Пресс для производства брикетов из опилок: как своими руками сделать станок для прессования опилок
Варианты станков для изготовления топливных брикетов
Современные технологии проявляют себя там, где, казалось бы, ничего нового не придумаешь. Примером тому являются топливные брикеты или, как их еще называют, евродрова. Это та же древесина, но за счет спецобработки получившая новые свойства, позволяющие ей сгорать с большей эффективностью.
Для их создания не требуются космические технологии – простейший станок для изготовления топливных брикетов представляет собой пресс. Поэтому наладить получение современного топлива с некоторыми свойствами, улучшенными по сравнению с обычными дровами, можно и своими руками.
Не забудь поделиться с друзьями!Содержание статьи
Чем хороши брикеты
Топливный брикет – измельченная древесина и древесные отходы, спрессованные в форму, удобную для транспортировки и хранения.
В результате обработки на станках прессованием под высоким давлением готовые брикеты приобретают новые качества.
- повышенная температура горения и, соответственно, лучшая теплоотдача;
- большая плотность брикетов приводит к более длительному горению одинакового объема;
- уменьшенное образование сажи и зольных остатков;
- брикеты выпускаются различной формы – короткие цилиндры, прямоугольные кирпичи. Но в любом случае они удобны для хранения и переноски.
Если сравнивать с обычными дровами, то ни по одному параметру евродрова не будут хуже. К недостаткам можно отнести то, что по внешнему виду брикета не всегда можно определить конкретную древесину, из которой он изготовлен. И если, например, требуется именно березовый брикет, то приходится положиться на добросовестность производителя.
Изготовление промышленным способом
Первым этапом при получении топливных брикетов в промышленных условиях является измельчение материала на специальных станках. Зачастую сырьем для изготовления брикетов служат отходы деревообработки – стружки, опилки, щепки. Крупные куски дерева измельчаются до состояния опилок размером не более 4 мм.
Затем происходит тщательная сушка древесины. Удельная влажность материала доводится до 10% и даже меньше. Чем суше древесина для последующего брикетирования, тем лучше качество готового топлива.
Завершающий этап – получение самих топливных брикетов. Для этого подготовленное сырье подвергают мощному давлению. Происходит повышение температуры, а из древесной массы выделяется клейкий компонент – лигнин. При большом давлении и в присутствии связующего лигнина древесная масса формируется в единый твердый брикет.
Плотность такого продукта превышает плотность природной древесины в 1,5-2 раза, что обеспечивает брикетному топливу повышенную теплоотдачу и увеличивает длительность горения. При промышленном производстве евродров различают два способа сдавливания.
youtube.com/embed/fCSmwm4BAM4″ frameborder=»0″ allowfullscreen=»allowfullscreen»>
Метод прессования
В случае прессования исходное сырье подвергается давлению в подготовленных формах с помощью гидравлического пресса. Типовая величина давления в станке для прессовочного производства топливных брикетов составляет 300-600 атмосфер. На выходе получаются брикеты в виде прямоугольных кирпичей или коротких цилиндров, в зависимости от формы, в которой они прессуются.
Метод экструзии
При этом методе происходит постоянное выдавливание древесной массы из выходного отверстия рабочего канала. Сырье загружается в бункер, оттуда подается в рабочий канал, где дополнительно разогревается. Канал выполнен в виде конуса, сужающегося к выходу. Подача сырья из бункера и его сдавливание в рабочем канале производится на станке шнековым винтом. Подобный пресс на основе шнека обеспечивает давление на сырьевую массу до 1000 атмосфер. Выходящая из экструзионной установки спрессованная «колбаска» охлаждается и нарезается на стержни нужного размера.
Брикетирование своими руками – за и против
Самостоятельно сделать пресс и наладить производство топливных брикетов возможно. Но это требует материальных затрат, физических усилий и времени. Надо учитывать и то, что достичь качества евродров, выпускаемых в заводских условиях, вряд ли получится. Конечно, можно приобрести станок, мало уступающий производственному, но затраты на приобретение будут колоссальными.
Необходимо хорошо представлять, для чего требуется собственное производство, какие есть для этого условия и какие предстоят затраты. Может быть, и не стоит отказываться от обычных дров или лучше закупать для отопления уже готовые брикеты.
Плюсы
Положительные стороны домашнего изготовления состоят в следующем. Собственные топливные брикеты не дадут качества горения, как у покупных, но будут эффективнее дров.
Если есть возможность получения большого количества древесных отходов – опилок, мелких обрезков, стружки, коры, – то из них выгоднее сделать спрессованные дрова. Опилки и стружка в чистом виде малопригодны для горения, а после обработки на станке для прессовки опилок из них выходит хорошее топливо.
Можно пустить в дело не только дровяные, но и любые другие горючие отходы – солому, сухие листья, бумагу, картон. По отдельности из них горючий материал – никакой, а в брикетах будет толк. Брикетированное топливо удобно для складирования и для загрузки в топку.
Минусы
Но есть и недостатки, о которых следует помнить. Попытки улучшить качество самодельных евродров могут привести к тому, что будет покупаться дорогостоящее оборудование или постоянно дополняться существующее. В итоге окажется, что выпуск собственных брикетов не оправдает затраты.
Самодельным топливным брикетам требуется место для качественной сушки. Просушивание на солнце не всегда оправданно. Требуется просторное сухое помещение. Хранить самодельные брикеты тоже надо так, чтобы они не впитывали влагу.
Домашние связующие материалы
На самодельных станках добиться давления, при котором из древесной массы выделяется лигнин, практически невозможно. Поэтому в сырье для самостоятельного брикетирования обязательно надо добавлять материалы, которые помогут связать, склеить сырье в монолитный брикет. Чаще всего для этих целей используют:
- глину. Объемная пропорция 1 к 10 древесного сырья;
- клей. Годится любой, но, естественно, лучше брать самый дешевый;
- измельченную бумагу или картон. Помимо того что это тоже горючий материал, в бумаге содержится лигнин. А бумажный лигнин свои клейкие свойства проявляет при замачивании. Правда, потом понадобится дополнительное время на просушку брикетов, содержащих бумагу.
Чтобы связующие добавки в полной мере проявили свои свойства, их надо тщательно перемешивать с горючим сырьем, а потом эту смесь замачивать в воде.
Обратите внимание! При промышленном производстве сырье перед прессовкой тщательно высушивают, а при самодельном – тщательно замачивают.
В этом основное отличие домашнего изготовления. Сушат топливные брикеты уже после прессовки, чтобы они затвердели, держали форму и хорошо горели.
Самодельный станок
Встречаются сведения об изготовлении в домашних условиях самодельных шнековых экструзионных установок. Но даже создатели таких эффективных станков для производства топливных брикетов отмечают, что устройства требуют качественных материалов и использования электродвигателя. Гораздо легче сделать вместо сложного станка обычный пресс.
Ручной пресс
Прессы, использующие только ручные усилия, бывают двух видов – винтовые и рычажные. В винтовых вариантах шток, сдавливающий сырьевую массу, перемещается накручиванием винта.
Измельчители
Важным этапом в производстве брикетов является измельчение древесного сырья. Конечно, можно делать это вручную, с применением простейших резаков. Но эффективнее будет механизировать этот процесс. Подойдет роторный станок, применяемый для измельчения растительной массы при производстве удобрений в домашних условиях. Умельцы применяют для этих целей и старые стиральные машины активаторного типа. На активаторе крепятся ножи, измельчающие загруженное сырье.
Станок с использованием готовых механизмов
Усовершенствовать ручной станок можно, снабдив его готовым гидравлическим домкратом или покупным гидравлическим прессом. Потребуются также материалы для крепления механизма и изготовления других элементов конструкции. Форма матрицы, в которой будет прессоваться сырье, может быть круглой или прямоугольной. Для круглых форм можно использовать стальные трубы нужного диаметра.
Основание станка для изготовления топливных брикетов сваривается из швеллеров. Для стоек подходят уголки размером 100 х 100.
Для формовочной матрицы берется толстостенная труба. Диаметр подбирается исходя из желаемых размеров готовых изделий. В трубе равномерно высверливаются несколько отверстий диаметром 4-5 мм для выхода воды при сжатии.
Матрица оборудуется съемным дном, необходимым для извлечения готовых брикетов. Но есть более перспективный вариант: дно приваривается к матрице намертво, а с внутренней стороны крепится пружина с диском чуть меньшего диаметра. При прессовке пружина сжимается, а после отведения штока – разжимается, выталкивая диском спрессованный продукт.
Для штока подойдет труба миллиметров 30 в диаметре. К ней приваривается пуансон, свободно входящий в матрицу. Другой конец штока крепится к гидравлическому механизму.
Перед загрузкой в матрицу древесную массу желательно хорошо перемешать. Барабан для перемешивания можно сделать из листовой стали или взять готовый от стиральной машины. Закрепляется барабан на стойках.
Подающий лоток, по которому сырье из барабана загружается в матрицу, тоже делается из стального листа.
На такой установке вряд ли удастся получить сверхплотные евродрова. Но с задачей сделать из рассыпающегося сырья твердый брикет она вполне справится. В итоге из отходов получится продукт, по плотности равный древесине, но спрессованный в удобную форму.
как сделать ручной или гидравлический пресс для производства своими руками и чертежи для его изготовления
Использование топливных брикетов очень популярно в Европе, особенно в северных странах, и в регионах с развитым животноводством. Они намного дешевле, чем привычный топливный материал, доступны, а для владельцев фермы не составит большого труда изготовить их самостоятельно.
В брикеты могут быть спрессованны любые горючие материалы, однако чаще всего применяют опилки, уголь с торфом, солому или древесную стружку. Подходит для прессования и щепа дерева.
О топливных брикетах
Топливные брикеты экологичны и безопасны, обладают хорошей теплоотдачей, разгораются быстрее, чем дрова, не искрят и долго горят.
Квадратная или прямоугольная форма позволяет складывать топливный материал для более удобного хранения. Основные недостатки — ломкость и низкая влагоустойчивость.
Если планируется изготовление брикетов из опилок, то они должны отвечать следующим требованиям:
- Влажность не более 12%,
- Средний размер около пяти миллиметров,
- Количеством загнивших опилок — менее 5% от всего объема.
Оборудование для изготовления брикетов
Метод брикетирования основан на создании максимального давления, достаточного для освобождения материала от влаги. На рынок поставляется несколько видов оборудования для изготовления брикетов. Полный же комплект включает в себя:
- Аппарат-измельчитель для сырья,
- Сушильный аппарат,
- Пресс.
Если изготавливать брикеты из опилок, оборудования требуется меньше — измельчитель не нужен, поскольку опилки имеют уже подходящий размер. Если возможна предварительная просушка опилок в хорошо проветриваемом помещении или же на открытом воздухе, то из списка оборудования можно исключить и сушилку.
Основным и самым важным является пресс для брикетов.
Это оборудование представляет собой силовое устройство, совмещенное с матрицей. С помощью силового каркаса передается давление на заготовленный материал. Пресс может использовать ручные или механические приводы для передачи давления.
Работает пресс для брикетирования опилок так: опилки засыпаются в специальную форму, включается работа привода, что ведет к сдавливанию материала внутри формы. Брикет вынимается и выкладывается на окончательную просушку.
Самодельный пресс
Пресс брикетировочный можно не только купить, но и сделать самостоятельно. Самодельное оборудование условно делится на две группы:
- С ручным приводом,
- Работающие от домкрата.
Чтобы изготовить пресс для топливных брикетов своими руками, понадобится также сделать металлическую квадратную или круглую форму, и пуасон. Форму обычно сваривают из металлического листа.
В стенках и на дне формы рекомендуется просверлить несколько отверстий тонким сверлом. Нужно это для того, чтобы в процессе прессования выделяемая влага уходила из формы. Для удобства форму можно сделать со съемным дном, тогда брикет будет удобнее вынимать.
А для сбора стекающей воды под форму обычно устанавливают небольшую емкость.
Пуасон также изготавливают из плоского листа металла, толщиной около 4,5 мм. Лист необходимо приварить к рычагу давления или закрепить на шарнирах. Пуасон необходимо сделать на несколько миллиметров меньше формы — он должен свободно заходить внутрь.
Не рекомендуется оборудование прессов двумя и более формами. Это повышает производительность, но снижает качество брикетов. Одного рычага давления недостаточно для качественного брикетирования в нескольких формах.
Пресс для опилок из домкрата в качестве рычага отличается большей производительностью, хорошей спресованностью брикетов и легкостью в использовании. Для изготовления пресса можно использовать также гидравлическую установку, которую часто применяют в сервисах по ремонту автомобилей.
Для изготовления брикетов очень важен не только пресс, но и помещение, где он установлен. Оно должно быть достаточно просторным, с хорошей вентиляцией, надежной электропроводкой и иметь несколько огнетушителей.
Настенный ручной пресс
Самодельный пресс можно прикрепить к стене для большего удобства. Для этого из любого прочного материала нужно сварить раму. Обычно используют металлический уголок. Готовую раму при помощи дюбелей крепят к стене. На верхней перекладине рамы устанавливают шарнир для рычага.
В качестве рычага можно использовать любой отрез металлической трубы, прочную металлическую шпильку или стальной круг с резьбой. Снизу рамы приваривают форму, а после этого к рычагу присоединяют пуасон. Длина трубы должна обеспечивать свободное вхождение пуасона в форму.
Напольный пресс
Напольный вариант пресса для изготовления опилок отличается тем, что форму с рычагом крепят к устойчивой металлической стойке. Обычно ее сваривают из уголка, или же используют старые столы, металлические треноги или любой доступный металлический каркас. Устройство такого пресса полностью аналогично настенному.
Процесс изготовления брикетов
Производство брикетов основано на создании высокого давления на материал. Высокое (выше 30 МПА) давление приводит к выделению лигнина и формированию брикета.
Чтобы изготовить в домашних условиях топливные брикеты из опилок своими руками, в исходное сырье необходимо добавить глину, клей для обоев или раскисшую бумагу, а также воду. Сделать брикеты из опилок без всех этих компонентов невозможно.
Как сделать брикеты: опилки смешивают с сухой глиной в соотношении десять к одному. В полученную смесь понемногу вливают воду, постоянно перемешивая, до образования кашеобразного состояния.
Хороший брикет получится из смеси, которая легко лепится в руках. Слишком жидкая смесь будет долго сохнуть, а слишком густая — плохо гореть.
Для лучшего горения можно добавить к опилкам немного сухих листьев или бумаги.
Полученную смесь закладывают в форму, прессуют, достают из-под пресса и выкладывают на просушку.
Переработка опилок в домашних условиях подобным образом очень удобна и практична. Для отопления сараев и других хозяйственных построек можно также изготавливать брикеты из использованных, но просушенных опилок.
Использование торфа и угля
Уголь и торф и сегодня являются актуальными отопительными материалами. Уголь выделяет очень много тепла, но его разгрузка и хранение очень хлопотно. Торф также хорошо горит, но его опасность состоит в том, что он легко воспламеняется, и должен храниться в темном месте с достаточной вентиляцией.
Брикеты из торфа или угля можно делать только тогда, когда материал имеется в очень большом количестве. Перед брикетированием и уголь, и торф необходимо хорошо просушить. Без предварительной просушки брикеты получатся влажными и будут плохо гореть.
Для угольного брикета необходима глина с водой, и угольная пыль. Для приготовления смеси удобнее всего использовать строительный миксер — ручное перемешивание больших объемов займет очень много времени. Брикетированный древесный уголь после прессования нужно также выложить на просушку, а уже потом убрать в помещение для хранения.
Многие частники предпочитают изготавливать древесноугольный брикет, вместо обычного угольного.
Для его получения к угольной крошке необходимо добавить немного опилок. Такие брикеты отличаются лучшими показателями теплоотдачи, большей сухостью и легкостью в приготовления.
Оборудование для изготовления угольных или торфяных брикетов точно такое же. Можно использовать один и тот же пресс для брикетирования угля, соломы, торфа или опилок. Разница лишь в силе оказываемого давления на материал.
Источник: http://NaLugah.ru/inventar/press-dlya-toplivnyh-briketov-iz-opilok-svoimi-rukami.html
Топливные брикеты из опилок: как сделать пресс для изготовления евродров
Брикеты из опилок — альтернатива обычным дровам. Они отличаются низкой зольностью, имеют компактные размеры, удобны при транспортировке, хранении, характеризуются высокой производительностью тепла (5 кВт на 1 кг). Единственный минус — цена. Изготовить топливные брикеты можно самостоятельно из недорогого сырья.
Процесс производства евродров
Прежде всего необходимо разобраться с промышленной технологией, чтобы в дальнейшем соблюдать ее принципы.
Сначала измельчают опилки, стружки, более крупные древесные отходы. Затем сырье тщательно просушивают до снижения уровня влажности на 90%. Кроме древесины брикеты для отопления могут включать отходы аграрной промышленности: шелуху зерновых культур, лузгу семечек. Если брикетированный образец состоит из угольной пыли, его лучше не использовать в быту.
После измельчения и сушки осуществляется основной этап производства — прессование опилок. Для этого используется брикетировочный пресс или экструдер, зависит от выбранного метода формовки топлива.
Экструзия и прессование — усиленное сдавливание исходного сырья с целью получения связующего вещества лигнина (природного компонента, выделяемого из древесины). Он заменяет клеящие составы, сохраняет экологическую чистоту топлива.
При первом способе сдавливания пресс гидравлический для брикетирования развивает усилие около 500 бар. Из-за этого происходит самопроизвольный разогрев сырья, опилки сбиваются в плотный прямоугольный кирпичик.
Экструзионная технология производства схожа с работой мясорубки. Исходный материал поступает в загрузочный бункер, при помощи шнека проталкивается в зауженный конический канал.
Шнековый пресс для производства топливных брикетов выдает усилие в 800–1000 бар. Получается шестигранный брикет, дополнительно прошедший обработку под высокими температурами, порезанный на сегменты равного калибра.
На чертеже показана конструкция шнекового агрегата в разрезе.
Брикетирование в домашних условиях
Покупать пресс для производства топливных брикетов не совсем разумно даже при наличии подручного сырья: приобретение вряд ли окупится, если только не наладить продажу готового продукта. Без профессионального агрегата невозможно выдержать промышленную технологию, получить лигнин, служащий связующим элементом.
Но есть способ использовать отходы древесного производства, вводя в опилочный состав различные вяжущие ингредиенты:
- клей для обоев,
- глину,
- бумагу.
Чтобы не приобретать профессиональное оборудование для сушки и прессовки стружки, применяется более доступная технология. Древесные отходы вымачивают в воде, соединяют с глиной в пропорции 1:10. Вместо глины добавляют размокший картон или клей для обоев.
После смешивания полученную массу закладывают в форму самодельного станка для производства брикетов, крепко сжимают руками. Кирпичики достают, отправляют на просушку.
Самодельное приспособление
Конструкция пресса для опилок включает механический винтовой привод. Перфорированная емкость, установленная на брикетер, после наполнения подготовленной смесью помещается под станину. Вручную закручивается винт, создается давление. Сделать приспособление несложно, не нужна схема или чертежи, достаточно взглянуть на рисунок.
Винтовой прибор имеет невысокую производительность. Работа с ним требует много времени на загрузку формы, закручивание винта. Не совсем удобно извлекать брикет из формы.
Альтернатива — самодельный пресс, предусматривающий рычажный элемент и специальный выталкиватель для извлечения готового материала. Чтобы оптимизировать производственный процесс, часто оборудуют станину не одной, а двумя формами.
Существует и более усовершенствованный вид механизированного оборудования.
Домашний мини-пресс может комплектоваться не ручным, а гидравлическим домкратом, что позволяет существенно увеличить производство топлива. Для сборки этого брикетировщика требуются определенные навыки.
Но не стоит рассчитывать на обеспечение давления, необходимого для выжимки лигнина. Без дополнительных связующих компонентов обойтись не получится.
Рукодельное топливо: за и против
Обычная неспрессованная стружка редко используется для отопления: она быстро сгорает, не производит много тепла, не все котлы могут функционировать на отходах мелкой фракции.
Для сжигания опилок подходят шахтные котлы, оборудование с верхним способом горения. Это сложные, дорогие приспособления. Проще создать пресс для производства брикетов самостоятельно. Но и это не очень выгодно.
В случае покупки пресса готовые евродрова обойдутся дешевле. При работе с самодельным прессом качество брикетов будет ниже, времени на процесс будет уходить больше.
Производство топливных брикетов из опилок не стоит внедрять только для получения выгоды. Придется потратить много времени на рабочий процесс, оборудовать места для сушки заготовок, складирования топлива, вероятно, покупать опилки.
Но если много времени, есть излишки отходов, можно попробовать сделать топливные брикеты самостоятельно. Более подробное описание процесса производства в видео.
Источник: https://derevo-s.ru/material/opilki/toplivnye-brikety-svoimi-rukami
Как сделать брикеты в домашних условиях
Статья подробно рассказывает как сделать брикеты в домашних условиях, а также пресс для опилок своими руками. Прессованные опилки для отопления это те же евродрова,только намного дешевле.
Ручной пресс в настенном исполнении
Данное устройство предназначается для крепления к стене, отсюда и все конструктивные особенности. Матрица жестко соединена с рамой, а та, в свою очередь, приделана к стене дюбелями. Раму изготавливают из любого подходящего вторичного металла – уголков, профильных труб и так далее. В ее верхней части устанавливается шарнирное соединение для рычага.
Эту роль может играть любая шпилька большого диаметра и достаточной длины, на которую надевается конец рычага с просверленным отверстием. Вместо шпильки можно применить обычный стальной круг с резьбами на концах или приваренный наглухо.
Рычаг, устанавливаемый на пресс для опилок, сделанный своими руками, удобнее всего сделать из трубы небольшого диаметра, выбрав произвольную длину. Впоследствии в процессе работы, рычаг можно будет нарастить при необходимости. К трубе приваривается шарнир пуансона на таком расстоянии, чтобы последний хорошо входил в матрицу. Вот, собственно, и вся конструкция.
Пресс для опилок с домкратом
Смысл применения домкрата понятен – увеличить давление и производительность, уменьшив трудозатраты. Обслуживать такой пресс для изготовления топливных брикетов своими руками гораздо проще, а изделия получаются плотнее, а значит, гореть будут дольше.
Фокус только в том, чтобы встроить домкрат в конструкцию пресса вместо рычага, но проблема вполне решаемая.
Топливные брикеты из опилок делают в домашних условиях и с применением существующего прессового оборудования. Форму и пуансон прилаживают на механический пресс либо на гаражную гидравлическую установку, предназначенную для ремонта автомобилей.
Суть процесса состоит в том, чтобы создать максимально возможное давление, выдерживая его в течение нескольких секунд для слива воды. Конечно, с помощью ручного пресса невозможно создать и десятой доли того усилия, что требуется по технологии, то есть, не менее 30 МПа. Из-за чего плотность брикет выходит в лучшем случае как у обычной древесины, но в домашних условиях и это неплохой результат.
Винтовой пресс для брикетов из опилок
Конструкция простого пресса для опилок включает в себя механический винтовой привод. Перфорированная емкость, установленная на брикетер, после наполнения подготовленной смесью помещается под станину, после чего вручную закручивается винт и создается давление.
Сделать такое приспособление не сложно, здесь не нужна мудреная схема или чертежи, достаточно взглянуть на рисунок.
разу оговоримся, что винтовой прибор не может похвастаться высокой производительностью, к тому же работа с ним требует много времени, потраченного на загрузку формы и закручивание винта. Также в данном случае не совсем удобно извлекать сформированный брикет из формы.
Отличной альтернативой представленному образцу может послужить самодельный пресс для брикетов, предусматривающий рычажный элемент и специальный выталкиватель для извлечения готового материала, при помощи которого форма освобождается гораздо легче.
Чтобы оптимизировать производственный процесс, нередко оборудуют станину не одной, а двумя формами.
Евродрова своими руками
Алгоритм изготовления топливных брикетов своими руками:
- замочить измельченный картон;
- смешать мокрый картон с опилками – пропорция 1:10;
- поместить массу в пресс и отжать от влаги;
- вынуть брикеты из форм и высушить
Мешать опилки можно бетономешалкой или миксером. Сушить уже готовые брикеты можно на солнце или на печи. Влажность топлива должна быть минимальной. Например, в заводских брикетах влажность 8-10%. В домашних условиях хотя бы достигнуть уровня обычных дров 18-25%.
Большинство твердотопливных котлов и пиролизных печей работает на топливе, влажность которых не более 30%. Чем меньше влаги в топливе, тем меньше пойдет тепловой энергии на ее выпаривание. Соответственно, сухой энергоноситель отдаст больше тепловой энергии, на обогрев помещения.
Когда есть смысл производить топливные брикеты
Делать топливные брикеты своими руками, как указано на видео выше, выгодно только тогда, когда у вас есть бесплатные опилки. Но даже при этом не всегда есть целесообразность этого мероприятия. К примеру, у вас свое деревообрабатывающее производство, которое нужно отопить.
Просто опилки бросать в печку неудобно, да и не горят они нормально. В этом случае есть смысл купить станок и штамповать на нем брикеты для своих нужд. Качество изделий будет приемлемым, и вы сэкономите на отоплении.
Вручную делать брикеты в этом случае слишком хлопотно, так как энергоносителя нужно много.
Для отопления частного дома самодельные брикеты тоже не лучший вариант и вот почему:
- низкое качество из-за использования самодельных прессов;
- на производство нужно много времени и сил.
Это, если не учитывать того, что пресс тоже надо изготовить самостоятельно. К тому же брикеты могут и не получиться. Неприятный сюрприз может ждать после сушки – кирпичики бывает просто распадаются. Смысл самостоятельного производства есть тогда, когда вы хотите сделать несколько кубов брикетов, чтобы иногда отапливать дачу.
Источник: https://prof-kirpich.ru/otoplenie/kotly/kak-sdelat-brikety-v-domashnix-usloviyax.html
Самодельные брикеты из опилок
Брикеты из опилок пользуются большой популярностью в Европе из-за их экологичности и доступности. У нас такой вид топлива тоже достаточно востребован. Ими можно топить камин, печку или разжигать мангал. Изготовить брикеты из опилок возможно и своими руками, правда понадобится специальное оборудование и знания о выборе подходящего сырья.
Что такое брикеты из опилок?
В неподготовленном виде топить опилками не выгодно из-за низкого КПД теплоотдачи. Для увеличения КПД их брикетируют путем уплотнения. Брикеты имеют влажность на уровне от 10 до 12% и теплоотдачу в 4500 ккал/кг. Такой КПД в 2-4 раза выше, чем у дров. Это является причиной популярности готового брикетированного продукта.
У производителей изготовление брикетов пользуется популярностью по причине выгоды и дешевизны изготовления. Деревообработчики получают возможность достигать безотходности производства.
Прессуют опилки без добавок. Процесс уплотнения способствует выделению лигнина, естественного клейкого вещества, благодаря которому достигается высокая прочность.
Особенности изготовления промышленным способом
Промышленное производство брикетов из опилок включает два рабочих процесса – дробление сырья и прессование. Если пресс создает высокое давление – на выходе получаются уже готовые брикеты. При применении пресса более низкого давления, брикетам понадобится сушка. Используют как горячее, так и холодное прессование.
Самые мелкие опилки получаются при распиловке леса, их и используют для брикетов высшего качества. Из обычных древесных опилок тоже получается вполне достойное топливо.
На производстве процесс изготовления брикетов из опилок выглядит следующим образом:
- Опилки засыпают в контейнер дробилки для измельчения.
- Полученную фракцию прессуют. Пресс пропускает сырье через фильеры, позволяющие получить на выходе определенную форму брикетов.
- Фасуют брикеты в пленку.
Исходное сырье должно иметь влажность не более 10%. Процесс прессования создает давление, повышающее температуру опилок. Они досушиваются до влажности 4%. При такой влажности их можно упаковывать.
Виды форм топливных брикетов из опилок
Различают три формы, получаемые в процессе прессования:
- Кирпичи – форма RUF.
Размеры- 150х100х60 мм. Влажность брикета до 10%, плотность порядка1,2 г/см3. Теплоотдачу дают в 4400 ккал/кг. Такие брикеты малозольные, хорошо горят. Упаковка весит 10 килограмм, в ней 12 брикетов. Производятся холодным прессованием и имеют большой срок хранения – 3 года.
- Карандаши – Pini Kay. Показатели влажности, теплоотдачи и плотности аналогичны RUF. Размеры -250х60 мм, с отверстием диаметром 18-20 мм. Горят прекрасно за счет наличия отверстия в середине брикета. Создается дополнительная тяга. Делаются шнековым прессованием при высоких температурах. Срок годности до пяти лет.
- Цилиндры – NESTRO. Влажность брикетов от 8 до 10%. Плотность -1,0 г/см3. Теплоотдача 3900 ккал/кг. Имеют длину от 200 до 380 мм. В диаметре такой цилиндр 90 мм. Делают брикеты прессованием при среднем давлении. Срок годности у них всего год и зольность выше, чем у двух других.
Лучше всего горят и долго хранятся Pini Kay и RUF. Хороши для отопления дома и растопки бани. Цилиндры лучше использовать для обогрева нежилых помещений из-за более высокой зольности.
Домашний способ прессования
Изготовление брикетов из опилок своими руками требует соблюдения определенной технологии и этапов производства.
Сырье и подготовка
Для изготовления брикетов из опилок своими руками нужно определенное сырье и оборудование. В качестве сырья можно использовать:
- опилки древесные, стружку и мелкую щепу;
- шелуху, полученную после обработки сельскохозяйственных культур – риса, гречихи, риса, подсолнечника;
- отходы угля и торфа – мелкая фракция;
- солому;
- макулатуру (картон и бумагу).
При выборе состава неоднородного сырья (из разных отходов), нужно помнить, что опилки должны занимать более 60%, чтобы обеспечить высокое качество горения.
Можно также использовать глину. В процессе домашнего прессования опилок лигнин не будет выделяться из-за низкой мощности пресса, поэтому понадобится связующее вещество, которым будет размоченный картон или глина. Картон вносят в подготовленное сырье в размоченном виде, он должен занимать не более трети объема. Глину вмешивают в опилочное сырье в пропорциях 1 к 10.
Некоторые умельцы вместо картона и глины вмешивают в сырье обойный клей. Он относительно натурален, но при наличии в нем химических добавок его использовать не рекомендуется. Брикеты при сгорании будут коптить.
Необходимое оборудование для производства брикетов из опилок:
- дробилка;
- пресс выбранной модификации.
- емкость для подготовки сырья.
Этапы изготовления брикетов из опилок своими руками
Процесс домашнего прессования опилок выглядит следующим образом:
- сушка сырья, если оно имеет высокую влажность;
- измельчение сырья в дробилке или ручным способом;
- перемешивание измельченного опилочного сырья с глиной или картоном;
- загрузка под пресс;
- прессование в формы;
- выгрузка и сушка на воздухе;
- упаковка в пленку.
Качество сушки можно проверить путем разлома брикета, он должен быть плотным и сухим на срезе. Если нет подходящей дробилки – можно применить перфоратор.
Пленка обязательно должна быть термоусадочной, чтобы влага не проникала в готовый продукт и сохранялась его форма.
Прессы для изготовления брикетов из опилок
Для производства брикетов из опилок можно использовать три вида прессов.
Механизм с ручным приводом
Процесс изготовления: сделать раму из металлической трубы ( сварить ее). Раму прикрепить для устойчивости к стене любой постройки. В нижней части рамы неподвижно закрепить форму бля брикетирования.
Сверху на шарнире надо закрепить длинный рычаг. К рычагу надо прикрепить пресс, который будет нажимать на сырье. Пресс должен быть меньше формы по размеру, чтобы вдавливать в нее массу. Таким прессом можно изготавливать брикеты небольшой формы.
Механический пресс может быть и винтовым. Он представляет собой емкость для сырья и металлическую станину, в которую вставляется пресс в виде винта с площадкой. Закручивание винта производит уплотнение сырья.
Плюсы такого механизма:
- простота изготовления своими руками;
- дешевизна материалов.
Минусы:
- большие усилия прессования;
- высокий износ рабочих элементов.
Механизм с гидравлическим домкратом
Изготовить его – процесс невыполнимый, но можно взять готовый автомобильный гидравлический домкрат. Минимальная его грузоподъемность 2 тонны. Усилие домкрата должно быть направлено вниз – к форме с сырьем.
Плюсы механизма:
- большое усилие прессования дает возможность получить качественные брикеты;
- можно получить брикеты разной формы.
Минусы:
- громоздкость сооружения;
- при покупке обойдется не дешево.
Шнековый пресс
Шнековый пресс напоминает мясорубку. Сделать его дома очень сложно, проще взять бывший в употреблении. Основная рабочая деталь в прессе – это шнек, он несет основную нагрузку и обеспечивает формирование брикета.
Шнековым прессом создаются брикеты в форме прямоугольника или восьмиугольника, в центре есть отверстие. Плотность таких брикетов очень высокая, они долго и равномерно горят.
Плюсы оборудования:
- высокое качество брикетов.
Минусы пресса:
- покупка обойдется не дешево.
Плюсы и минусы самодельных брикетов
Преимущества топливных самодельных брикетов из опилок:
- углекислого газа выделяется намного меньше, чем при топке дровами или углем;
- компактный продукт, требующий мало места для хранения;
- материал не гниет из-за высокой плотности;
- ровно и красиво горит;
- в доме не будет мусора и пыли;
- экономия средств, при условии доступности сырья и оборудования для изготовления;
- брикеты долго горят – до четырех часов;
- выделяется мало дыма;
- не выбрасываются в воздух вредные вещества;
- чистку дымохода можно будет производить в три раза реже;
- экологично и безопасно;
- мощность котла увеличивается на 50%;
- сжигание угля дает зольность 20%, а брикетов 1-1,5%;
- кубометр брикетов из опилок по уровню теплоотдачи равен 4-6 кубометрам дров.
Недостатки самодельных брикетов из опилок:
- при недостаточном усилии пресса, брикеты могут рассыпаться;
- в домашних условиях готовые брикеты трудно хорошо высушить. В летнее время их можно просушить на солнце, а в другое время года – только в помещении, что не дает сильного снижения влажности. Соответственно они будут хуже гореть.
- изготовление и сушка брикетов требуют много места;
- процесс изготовления крайне трудоемкий и требует больших физических усилий.
Брикеты нужно хранить в сухом помещении. Срок хранения брикетов из опилок, сделанных в домашних условиях, не превышает года. Зола, получаемая от сгорания продукта, является прекрасным удобрением.
Самодельные брикеты из опилок являются дешевым и безопасным топливом. Если есть возможность их сделать своими руками, то брикеты сделают процесс отопления дома выгодным и экологичным.
Источник: https://pechiexpert.ru/brikety-iz-opilok-svoimi-rukami-01/
Станок для изготовления топливных брикетов из опилок
В современном мире брикеты из опилок, как один из видов теплоносителей, не имеют широкого использования среди населения. Высокая стоимость – вот главный аргумент. В связи с этим некоторые задумываются о самостоятельном изготовлении специального оборудования у себя дома или на даче.
Большинство согласится с тем фактом, что гранулы из опилок являются одними из лучших и эффективных видов твёрдого топлива, которое можно использовать для прогрева дома. Из явных преимуществ особо выделяются их высокая калорийность, удобство в использовании, а также совсем небольшая зольность.
Тем более что сырье для изготовления брикетов можно приобрести по смешной цене, или использовать для этой цели производственные отходы деревообрабатывающих предприятий.
Примеры некоторых из них:
- Опилки;
- Части досок;
- Древесина;
- Солома;
- Ветки деревьев и сухие листья;
- Картон, бумага.
Производство данного вида брикетировочных теплоносителей очень выгодные и с финансовой, и с экологической точек зрения.
Технология изготовления
Принцип изготовления таких топливных гранул не представляет собой ничего сложного. Сначала сырье просушивается, а затем помещается в специальное устройство – брикетный станок.
Есть два способа для собственноручного производства брикетов из опилок:
- Термическая обработка и давление. Эти два метода применяются в производстве, чтобы на исходном этапе получить качественную продукцию, так как позволяют создать крепкий внешний слой и сохранить плотность заготовки.
- Прессование сырья. Этот метод производства хорош для комплектации небольшого цеха по изготовлению топливных брикетов разной формы своими руками.
Устройства для производства топливных брикетов
Для эффективной утилизации биологических отходов производства существуют специальные брикетирующие станки. Дрова, опилки, сухая трава, лузга подсолнуха – основное сырье. Конечным продуктом является крепкий брикет, который еще называют евродровами.
Типы устройств, используемых для производства топливных брикетов:
- сушилка, используется для просушки сырья;
- дробилка, измельчает на фракции приблизительно одинаковых размеров;
- Гранулятор;
- Устройство для изготовления брикетов различной формы и размеров.
Этапу подготовки сырья необходимо уделить особое внимание. Влажность должна быть на минимальном уровне.
Станок для изготовления – механизм работы
Станок для изготовления брикетов из опилок имеет в своей конструкции несколько узлов. На первой стадии сырье просушивают, после чего дробят на мелкие фракции одинакового калибра. Конечным этапом изготовления топливных брикетов есть прессование. Если объем работы не слишком большой, то можно обойтись одним только устройством для прессования.
Намного лучше с данной задачей справится гидравлический домкрат, который крепится на опорной раме. При этом опорная точка направляется строго вниз. Под ним крепится форма, которую затем наполняют нужным материалом. Чтобы конечный продукт был нужной формы, для штока следует изготовить и провести установку насадки, которая в точности повторяет форму ёмкости для формирования топливных брикетов.
В этой схеме производства топливных брикетов имеются некоторые недостатки:
- Очень низкая производительность.
За один полный цикл работы изготавливается только одно изделие.
- Неоднородность в плотности материала. Это связано с тем, что гидравлический домкрат не в силах равномерно распределять давление по всему исходному материалу, который находится в форме.
Если использовать технологию производства топливных брикетов, что приведена выше, то можно без проблем обогреть дом на один отопительный сезон.
Устройство, калибрирующее сырье
Данное устройство используется для отсеивания больших частиц на дробилку.
После этого исходный материал отправляется просушиваться.
Сушилки
Степень влажности исходного материала является одним из самых важных параметров для того, чтобы получить брикеты хорошего качества.
Для этой цели используются диспергаторы. Их удобство заключается в том, что высушивание идет за счет горячего дыма.
Прессы
На промышленных предприятиях используют прессы для брикетирования универсального типа. Брус разделяется при помощи ножа, находящегося внутри пресса. Также имеется система термодатчиков.
Составные частицы топливного брикета связывает между собой лигнин – вещество, выделяющееся при высоком давлении и температуре.
Дополнительные механизмы
Чтобы повысить производительность и уменьшить физические нагрузки при изготовлении топливных брикетов, следует использовать дополнительные устройства:
- Транспортеры, подающие исходный материал в сушку.
- Бункер для накопления сырья с дозатором и ворошителем.
- Магниты, задача которых – улавливать и извлекать из материалов разные металлические примеси.
- Сортировщик, выполняющий работу за счет вибрации.
- Автомат, который упаковывает готовый продукт.
Видео: изготовление брикетов из опилок.
Топливные брикеты из различных видов сырья
Все знают о том, что бумага горит очень хорошо и выделяет значительное количество энергии. При этом остается сравнительно небольшое количество пепла. Если такой макулатуры в доме вдоволь, можно попробовать собственноручно изготовить из нее топливные брикеты для обогрева. Хотя сделать это не так уж и просто, как может показаться:
- Первым делом потребуется значительное количество бумаги.
- Ее необходимо будет каким-то образом измельчить на маленькие кусочки.
- Затем измельченную макулатуру следует замочить в воде комнатной температуры и подождать, пока этот раствор не станет жидким и однородным.
- После этого остатки жидкости нужно слить, а всю смесь, которая осталась – распределить по формам.
- Когда практически вся вода испарится из массы, ее необходимо извлечь из формы и отправить просушиться на свежий воздух.
Опытные мастера добавляют в замоченную бумагу немного крахмала. Также некоторые используют бумагу для производства брикетов из опилок. Она выступает связывающим элементом. Но следует помнить, что чем меньше фракция опилок, чем больше макулатуры потребуется для изготовления топливных брикетов.
Брикетированные опилки – эффективное и сравнительно дешевое средство для прогрева дома в отопительный сезон. Производить их можно, изготовив станок для производства брикетов. Нужно лишь иметь место, свободное время и сырье. Если нет возможности приобрести опилки или макулатуру по мизерной цене, то в производстве теряется всякий смысл и рациональней будет закупить партию дров для отопления. Но выбор зависит, конечно же, от самого домовладельца.
Republished by Blog Post Promoter
Брикеты из опилок своими руками, пресс для производства брикетов
Нельзя отрицать, что брикеты из опилок — это один из самых эффективных видов твердого топлива, используемых для отопления дома. Они высококалорийны (выход тепла — около 5 кВт с 1 кг при сжигании), имеют небольшую зольность, а также удобны в складировании, поскольку занимают мало места. Но вот дешевым это горючее точно не назовешь, топить котел или печь евродровами в течении всего сезона может себе позволить далеко не каждый.
Отсюда и возникает интерес у многих домовладельцев – а нельзя ли как-то сделать топливные брикеты своими руками? Особенно когда есть для этого сырье по мизерной цене. Решение этого вопроса как раз и является темой данной статьи. В ней будут рассмотрены различные технологии производства брикет из опилок и других видов сырья на производстве и в домашних условиях. По итогу станет понятно, при каких обстоятельствах имеет смысл браться за это дело.
Способы изготовления брикетов
Чтобы получить представление, как можно сделать топливные брикеты своими руками, надо вначале изучить, как их производят в заводских условиях. Подготовительный этап при любой технологии одинаков и заключается в измельчении и сушке сырья. Таковым выступают, конечно же, опилки и более крупные отходы деревообрабатывающего производства, которые перерабатываются для изготовления брикет. Затем сырье подвергают просушиванию с целью довести его влажность до показателя не более 8—10%.
Для справки.
Также в качестве исходного материала для производства евродров могут служить различные агропромышленные отходы (шелуха, лузга семечек) и даже угольная пыль.
Дальше начинается основная операция – брикетирование, проще говоря, — прессовка опилок. На сегодняшний день это проделывают двумя способами:
- Формование из опилок брикетов на гидравлическом прессе.
- Производство методом экструзии.
Надо сказать, что при обеих технологиях результат достигается за счет сильного сдавливания древесного сырья, вследствие чего из него начинает выделяться природный компонент — лигнин. Он и служит связующим веществом для этой рассыпчатой массы, других не предусматривается. Разница только в способе сдавливания, в первом случае используется гидравлический пресс для брикетов, развивающий усилие 300—600 Бар.
От такого сжатия сырье самопроизвольно разогревается, что только способствует формованию прочного прямоугольного «кирпичика». Как функционирует брикетировочная линия с гидравлическим прессом, показано на видео:
youtube.com/embed/WgPb7tzStjQ?feature=oembed» frameborder=»0″ allow=»accelerometer; autoplay; encrypted-media; gyroscope; picture-in-picture» allowfullscreen=»»/>
Вот так шнековым прессом выдавливаются евродроваЭкструзионный метод производства брикет из опилок легко понять на примере обычной домашней мясорубки или соковыжималки. Сырье загружается в приемный бункер агрегата и перемещается шнеком в сужающийся рабочий канал конической формы. Там и происходит его сжатие, при этом шнековый пресс для брикетов развивает чудовищное усилие – до 1000 Бар.
На выходе получаются дрова из опилок в виде шестигранника, которые проходят дополнительную термическую обработку и отрезаются в один размер специальным ножом. Устройство шнекового пресса для опилок в разрезе показано на чертеже:
Основная нагрузка ложится на шнек (поз. 5) и коническую втулку (поз. 7), износ деталей напрямую зависит от количества выдавленных брикетовИзготовление в домашних условиях
Понятно, что приобретать столь мощное оборудование, чтобы прессовать брикеты у себя дома – пустая затея. Даже если вы располагаете средствами и дармовым сырьем, окупить его стоимость удастся только в том случае, если прессовать дрова из опилок на продажу. Это значит, что выдержать традиционную технологию с выделением лигнина не удастся.
Подсказка. Отходы зимней обрезки деревьев отлично пойдут на брикетирование, если их предварительно измельчить дробилкой. О процессе сборки такого измельчителя веток читайте в отдельном материале.
Взамен домашние умельцы приспособились для формования «кирпичиков» использовать разные связующие, например:
- обойный или другой самый дешевый клей;
- глина;
- бумага, гофрокартон.
Чтобы не покупать дорогое сушильное и прессовое оборудование, в домашних условиях топливные брикеты делают следующим образом. Опилки замачивают в воде и тщательно перемешивают с глиной в пропорции 1 : 10, либо добавляют размоченный картон или обойный клей. Получившуюся смесь для изготовления брикет помещают в форму самодельного ручного пресса для опилок и сжимают усилием рук. Затем «кирпичик» извлекают из формы и кладут сушиться естественным путем, на улице.
Для справки. По этой технологии сообразительные хозяева прессуют брикеты из любых доступных материалов, способных гореть: из соломы, бумаги, картона, листьев, шелухи семечек и так далее.
Оборудование для производства
Простейший пресс для изготовления топливных брикетов, сделанный своими руками, имеет винтовой ручной привод. Формовочная емкость с перфорацией наполняется смесью и устанавливается под станину, давление создается за счет закручивания винта. Конструкция очень проста и подробно рассказывать о ней нет смысла, достаточно посмотреть на рисунок.Подобные винтовые станки для прессования брикет из опилок не слишком популярны в силу низкой производительности. Слишком уж много уходит времени на загрузку емкости, закручивание винта и извлечение готового изделия. Куда быстрее и проще выдавливать «кирпичики» на самодельном прессе с длинным рычагом и механизмом выталкивания брикеты наружу. Для ускорения процесса к станине можно приварить 2 формы вместо одной.
Некоторые мастера-умельцы могут похвастать и более совершенным механизированным оборудованием. И правда, ручной станок можно усовершенствовать и повысить производительность брикет, установив вместо ручного привода гидравлический домкрат. Чтобы собрать такой агрегат, придется немало повозиться, зато и результат получится куда лучше.
Ручной станок с гидравлическим домкратомПримечание. Даже используя гидравлический домкрат в самодельном прессе, создать давление хотя бы 300 Бар все равно не удастся. Поэтому воспроизвести заводскую технологию без добавления воды и связующих все равно не получится.
Невзирая на большие трудности с изготовлением деталей, кое-кому из мастеров удалось собрать шнековый пресс и получить брикеты довольно приличного качества. Об этом свидетельствуют отзывы таких людей на форумах. Но все они отмечают большие затраты на производство деталей шнека и корпуса из стали высокого качества. Опять же, без электрического привода здесь не обойтись, при самом скромном подсчете требуется двигатель мощностью не менее 7 кВт.
Самодельные брикеты – за и против
Причины, из-за которых данный вид топлива очень привлекателен, понятны. Когда у человека имеется собственное древесное производство либо возможность дешево покупать опилки для брикет, то мысли об их изготовлении в домашних условиях вполне закономерны. Дело в том, что далеко не всякая отопительная техника приспособлена для сжигания опила. Как правило, древесная мелочь в обычной печи или котле сгорает быстро и отдает мало тепла, да еще и половина просыплется в зольник.
Для успешного сжигания отходов древесины нужен специальный котел шахтного типа или верхнего горения. Сделать такой довольно сложно, гораздо радужнее видится перспектива прессования опилок в топливные брикеты.
![]()
Оказывается, здесь тоже не все так просто и вот почему:
- Покупать заводское сушильное и прессовое оборудование – неоправданно дорогое мероприятие. Дешевле приобрести готовые евродрова.
- Можно сделать пресс для брикет самому и делать их кустарным способом. Но изделия будут низкого качества и дадут мало тепла, а времени отнимут много.
Пункт второй требует разъяснения. Из-за невозможности соблюсти технологию «кирпичики» после сушки получаются легкими из-за малой плотности. Их удельная теплота сгорания втрое ниже, чем у древесины, значит, для отопления их понадобится втрое большее количество. Весь процесс займет массу времени и отнимет много энергии. Да и хранить такой объем топлива, чтобы оно не набралось влаги, весьма затруднительно.
Познавательное видео для энтузиастов, желающих давить заняться ручным брикетированием разнообразных домашних отходов:
youtube.com/embed/I0aHw8CmE3o?feature=oembed» frameborder=»0″ allow=»accelerometer; autoplay; encrypted-media; gyroscope; picture-in-picture» allowfullscreen=»»/>
Заключение
Изготавливать топливные брикеты своими руками на самодельном оборудовании, в принципе, можно. Но для этого нужно иметь достаточно свободного времени и место для сушки и хранения горючего. Также важно, чтобы опилки не приходилось возить издалека или дорого покупать. При таком раскладе мероприятие вообще теряет всякий смысл, лучше уж купить грузовик дров. Выбор за вами, уважаемые домовладельцы.
Интересная конструкция пресса для изготовления топливных брикетов
Наш мир не стоит на одном месте, поэтому самые ультрасовременные технологии проявляют себя в таких отраслях, в которых как может показаться придумать что-то новое совершенно не возможно! Самым ярким тому доказательством, которое смело можно привести здесь в виде примера, являются топливные брикеты.

Для создания топливных брикетов не нужны какие-нибудь запрещенные технологии, космические наработки и т.д. В основе простейшего станка для брикетирования лежит обычный пресс. Поэтому наладить производство таких дров, с некоторыми улучшенными свойствами по отношению к обычным дровам, дело вполне реальное. Топливный брикет — это измельченная древесина, разнообразные стружки, опилки, угольные отходы и даже шелуха от семечек, которые спрессованы в определенную форму, удобную для хранения и транспортировки. Так же имеются и другие достоинства данного вида топлива. Вот некоторые из них:
Увеличенная температура горения и соответственно более высокая теплоотдача. Так как брикеты спрессовываются под большим давлением, то, соответственно имеют большую плотность, что позволяет им дольше гореть по сравнению с топливом такого же объёма. Брикеты уменьшают количество образования сажи и золы. И многое другое.
Вот о таком станке, который своими руками изготовил автор Ютуб-канала МихалычTV или своими руками и пойдет речь в данной статье.
Для работы необходимы:
сварочный станок
болгарка
дрель со сверлами разного диаметра
Шаг 1.
Автор приступает к изготовлению загрузочных бункеров. Для этого используется профильная труба квадратного сечения. Отпиливаются 4 заготовки необходимого размера, в которых сначала накерниваются места для отверстий, а потом высверливаются сами отверстия во всех всех заготовках со всех 4 сторон. После данной процедуры поверхности подвергаются шлифовке как изнутри, так и снаружи. Далее все детали сваривают, предварительно поставив между ними проволоку диаметром 6 мм. Это нужно для того, чтобы во время прессовки топливной массы из нее свободно выходила влага. Для того чтобы масса при загрузке не забивала межъемкостные промежутки, там будут приварены заглушки из той же проволоки.
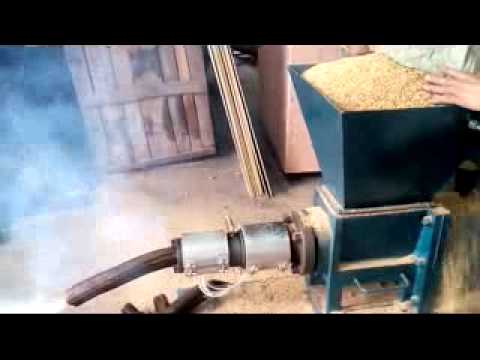
Шаг 2.
Нарезаются 4 металлические полосы, которые будут играть роль юбки на загрузочных емкостях. Служат они ограничителями, чтобы во время загрузки топливная смесь не выпадала за пределы емкостей. После автор изготавливает дно для емкостей. Оно должно быть открывающимся, чтобы полученные брикеты можно было легко и удобно извлечь из станка. Отрезается пластина, которая усиливается по бокам ребрами жесткости из профильной трубы или уголков. Это важный момент так как на эту часть станка будет приходиться вся нагрузка при работе пресса. В дне тоже делаются отверстия. Изготавливается шарнирное соединение для открывания дна.
Далее автор изготавливает так называемые поршни, которые будут входить внутрь загрузочных емкостей и прессовать смесь. Для этого к пластине приваривается 4 куска профильной трубы, на концах которых приварены площадки, размером как и диаметр загрузочных емкостей. Эти площадки будут давить на смесь и прессовать ее. Верх поршневой группы усиливается уголками.

Шаг 3.
Автор начинает собирать изготовленные части в единое целое. Приваривается к основе ограничивающая юбка и опоры станка. Ставится дно.
Шаг 4.
К основанию станка привариваются упоры для гидравлического домкрата. Сам домкрат установлен на крышку поршневой группы и на поперечную перекладину, к которой он закреплен с помощью уголков на подвижное болтовое соединение. Имеющаяся сбоку длинная рукоять помогает в поднятии домкрата и поршневой группы для закладки топливной смеси. Конечно это очень неудобно и в плане загрузки, и в плане эксплуатации станка. Но тем не менее идея достаточно интересная и работоспособная.
Вот, по словам автора, результат работы данного станка. Загружая большее или меньшее количество смеси, на выходе получаем брикеты нужного вам размера.
Источник (Source) Становитесь автором сайта, публикуйте собственные статьи, описания самоделок с оплатой за текст.
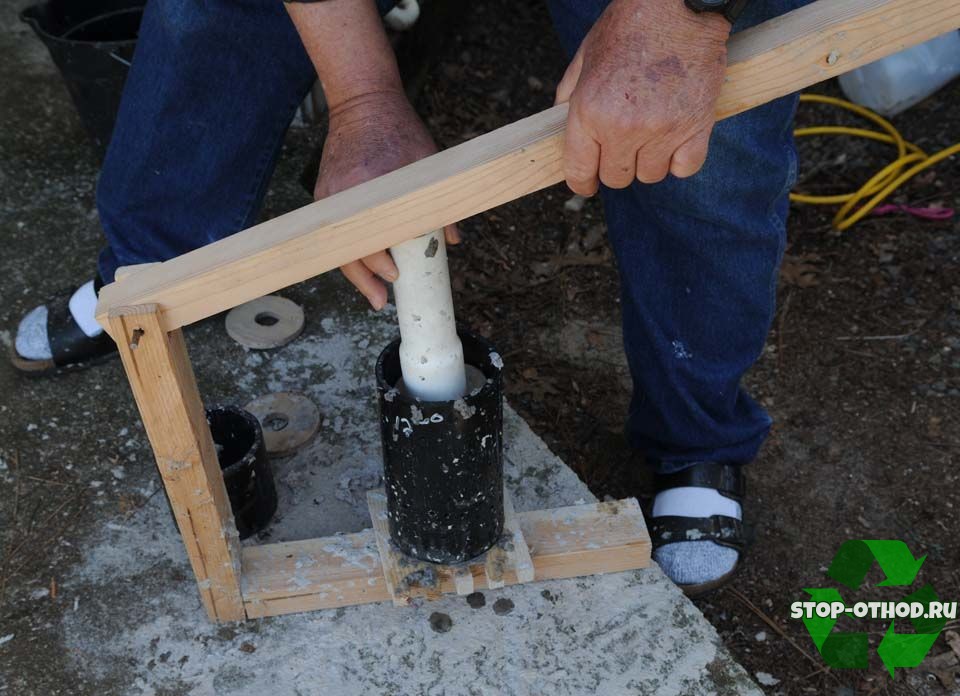
Как сделать пресс для топливных брикетов
Здравствуйте, уважаемые читатели и самоделкины!Такие отходы как опилки и разного рода макулатура, малопригодны для сжигания в котлах на твердом топливе. Для того, чтобы топить такими отходами — нужен либо специальный котел, либо из них нужно делать топливные брикеты.
В данной статье автор YouTube канала «Самоделкин Иван» расскажет Вам, как он сделал специальный пресс для изготовления топливных брикетов.
Такой пресс не очень сложен в изготовлении, однако потребуется небольшой объем сварочных работ.
Материалы, необходимые для самоделки.
— Стальной уголок, профильная труба, полоса, 6-мм лист
— Болты, гайки, шайбы, стальная шпилька
— Аэрозольная грунтовка, эмаль.
Инструменты, использованные автором.
— Шуруповерт, кобальтовые сверла по металлу
— Коронки по металлу
— Кондуктор для сверления отверстий
— Сварочный полуавтомат, маска хамелеон
— Магнитные уголки для сварки
— Насадка на шуруповерт «точилка для сверл»
— Гейферный захват, F-струбцины
— Горизонтальная ленточная пила, ленточный шлифовальный станок
— Электронный штангенциркуль, полуавтоматический керн
Процесс изготовления.

Основной частью станочка будет так называемая «матрица», в которой будут спрессовываться брикеты.
Пресс-форма изготавливается из профильной трубы 100×60 мм. Отрезок длиной 120 мм мастер получает на ленточной пиле, хотя можно обойтись обычной болгаркой.
Так как смесь будет состоять из макулатуры с водой (или опилок с добавлением клеевого раствора), то нужно сделать отверстия для выхода излишков жидкости.
Со всех наружных сторон заготовки наносится разметка с шагом 20 мм.
Используя керн, мастер намечает центры будущих отверстий на пересечении линий.
Сверление отверстий лучше выполнять на станке, ввиду большого их количества. При отсутствии сверлильного станка, можно воспользоваться простым кондуктором для сверления отверстий и шуруповертом.
В качестве прижима послужит кусочек стального уголка 50×50 мм длиной 90 мм.
Такая деталь отлично входит в пресс-форму, с небольшими зазорами по сторонам. Эти зазоры даже необходимы для того, чтобы поршень не заклинивало в форме.

Для стойки подойдет профильная труба 40×40 мм, к нижней части которой будет крепиться основание размерами 150×70 мм. Его мастер вырезает из стальной пластины толщиной 6 мм.
Углы заготовки закругляются на ленточном шлифовальном станке. Также в ней высверливаются четыре 10 мм отверстия для крепежных болтов.
Для быстрой заточки сверл можно использовать вот такую насадку для шуруповерта.
Для того, чтобы закрепить пресс-форму на стойке, потребуется проставка из отрезка профильной трубы 40×25 мм длиной 100 мм.
При сваривании элементов конструкции между собой, автор фиксирует их гейферным захватом.
Профильная труба приваривается к пресс-форме прерывистым швом. Так не перекрывается часть отверстий, и не поведет саму форму.
Частью шарнирного механизма послужит вот такая толстостенная цилиндрическая втулка. Ее нужно обрезать по длине так, чтобы она входила внутрь стойки.
Далее, в верхней части стойки, нужно сделать проушину для рычага из профильной трубы 25×25 мм.

Также сверлятся два отверстия под болт М12.
Втулка устанавливается на свое место, и через нее продевается болт.
Итак, рычаг имеет длину 750 мм, и на одном его торце нужно сделать выборку для плотного соединения со втулкой.
Втулку нужно приварить к рычагу с обеих сторон. Это место можно дополнительно усилить парой накладок из стальной полосы.
Для удобства загрузки материала в пресс-форму, на ее верхней части нужно сформировать горловину.
С тыльной стороны мастер приваривает кусочек стальной полосы шириной 40 мм. Она как раз перекроет открытый торец проставки между формой и стойкой.
С боковых сторон она должна выступать на 25 мм. Оставшийся периметр обваривается 25-мм полосой.
Также можно сделать небольшой наклон полос.
С нижней стороны пресс-формы нужно установить откидную крышку. Автор делает ее из стальной полосы толщиной 4 мм.
Закрепляться эта крышка будет на оси из стальной шпильки М10. Проушины для этой оси вырезаются из полосы толщиной 10 мм.
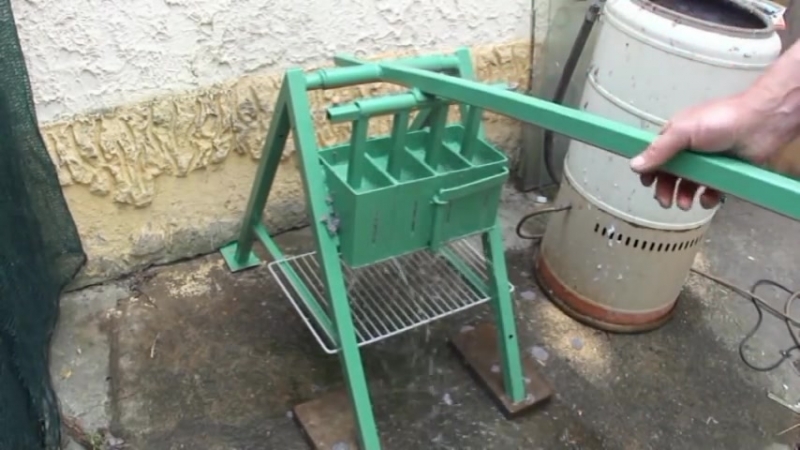
К передней части мастер приварил пару гаек М10, и сделал механизм замка.
Крючок вырезан из куска стального уголка. А примененная шпилька при закрывании немного приподнимает крючок, дополнительно прижимая им крышку.
В крышке также проделано несколько отверстий, и она приварена к оси.
Пресс-форма приваривается к стойке на расстоянии 100 мм от оси рычага до верхней части формы. Это и будет полный диапазон хода поршня.
Верхняя часть шарнирного механизма сделана из профильной трубы 25×25, длиной 30 мм. Этот кусочек приваривается к рычагу.
Шарнирная схема соединения штока поршня и рычага аналогична шарнирному соединению рычага со стойкой.
Ко второму концу штока приваривается тот самый «поршень» из стального уголка.
Автор не проваривал швы полностью, а лишь прихватил детали между собой для проверки работы механизма.
Пресс готов к работе, и для него нужно подготовить материал. Мелко измельченный картон, и другую макулатуру Иван замачивает в воде на 10 минут.

Готовая смесь загружается в пресс-форму, и излишки воды выходят через отверстия при прессовке.
Чтобы вытащить готовый брикет, достаточно открыть лючок и выдавить брикет поршнем.
В итоге получаются вот такие брикеты. Макулатуру и бумагу нужно достаточно сильно измельчать, чтобы получить более плотные брикеты и равномерную структуру.
Заготавливать такие брикеты лучше летом, ведь сушить их желательно на солнце. Если это выполнять внутри помещения — то можно достаточно сильно поднять влажность воздуха, что не очень желательно.
После проверки пресса, мастер окончательно проварил швы. А для защиты изделия от коррозии, он зачистил все его поверхности, и обезжирил их.
Затем наносится слой грунтовки по металлу, а после ее высыхания — пара финишных слоев эмали.
Благодарю Ивана за простую конструкцию пресса для изготовления топливных брикетов.
Всем хорошего настроения, крепкого здоровья, и интересных идей!
Подписывайтесь на телеграм-канал сайта, чтобы не пропустить новые статьи.
Авторское видео можно найти здесь.
Источник (Source) Становитесь автором сайта, публикуйте собственные статьи, описания самоделок с оплатой за текст. Подробнее здесь.
Ручной брикетировочный пресс — утилизация макулатуры и опилок — VUTHISA
Для этого слайд-шоу требуется JavaScript.
Зависимость от дров для приготовления пищи в развивающихся странах привела к истощению лесов со скоростью 2,5–3% в год. Именно здесь, в беднейших частях мира, сельские жители проводят значительную часть своего времени, собирая дрова для приготовления, разогрева и изготовления древесного угля. Чтобы противостоять этой зависимости от древесины, в начале 80-х годов были предприняты попытки найти альтернативы. Одна из изучаемых альтернатив — изготовление топливных брикетов из недревесной биомассы для приготовления пищи. Доктор Брайант и студенты Вашингтонского университета в США разработали новый недорогой процесс изготовления брикетов с использованием недревесных сельскохозяйственных остатков, обычной воды и ручного пресса для древесины.
Процесс брикетирования был прост, и его можно было внедрить в бедных сельских общинах, требуя мало технологий и очень мало денег. С небольшими усилиями сельчане теперь могли создавать свои собственные дрова из сельскохозяйственных остатков.Чтобы сделать брикет, обычные листья, трава и солома измельчались и превращались в пюре. Затем эту пасту прессовали в круглые лепешки и сушили. Полученный брикет будет продаваться как заменитель топливной древесины и древесного угля на местном рынке. В 1994 году Фонд «Наследие», США, подхватил процесс изготовления брикетов Брайанта и расширил масштабы своей деятельности. Сегодня благодаря обучению Legacy Foundation и онлайновым медиа-сервисам технология и процесс производства брикетов распространилась на одиннадцать других стран, таких как Гаити, Уганда, Мексика, Непал, Кения, Мали и Танзания. Фонд также выпустил 8 технических / учебных пособий по всем известным аспектам производства брикетов.
Vuthisa приобрела права на продвижение и распространение этой технологии в южной части Африки. Фонд Legacy Foundation выпустил на рынок новый пресс с трещоткой, который заменит деревянные прессы, которые теперь производятся в Южной Африке.
Пресс с храповым механизмом спроектирован так, чтобы складываться при транспортировке, а после установки в несколько простых шагов обеспечивает необходимую мощность для сжатия опилок и бумаги, смешанных во влажной суспензии, в топливные брикеты средней плотности.Используя обычные инструменты и навыки, Ratchet Press может работать как на индивидуальном, так и на постоянном предприятии по производству брикетов. Несмотря на то, что он компактен и портативен, он может обеспечивать почти такое же усилие, как и их более крупный пресс для дерева с комбинированным уровнем Mini Bryant. Они выпустили 3 руководства Ratchet Press, а именно; Руководство по сборке, эксплуатации и маркетингу пресса с трещоткой, в котором подробно объясняется, как построить (если не требуется фактический пресс, заказанный у Vuthisa) пресс, упорядочить и подготовить материалы и успешно управлять прессом.
Посмотрите это демонстрационное видео о нашем последнем Ratchet Press:
Vuthisa также начала производство тестовых брикетов (TBM) по лицензии, поэтому посетите наш интернет-магазин, чтобы узнать цены. Довольно большая часть людей, которые покупают руководства пользователя, никогда не берут на себя обязательство строить настоящие печатные машины, возможно, из-за нехватки времени или денег или из-за отсутствия инструментов для мастерских и / или технических ноу-хау. Закажите этот «Пресс-кит», чтобы ознакомиться с концепцией ручных брикетировочных машин низкого давления для дерева и металла.
Поставьте отметку «Нравится» на нашей фан-странице в Facebook и получите БЕСПЛАТНУЮ ссылку для скачивания в формате PDF на «Тестовый брикетировщик»:
Тестовая брикетировочная машина может быть построена менее чем за 125 долларов США и почти не требует обслуживания, требуются только основные работы по сверлению и сварке (не более 10 см). Если вы хотите привлечь финансирование для развертывания программы с использованием этой технологии, эта печатная машина будет наиболее подходящей для этой цели. Как уже упоминалось, БЕСПЛАТНАЯ ссылка для скачивания «Конструкция тестового брикетировщика и руководство пользователя » будет поставляться с каждым руководством, приобретенным на этом сайте.
Посмотрите это демонстрационное видео о машине для производства тестовых брикетов:
Также посетите наш аккаунт в Instagram, чтобы увидеть больше фотографий: https://www.instagram.com/vuthisa/
Закажите трещоточный пресс здесь (минимальный заказ 2 шт.):
Для получения дополнительной информации о процессе брикетирования и доступа к их электронным практическим руководствам посетите эту страницу:
Нравится:
Нравится Загрузка. ..
Пресс для брикетирования древесины Alois
Алоис Шмид пишет:До недавнего времени это был мой пылесос. Я перешла на бочки из мешков потому что стружку можно придавить в бочках, а бочки можно сложены.
Но стружку в дровяной печи сжечь тяжело, а бросать не хотелось их тоже. Я искал пресс для брикетов. Промышленные машины доступны по цене от 10 000 евро.Но есть разные самодельные прессы для брикетов в сети, например здесь: http://www.brikomat.com
Для своего самодельного брикетировочного пресса я купил новый пылеуловитель. за 600 евро, включая трубопроводы. Я также купил Этот электрический дровокол в то время стоил 200 евро. Я начал работать над прессом для брикетов два года назад.
К настоящему времени машина работает автоматически, без проблем.Он все еще может использовать улучшения, а скорость производства очень
в зависимости от типа используемой стружки. Машина работает быстрее всего с
короткая стружка твердых пород. При беге немного тормозит
с длинными тонкими стружками хвойных пород. Чем выше содержание лигнина
(см. Википедию)
тем тверже становятся брикеты.
Контроллер имеет переключатели на обоих концах диапазона, а также датчик гидравлического давления.В отличие от промышленных машин, здесь нет сжатие брикетов, поэтому давление строго зависит от трение брикетов в канале. Это делает контроль машина посложнее.
Чем глубже поршень входит в трубу, тем короче оставшаяся труба, по которой должны проходить брикеты, и тем меньше трение. Если нырнуть слишком далеко, брикеты не будет достаточно сжатым и развалится.Но если удары будут слишком короткими, трение брикеты в трубе могут подняться слишком высоко, и машина остановится вниз от избыточного давления. Затем мне нужно вручную очистить застряли брикеты, высверлив их из трубы.
Длина хода должна соответствовать типу используемой древесины.
График слева показывает, как работает контроллер. После 3,5 секунд хода (стадия 1) гидравлическое давление
должно быть минимум 5 бар.На ступени 2 и 3 давление должно быть не менее 6 и 10 бар соответственно.
Если требуемое давление не достигается, баллон возвращается на
еще один ход, чтобы прижать больше материала.
Если давление достигает пика и падает более чем на 3,5 бар
до достижения стадии 4 он также начинает новый ход.
По достижении ступени 4 цилиндр возвращается только после падения давления.
ниже 50 бар или при срабатывании концевого выключателя.
1 бар — это 100 килопаскалей, или около 14.5 фунтов на квадратный дюйм.
Вышеуказанные параметры времени и давления можно регулировать, и я не всегда работать с этими значениями.
Электромагнитный магнит (зеленый) для управления гидравликой и электронным датчиком давления внизу (черный). Датчик может показывать до 160 бар.
Прижимной стержень с выступом на конце. Выступ
Помогает при нанесении нескольких ударов сформировать единый брикет, который не развалится.
Крепление нажимного стержня к главному цилиндру.Винты позволяют снятие прижимного стержня и помощь при обратном ходе.
Изначально я использовал трубу с внутренним диаметром 35 мм, но гидравлическая цилиндр имел для этого недостаточную силу. Я добавил трубу поменьше внутри исходной трубы с внутренним диаметром 28 мм. При силе 7 тонн это должно дать мне давление 1136 кг / см 2 . Для трубы большего размера она составила 727 кг / см 2 . Еще лучше было бы давление.
Я разрезал трубу и загнул получившиеся «створки» наружу. Контейнер прикручены к закрылкам.
Это показывает, где раньше был раскалывающий клин. На его месте прижимная труба и прикрепленный контейнер для стружки.
Шнеки перемещают стружку в отверстие в прижимная труба.
Оранжевые шестерни входят в зацепление со шнеками, как червячные.Шестерни
помогают предотвратить налипание стружки на шнек, чтобы предотвратить
стружка заедает.
Контейнер для стружки, полный стружки.
Я использовал мотор стеклоочистителя от Opel Ascona до мощность шнека …
… в сочетании с цепями и звездочками от велосипеда.
Магнитный датчик определяет вращение шнека.Если нет импульсов обнаруживаются за десять секунд работы шнека, предполагается, что шнеки заклинивают, и машина останавливается.
Здесь вы можете увидеть снятый с машины шнек. Шнек крепится к ступицам с помощью двух болтов M8.
Это показывает, как был сделан шнек.
Это выходная сторона машины. Колесо входит в зацепление брикеты через прорезь в трубе.
Магнитный датчик обнаруживает винты в сторона колеса. Два оборота колеса составляют почти ровно один метр брикета. Количество брикетов и часы работы записываются, чтобы я мог подсчитать, сколько метров брикета в час производятся.
Еще одна причина контролировать производство брикетов:
Если вращение не обнаруживается более трех минут,
машина выключается. Либо емкость для стружки пуста, либо
стружка застряла или застряла на шнеках.
Колесо опирается на брикеты собственным весом. Шурупы по дереву со срезанными головками действуют как шипы для зацепления брикеты.
Брикеты подаются по пандусу в бочку.
На конце пандуса есть клин, чтобы брикеты отломались, если они станут слишком длинными. Иначе кто-то промахнется мимо ствола.
Друг построил для меня электронику, а программное обеспечение я написал сам.Переключатель на передней панели позволяет переключаться между непрерывным режимом работы. или работа по расписанию (например, работа в течение одного часа).
Большинство компонентов у меня уже лежало дома. У меня был только купить датчик давления и трансформаторы новые. Корпус, куплены контроллеры мотора и магнитные датчики б / у. Пока что эта пресса мне стоило от 600 до 800 евро.
Конечно, машину можно было оптимизировать и дальше.Можно предварительно сжать
стружка, которая ускорит производство. Но это было бы тоже
пока сложно. Я думаю об улучшении
механизм подачи. Моим последним изменением было запустить шнеки в
противоположное направление.
Изменение направления шнека фактически увеличило производительность, так как стружка теперь проталкивается ближе к отверстию в трубе. Я тоже думаю об альтернативе шнекам, но придется подождать, пока не будут завершены другие проекты.
Позже напишу подробнее о своей мастерской, но сначала мне нужно немного прибраться.
Это показывает, как я использую брикеты в дровяной печи. Через дверь видно, что сейчас лето, так что сейчас только позирование.
Алоис позже добавил:
Я добавил в пресс киловаттметр, чтобы можно было потренироваться его эффективность.
Для показанного ствола я использовал смесь опилок, которая дает лучший выход. Я использовал опилки от настольной пилы от резки дрова, и строгальные стружки из клена.
Бочка вмещает 51,4 кг брикетов, а машина использовала 13,5 кг. КВтч электроэнергии для их производства.
Поскольку электроэнергия стоит около 0,25 евро / кВт · ч, моя стоимость электроэнергии составляет 3,35 евро.
Древесные брикеты стоят 2,25 евро за 10 кг, но моя электроэнергия Стоимость всего 0.65 евро за 10 кг. Но я не считаю стоимость машина или стружка.
Машина потребляет в среднем менее 1 кВт, поэтому потребовалось более 13 часов на производство. Я не смотрел время, потому что машина работает автоматически и без присмотра.
См. Также:
Еще проекты читателей на woodgears.ок.
Физиохимическая характеристика брикетов, изготовленных из различных видов сырья
Уплотнение биомассы может решить проблемы обработки, транспортировки и хранения, а также поддается автоматической загрузке и разгрузке транспортных средств и систем хранения. Целью данного исследования является сравнение физико-химических свойств брикетов из разного сырья. Сырье, такое как кукурузная солома, просо просо, трава луговой пуповины, опилки, трава голубиного гороха и стебли хлопка, уплотняли с использованием системы брикетирования.Физические характеристики включают гранулометрический состав, средний геометрический диаметр (GMD), плотности (объемные и истинные), пористость и температуру стеклования. Также был проведен анализ состава контроля и брикетов. Статистический анализ подтвердил наличие значительных различий в этих физических свойствах и химическом составе контрольных и брикетов. Корреляционный анализ подтверждает вклад лигнина в насыпную плотность и долговечность. Среди испытанного сырья стебель хлопка имел самую высокую объемную плотность 964 кг / м 3 , что в 11 раз больше, чем у контрольного стебля хлопка.Наивысшая (96,6%) и самая низкая (61%) стойкость были у кукурузной соломы и гороха голубиного.
1. Введение
В последние четыре десятилетия исследователи сосредоточили свое внимание на альтернативных топливных ресурсах, чтобы удовлетворить постоянно растущий спрос на энергию и избежать зависимости от сырой нефти. Биомасса кажется привлекательным сырьем из-за ее возобновляемости, изобилия и положительного воздействия на окружающую среду, которое приводит к отсутствию чистого выброса диоксида углерода и очень низкому содержанию серы. Биомассу очень трудно обрабатывать, транспортировать, хранить и использовать в ее первоначальном виде из-за факторов, которые могут включать в себя высокое содержание влаги, неправильную форму и размеры, а также низкую насыпную плотность.С помощью уплотнения можно производить уплотненные продукты одинаковой формы и размеров, с которыми можно легче обращаться с использованием существующего оборудования для погрузочно-разгрузочных работ и хранения, и тем самым снизить затраты, связанные с транспортировкой, погрузочно-разгрузочными работами и хранением. Tumuluru et al. [1] классифицировал обычные процессы уплотнения биомассы на прессование, гранулирование, экструзию и брикетирование, которые выполняются с использованием желонки, гранулятора, винтового пресса, поршневого пресса или роликового пресса.
Пакетирование, брикетирование и гранулирование являются наиболее распространенными методами уплотнения биомассы; Гранулирование и брикетирование — наиболее распространенные уплотнения, используемые для твердого топлива.
В общем, биомасса / сырье представляет собой ячеистый материал с высокой пористостью, поскольку внутренняя часть ячеек состоит в основном из воздуха, заполненного большими вакуолями в сухих условиях [2]. В общем, природные связующие, такие как лигнин, белок и крахмалы, присутствующие в исходном сырье, усиливают связь между частицами в процессе уплотнения. Из-за приложения высокого давления частицы сближаются друг с другом, вызывая силы притяжения между частицами, а естественные связывающие компоненты в исходном сырье выдавливаются из ячеек, образуя твердые мосты между частицами [3].Многие виды сырья, уплотнительные машины и параметры процесса влияют на качество уплотненных продуктов. Несколько исследователей сообщили, что состав сырья, такой как лигнин, гемицеллюлоза и экстрактивные вещества, типы сырья, фракция того же сырья, размер частиц исходного материала и содержание влаги, процент мелких частиц, тип уплотнительной машины, диаметр фильеры, предварительный нагрев / впрыск пара, температура и давление являются основными переменными, которые влияют на качество уплотненных материалов [4–12]. Состав сырья — одна из основных переменных; поэтому понимание изменений состава из-за уплотнения может быть полезно для понимания их поведения при уплотнении [1]. Обзор литературы показал, что только Theerarattananoon et al. [13] сообщили об изменениях в химическом составе до и после гранулирования различного сырья, без брикетирования. Размеры окатышей, развитие трения / сдвига во время окомкования и брикетирования будут разными. Следовательно, это исследование было предпринято с двумя целями: (1) изучить изменения химического состава различного сырья из-за брикетирования и (2) проверить связь различных переменных, которые влияют на объемную плотность и долговечность.
2. Материалы и методы
2.1. Подготовка и характеристика исходного сырья
Просо прутьевидное и трава луговой пуповины, полученные с различных местных ферм, были измельчены на молотковой мельнице (Speedy King, Winona Attrition Mill Co, MN) с использованием 8-миллиметрового сита для уплотнения и отправлены в Сельскохозяйственный университет Тамил Наду (TNAU). Коимбатур, Индия. Точно так же кукурузная солома, голубиная трава гороха и стебли хлопка были собраны с экспериментального поля в TNAU, Коимбатур, Индия. Опилки были получены на местной лесопилке, расположенной в Коимбаторе, Индия.Композиционные анализы сырья и брикетов, таких как общее содержание твердых веществ, целлюлозы, гемицеллюлозы, лигнина, золы и экстрактивных веществ, проводили в трех экземплярах, как описано Sluiter et al. [14–16] с использованием муфельной печи и ВЭЖХ и приведены в таблице 1.
| ||||||||||||||||||||||||||||||||||||||||||||||||||||||||||||||||||||||||||||||||||||||||||||||||||||||
Различные буквы в одном столбце означают, что средние значения статистически различаются (). |
2.2. Анализ размера частиц
Перед брикетированием средний геометрический диаметр измельченного сырья был определен с использованием стандарта ASAE S319.4 [17] с помощью встряхивающего устройства для сит Ro-Tap (WS Tyler Inc., Mentor, OH, USA) с Сито США с номерами 6, 7, 10, 16, 20, 30, 50, 70 100, 140, 200 и 325 (размеры отверстий сита: 3,35, 2,80, 2,00, 1,190, 0,841, 0,595, 0,297, 0,210 и 0,149 мм , соответственно). Для каждого испытания образец весом 100 г помещали в стопку сит, расположенных от самого большого до самого маленького отверстия.Время встряхивания сита составляло 10 минут, как указано в стандарте ASAE Standard S319. Средний геометрический диаметр (dgw) образца и геометрическое стандартное отклонение диаметра частиц (Sgw) рассчитывали в трех повторах для каждого сырья.
2.2.1. Брикетирование
Система брикетирования состоит из двигателя мощностью 40 л.с., загрузочного бункера и фильеры, производительность составляет 150–200 кг / ч. В системе можно было выбрать сечение матрицы 60 или 90 мм. Для этого исследования использовалась матрица диаметром 60 мм.На рисунке 1 показана система брикетирования вместе с сырьем и брикетами. Брикетировочная машина представляет собой простой горизонтальный брикетировочный пресс. Погрузочно-разгрузочный винтовой конвейер с электродвигателем мощностью 2 л.с., соединенным с редуктором и регулируемым шкивом с клиновым ремнем. Вал перемещает эксцентриковый диск через шатун, где круговое движение соединено с линейным движением. Эксцентриковый диск соединен с поршнем из легированной стали, который совершает возвратно-поступательное движение в неподвижном чугунном цилиндре. В поршне установлен штамп из закаленной и шлифованной легированной стали.Матрица из закаленной шлифованной легированной стали удерживается в стальном держателе матрицы. Сырье, прошедшее в бункер машины, перемещается в камеру, где пуансон проталкивает материал в матрицу, формирует цилиндрический брикет и проталкивает его дальше в разъемную матрицу и линию охлаждения. Брикеты были собраны и отправлены через FedEx в Государственный университет Южной Дакоты для дальнейшего анализа.
2.2.2. Плотность и пористость
Объемные плотности измельченного сырья и брикетов измеряли в соответствии со стандартным методом ASAE S269.4 декабря 01 [18]. Используемый контейнер представляет собой стеклянный контейнер объемом 2000 мл. Насыпная плотность рассчитывалась по массе сырья и брикетов, занимающих контейнер.
Многотомный пикнометр Micromeritics и ячейка (125 см 3 ), поставляемые с оборудованием, использовались для измерения истинной плотности образцов. Измерение основано на разнице давлений между известным эталонным объемом и объемом ячейки для пробы. Гелий используется в качестве газа для заполнения ячейки сравнения и образца на 19.5 ± 0,2 фунта на кв. Дюйм, как указано в руководстве к прибору. Истинная плотность материала измерялась по уравнению где — вес образца, — пустой объем ячейки для образца, — , — объем расширения, — давление до расширения, — давление после расширения.
Пористость — это мера пустот в материале, которая представляет собой долю объема пустот от общего объема; обычно находится между 0-1. Пористость рассчитывается по истинной плотности и объемной плотности, измеренным, как описано ранее:
2.3. Прочность
Долговечность брикетов определялась с использованием прибора для испытания на долговечность гранул (модель PDT-110, Seedburo Equipment Company, Чикаго, Иллинойс) по методу S269.4 [18]. Около 200 г брикетов были разделены на две партии по 100 г каждая. Каждую партию помещали в измеритель прочности гранул на 10 мин и работали со скоростью 50 об / мин. Образец был помещен на № 4 (4,75 мм) до и после галтовки и измеряли массу, остающуюся на сите. Затем рассчитывалась долговечность гранул, используя следующее уравнение: где — масса брикетов, оставшихся на грохоте после галтовки (г), и — масса брикетов, оставшихся на грохоте до галтовки (г).
2.4. Температура стеклования
Температуру стеклования ( ) исходного сырья оценивали с использованием дифференциального сканирующего калориметра (DSC) (серия Q, TM Model Q200, TA Instruments, New Castle, DE). Холодильная система охлаждения (RCS40), снабженная модулем DSC, может контролировать температуру образца от -40 ° C до 400 ° C. Примерно 2,0–2,2 мг исходного сырья находилось в алюминиевом поддоне и подвергалось нагреванию в диапазоне от 10 до 150 ° C со скоростью нагрева 5 ° C / мин.Пустой алюминиевый поддон считался эталонной ячейкой. Программное обеспечение универсального анализатора, предоставленное TA instruments (New Castle, DE), было использовано для анализа термограмм с использованием метода интегрирования половинной высоты [19].
2.5. Статистический анализ
Все измерения физических и химических свойств были выполнены в трех экземплярах, и данные были проанализированы с помощью процедуры Proc GLM для определения статистической значимости с использованием SAS 9.2 [20] с использованием ошибки типа I ( α ), равной 0.05.
3. Результаты и обсуждение
Брикетировочные машины могут обрабатывать более крупные частицы с широким диапазоном содержания влаги без дополнительных связующих, а не грануляторы. Кроме того, трение / сдвиг между частицами и брикетирующим устройством намного меньше, чем при гранулировании / кубовании [21]. Стандартная форма топливной таблетки — цилиндрическая, диаметром от 6 до 8 мм и длиной не более 38 мм. Если гранулы имеют диаметр более 25 мм, их обычно называют «брикетами».Размеры окатышей, указанные в литературе, составляют 4–7 мм в диаметре и 13–23 мм в длину [22, 23], тогда как брикеты могут иметь диаметр от 25 до 100 мм и длину от 25 до 280 мм [24]. Размеры, трение / сдвиг, нагнетание пара / предварительный нагрев и связующее будут иметь гораздо больше различий в полученных брикетах, которые следует учитывать при сравнении данных по брикетам, представленных в этом исследовании.
3.1. Анализ размера частиц
Помимо содержания влаги, гранулометрический состав и размер частиц являются двумя важными факторами, которые влияют на объемные физические свойства исходного сырья.Насыпная плотность измельченного сырья зависит от размера и гранулометрического состава. Распределение частиц по размерам также отражается на доступной площади поверхности. Размеры частиц влияют на истинную плотность исходного сырья [25], а также на долговечность [9]. Анализ размера частиц исходного сырья показан на рисунке 2. В целом, все исходное сырье имело более 50% размера частиц в диапазоне 0,297–1,68 мм, как видно из рисунка. Основная часть PCG сместилась в сторону частиц меньшего размера из-за их игольчатой формы (рисунок 1 контроль PCG).Распределение проса просо, голубиного гороха и стебля хлопчатника было одинаковым, как видно из рисунка 2. Хотя во время измельчения использовались разные сита / сита, аналогичная тенденция распределения частиц по размерам (нормальное распределение) наблюдалась для проса проса [26], обрезки оливковых деревьев. [12], солома ячменя, канолы, овса и пшеницы [27]. Colley et al. [26] сообщили, что сита с размером отверстий 0,595 и 0,850 мм удерживали 29,5 и 38,6% измельченного проса при использовании сита 3,18 мм; в данном исследовании, стяжка 8 мм
Превращение отходов в энергию с помощью брикетов из биомассы
В среднем США ежегодно производят около 250 миллионов тонн твердых отходов.Более половины этих отходов — это органические материалы, такие как бумага, картон, садовая обрезка или побочные продукты сельскохозяйственной и лесной промышленности. Этот органический материал, иначе известный как биомасса, может быть преобразован в брикеты из биомассы, которые могут конкурировать или сосуществовать с традиционными горючими веществами.
Что такое брикет из биомассы?
Рецепт брикета из биомассы относительно прост. Брикеты являются продуктом прессования под низким давлением биомассы, такой как опилки, сельскохозяйственные отходы, бумага и т. Д.Этот процесс сжатия позволяет биомассе гореть дольше, чем если бы она оставалась свободной. При правильном формировании сжатая биомасса может гореть при тех же температурах и в течение того же времени, что и древесина, гранулы или уголь.
Чтобы подготовить сырье для процесса прессования, органические материалы разделяются на предмет их горючести и характеристик, а затем дробятся или измельчаются на грубые порошкообразные опилки. Затем этот порошок пропускают через пресс с механическим приводом высокого или низкого давления, который нагревает порошок и проталкивает его через матрицу.В зависимости от потребностей конечного пользователя брикеты имеют различные формы и размеры, от больших однородных твердых брикетов до более мелких окатышей.
Реальные преимущества брикетов из биомассы
Представьте себе, что в вашем котле сжигается источник топлива, который дает больше энергии на ваш доллар, чем уголь, но при этом выделяет меньше токсичных парниковых газов. Брикеты из биомассы экологически безопасны, полностью возобновляемы и просты в использовании. Их можно использовать для кипячения воды и выработки энергии пара, приведения в действие турбин, вырабатывающих электричество, и даже для обогрева домов и предприятий.
При минимальной механической подготовке вы можете сжигать брикеты биомассы в котлах и печах, построенных с учетом угля или дров. Вы даже можете сжигать уголь и биомассу вместе, если хотите. Брикеты из биомассы легко справляются с любым процессом, в котором вы полагались бы на древесину или уголь, и могут быть адаптированы для удовлетворения ваших конкретных потребностей. Их можно использовать (и даже создавать) на личном уровне или масштабировать для поддержки целых предприятий и даже городов.
Наконец, брикеты из биомассы сокращают потребность в импорте и экспорте ископаемого топлива по всему миру, поскольку они могут производиться внутри страны из местных растительных, животных и твердых бытовых отходов.
Общая кинематика — ваш специалист по вибрации
Когда дело доходит до процесса просеивания, разделения и подготовки биомассы к превращению в энергию, вы можете положиться на обширную линейку вибрационного оборудования General Kinematics. У нас есть полный спектр современного оборудования, которое вы не найдете больше нигде. Это технологическое преимущество плюс десятилетия опыта — выигрышная комбинация, которая поможет вам максимально эффективно использовать биомассу в энергии.
Свяжитесь с одним из членов нашей команды GK сегодня и позвольте нам показать вам, как мы можем произвести революцию в вашей работе.
Автоматический пресс для брикетирования опилок Hot Press от Китайского производителя, завода, завода и поставщика на ECVV.com
Экспортные рынки: | Северная Америка, Южная Америка, Восточная Европа, Юго-Восточная Азия, Африка, Океания, Средний Восток, Восточная Азия, Западная Европа |
---|---|
Место происхождения: | Хэнань в Китае |
Детали упаковки: | Упаковка деревянных ящиков |
Краткие сведения
- Послепродажное обслуживание: Инженеры, обслуживающие технику за рубежом
- Гарантия: 1 год
- Сертификация: ISO
- Состояние: Новый
- Особенности: автомат
- Вес: 850 кг
- Размер (Д * Ш * В): 1700 * 660 * 1300 мм
- Мощность (Вт): 11 кВт
- Напряжение: 380в
- Номер модели: РББ-1
- Название бренда: РБ
- Производственная мощность: 200 кг / ч
- Заявка: брикет из биомассы
- сырье: опилки, рисовая шелуха и т. д.
- Влажность материала: 12%
- размер материала: 3-5 мм
Технические характеристики
Машина для производства брикетов из опилок
Конструкция винтовой машины для производства брикетов из биомассы для продажи
1 бункер
2 теплоизоляционная крышка
3 нагревательный круг
4 гребных винта
5 нагревательная трубка
6 коническая втулка
7 стентов внутренний рукав
8 стентов
Применение материала:
1.Идеальным размером были опилки 3–5 мм.
2. Идеальный уровень влажности 8% -12%.
3. Древесные опилки, древесные отходы, рисовая шелуха, листья, скорлупа кокоса, скорлупа арахиса и так далее.
Брикетировочная машина для древесного угля была награждена 2 патентами, показывающими характеристики высокой производительности, низкого энергопотребления, долговечности и компактности. Многие данные о производительности, такие как емкость, плотность древесных брикетов, потребление электроэнергии и степень пригодности для носки, достигли высокого уровня.Машина для брикетирования древесного угля может использоваться как машина для брикетирования древесного угля при замене некоторых запасных частей. Наружный диаметр готовых брикетов 50-80 мм.
Эта машина используется для превращения опилок в половинки угля. Оборудован системой обогрева с автоматическим регулированием. Изделие этой машины можно использовать для обогрева котла, камина и т. Д. Для обогрева дома. Используя присущие древесному сырью характеристики, посредством шнековой экструзии, высокой температуры и высокого давления, древесное сырье для создания микроволоконного лигнинового пластика объединяется в топливный стержень.
Модель | RBB-1 | РББ-2 | РББ-3 |
Производительность (кг / ч) | 160-200 | 220–260 | 280-320 |
Мотор | 11 кВт | 15 кВт | 18.5 кВт |
Диаметр брикета (мм) | 50мм-60мм | 50мм-60мм | 70мм-80мм |
Размер (мм) | 1700 * 660 * 1300 | 1860 * 800 * 1360 | 1900 * 900 * 1450 |
Процесс брикетирования металла и дерева
Простые шаги по созданию ценности из ваших отходов
В конце концов, одна из самых больших головных болей для любого магазина — это отходы от повседневной работы.В какой бы форме они ни были, остаточные отходы занимают место, вызывают проблемы с безопасностью у вас и ваших сотрудников и требуют денег для утилизации.
Вот где приходит на помощь RUF. RUF Briquetting Systems позволяет вам легко превратить иначе бесполезный материал в компактный, легкий в управлении источник дохода. После первоначальной настройки вам останется только загрузить брикетер ломом, включить машину и посмотреть, как ваша работа станет более эффективной, устойчивой и прибыльной.
Преимущества брикетировщиков RUF:
- Работает без оператора
- с гидравлическим приводом
- Управляется программируемым логическим контроллером (ПЛК)
- Продам полученные металлические брикеты или древесные брикеты
- Восстановленная стоимость СОЖ (масла, смазки) из металлов
- Компактная конструкция для легкой интеграции в производственный цех
- Разработан для автоматической круглосуточной работы с малой мощностью
- Готовность к обращению и транспортировке сразу после пресса
Получите больше от ваших материалов
Как наши брикеты превращают ваш лом в брикеты:
- В брикетировщик загружены остаточные отходы.
- Материал транспортируется в камеру предварительной загрузки конвейерным шнеком.
- Устройство предварительного нагнетания вдавливает материал в основную камеру прессования (для обеспечения постоянного размера брикета).
- Главный пресс-плунжер сжимает материал в форму и придает брикету окончательную форму и плотность.
- Форма с возвратно-поступательным движением перемещается в сторону, и брикет выталкивается параллельными эжекторами, когда формируется второй брикет.
Примечание. Этот принцип применяется к прессу пресс-формы, который прессует и выталкивает брикеты параллельно, увеличивая почасовую производительность. Наши слайд-прессы сжимают и сжимают только один брикет за раз. Хотите знать, какой тип брикетировщика подходит для вашей работы? Свяжитесь с нами, чтобы узнать.
Проверим ваш лом
Не уверены, получится ли брикет, или просто хотите посмотреть, что мы можем сделать? Лучший способ узнать это — протестировать наши брикетеры на собственных отходах.Отправьте нам свой лом, и мы отправим вам брикет.
Чтобы узнать больше о наших машинах для брикетирования или их применениях, позвоните 888-894-5773 или свяжитесь с нами сегодня.
Посмотрите, как работает процесс брикетирования древесины
Посмотрите, как работает процесс брикетирования металла
.