны, можно это делать самыми обыкновенными техниками, просто предварительно сделав подошву, и уже по ней начинать вязку.
Для того чтобы сделать подошву, следует обвести на одном листке картона стопу (то есть понадобится 4 листа картона на обе ноги).
После этого вырезать формы и склеить между собой.
Затем обтянуть тканью (лучше использовать натуральную, чтобы было комфортно ногам) и сшить. Таким образом, подошва готова. После уже приступать к вязанию.
Тем, кто ни разу не сталкивался с вязанием, стоит посоветовать посмотреть тематическое видео или фото. И для начала попробовать себя в более легких вещах, просто связать несколько петель. А после уже приступать к тапочкам.
Более сложные варианты
Конечно, речь пойдет о туфлях. В этом случае понадобятся дополнительные инструменты, материалы, а также правильные выкройки. Если домашние мягкие тапочки, в случае небольших огрехов при вязании, все равно примут форму ноги, то, в случае с неправильным пошивом твердой обуви, результат вряд ли порадует. И носить такие вещи будет невозможным.
Попробуем коротко рассказать, из чего состоит пошив туфлей своими руками, а вот приступать к делу все же рекомендуется, посмотрев соответствующие материалы.
Самой важной частью изготовления обуви являются колодки. Это и есть основа любых туфлей, к производству которой особые требования. Чтобы изготовить правильно обувь недостаточно просто сделать выкройку, необходимо качественно и правильно соединить все элементы и работать с колодками.
Колодки можно сделать своими руками или купить уже готовые под определенный размер. Именно этот «обувной манекен» позволит качественно сделать первоначальные этапы и части туфлей.
Для того чтобы создать форму, можно вырезать ее из дерева, но процесс достаточно сложный, в особенности для новичков. Можно использовать старые туфли, предварительно сделав их жесткими, но такой вариант также не даст хорошего качества. Поэтому лучше обратиться в специализированный магазин, и купить эту деталь, а еще лучше в дополнение и удобную подставку к ней.
После того, как колодки готовы, можно приступать к выкройкам. Для этого нужно сделать лекало.
Колодку обклеить бумагой или скотчем, и на нем нарисовать форму будущей обуви. После чего перенести чертеж на материал изготовления. Кстати, о материале. Первоначально лучше всего использовать кожу, ее жесткость позволит лучше придать туфлям форму. Причем для заготовки подошвы лучше использовать специальный вид кожи, называется «чепрак» и делается из самой жесткой части коровьей шкуры.
Перенеся лекало на материал верха, то есть более мягкую кожу, можно делать выкройку, то есть вырезать. Далее внутренняя часть подошвы подгоняется по размеру, делается она по колодке или же очерчиванием собственной ноги, в случае необходимости, подрезается. Потом верх натягивается на колодку и подошву. Крепится сначала небольшими гвоздями, после чего скобами и уже потом проклеивается с использованием специальной декоративной окантовки и полиуретанового клея.
Гвозди потом необходимо вытащить, а туфель снять с колодки, но делается это уже после крепления основной подошвы. Также стоит отметить, что для низа можно использовать другой материал, например, резину, полимерные заготовки или тот же полиуретан. Все зависит от сезонности обуви и от предъявляемых к ней запросов.
Основная подошва сначала крепится, а уже потом специальным обувным ножом подрезается и подгоняется непосредственно под туфли.
Каблук – заключающий этап. Конечно, новичкам шпильку будет сделать достаточно трудно, а вот широкий и низкий «мужской вариант» — вполне возможно. Он также сначала подрезается по внутренней стороне, а затем уже подгоняется по подошве и заднику.
Надоело пропускать премьеры в кинотеатре из-за бешеного ритма жизни? Устали от того, что по телеканалам стоящие фильмы транслируются в неудобное для Вас время? В Вашей семье часто родные делят пульт от телевизора? Ребенок просит посмотреть мультфильмы для детей, когда Вы заняты, а на каналах нет хороших мультфильмов? И, в конце концов, Вы просто хотите расслабиться после трудового дня на диване в домашней одежде за просмотром интересного фильма или сериала?
Для этого лучше всего иметь всегда в закладках любимый сайт, который станет для Вас лучшим другом и помощником. «А как же выбрать такой сайт, когда их так много?» — спросите Вы. Лучшим выбором для Вас будет именно наш видео сайт
Почему именно наш ресурс? Потому что он объединяет в себе множество положительных особенностей, которые делают его универсальным, удобным и простым. Вот список основных преимуществ ресурса.
Бесплатный доступ. Многие сайты просят клиентов покупать подписку, чем наш портал не занимается, так как считает, что у людей должен быть свободный доступ в сети интернет ко всему. Мы не берем с наших зрителей плату за просмотр!
Не нужно никакой регистрации и СМС на сомнительные номера телефонов. Мы не собираем конфиденциальную информацию о наших пользователях. Каждый имеет право на анонимность в интернете, что мы и поддерживаем.
Отличное качество видео. Мы загружаем материалы исключительно в HD формате, что, безусловно, способно порадовать любимых пользователей. Ведь гораздо приятнее смотреть хороший фильм с качественной картинкой, чем с изображением низкого качества.
Огромный выбор. Здесь Вы найдете видео на любой вкус. Даже самому заядлому киноману всегда найдется, что посмотреть у нас. Для детей есть мультфильмы в хорошем качестве, познавательные программы о животных и природе. Мужчины найдут для себя интересными каналы о новостях, спорте, автомобилях, а также о науке и технике. А для наших любимых женщин мы подобрали канала о моде и стиле, о знаменитостях, ну и конечно музыкальные клипы. Устроив вечер в кругу семьи, или с друзьями Вы сможете подобрать веселую семейную комедию. Влюбленная пара понежиться за просмотром любовной мелодрамы. После рабочего дня расслабиться помогает захватывающий сериал или детектив. Фильмы в HD формате нового времени и прошлых лет представлены на абсолютно любой вкус и могут удовлетворить потребности любого зрителя.
Возможность скачивать видео. Абсолютно любой материал на сайте можно скачать к себе на компьютер или флешку. Если вдруг Вы соберетесь на дачу с ноутбуком, где нет интернета, или захотите посмотреть фильм на большом экране телевизора, то Вы всегда можете заранее скачать, а после посмотреть в нужный момент. При этом Вам не придется ждать своей очереди, чтобы скачать видео, как это бывает на торрентах или других похожих сайтах.
Безопасность. Мы следим за чистотой контента, каждый файл перед закачкой проверяется. Поэтому на нашем сайте нет никаких вирусов и шпионских программ, и мы тщательно следим за этим.
Новинки. Регулярно мы обновляем и добавляем на портал новые мультфильмы, сериалы, ТВ-шоу, музыкальные клипы, новости, обзоры, мультсериалы и т.д. и всё это Вы можете посмотреть совершенно бесплатно, без регистрации и смс. Мы стараемся для Вас, для наших любимых посетителей.
Онлайн-просмотр. На нашем сайте не обязательно предварительно скачивать фильм, чтобы его посмотреть, достаточно просто включить и наслаждаться просмотром. Благодаря профессиональной настройке не будет никаких торможений, и ничто не сможет Вам помешать посмотреть интересный фильм.
Закладка. На сайте можно нажатием одной кнопки со звездочкой отравить видео в закладки и вернуться к нему позже. У каждого, наверняка бывало, что увидел на сайте интересное видео, которое хочешь посмотреть, но прямо сейчас нет возможности. Данная кнопка поможет Вам в этом и, освободившись, Вы с легкостью сможете посмотреть, то что хотели.
Удобный интерфейс. Поиск нужного видео не займет у Вас много времени, так как сайт лучшим образом адаптирован для пользователей, и всё интуитивно понятно. Даже ребенок сможет разобраться и включить для себя мультфильм или какую-нибудь программу о животных, природе.
Кино как искусство появилось сравнительно недавно, но уже успело тесно переплестись с нашей жизнью. Множество людей из-за спешки нашего времени уже годами не ходили в театр, в галерею или музеи. Однако трудно себе представить человека, который не смотрел сериал или фильм хотя бы месяц. Киноискусство является синтезом театра, музыки, изобразительного искусства и литературы. Таким образом, оно дает даже самому занятому человеку, у которого нет времени ходить по театрам и галереям, быть ближе к искусству и духовно совершенствоваться.
Также кино заняло сферу и общедоступного развлечения. Просмотр комедий, боевиков, вестернов и т.д. отлично вписывается в какой-нибудь вечер в кругу семьи. Ужастики отлично щекочут нервы даже самого бесстрашного человека. Мультфильмы обожают дети, а некоторые можно смотреть и всей семьей. Познавательные видео помогают расширить знания, посмотреть на мир шире и удовлетворить собственное природное любопытство.
Человек в двадцать первом веке уже не может представить свою жизнь без технологий будущего, кажется, в будущем машины, роботы и техника смогуд заменить человека, а точнее выполнение многих автоматических работ, по этому каждый хочет смотреть какие технологии будут в будущем. На сайте Вам и не нужно откладывать просмотр, просто добавьте видео в закладки и в любой момент можете к нему вернутся и отлично провести время за просмотром качественного видео.
Не отказывайте себе в удовольствии, начните смотреть уже прямо сейчас! Знакомьтесь с обновлениями, с новинками, выбирайте то, что хотели бы посмотреть позже. Порадуйте себя и близких интересными фильмами в хорошем качестве!
Поделись статьей:
Похожие статьи
Как делают колодки
Накладки для обуви являются отправной точкой для любого проекта по дизайну обуви и имеют решающее значение для формы и функций всех типов обуви. Последний используется обувной фабрикой для определения формы обуви. Последнее также определяет посадку, характеристики, эргономику и стиль обуви. Круглые пальцы ног, заостренные пальцы, низкий каблук или высокие каблуки — все эти атрибуты определяются последней обувью. Эти атрибуты делают различную обувь подходящей для бега, баскетбола, пеших прогулок или высокой моды.Когда обувь находится в руке последней, мастер выкройки создает выкройку обуви, которая плотно прилегает к последней. Как только дизайн подтвержден, выкройки сортируются после последнего для каждого размера обуви. Обувные колодки могут быть изготовлены из литого пластика, резного дерева или литого алюминия.
При обсуждении атрибутов последнего вам необходимо знать общие термины. Большинство измерений — это объем, а не традиционные длина и ширина, связанные с посадкой обуви.Нажмите здесь, чтобы узнать, как измеряется срок службы обуви
Последнее изготовление — это искусство.Опытный изготовитель последнего будет иметь многолетний опыт работы и, возможно, окончил школу изготовления последнего. Делая последнюю, необходимо учитывать анатомию стопы, особенно то, как форма стопы изменяется при сгибании. Когда колодки разрабатываются для нестандартной обуви, необходимо учитывать каждый размер стопы клиента и желаемый стиль.
Последние типы обуви:В зависимости от стиля обуви, которая производится последней, потребуются некоторые специальные функции, чтобы обувь могла освободить последнюю.В стандартной спортивной обуви с плавающим язычком на шнуровке можно использовать прочную колодку. Мокасам, оксфордам и ботинкам потребуется резиновая накладка, которая может быть шарнирно сочлененной, чтобы обувь не повредилась во время износа.
Твердые колодки для обуви: Самый распространенный тип колодок для обуви. Цельные колодки могут быть изготовлены из пластика, алюминия или дерева.
Накладная колодка на петлях: Накладная колодка на петлях часто используется для изготовления тонкой кожаной обуви. Последний может регулироваться, что позволяет легко снимать.
Совок Последний: Подъемник в совке является съемным, что позволяет придавать форму конусу обуви.
Телескопическая Последняя: Последняя телескопическая телескопическая труба, используемая для высоких ботинок, разделяется на части, что позволяет легко снимать.
Деревянная обувь для обувиДеревянная колодка для башмаков может быть изготовлена на токарно-копировальном станке, фрезеровании с ЧПУ и даже ручной резьбе.
Плюсы: Отлично подходит для ручного, индивидуального или индивидуального пошива обуви.Легко настраивается с помощью ручных инструментов и может быть изготовлен под конкретного клиента. Деревянная поверхность подходит для гвоздей и гвоздей, необходимых для изготовления обуви на заказ. Идеально подходит для обуви ручной работы за высокие деньги или последней проверки ручной работы. Деревянная колодка может быть цельной, навесной, совковой и телескопической.
Минусы: Деревянные колодки дорогие, хрупкие и подвержены короблению и гниению в сыром виде. Они не согласны с тепловыми туннелями или вулканизационными печами. Деревянные колодки неприемлемы для современного массового производства.
The Plastic Последний:Современная пластиковая колодка для обуви изготовлена из полиэтилена высокой плотности (HMW-HDPE), что позволяет заделать множество прихваток, прежде чем потребуется ремонт. Пластиковая пластина изготавливается путем введения пластиковой «заготовки», имеющей примерно форму каждого размера. Эти пластиковые заготовки затем обрабатываются (или режутся) на станке для резки (или токарном станке) с компьютерным управлением. В процессе токарной обработки колодки проходят черновую резку на высокой скорости, а затем перемещаются на другой станок для окончательной обработки.После поворота носок и пятка обрезаются пилой, а затем шлифуются до окончательной формы.
Плюсы: Пластиковые колодки для обуви — это новейшее достижение в современном обувном производстве. Легко изменить форму для испытаний на подгонку, колодки можно обрабатывать, шлифовать и подпиливать. Пластиковые колодки компьютерной обработки могут быть очень точными для точной подгонки. Легко выпускается в массовом производстве, невосприимчив к жаре и влаге. Пластиковая колодка — это рабочая лошадка современной фабрики качественных кроссовок. Пластиковая накладка может быть сплошной, навесной, совковой и телескопической.
Минусы: Пластиковые колодки могут быть дорогими. Они очень прочные, но при неосторожном обращении на них могут появиться сколы, вмятины и царапины. Пластиковые колодки больших размеров для сапог могут быть тяжелыми и трудными для рабочих. Пластиковые колодки нельзя использовать в вулканизационных печах. Их переработка может быть более дорогой, поскольку их необходимо измельчать и переплавлять.
Конец алюминиевыйЧаще всего используется в производстве обуви, литые алюминиевые колодки больших размеров удобны в обращении.Часто используется для изготовления зимних ботинок и резиновых сапог в стиле веллингтона. Серийно производимые на довольно примитивных литейных заводах, литые алюминиевые колодки производятся полыми в формах для литья в песчаные формы.
Плюсы: Литые алюминиевые колодки для обуви дешевы, просты в массовом производстве и непроницаемы для тепла и влаги. Металлическая колодка необходима для производства вулканизированной обуви. Он идеально подходит для небольших серий, легко перерабатывается, изготовлен из легкого алюминия. Литой алюминий также очень прочен.
Минусы: Форма не такая точная, как дерево или пластик. Не так-то просто содержать в чистоте. Качество может быть подозрительным. Необходимо следить за изменением размеров. Шероховатые поверхности могут повредить футеровку.
Посмотреть, как изготавливаются колодки, можно здесь. Наконечник для 3D-печати можно скачать здесь.
The Shoe Last Глава 13Чтобы узнать больше о дизайне колодок, производстве колодок, деревянных колодках, пластиковых и металлических колодках, ознакомьтесь с главой 13 книги
«Как делают обувь».
Как это:
Нравится Загрузка …
Долговечность обуви закладывает основу для хорошей обуви
Обувные колодки закладывают основу для создания качественной мужской обуви. Идеально подобранная обувь может быть получена только с использованием идеальной колодки. Обувные колодки уже использовались в древности, но быстро канули в Лету. Лучшие колодки изготавливаются из древесины бука.
Накладки для обуви представляют собой трехмерные формы, похожие на упрощенные человеческие ступни, и обычно изготавливаются из дерева.Мужская обувь строится на основе долговечности на более поздних этапах изготовления обуви. Таким образом, колодки являются чрезвычайно важным элементом изготовления обуви. Идеально подобранная обувь может быть получена только с использованием идеальной колодки. Принятие во внимание подушечек стопы, пяток и подъема стопы, а также того, как высота пятки изменяет перекатывающее движение стопы, определяет посадку готовой обуви.
колодки использовались в древности, но канули в лету
Археологические находки подтвердили, что древние римляне использовали колодки для изготовления обуви.В какой-то момент эти знания были утеряны и не были восстановлены до средневековья, когда сапожники снова начали использовать колодки для изготовления обуви. Искусство последней асимметрии также было утеряно и позже восстановлено. Древние греки и римляне учитывали разницу между левой и правой ногой, тогда как более поздние сапожники измеряли только одну ногу и использовали это измерение для изготовления обуви для ножек кабин. Естественно, такая практика приводила к значительному дискомфорту при ношении. В начале 19 века асимметричные колодки были заново открыты и стали использоваться, как и прежде, для обеспечения идеальной посадки обуви.
Люки из медного бука и граба.
.Для изготовления долговечных изделий используется только самая лучшая древесина. Во время обработки и хранения древесина должна выдерживать высокое давление, удары молотка, забивание гвоздей, влажность и колебания температуры. Породы древесины, которые соответствуют этим критериям, включают буковую древесину, клен, дуб, вяз и орех. Однако лучший выбор — медный бук и граб.
В последней мастерской изготовителя бревна распиливают на куски длиной примерно 32 см.Эти детали также имеют толщину от 30 до 40 см, а это значит, что из каждого куска дерева можно сделать от четырех до шести колодок. Затем древесину пропаривают при температуре 120 градусов и оставляют сушиться примерно на два года. В конце этого периода влажность древесины составляет всего от 16 до 18 процентов. Однако для дальнейшей обработки эту долю необходимо уменьшить до 10–12 процентов. Это достигается за счет использования сушильной камеры, в которой древесина, из которой будут изготовлены балки, обрабатывается горячим воздухом в течение трех недель.
Колодки можно использовать много лет
В то время как предыдущие производители когда-то делали изделия исключительно вручную, сегодня последние производители по всему миру используют так называемые принтеры. Древесина закрепляется на токарном станке в принтере, и подбирается последний шаблон, соответствующий желаемому типу и размеру обуви. Затем принтер производит пару асимметричных листов в течение пяти-шести минут.
Изготовители последних вручную добавляют последние штрихи к печатным колодкам. Последний изготовитель отпиливает биты, используемые для крепления дерева к подноску и пятке, и просверливает несколько горизонтальных отверстий в верхней трети последнего, что облегчает удаление последнего из пришитой обуви и вокруг него.Последний производитель также отпиливает от последнего клин с тонкой изогнутостью, чтобы облегчить удаление последнего, когда последний выполнил свою задачу по изготовлению обуви.
Последняя передается сапожнику, который оставляет последнюю готовую. Он будет использовать его для тестирования прототипов обуви и, в случае проблем с обувью, сделанной из последней, попросит последнего производителя внести коррективы. Если сапожник заканчивает изготовление обуви из последней, он кладет ее на хранение. Качественные колодки могут служить долгие годы при условии, что они хранятся в помещении при соответствующей температуре и уровне влажности.
CalexFit, Центр обезболивания стоп — Библиотека
CalexFit, Центр обезболивания стоп — Библиотека — колодки для обуви и метрологияБашмаки и метрология
Большая часть обуви сделана на износ. Это модель стопы с размеры и форма аналогичны анатомической стопе, но существенно отличаются чтобы не быть точным. Подгонка обуви и в некоторой степени последнее влияет на ее долговечность.
Традиционно до массового производства оригинал Сапожник начал процесс с контура подошвы.Он вырезал или выточил деревянную колодку от отпечатка. Последний (‘последний’, Старый Английский означает след) традиционно делали из дерева, но теперь теперь доступны в металле или пластике. Это сложные конструкции из множество измерений (определяется статистически). Плечи не одинакового размера и размеры анатомической стопы, но вместо этого абстрактная форма с специфические функции. Обычно он глубже в области среднего отдела стопы, имеет резкий «край пера», где верхняя поверхность встречается с подошвой, защелкивается вдоль линия верха (вокруг щиколотки) зачесана и расширена в пальце ноги область, край.Это обеспечивает форму, которая обеспечивает соответствующее натяжение, когда обувь деформируется, чтобы удерживать нагруженную ногу. Lasts обеспечивает рабочую поверхность на каким плоским кожаным компонентам можно придать пластиковую форму. Физический размеры соответствуют ступне во время активности, а последняя содержит современная мода и стили, такие как форма мыска. Позволить последнему быть снятые с обуви, они часто навешиваются вокруг подъема стопы. Обувь длится сделаны не так, чтобы походить на ступни, а должны подходить производителю обуви.Современные колодки совершенно не похожи на стопу с подошвой последних, плоской чтобы помочь в производстве. Производство обуви было отнесено к трем товарные позиции: точеная обувь, прорезная обувь и обувь со сквозным швом.
Башмак точеный
Башмак точеный сделан наизнанку только с вылетом подошва между ступней и землей. Верх и подошва очень гибкий. Последняя разрабатывается в едином размере, а затем изготавливается набор в диапазон размеров и ширины, в которых будет изготавливаться обувь.Маркированные размеры могут незначительно отличаться от одного производителя к другому. Нет уже давно популярная техника.
Антропометрия
Исследования показывают, что более 90% людей имеют разный рост. ноги. Несмотря на то, что ножки имеют одинаковую длину, другие размеры меняются в зависимости от индивидуальная ступня. Активность стопы также изменит форму идентичные ножки в соответствии со структурой и функцией придаток. Идея идеальной посадки не реальность.Потому что распространение или пропорции массы стопы различаются у разных людей, что означает линейную измерения, такие как длина и ширина только стопы, неадекватны. Это Важно, чтобы сапожники учитывали массу и объем стопы, если быть предоставленным. Чтобы обеспечить наилучшее соответствие, измерения проводятся на стратегических предприятиях. местоположения, и сапожник использует как линейное измерение, так и измерение объема, чтобы построить обувь. Современный последний выполнен в трех измерениях, хотя и не прямая копия стопы.Вместо этого это сделано с производством требования, в виду. Последний может произвести до 35 измерений перед модель последняя может быть изготовлена. Слесарь-обувщик может сосредоточиться на длине, мяче ширина, пятка, линия верха, свод и подъем. Ожидается, что обувь будет хорошо носить, хорошо себя чувствуют, при ношении держат форму, сохраняют стилевой характер, проступают должным образом, обеспечить разумную свободу стопы, ухаживать за ступней и обувью баланс, остаются структурно нетронутыми. Эти функции не всегда зависят от качества материалов или компонентов или производственного процесса.В конструкция и многочисленные размеры последнего служат основанием для вышесказанного.
Функции, встроенные в последнюю, включают:
Измерения
Большинство измерений — это объем, а не традиционные длина и ширина связаны с посадкой обуви.
Обхват мяча Это размер обхвата вокруг мяч последнего для определения припуска по ширине и объему внутри обувь.
Обхват талии Обхват талии по последней.
Обхват стопы Окружность стопы на подъеме.
Обхват пятки Расстояние вокруг стопы от заднее основание пятки до подъема стопы.
Обхват стопы
Произведено четыре измерения обхвата и окружности. на последнем. Это мяч, талия, подъем и пятка (от пятки до пятки). в ногу).Измерение требует тщательной оценки стопы, которая не может быть выполнено с той же точностью, что и линейные измерения. Современный последний производитель использует точные инструменты для определения обхвата, но старый сапожники использовали маховик для того же эффекта.
Отступающий носок
Это та часть последнего, которая выходит за пределы кончики пальцев, образующие округлый контур передней части обуви. А конусообразный отступ, например, в сегодняшней острой обуви, увеличивает общую длину обуви.В плохо спроектированной колодке отступ может зайти на пальцы ног. усиление напряжения на концах пальцев ног. Это можно назвать плотным прочный.
От пятки к мячу
Это определяет положение шарнира передней части стопы (плюсневые фаланговые суставы) и самая широкая часть обуви (поперек головки плюсны).
Пружина пальца
Это описывает высоту нижней поверхности подошва у мыска, чтобы придать обуви легкий рокерский эффект.Количество Пружина носка (встроенная в колодку) зависит от фасона обуви, толщины подошвы и высота каблука. Это встроено в последнюю конструкцию и компенсирует жесткость обуви и обеспечивала беспроблемный взлет в двигательная установка. Чем жестче материал подошвы, тем больше пружина носка. Многие туфли также имеют небольшую пружину на пятке.
Протектор
Обозначает ширину подошвы под мячом. последнего и он должен соответствовать размеру стопы.Протектор точка на последнем представляет нижнюю переднюю часть сразу за мячом и в контакт с базовой плоскостью.
Под факел
Это описывает кривую или контур последнего. В замах определяется положением передней части, когда последняя пополам продольно вперед от центра пяточной дуги. В inflare длится, наблюдается внутренний поворот медиальной части к передней части и большая часть современные туфли сделаны на накидных колодках (банановые накладки), потому что это считается обувь более удобная.Последняя вспышка описывает обратное с махи лежа на боковую сторону передней части. Иногда используется в сделанных на заказ обувь для младенцев с диагностированными проблемами развития стопы. Прямые last не описывают ни предпочтения в отношении вспышки, ни вспышки. Длинная ось последний, проведенный через пополам изгиба пятки, описывает два равные продольные половинки. Нормальная стопа имеет прямую ось и, следовательно, прямую обувь можно носить на любой ноге. До введения машин для изготовления туфель на каблуках было обычным делом прямая ракета вплоть до рубежа ХХ века.
Все о обуви: колодки и метрология
(последнее изображение обуви через Pinterest)
«Тесные отношения между мужчиной и его обувщиком основывались на общем секрете измерений клиента. Статистика клиентов никогда не разглашалась».
Большая часть обуви изготавливается на последней, которая представляет собой модель ступни с размерами и формой, аналогичными анатомической ступне, но достаточно отличающимися, чтобы быть точными. Последний подходит для производства обуви и в некоторой степени влияет на окончательную посадку и долговечность обуви.
Last
Перед массовым производством производитель обуви начал процесс изготовления обуви с контуров подошвы. Деревянный брусок (последний блок) был вырезан или вырублен в деревянную планку с отпечатка. Вначале последний («лаэст», древнеанглийский означает след) был сделан из дерева, но теперь он сделан из металла или пластика. Это сложные конструкции, составленные из множества размеров стопы. Готовые колодки — это не точный размер и размеры анатомической стопы, а абстрактное представление с конкретными функциями.Обычно он глубже в средней части стопы с острым «краем пера», где верхняя поверхность встречается с подошвой. Последняя обрезается по линии верха (вокруг щиколотки), расширяется и расширяется в области пальцев. Это обеспечивает форму и соответствующее натяжение, когда обувь деформируется, чтобы удержать нагруженную ступню. Плашки дают рабочую поверхность, на которой плоским кожаным деталям можно придать пластиковую форму. Физические размеры соответствуют ступне во время активности, а последняя соответствует современной моде и стилям, таким как форма пальца.Чтобы последние можно было снять с обуви, их часто навешивают вокруг подъема стопы. Современные колодки совершенно не похожи на стопу с подошвой последних, плоской для облегчения производства. Последний — самый важный элемент в процессе изготовления обуви. Последние производятся на основе измерений, чтобы гарантировать правильный размер и посадку обуви, включая характеристики протектора и обуви. Стандартные измерения включают обхват мяча, талии и подъема стопы для заданных размеров обуви в зависимости от типа обуви.
Антропометрия
Исследования показывают, что более 90% людей имеют ступни разного размера, а морфология каждой ступни бесконечна, несмотря на то, что эти колодки созданы для пары. Идея идеальной посадки не реальна. Это дополнительно осложняется распределением или пропорциями массы стопы, которые различаются у разных людей, что приводит к тому, что линейные измерения, такие как длина и ширина стопы, неадекватны. Также важно, чтобы сапожники учитывали массу и объем, если может быть обеспечена точная подгонка.Чтобы обеспечить наилучшую посадку, измерения производятся в стратегически важных местах, и сапожник использует как линейное измерение, так и измерение объема для изготовления обуви. Современная колодка выполнена в трех измерениях, хотя и не является точной копией стопы. Вместо этого он сделан с учетом производственных требований. Последний производитель может произвести до 35 измерений до того, как будет изготовлена последняя модель. Слесарь-обувщик может сосредоточиться на длине, ширине мяча, пятке, линии верха, своде и подъеме стопы. Ожидается, что обувь будет хорошо изнашиваться, чувствовать себя хорошо, сохранять форму при износе, сохранять свой стиль стиля, правильно протекать, обеспечивать разумную свободу стопы, поддерживать баланс стопы и обуви, оставаться структурно неповрежденной.Эти характеристики не всегда зависят от качества материалов или компонентов или производственного процесса. Основанием для вышесказанного служат конструкция и многочисленные размеры последнего.
Размеры
Большинство измерений — это объем, а не традиционные длина и ширина, связанные с посадкой обуви.
Горловина
Расстояние от мыска до заднего шва.
Длина
Измерение длины стопы от задней части пятки до кончика самого длинного пальца ноги.
Обхват стопы
На колодке производятся четыре измерения обхвата и окружности. Это мяч; талия, подъем и пятка (от пятки до подъема). Измерение требует тщательной оценки стопы, что не может быть выполнено с такой же точностью, как линейные измерения. Современные производители обуви используют точные инструменты для определения обхвата, но старые сапожники использовали для этого же размах руки. Размеры стопы измерялись относительно руки сапожника; подушечку стопы сравнивали с обхватом между большим и средним пальцами.Подъем измеряли между большим пальцем и мизинцем. Этот метод сильно варьировался в зависимости от размера руки сапожника.
Обхват шарика
Это измерение обхвата вокруг шарика последнего для определения допуска по ширине и объему внутри ботинка.
Обхват талии
Обхват талии по последней.
Обхват стопы
Обхват стопы на подъеме.
Обхват пятки
Расстояние вокруг ступни от задней части пятки до подъема стопы.
Recede Toe
Это часть последнего, которая выступает за кончики пальцев, образуя закругленный контур передней части обуви. Сужение, как в обуви с острым носком, увеличивает общую длину обуви. В плохо спроектированной колодке отступ может задевать пальцы ног, увеличивая напряжение на концах пальцев. Это можно назвать длительным.
Пятка к мячу
Определяет положение шарнира передней части стопы (плюснефаланговые суставы) и самой широкой части обуви (поперек головок плюсневых костей).
Пружина носка
Описывает приподнятую нижнюю поверхность подошвы у носка, чтобы придать обуви легкий рокерский эффект. Количество пружины мыска (встроенной в колодку) зависит от стиля обуви, толщины подошвы и высоты каблука. Он встроен в последнюю конструкцию и компенсирует жесткость обуви и обеспечивает плавный переход в движение. Чем жестче материал подошвы, тем больше пружина носка. Многие туфли также имеют небольшую пружину на пятке.
Протектор
Определяет ширину подошвы под подушечкой последнего и должен соответствовать размеру ступни. Точка протектора на последнем представляет собой нижнюю переднюю часть сразу за мячом и контактирует с базовой плоскостью.
Flare
Описывает кривую или контур последнего. Замах определяется положением передней части, когда последняя делится пополам в продольном направлении вперед от центра пяточной дуги. В накладках inflare есть внутренняя середина качания к передней части, и большинство современных туфель изготавливаются на накладках inflare (банановая колодка), потому что считается, что обувь более удобна.Последняя вспышка описывает обратное с замахом, лежащим на боковой стороне передней части. Иногда используется для изготовления обуви на заказ для младенцев с диагностированными проблемами развития стопы. Прямые последние не описывают ни предпочтений в отношении вспышки, ни вспышки. Длинная ось последнего, проведенная через пополам изгиба пятки, описывает две равные продольные половины. Нормальная стопа имеет прямую ось, и, следовательно, прямую обувь можно носить на любой ноге. До появления оборудования для производства туфель на каблуках было обычным делом, чтобы обувь делалась с прямым расклешением до начала двадцатого века.
Отзыв написан 16.06.2020.
Изготовление колодок для обуви
Изготовление колодок для обувиИзготовление колодок для обуви по индивидуальному заказу
колодки готовые
, это должно дать вам четкое представление о том, как будут выглядеть мои колодки после завершения.слепок для стопы сделан с альгинатом, а колодки изготовлены из силиконового каучука RTV с твердостью по Шору 20 А. это резинка твердость (жесткость — хорошее описание)
зачем делать колодки, если их можно купить? Во-первых, использованные колодки не подходят для ваших ног. во-вторых, длится производятся партиями в разном количестве, а это означает, что вам нужно будет заплатить за весь выпуск, чтобы сделать их новыми. умножьте пробег на стоимость пары… и вам не нужно говорить, что каждая пара дорогая, не так ли? может ты будет достаточно удачлив, чтобы найти набор по разумной цене в Интернете (дайте мне шанс Вегаса на это!), но если вы хотите попробуйте свои силы в изготовлении обуви самостоятельно, этот процесс может сэкономить вам много времени и денег, а также поможет получить хорошо подходит
изготовление формовочной коробки — контур лапки
, используя использованный мазонит, я вырезал два куска немного больше, чем мой след.прослеживая вокруг моих ног с маркер установил начальный минимальный периметр для внутренних размеров коробки
Чем ближе эти размеры соответствуют стопе, тем меньше потребуется материала. альгинат должен иметь около толщиной полдюйма вокруг модели (все поверхности вашей стопы) из-за ее недостаточной прочности. точно сказать где ваши ноги, когда они погружены в непрозрачную слизь, на удивление сложно, а это означает, что пространство вокруг ваша ступня во время заливки — неизвестная переменная.все эти факторы необходимо учитывать при определении внутреннего размеры формовочной коробки. также обратите внимание, что облицовка из мазонита обеспечивает гладкую поверхность, но поскольку альгинат рекламируется как одноразовый материал для форм, мы не заботимся об его удалении. если другой формовочный материал (многоразового использования), это было бы желательно, но это не повлияло на выбор материалов — они были просто бесплатными и доступными
изготовление опалубки — подготовка стенок короба
фанера и облицовка из масонита были покрыты слоем резинового клея, который перед тем как высохнуть. прижимаются друг к другу.имейте в виду, что резиновый клей изначально позволит двум поверхностям немного скользить, поэтому не забывайте повторно проверять выравнивание на каждом этапе сборки — вам нужны узкие углы, чтобы предотвратить водянистую альгинат от ускользания
обратите внимание на резиновый клей — это не просто резиновый клей. это продукт торговой марки, который спас мне много денег. каждый раз, когда подошва или подкладка начинает расшатываться (обычно на моих кроссовках), я осторожно отодвигаю ее обратно и постарайтесь ослабить его как можно сильнее: если край клея проваливается, то и остальной обязательно даст путь в конце концов.не исправляйте просто свободный периметр, иначе проблема останется в центре обуви за пределами ваш охват
да, это дорогое удовольствие. но если вы будете искать, вы можете найти его — и его тоньше — из единственного источника, каждый в потрясающая цена. есть дополнительная плата за подачу заказа на сумму менее ста долларов, но даже с этой надбавкой и доставкой цемент и разбавитель были дешевле, чем цемент в других местах. проверять вокруг — этот клей считается обязательным при изготовлении и ремонте обуви (разбавитель не так важен)
изготовление опалубки — сборка
и, вот так, коробка готова (мучительно подробные и многословные шаги и пояснения удалены для комфорт посетителей)
готовая опалубка
сладкое.если есть какие-либо вопросы относительно утечки, я рекомендую нанести бусину оригинального липкого клея Aleene на швы
поудобнее
потребовалось время, но в конце концов я нашел комбинацию стула и опоры, которая позволила бы мне расслабиться. в то время как альгинат вылечил
, если вы похожи на меня, сидеть неподвижно десять-пятнадцать минут — это настоящая пытка… есть … так много … сделать … должен … сбежать …
помните: вы должны держать ногу неподвижно, примерно на полдюйма от дна формы и по центру сбоку. в сторону, спереди назад. может ты сможешь сделать это стоя или в неудобном сидячем положении, но не я
предупреждения о безопасности
, здесь мы обращаем внимание на альгинат и готовимся к заливке. альгинат — очень мелкий порошок, который может попадает в легкие и соединяется с влагой и слизью, образуя резину.это фатально, так что следуйте указания по безопасности от производителя
ради любви к богу обратите внимание. любой, кто меня знает, знает, что я обычно игнорирую меры предосторожности. у меня были обморожения двадцать три раза (и это количество продолжает расти), траншея ступня один раз, сломал больше костей (включая мой череп — фактически в два раза), чем средний человек (но меньше, чем Evil Knievel), часами стойте, рисуя ядовитые пары, используйте настольную пилу без предохранительного снаряжения, я ветеран-инвалид. (у меня сильная и непрекращающаяся боль в спине), упал с серьезной высоты, выбросил больше мотоциклов, чем кто-либо из своих знакомых, мне на голову падали тяжелые предметы (вы видите здесь узор?), бросил сигарету в пятигаллонную канистру с газом (случайно, в темноте, в лесу в Германии), был сброшен с лошади, соскользнул с холма и потерял значительную кожа на ноге, была искалечена собакой, все еще бегала ножницами, из-за чего автомобильный аккумулятор взорвался и разбрызгался кислота в лицо, потому что я небрежно курил рядом с ней, жонглировал ножами в детстве. честно пережил больше несчастных случаев, чем мне хотелось бы думать, и в целом я не боюсь умереть.никогда не было. я Я не глупый парень, но по какой-то причине я ОТСТАЛСЯ, когда дело доходит до безопасности. это один случай, когда я не стал искушать судьбу — пудра такая прекрасная!
безрассудство здесь — это не шанс, что случится что-то плохое — это гарантия. порошок очень мелкий и может оставаться подвешен в воздухе на длительное время. хорошо после заливки я снял маску и все еще чувствовал ее запах в воздухе — это следует воспринимать очень серьезно
Держите контейнер для альгината закрытым, когда не дозируете порошок.дозировать медленно — у вас есть время
Я настоятельно рекомендую вымыть пол после выдачи. Распределите на полу, а не на столешнице. это потому что там почти наверняка будет немного порошка в воздухе, и вам нужно, чтобы он был как можно ближе к полу, чтобы он мог осесть как как можно быстрее без приземления на несколько поверхностей. приготовьте влажную швабру и держите ее рядом с собой, когда вы ее раздаете — не ходить вокруг и поднять!
хорошо, это мое предупреждение.не беспокойтесь звонить: я не везу вас в больницу
Температура и объем воды
по данным производителя и по моим личным подсчетам, у меня было на пятьдесят процентов больше, чем нужно для работы. очевидно должно быть что-то не так, и, опасаясь, что мне хватило только на то, чтобы все исправить с первого раза, я решил провести небольшой тест. этот тест окупился
Вуказаниях указана температура воды восемьдесят градусов по Фаренгейту (gesundheit), и я точно выполнил.кулер вода продлевает рабочее время (сколько времени у вас есть для смешивания), а также время извлечения из формы (сколько вам нужно ждать перед тем, как снять ногу). соотношение по объему один к одному, альгинат и вода
также имейте в виду, что если в вашем районе очень жесткая вода, вам, вероятно, следует купить немного дистиллированной воды в продуктовом магазине.
смешивание альгината с водой
медленно добавьте воду к альгинату, осторожно перемещая ливень, чтобы начать процесс смешивания.тщательный смешивание имеет решающее значение для получения хороших результатов. вы не можете смешать
тестирование альгината
с использованием рекомендованного количества воды и температуры воды заставил альгинат начать схватываться задолго до время, указанное в документации производителя. зная, что это было важно позже
явно возникла проблема с проталкиванием моего пальца в быстро гелеобразующий альгинат. производитель рекомендует заливать альгинат в форму в самой нижней точке, позволяя ему окружать объект при повышении уровня.также предложил наносит тонкий слой лосьона или вазелина, главным образом для того, чтобы облегчить врастание волос в альгинат. это могло бы помочь здесь
семьдесят градусов работали намного лучше, когда я налил позже и добавил немного больше воды, чем требовалось. такое же влияние на время отверждения, как и при использовании более холодной воды
пробная заливка стекловолоконной смолой
не уверен, будет ли стекловолоконная смола совместима с альгинатом (не все) Я смешал небольшую партию и вылил это в
результаты испытаний
детализация была потрясающей — гораздо больше деталей, чем требуется в колодке для обуви.
Состояние формы
форма выглядела так, как будто она была в достаточно хорошем состоянии, чтобы ее можно было снова использовать, а позже, успешно, с скребки из той же силиконовой резины RTV, которая использовалась для заливки последнего
собрать все необходимое
установите все на свои места и приготовьтесь перемешать и залить
заливка альгината
опалубка оказывается слишком большой.чтобы материал доходил до лодыжки, я постоянно зачерпываю его с углов и поместите его вокруг моей лодыжки, откуда он медленно оседает. пока это работало, это было хлопотно. мой врожденные подозрения насчет того, что уголки потребляют слишком много материала, подтвердились
легко обнаруживается увеличивающаяся жесткость пресс-формы вокруг стопы. примерно через десять-пятнадцать минут (в зависимости от температуры воды и объема воды) вы будете готовы снять ногу.медленно перемести свой колени из стороны в сторону, стопа должна оставаться неподвижной. Как только вакуумное уплотнение сломается вокруг лодыжки, начните осторожно сгибать ногу. Единственный совет, который я могу дать, — это выгнуть ногу, чтобы под ногой образовался пузырь воздуха. движение пальцами ног заставит воздух проникать в пальцы ног и вокруг них, делая стопу в значительной степени свободной. когда я поднял ногу с формы, пластырь над моей аркой порвался от лодыжки на несколько дюймов вниз. это было идеально, так как он открывался ровно настолько, чтобы освободить мою ногу, и достаточно плотно закрывался, когда я заливал силиконовую резину
кастинг последние
Литьеосуществляется путем тщательного смешивания двух силиконовых компонентов и заливки смеси в форму.Я предлагаю наклонить форму вперед так, чтобы пятка оказалась выше пальцев ног, и медленно вылить на дно формы прямо перед пятка. Резина RTV будет медленно стекать в пальцы ног, уровень повышается по мере заполнения формы. аккуратно установите форму вниз и закончить заливку. это поможет свести к минимуму пузыри. мои колодки полны пузырьков воздуха, RTV был избит. мне нравится этот взгляд, но если вам не все равно, что думают другие, делайте свою работу как можно более профессионально и избегать пузырей
изготовление формы было сложной задачей, но отливка последней — самая простая часть — здесь действительно нечего показывать
снятие литой опоры
после двадцати четырех часов отверждения ступня начинает выступать.просто оторвите альгинат и выньте последний
Альгинат после литья и отверждения
альгинат очень тяжелый от влаги и разрывается, как прокаженная плоть.
Модификации опалубки
две банки для кофе и пара ножниц для жести позволяют мне модифицировать форму для другой ножки
Завершены модификации опалубки
после крепления банки к форме стыки герметизируются валиком Aleene’s.когда высохнет форма коробка готова к следующему последнему
постскриптум
, показанная здесь окраска основного покрытия была первым шагом в создании прекрасного ожерелья. эта чертова штука почти невозможно сфотографировать. рядом — слепок пальца из силикона RTV.
колодки на продажу —
На этой странице вы найдете нашу полную коллекцию колодок, выставленных на продажу.Они доступны в половинных размерах и различной ширины (см. Размеры в наших таблицах размеров). Они также доступны в виде специальных колодок для обуви и колодок для обуви (уровень настройки выбирается на странице продукта). Во всех наших колодках используется наша запатентованная система крепления рельсов Shoe Last Rail. Благодаря этому их очень легко снимать с обуви в сборе с минимальным воздействием на обувь. Приведенные ниже параметры можно использовать для сортировки нашей коллекции колодок для продажи.
Наши колодки изготавливаются под заказ.Пожалуйста, позвольте около двух недель производства плюс время доставки.
Отображение 1–12 из 24 результатов
Индивидуальные колодки на продажу
Все наши колодки для обуви, выставленные на продажу, можно настроить по индивидуальному заказу. Просто выберите «индивидуальный» в раскрывающемся списке уровня настройки на странице продукта. Затем вам будут предоставлены поля для ввода точных последних размеров обуви. Чтобы узнать, как определить размеры обуви по индивидуальному заказу, посетите нашу страницу по длине обуви по индивидуальному заказу. Если вы предпочитаете покупать колодки, указав размеры стопы, рассмотрите возможность продажи наших колодок на заказ.
Продажа колодок по индивидуальному заказу
Все предлагаемые нами колодки для обуви можно заказать по индивидуальному заказу. Выбрав вариант «на заказ» в раскрывающемся списке уровня настройки, вы увидите поля для ввода размеров стопы. Вам также нужно будет загрузить следы ног или отсканированные изображения. Мы учтем все ваши пожелания и создадим для вас специальные колодки для обуви. Чтобы узнать больше об этом процессе, пожалуйста, посетите последнюю страницу нашей обуви на заказ.
Продажа колодок по стилю
Все наши колодки, выставленные на продажу, разделены на категории по стилю обуви.Вы можете сортировать по заданному стилю с помощью раскрывающихся списков в верхней части этой страницы. Например, если вы отсортируете по длине ботинка, вы увидите, что у нашей обуви самый высокий подъем лодыжки. У низкорамных колодок есть несколько меньший подъем, но все же больше, чем у стандартных колодок. У нас также есть в продаже колодки для обуви, специально разработанные для изготовления сандалий. У них более широкий каблук и носок, чтобы стопа не соскальзывала с сандалии, а также канавки для ремешков. У нас есть ортопедические колодки для обуви для лечения различных заболеваний стопы.Более тонко, наши оставшиеся на продажу колодки подразделяются на классические, повседневные и спортивные.
Мы также классифицируем наши колодки для продажи по типу мыска. Чаще всего стиль носка соответствует тому, что следует из названия. Но стиль обуви до последнего пальца также может повлиять на комфорт. Например, наша обувь в стиле бананового носка лучше подходит для ног с большим первым пальцем. Наши другие стили игрушек включают заостренные, полукруглые, круглые, полукруглые, квадратные, полуквадратные и наклонные.
Несоответствующие колодки на продажу
У людей не всегда точно совпадают размеры левой и правой стопы.Вот почему у нас есть возможность заказать несоответствующие колодки. Для нас это дополнительная работа, поэтому мы добавляем дополнительную плату, за исключением специальных колодок для обуви.
Дополнительное место в колодках для стельки / ортопедии
Стельки, стельки и т. Д. (Мы называем их все вставками) важны для комфорта стопы. Но иногда они могут быть довольно громоздкими. Таким образом, обувь и, следовательно, колодка для обуви должны быть соответственно больше. Такого почти никогда не бывает. Но мы делаем все возможное, чтобы из наших колодок можно было получить максимально удобную обувь.Просто выберите тип вставки из раскрывающегося списка. Дополнительная добавка добавлена для стандартных размеров, но включена для нестандартных и сделанных на заказ колодок.
2D-выкройки для наших колодок на продажу
Предоставляя гибко настраиваемые колодки для обуви, мы берем на себя самый сложный аспект изготовления обуви. Но одним из недостатков этого является то, что у вас нет исходных данных, на основе которых можно было бы разрабатывать шаблоны. По этой причине мы намерены создать плоские 2D-поверхности для колодки для обуви. На них вы можете создавать свои выкройки.На данный момент мы предоставляем только последнюю выкройку низа (стельки). Позже мы также будем поставлять на продажу всю плоскую поверхность для всех наших колодок для обуви.
Подходящие компоненты для наших колодок на продажу
В настоящее время мы развиваем возможность производства различных компонентов, соответствующих нашим индивидуальным колодкам для продажи. К таким компонентам относятся высокие каблуки, танкетка, платформы, стельки (вставки) и подошвы. Наша цель — чтобы вы могли заказать все необходимое, чтобы вы просто собирали детали, которые мы отправляем, для производства высококачественной обуви по индивидуальному заказу.
Создание последней обуви для нестандартного дизайна обуви
В обувной индустрии всегда есть место для предпринимателей, которые будут разрабатывать симпатичную обувь, не ограничивающую естественную форму стопы, что является редкостью. Первым инструментом, необходимым для экспериментов с индивидуальным дизайном обуви, является колодка для обуви. Традиционно колодки для обуви вырезаются из дерева, но описанные здесь шаги позволяют быстро слепить любительские колодки из хозяйственных принадлежностей. Форма последней определяет форму обуви, поэтому ее подгонка под вашу собственную ногу закладывает основу для обуви, которая идеально подходит.
Дизайн обуви — это то, что, как дизайнер одежды, я бы с радостью предоставил сапожникам, если бы мог. Тем не менее, когда я готовился фотографировать свой дизайн одежды для маркетинга, поиск доступной обуви, которая подходила бы моему манекену и подходила бы к одежде, привел меня к пути к созданию обуви на заказ. Некоторые манекены, в том числе и мой, крепятся на стержне под одной ногой. В этом случае необходимо просверлить отверстие в одной обуви каждой пары, которую носит манекен, чтобы обувь манекена стала бесполезной для ношения человеком.Обувь-манекен по индивидуальному заказу может быть изготовлена с минимальным усилением и тканевой подошвой, что снижает стоимость и предлагает бесконечные возможности для сочетания с различными нарядами.
Шаг 1. Оберните одну ногу полиэтиленовой пленкой
Для начала оберните одну ногу полиэтиленовой пленкой, такой как Saran Wrap, которая обычно используется для хранения продуктов. Если одна ступня больше другой, оберните большую ступню. Используйте небольшие кусочки ленты, чтобы удерживать полиэтиленовую пленку на ступне. Если манекен сделан из стекловолокна, будьте предельно осторожны, чтобы не поцарапать краску.Для манекенов из стекловолокна разместите полосу картона шириной 1 дюйм вертикально вдоль задней части пятки до задней части щиколотки, чтобы защитить краску при последующем удалении формы.
Шаг 2. Оберните упаковочную ленту вокруг пластиковой пленки
Обернув ступню полиэтиленовой пленкой, оберните по крайней мере три слоя прозрачной упаковочной ленты вокруг ступни, стараясь при необходимости вырезать на ней кусочки, чтобы лента могла иметь гладкую форму с минимальными складками.Хотя для обуви, изображенной на последней фотографии, использовалось около трех слоев ленты, было бы полезно несколько дополнительных слоев, чтобы последний не деформировался немного не по форме во время набивки.
Шаг 3: Отрежьте форму стопы и исправьте порез
Вне зависимости от того, делаете ли вы накидку для человека или манекен, рекомендуются медицинские ножницы, которые можно приобрести в магазинах медицинских товаров. Пластиковый наконечник предотвращает повреждение или травму при резке. Когда я использовал эти ножницы, чтобы вырезать форму с моего манекена из пенопласта, кончик мягко отодвинул пену, а не проткнул ее, как это сделали бы острые ножницы.Прижмите ножницы к ступне, чтобы уменьшить ширину ножниц. Вырежьте прорезь вдоль пятки формы и снимите форму с лапки. Закройте разрез несколькими слоями упаковочной ленты.
Шаг 4: Заполнение формы для лапки набивкой
Маленькие кусочки набивки лучше всего подходят для заполнения формы для ног. Если вы используете цельный кусок ватина, разрежьте его на мелкие кусочки. Используя ножницы или другой длинный предмет, войдите в форму, чтобы сжать начинку во время наполнения.Колодка для обуви должна быть как можно более прочной для большего удобства использования. Два шарика отмечают выступы на лодыжках с обеих сторон изображенной формы, но это необязательно. При желании перед заполнением прикрепите шарики к внутренней части формы липкой лентой, чтобы шарики оставались на месте. Также необязателен круглый кусок плотного поролона в верхней части щиколотки, который помогает сохранить форму в проеме. После заполнения закройте отверстие несколькими слоями упаковочной ленты.
Шаг 5. Отрежьте тканевое покрытие для обуви
Чтобы разрезать тканевое покрытие колодки для обуви, используйте графическую ленту шириной 1/8 дюйма, такую как графическая лента ChartPak, которая показана на рисунке, для обозначения места шва.Эластичный трикотаж легче подогнать по форме, чем тканый. Плотно прижмите ткань ко дну формы и отметьте черную линию, которая проходит сквозь ткань. Повторите то же самое для верхней части формы, разрезав ткань перед щиколоткой, чтобы можно было свободно обернуть ее сзади. Для лодыжки вырежьте круглый кусок, чтобы прикрепить его к прямоугольнику. Вырежьте припуски на швы 1/4 дюйма на всех деталях. Удалите графическую ленту, прежде чем пришивать ткань вокруг формы.
Шаг 6: Пришейте тканевое покрытие на месте, чтобы закончить последний ботинок
Сметайте руками верхнюю и нижнюю части стопы.Оставьте большую часть вертикального шва пятки открытым. Прошиваем машинной строчкой стрейч и убираем наметку. Обрежьте швы и поместите поверх формы для ног. Стежок закрыл оставшуюся часть пяточного шва вручную. Машиной сшейте детали лодыжек вместе. Прошиваем рукой вокруг щиколотки.
Ваша кастомная колодка для обуви готова! При изготовлении выкройки обуви упомянутую выше графическую ленту можно использовать для наложения линий рисунка на последнюю. Драпируйте выкройки обуви той же тканью, которая будет использоваться для готовой обуви, будь то трикотаж или ткань.