Печка из дисков автомобиля: Печь из дисков автомобиля (колесных) своими руками
Печь из дисков автомобиля (колесных) своими руками
Печь из дисков от автомобильных колес способна обеспечить обогрев комнаты до 15-16 кв. м, топку бани или стать недорогим эффективным варочным прибором, о чем, собственно, и есть эта статья. Ее главное достоинство доступность высококачественного материала – толстой, стойкой и прочной стали. Котельная сталь в листах и профилях дорога, а обычная конструкционная в печном строении быстро прогорает.
В дополнительном преимуществе печи из дисков можно убедиться на опыте. Возьмите два куска металла примерно одного размера и веса: один из простой стали, а другой вырезанный из колесного диска, и нагрейте посильнее, хотя бы в кухне на газе. От первого сразу пойдет запах горячего железа, а второй можно раскалить до оранжевого (ок. 900 градусов), ничего неприятного в воздухе не ощущая. Печь из колесных дисков практически не сушит воздух и не выделяет в атмосферу вредные пары, потому что диски для колес делаются из спецсталей, стойких к коррозии.
Что нужно знать о дисках
Печь на отработке. изготовленная с использованием автомобильных дисков. Не делайте такие!
Для изготовления печи из дисков своими руками необходимо знать не только достоинства, но и недостатки исходного материала и некоторые, существенные в данном случае, особенности конструирования печей. Недостаток спецстали – она не нормируется на сварочные свойства. Технологий производства дисков для колес существует несколько, но сварка для этого если используется, то весьма ограниченно, с последующим термоотпуском (отжигом) и дефектоскопией шва. И, разумеется, никакой конструктор автотранспорта не закладывается на то, что к колесам в процессе эксплуатации будет что-то подвариваться.
Отсюда следует очень важный с точки зрения безопасности вывод: печь на отработке из дисков (см. рис.), равно как печи длительного горения и пиролизные из них, делать нельзя ни в коем случае! Разве только вы очень хотите, чтобы в один совсем не прекрасный момент через трещину в шве потекло кипящее, вероятнее всего, и горящее, масло или начали выделяться химически агрессивные высокотоксичные газы.
Примечание: сварочные швы для особых условий эксплуатации, не проконтролированные на качество должным образом, считаются ненадежными. Сварные сосуды, работающие под давлением, жаровые и для химически агрессивного содержимого, не прошедшие дефектоскопию и после нее испытаний в рабочем режиме использования, априори признаются негодными. Любая печь удовлетворяет как минимум двум из указанных условий.
Тем не менее, сделать вполне безопасную твердотопливную печь из автомобильных дисков на сварке для нежилых помещений (дачный дом тоже к ним относится) вполне возможно, если соблюдать след. правила:
Каечственно выполненный сварочный шов
- Сварной шов должен быть зрительно высококачественным, без видимых дефектов – трещин, брызг, раковин, пузырей, см. рис. справа;
- За один раз сваривать можно только по две сопряженные детали, варить сразу всю конструкцию ни в коем случае нельзя!
- После проводки каждого шва сваренным деталям нужно дать отдых для рассасывания остаточных внутренних напряжений, прим.
от 3 мин на каждый килограмм массы соединенных деталей. Практически – варить дальше не ранее, чем когда в 3-4 см от конца шва к металлу можно будет прикоснуться голой рукой;
- Готовая печь после суточной выдержки на рассасывание тех же напряжений подвергается испытательному прогону, от 3-х часов стационарная и от часа переносная уличная, на полной мощности, т.е. с полностью открытым воздушным дросселем (если он есть) или топочной/поддувальной дверцей, и максимальной загрузкой топлива.
В течение испытательного прогона одновременно происходит и отжиг печи. Обнаруженные мелкие дефекты сварки, не более 2-х на шов, устраняются спустя сутки, после чего прогон печи с отжигом повторяется.
Примечание: модуль коэффициента термического расширения ТКР стали для автодисков существенно меньше, чем у конструкционных сталей. Почему – понятно, но это обстоятельство тоже нужно иметь в виду, делая печь, см. далее.
Что нужно знать о печах
Делая печь из дисков автомобиля, нужно знать еще об одном обстоятельстве. По правилам строения пламенных печей на твердом топливе от пода топки или колосниковой решетки, т.е. оттуда, куда кладут топливо, до первого по вертикали препятствия току дымовых газов (напр. свода топки) должно быть не менее 40-50 см, если в печь загружается кондиционное топливо. Если сырое или бросовое, указанное расстояние нужно увеличить до 60-80 см; время прогрева печи тогда вырастет. Последнее для печей из дисков несущественно, т.к. прогреваются они быстро.
Причина – из твердого топлива выделяются горячие пиролизные газы, вносящие существенную, или даже определяющую, долю в тепловыделение. Если пиролизные газы соприкоснутся с менее нагретой поверхностью, они не смогут догореть и выпадет сажа. При дальнейшем пользовании такой печью произойдет ее закоксовывание – на своде топки и в дымоходе образуется плотный нагар. Он не только уменьшает тепловую эффективность печи (аналог КПД в печном деле), но и пожароопасен.
Примечание: высокую топку под сырое топливо делают, чтобы пиролизные газы и пары воды успели разделиться, а первые еще и догореть, прежде чем достигнут свода.
В таком случае топлива загружают не более чем на половину высоты топки.
Печи из дисков очень часто эксплуатируются именно на бросовом топливе (гнилой сушняк, сыроватые обрезки и т.п.), но в то же время негодных дисков на высокую печь может просто не хватить, или же оптимальная в данном случае схема печи (см. далее) не позволит сделать высокую топку. Тогда сделать печь из дисков можно, применив нестандартную колосниковую решетку из стального листа от 6 мм и арматурных прутьев от 10 мм. Опасаться, что воздуха на горение не хватит, не нужно: через отверстие диаметром 10 см, при дымоходе высотой 1,5 м, его пройдет достаточно для мощности 18 кВт на дровах и 30 кВт на угле. Печь из дисков такую никогда не разовьет.
Нестандартный колосник для печи из автодисков
Нестандартный колосник просто вкладывается в печь с зазором ок. 6-10 мм, из-за разности ТКР материалов, см. выше. Такое исполнение имеет еще одно преимущество – решается проблема зольника, для печей из дисков достаточно серьезная.
Примечание: горизонтальные печи из дисков (см. далее) с той же целью делают бесколосниковыми, т.е. топливо горит на поду печи, а приток воздуха регулируется дросселем в поддувале. Стойкость стали для дисков вполне позволяет применить такое решение.
Какую печь делать?
Исходя из вышеизложенного, возможности самостоятельного изготовления печи из автодисков можно разложить по полочкам таким образом:
- Когда желательно и нужно, т.к. использование именно автодисков позволяет улучшить качество печи и/или упростить ее изготовление.
- Когда можно для основных (жаровых) частей печного строения вместо дорогой жаропрочной стали.
- Когда возможно частично в качестве достаточно стойкого подручного материала.
- Когда нельзя ни в какую – рассмотрено выше.
Когда нужно
Лучшее использование автодисков для печи – в мобильных (переносных) уличных и садовых варочных печках и в качестве огнища для костра. В простейшей печи-очаге из дисков для дачи используется большая масса и высота борта (обода диска), что позволяет стабилизировать теплоотдачу и дает некоторую защиту от ветра. Как сделать простую дачно-садовую печку из автомобильного диска, см. видео:
Видео: садовая мини-печь из автомобильных дисков
Для казана
Однако наилучшее применение автодисков в садовых печах – под казан. Печь из дисков для казана совершенно круглая, а именно в углах кирпичной печи под казан варочная посуда греется слабее, и там оседает сажа. Дисковая печь обеспечивает абсолютно равномерный нагрев казана и экономию дров, что при использовании бросового топлива весьма существенно. Собранных на участке и в окрестностях веток и щепок может не хватить, чтобы плов или бешбармак поспел, как полагается. А сыроватое и подгнившее топливо в массивной кирпичной топке просто не разогреет варочную посудину в нужной степени.
Как неправильно и правильно сделать печь под казан из дисков
Дымовые газы идут по пути наименьшего сопротивления. Если просто сварить 2 диска и прорезать сбоку топочное отверстие, то горячие газы и без посуды пойдут через технологические (для облегчения конструкции) отверстия в ступице диска, поз. 1 на рис., т.к. их общая площадь больше, чем крепежных и осевого, и они ниже. Если печку раскочегарить на максимале, то, возможно, из осевого отверстия покажется язычок пламени, поз. 2, но с казаном на конфорке такой печи весь жар снова уйдет вбок без толку, поз. 3, или же, если попытаться часть техотверстий заглушить, или добавить топлива, пламя вырвется из загрузочной дверцы, поз. 4. На такой печке хорошо получается пища, приготовляемая томлением над углями, поз. 5, но не все же так готовят.
Правильная печка под казан из дисков должна быть, во-первых, снабжена плотно закрывающейся дверцей на загрузочном проеме. Во-вторых, казан должен сидеть в вырезе конфорки, частично перекрывая технологические отверстия в ступице, поз. 6. Добиться этого несложно: нужно вырезать болгаркой середину ступицы, как показано на поз. 7. Остаток не пропадет – из него получится отличный колосник. Как сделать садовую печь под казан из дисков автомобильных колес, см. также ролик
Видео: печь под казан из дисков
Вариант для барбекю
Не вырезать сердцевину ступицы диска нужно, кроме под томление на углях, в том случае, когда делается садовая печь-барбекю из дисков. Тогда на конфорку ставят решетку – рассекатель пламени, которая будет в то же время и кулинарной решеткой-рашпером. Преимущество данной конструкции в том, что на рашпере образуется несколько разных температурных зон, поз. 1 на рис. справа, что позволяет, напр., готовить одновременно ростбиф rare (полусырой с кровью), medium (сочный, в меру пропеченный, как шашлык), и well done (прожаренный до хрустящей корочки). Если на пикнике компания – все получат одновременно каждый по своему вкусу. Такую печь желательно делать из дисков с небольшим количеством широких технологических отверстий в ступице, напр. от «Газели». Решетку делают из велосипедных спиц. Варить их нет необходимости: они прекрасно соединяются жаростойким клеем по металлу (холодной сваркой).
Примечание: из дисков того же типа иногда делают печи без топочной дверцы (поз. 2 на рис. справа), подкладывая при топке не толстую щепу через техотверстия в ступице. Но печка получается прожорливой и плохо варящей. Почему – см. выше.
Когда можно полностью
Полностью из дисков хорошо получается отопительная печка-буржуйка. Плюсом в данном случае будут ее большие теплоемкость и время теплоотдачи – металл корпуса толстый – хотя, конечно, не такие, как у литой чугунной, и некоторое увеличение КПД. Минусом – более высокая трудоемкость изготовления усовершенствованных печей повышенной эффективности вследствие сложной конфигурации корпуса.
Отопительные печи-буржуйки из дисков
Если бросового топлива в достатке, то печь-буржуйка из дисков для отопления небольшого помещения может быть выполнена без внутренних перегородок-рассекателей (см. далее) горизонтальной, поз. 1 на рис. Такую печь весьма желательно делать из дисков грузового автомобиля: во-первых, больший объем печи увеличит ее КПД и время теплоотдачи. Во-вторых, вследствие сложной поверхности обода диска площадь выделяющей тепло наружной поверхности может быть в полтора-два раза больше, чем у простой круглой того же объема из бочки или трубы. Это же обстоятельство вместе с высокой коррозионной стойкостью дисков автомобильных колес позволяет снабдить печь рубашкой для водяного отопления, см. напр. след. сюжет:
Видео: печь-буржуйка из дисков с рубашкой
Горизонтальные буржуйки громоздки, поэтому чаще делают вертикальные.
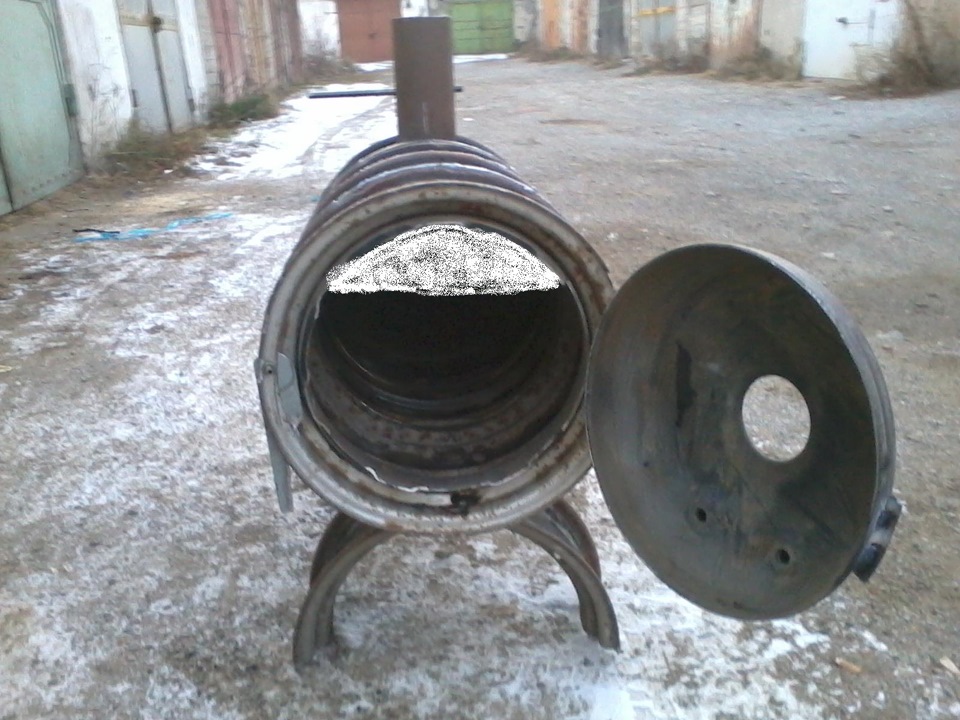
Что касается теплотехнических качеств, то улучшить их можно двумя способами. Первый – когда требуется быстрый прогрев помещения, а время теплоотдачи несущественно, напр., если печь ставится в гараж. Тогда ее верхнюю, жаровую, часть окружают кольцевым кожухом из тонкой стали (не оцикованной! Цинк плавится при 440 градусах, а его пары ядовиты!), с зазором 40-60 мм, поз. 2 на рис. Буржуйка таким образом превращается в печь-калорифер. Но, кстати, намного более эффективной будет горизонтальная печь-калорифер из дисков, см. далее.
Второй способ используется, когда нужно, наоборот, увеличить время теплоотдачи после топки, напр., в дачном домике, обитаемом с весны до осени. Для этого нужно облицевать печь любым доступным способом материалами, сочетающими в себе высокую теплоемкость и теплопроводность. Печной камень стеатит (талькохлорит) дорог, но шамотный кирпич (поз. 3) вполне его заменит. В крайнем случае можно на варочную поверхность наложить дикого камня потяжелее и поплотнее, поз. 4. Если печь из 4-х грузовых дисков, топливо полностью догорает и вьюшка закрывается к полуночи, то в спортивном костюме под армейским одеялом до 6-7 часов утра спится спокойно. Выспаться можно.
Усовершенствуем буржуйку из дисков
Повысить тепловую эффективность любой буржуйки возможно, устанавливая внутри перегородки-отсекатели. Таким образом образуется камера-дожигатель. В таком случае и воздушный кожух, преобразующий буржуйку в калорифер, также увеличивает КПД печи.
Схемы устройства печей-буржуек из дисков автомобильных колес
Схемы устройства буржуек из дисков даны на рис. Вертикальная простая (поз. 1) компактнее, несколько эффективнее горизонтальной (поз. 3) и дает варочную поверхность, но поставить в нее отсекатель камеры дожигания (поз. 2) сложнее, т.к. в данном случае он должен быть по всему контуру, прилегающему к корпусу печи, приварен к нему. Однако вертикальная буржуйка и с однооборотным дожигателем достигает КПД немного более 60%. Простая горизонтальная буржуйка (поз. 3) наихудшая по всем параметрам, но на ее основе делаются печи вполне эффективные. Ведущая величина для разработки модификаций – наименьший внутренний диаметр топливной камеры d.
Примечание: для сварки корпуса буржуйки из автодисков их ступицы вырезаются полностью, см. рис. справа.
Размерные соотношения для буржуек из дисков с одно- и 2-х оборотным дожигателем даны на поз. 4 и 5. КПД у обеих прим. 60%, но 2-оборотная сохраняет его на бросовом топливе, а однооборотной для обеспечения максимально возможной тепловой эффективности требуется качественное. Вырезать отсекатель (сталь от 4 мм) точно по внутреннему контуру корпуса печи не надо: в его заготовке нужно только выбрать лунки так, чтобы остался зазор между отсекателем и стенкой корпуса ок. 1,5 см. поз. 4а. Тогда дожигатель станет самонастраивающимся под ход (режим топки) печи и она будет держать КПД, близкий к максимальному, и на малом, и на полном ходу. Подобное решение используется в печах булерьян, но там для этого пробивают отверстия в отсекателе. В массовом производстве так выгоднее: отсекатель все равно вырубается за один ход пуансона пресса, а металоотходы охотно покупают металлурги как высококачественное сырье для мартеновских печей. Ну, а в домашних условиях проще оставить щель по краям отсекателя.
Горизонтальная буржуйка из дисков с дожигателем по эффективности вообще сравняется с булерьяном, если ее снабдить воздушным кожухом со щелевым соплом вверху и юбкой-воздухозаборником внизу, поз. 5а. Кожух должен прилегать снаружи к корпусу, а образовавшиеся каналы будут действовать точно так же, как в булерьяне или печах Инженер Бутаков, Огонь-Батарея и т.п.
Примечание: в дымоходах высокоэффективных буржуек из дисков (поз. 2 и 5) обязательно должен быть сборник конденсата со сливным краном, т.к. дымовые газы из них выходят чуть теплые.
На основе горизонтальной буржуйки из дисков можно сделать и полноценный отопительный котел, поз. 6. Если сварить его жаровой корпус из камазовских дисков, можно разогнаться до тепловой мощности ок. 40 кВт, а этого хватит для обогрева обычного жилого дома.
Отопительный котел из дисков автомобильных колес
Однако делать корпус теплообменника из дисков того же размера, поз. 1 на рис., нерационально: тогда придется ставить конструктивно сложный и требующий периодического ремонта огнетрубный теплоприемник, поз. 2. Корпус теплообменника лучше сварить из дисков меньшего размера, напр. от легкового автомобиля. Температура в нем тогда повысится до значений, позволяющих применить водотрубный теплоприемник. Из профилактических мероприятий он требует только ежегодного испытания под давлением в порядке опрессовки системы перед запуском и осмотра после него.
Водотрубный теплоприемник представляет собой частый цельный змеевик, по которому течет теплоноситель. Расстояние между ветвями равно наружному диаметру трубы; располагаются ветви в шахматном порядке. Сделать водотрубный теплоприемник для теплообменника домашнего котла из дисков можно из медной трубки с просветом от 20 мм и толщиной стенок от 2 мм. Ввод-вывод теплоприемника в теплообменник в таком случае герметизируются холодной сваркой.
Печь частично из дисков
Банная печь, построенная с использованием автодисков
В качестве составных частей автодиски широко используются в банных печах. Банная печь из дисков может быть построена и целиком, но только для сауны еле-еле среднего уровня. В русской бане пар от любой цельнометаллической печи жестковат.
Как выглядит печь в баню, построенная с использованием дисков автомобильных колес, показано на рис. права, а полная схема ее устройства дана на рис. ниже. Главное, что в данной печи обеспечивает надлежащее качество пара – кирпичная топка. Автодиски используются как вместилище содержимого закрытой каменки и для изготовления водогрейного бака.
Схема устройства и чертежи печи для бани, построенной с использованием дисков от автомобильных колес
Примечание: строить самодельную банную печь с открытой каменкой возможно только специальной конструкции целиком из кирпича, обеспечивающей полное, до углекислого газа и паров воды, дожигание отходящих от топки газов до того, как они подойдут к каменке.
Фирменные металлические банные печи с открытой каменкой делают для этого из специальных материалов по сложной технологии. Если попытаться повторить такую своими силами из обычных материалов, из каменки при каждой наддаче воды будет вылетать облако сажи.
Данную печь для бани повторило уже много любителей попариться в своей баньке. В общем все довольны; замечен только один стойкий дефект: нижний отсекатель (детали Подкос и Отражатель справа на рис.) спустя год-два корежится и отрывается от подкосов, или подкосы от корпуса. Причина очевидна: разные ТКР стали указанных деталей и корпуса из автодиска. Чтобы устранить дефект, нужно, видимо, отсекатель сделать тоже из диска меньшего размера, напр., легкового. Большую часть обода надо вырезать, оставив 4 ножки. Затем нагреть места перехода обода в ступицу и отогнуть ножки в размер.
Заваривать отверстия в ступице нет нужды. За счет теплопередачи на корпус отсекатель будет немного холоднее дымовых газов. Поскольку ступица выпуклая, под ней образуется газовая пробка наподобие газовой вьюшки в колпаковой печи, как в плохой садовой печке из дисков, см. выше, и дымовые газы все равно будут обтекать дно каменки, как показано стрелками на схеме.
Вариант комби
Негодные диски от колес у любителей десятками в гаражах не валяются, а изнашиваются, как правило, попарно, то ли передние, то ли задние. В таком случае, чтобы сделать из дисков достаточно эффективную печку с высокой топкой, пару дисков нужно будет дополнить куском стальной трубы подходящего диаметра со стенками от 6 мм.
Устройство печи из 2-х дисков от автомобильных колес показано на рис; ничем особенным от описанных выше она не отличается. Такая же печь может быть выполнена и горизонтальной. Об оформлении конфорки см. выше.
Устройство печи из 2-х автодисков и отрезка трубы
Загрузка…Обсуждение темы «Печь из автомобильных дисков»
Ниже Вы можете поделиться своими мыслями и результатами с нашими читателями и постоянными посетителями.
Также можно задать вопросы автору*, он постарается на них ответить.
схема и инструкция по изготовлению
Печь под казан из дисков – это самый простой способ изготовления приспособления для готовки не только кушаний восточной кухни. На такой печи готовят блюда любой кухнимира на открытом огне. Простота конструкции позволяет выполнить работу самостоятельно при начальных навыках электросварки.
При подборе дисков для будущей печки важно учитывать размер казана. Для большой посуды может подойти колесный диск от грузовика диаметром 500 мм и высотой 250 мм. Для небольшой печи можно использовать штампованные детали от легковых авто.
Особенности конструкции
Отличительная особенность такой конструкции – это простота и возможность сделать отличный очаг без затрат на покупку дорогостоящего материала. Нет надобности закупать листы стали, размечать и отрезать болгаркой детали. Затем стыковать, прихватывать и выполнять другие слесарные работы.
Печь состоит из нескольких колесных дисков сваренных вместе. Если казан небольшой, можно его устанавливать на лицевую сторону диска. Для этого детали выкладываются навстречу тыльными сторонами. Для установки средней посуды вырезается место с крепежными отверстиями для колеса.
Большой таганок можно устанавливать с тыльной стороны диска. В этом случае лицевая сторона полностью вырезается, затем детали соединяются между собой. Диск с вырезанной частью стыкуют с тыльной стороной 2-й детали. В такой конструкции сохраняется достаточное место для закладки дров в топку.
Пример конструкции печи под казан из автомобильных дисков
Такая конструкция обладает рядом достоинств:
- толстый металл дисков продляет жизнь самоделки. Стенки не сгорают при сильном нагреве и не деформируются под действием высокой температуры;
- для изготовления используется бросовый материал, поэтому для производства печи потребуется подготовить всего несколько электродов и дисков на болгарку. Весь остальной материал найдется у каждого домашнего мастера;
- при установке без ножек – конструкция устойчива;
- печка будет исправно служить даже при частых использованиях;
- можно установить дополнительный диск и увеличить объем топки без дополнительных затрат;
- на печи можно устанавливать все виды посуды подходящие по размеру;
- у такого устройства высокий уровень теплоотдачи, поэтому ее можно использовать для отопления помещения гаражей или подсобок на участке.
Для того чтобы сделать печь из дисков автомобиля для казана, важно разобраться с местом установки печи, размещением казана и только потом приступать к подготовительным работам.
к содержанию ↑Материалы
Наша печка под казан из автомобильных дисков будет состоять из 3-х дисков с размещением большого размера посуды на тыльной стороне диска. Для отведения дыма предусматриваем установку трубы. Такая конструкция вызовет небольшие потери тепла, но поможет повару не задыхаться от дыма во время готовки. Казан будет погружаться в печь на 2/3 высоты, поэтому потребуется сделать печь из 3-х секций.
Для работы необходимо:
Наименование | Количество |
Колесные диски | 3 шт |
Для ручки на дверцу | Пруток, диаметром 8-10 мм, длиной 200 мм |
Ручки для переноски печи | 2 детали из прутка длиной 250 мм |
Для петли и защелки | Пруток: 2 детали по 100 мм. Профиль 20 мм – 4 детали по 50 мм |
Труба стальная для дымохода | Отвод из трубы диаметром 50 мм. Отрезок трубы с козырьком, длиной 1,5-2 м. |
Подойдут такие диски
Если печь необходимо приподнять для удобства приготовления пищи, можно приготовить 4-е ножки из уголка или профильной трубы одинакового размера.
к содержанию ↑Инструменты
Для того чтобы сделать печь для казана из автомобильных дисков, понадобится приготовить набор инструментов и оборудования:
- сварочный аппарат;
- электроды для сварки конструкционных сталей;
- сварочная одежда, маска и перчатки;
- болгарка;
- несколько отрезных и зачистных дисков;
- молоток, напильник, плоскогубцы;
- небольшие настольные тиски.
Пошаговая инструкция по изготовлению
Как сделать печь для казана из колесных дисков своими руками, решить эту проблему поможет знание основных этапов изготовления данной конструкции:
- Сначала необходимо подготовить диски к сварке. Для этого на верхней детали полностью вырезается лицевая сторона. Это делается для свободного прохода и равномерного распределения тепла в зоне приготовления пищи. Аналогичную работу выполняем со средней частью будущей печи. Нижний диск оставляем без изменений. Для устранения путаницы, на деталях мелом пишем место установки деталей.
Вырезаем лицевую часть
- Нижнюю деталь выкладываем на ровной поверхности лицевой частью вниз. На нее размещаем среднюю деталь внутренней частью диска вниз. Проверив его положение, делаем 4-е прихватки через 900.
- Размещаем на сборном узле 3-ю деталь лицевой стороной вниз, проверяем правильную установку детали и прихватываем в 4-х местах.
Сборка
- Еще раз, проверив сборку и расположение отдельных частей в вертикальной плоскости, можно приступить к обварке конструкции. Здесь важно отметить – не выполняйте обварку одного шва полностью. Для предохранения от деформаций детали лучше варить пошаговым способом. Проварив небольшой участок на 1-м стыке, поверните конструкцию на 900 и проварите участок шва с этой стороны. Затем перейдите на сварку 2-го шва. Так чередуя стороны и швы, проварите все стыки.
- Отбиваем шлак и проверяем качество шва. При обнаружении непроваров, подрезов или дырок обязательно добавляем на эти места расплавленный металл.
- На болгарку ставим зачистной круг и зачищаем швы и места резов лицевых частей.
- Теперь важно сделать хорошую дверку для закладки дров. Отступив от низа печи 200 мм, размечаем окно для топки; высота –180 мм; ширина – 200 мм.
- Вырезаем болгаркой с отрезным кругом по линиям разметки окошко. Отрезанную деталь мы будем использовать для изготовления дверцы. Для этого по 3-м сторонам прихватываем проволоку сечением 6-8 мм по наружной стороне заготовки. С петельной стороны посередине окна, привариваем деталь из профильной трубки. Во вторую трубку вставляем пруток для петли и прихватываем его с одной стороны.
Вырезаем дверцу
- Устанавливаем дверь на место, ставим ответную часть петельки и привариваем трубку к диску. К дверце прихватываем готовую загнутую П-образную ручку и ставим самодельный шпингалет из прутка и профиля.
Пример дверцы (их можно делать по-разному)
Получившаяся конструкция
- Если требуется, размечаем и привариваем 3-4 ножки под небольшим углом. Для лучшего провара концы заготовок необходимо зарезать под угол, чтобы ножки прилегали к печи плоскостью.
“Ноги” для печки
- На противоположной стороне от дверцы, вверху средней детали размечаем место установки дымохода. Электросваркой аккуратно вырезаем отверстие по размеру трубы, вставляем отвод так, чтобы свободный конец смотрел вверх. Труба должна выставляться заподлицо с металлом колесного диска. Делаем 3-и прихватки, убедившись в правильном положении детали, обвариваем стык по кругу.
- На дымоход наматываем несколько витков асбестового шнура и вставляем в отвод. Труба должна садиться плотно, а шнур будет препятствовать выходу дыма на месте соединения.
Почти готовая конструкции, осталось лишь приделать ручки и зачистить детали.
- Все детали зачищаются болгаркой, заусеницы от резов лучше сбить напильником.
- Из прутка делаем ручки для переноски печи. Для этого на заготовках с обеих сторон размечаем расстояние 50 мм и загибаем под угол 900, зажав заготовку в тисках с выступающим вверх коротким отрезком. Загибаем молотком. Затем вверху конструкции, на противоположных боках, делаем разметку мест крепления ручек, выставляем и привариваем их.
Наша печь из колесных автомобильных дисков готова.
Дополнительно можете посмотреть видео:
Другие примеры разных самодельных конструкций печки под заказ из дисков на фото:
Фото 1
Фото 2
Фото 3
Фото 4
Фото 5
к содержанию ↑Как правильно пользоваться?
Нашу конструкцию устанавливаем в лоток. Готовить на печи сразу не рекомендуется. Диски, как правило, окрашены и на них остается масло и тормозная жидкость. Поэтому чтобы плов не «благоухал» запахами сгоревшей химии, печь сначала прокаливают. Для этого через верх, топка полностью заполняется дровами. Использую жидкость для розжига, зажигаем пламя и даем дровам полностью сгореть.
Теперь дав печи остыть, высыпаем золу и остатки дров. Наждачкой и щеткой по металлу очищаем стенки печи, удаляя остатки краски и нагара. Выполнив эти работы можно приступать к приготовлению плова и других вкусных блюд с запахом сгоревших дров.
Теперь дрова закладываются в топку через дверку. Уложив немного древесной коры и щепы, зажигаем пламя. Снизу поступает кислород через отверстия в диске, обеспечивая пламя питанием воздуха, а сверху отработанные газы и дым выводятся в дымоход. Такая конструкция создает достаточную тягу и хорошие условия для горения.
Процесс готовки в самодельном казане
При приготовлении блюд важно не подкладывать много дров, поддерживая постоянную температуру нагрева в печке. Для этого не старайтесь закладывать сразу большое количество дров. Сильное пламя приведет к сгоревшей пище и расстройству повара. Все придет с опытом, не бойтесь экспериментировать, но лучше затратить немного больше время, постепенно подкладывая дрова в топку, чем получить сгоревшее мясо или плов.
После приготовления пищи не следует сразу начинать обслуживание и уборку. Необходимо дать металлу остыть, а уж потом начинать вычищать золу и не сгоревшие остатки дров, ссыпая их в поддон через отверстия в нижнем диске. Для удаления крупных огарков потребуется перевернуть печь и вытрусить отходы в поддон. Золу применяют для подкормки садовых растений и цветов.
Для удобства передвижения по участку, печь можно установить на колеса. Все зависит от фантазии и навыков мастера. Такую конструкцию можно использовать для жарки мяса на сковороде и приготовления первых блюд. Но шедевром был и остается восточный рассыпчатый плов, который для вас приготовит печка для казана из дисков, сделанная своими руками.
преимущества, материалы и оборудование, процесс монтажа
На чтение 5 мин Просмотров 196 Опубликовано Обновлено
Покупка портативной (переносной) печи для бани или дачи требует немалых финансовых вложений. Вместе с тем, задача таких отопительных приборов не настолько велика, чтобы тратить деньги на изделие заводского производства. Намного проще и дешевле изготовить самостоятельно печь из дисков. Старые автомобильные диски можно по приемлемой цене приобрести в приемках металла. Для проведения работ приветствуются навыки в работе со сварочным аппаратом и болгаркой.
Чем хороша печь из автомобильных дисков
Основные преимущества конструкции — низкая стоимость и прочностьПечка из автомобильных дисков выгодна тем, что все необходимые материалы легко найти и стоят они недорого. Дополнительное преимущество в том, что автомобильные диски производят из стальных сплавов большой толщины, они не подвержены воздействию коррозии и деформации под воздействием высоких температур.
Печка из колесных дисков способна функционировать на любом твердом топливе, даже угле. Толстый металл эффективно аккумулирует тепло, несмотря на то, что по инертности сталь уступает чугуну.
Дискам автомобилей свойственна особая конструкция – торцевая часть с отверстиями. Это можно выгодно использовать для организации конфорки с колосниковой решеткой.
Основные преимущества печей из дисков:
- универсальность использования по топливу;
- невысокая стоимость материалов изготовления;
- простота изготовления и монтажа;
- высокая надежность и прочность;
- продолжительный эксплуатационный срок;
- выгодная конфигурация единичного элемента.
Прежде чем приступать к изготовлению, важно ознакомиться с этапами производства и подготовкой рабочего инвентаря.
Материалы и инструменты для монтажа
Печь диаметром 0,5 м из дисков КАМАЗаЧтобы сделать печь для бани из дисков, нужно подготовить следующий набор инструментов:
- 4-6 стальных швеллера;
- газовый резак или болгарка с кругами по металлу;
- электроды и сварочный аппарат;
- защитные приспособления: краги, очки;
- дверные подвесы;
- железный лист толщиной 8 мм;
- 2 отреза диаметром 160 мм, толщиной 5 мм, длина трубы 50 см.
Чтобы возвести корпус, потребуется 4 диска, предназначенных для грузовой машины, например, КАМАЗа. Диаметр такой печки будет равен 0,5 м с толщиной стенок 1 см.
Правила пожарной безопасности при обустройстве печи из колесных дисков
В помещении печь из дисков для безопасности окружают огнеупорным кирпичомЕсли человек принял решение самостоятельно изготовить печку, он должен ознакомиться со сводом правил по пожарной безопасности. В будущем это позволит предупредить несчастные случаи.
Печка из дисков при работе обогревает инфракрасным теплом. Поэтому нужно позаботиться об экранировании, иначе инфракрасные потоки не будут преобразовываться в тепло, эффективность от такого обогрева будет мала. Для этого корпус окружают обшивкой из стали, которую монтируют таким образом, чтобы тело печи находилось на расстоянии от пола и обшивки в 10 см.
При эксплуатации отопительного самодельного оборудования важно соблюдать следующие правила безопасности:
- На пол нужно уложить стальной лист или железобетонную плиту. Делается это таким образом, чтобы покрытие было больше, чем диаметр конструкции. Благодаря этой несложной процедуре удастся предупредить попадание угольков на пол, что может стать причиной возгорания.
- Дымоходная труба и металлическая печь не должны контактировать с легковоспламеняющимися материалами. Для безопасности дополнительно рекомендуется использовать изоляционные прокладки.
- Настоятельно не рекомендуется при растопке использовать жидкие разжигатели, поскольку это может стать причиной выброса огня из отверстия топки.
- На этапе изготовления отопительного оборудования важно позаботиться о том, чтобы топочная часть конструкции выходила к предбаннику.
Следующее правило не является обязательным, но оно обеспечивает дополнительную безопасность при использовании печи: организация древесных подвесов.
Этапы монтажа печи из дисков своими руками
Уличный вариант проще сделать из-за отсутствия дымоходаС помощью болгарки нужно вырезать сердцевину у автомобильных дисков. На самом верхнем ее можно оставить.
Следующий этап – сварка элементов печи. Для проведения сварочных работ понадобятся электроды 5 мм.
Нижний диск надежно приваривают к железному листу, размеры которого должны превышать размеры диска. Если печь будет использоваться только на улице, потребность в этом условии отпадает.
Если конструкция будет предназначена для обогрева помещений, на верхнем диске в одно из имеющихся отверстий вставляется труба, остальное пространство герметично заделывается листом железа. Далее все диски нужно сварить между собой таким образом, чтобы между ними не было зазоров и щелей, иначе огонь и дым могут проникнуть в помещение.
Дальше приступают к изготовлению отверстия под топку, но делать это нужно на таком расстоянии, чтобы осталось место для поддувала. Преимущественно его делают во втором снизу диске, а для зольника в первом. Отпиленный кусок металла не нужно выбрасывать, он понадобится для двери.
Аналогичным образом делается отверстие для поддувала. Для хорошей тяги достаточно соблюдать размеры приблизительно 30 на 15 см.
Для колосника нужно подыскать подходящую по размерам решетку. Если такой найти не удалось, можно воспользоваться листом металла, в котором предварительно будут проделаны отверстия.
В завершение обязательно устанавливают дверцу. Для этого сначала приваривают петли, на которых она будет держаться. Далее к петлям приваривается непосредственно дверь. Чтобы ее удобно было открывать, рекомендуется оснастить дверцу ручкой. Использовать в этих целях можно любую фигурную ручку, болт или сверло по металлу.
Самодельные печи – это эффективный аналог отопительного оборудования производственного изготовления. Однако при неправильном монтаже или эксплуатации прибор может быть небезопасным.
2 способа изготовления своими руками
Любители отдыха на природе знают, что самые вкусные блюда – те, что приготовлены на открытом огне. И если нет желания тратить средства на приобретение дорогостоящих мангалов или барбекю, можно построить печь для казана из дисков, которые наверняка найдутся в гараже любого владельца авто. А еще такую печку можно использовать не только для кулинарных изысков, а и для обогрева гаража или бани.
Особенности устройства дисковых печей
Печка под казан из автомобильных дисков, ничем не уступает готовым покупным приспособлениям для готовки на открытом огне. У нее есть топка с дверцей, куда подкидываются дрова. А выемка имеет правильную форму и гладкие края, где свободно помещается котелок, решетка гриля, сковорода или несколько коротких шампуров.
Печка из колесных дисков на даче
Кроме того, печь для казана из колесных дисков обладает рядом преимуществ перед другими самодельными мангалами. В отличие от железных бочек, которые тоже используются для приготовления блюд на костре, диски намного дольше служат и не прогорают. А их конструкция обойдется намного дешевле, чем печь из толстого стального листа.
Плюсы дисковой печки:
- Быстрый и равномерный нагрев.
- Устойчивость к высоким температурам.
- Хорошая теплоотдача.
- Долговечность.
- Низкая себестоимость – практически все материалы можно найти бесплатно.
- Простота изготовления.
- Возможность подобрать самому оптимальный размер для конструкции.
Обратите внимание! Диаметр печки должен быть таким, чтобы 2/3 казана оказались внутри нее, при меньшем погружении сложно добиться равномерного прогрева всего котла, а при большем – посуду будет неудобно снимать с огня.
Инструменты и материалы для работы
Чтобы изготовить печь для казана из дисков своими руками, понадобится обычный набор из арсенала домашнего мастера с рулеткой, наждачной бумагой и гаечными ключами, а также:
- 1 метр прямоугольной трубы;
- 3 крупных болта и гайки;
- отрез проволоки 8 мм в диаметре;
- 4 гайки на 10;
- болгарка с насадками для работы по металлу;
- сварочный аппарат, электроды и средства защиты (маска, краги, фартук).
Что касается самих дисков, для печки под казан потребуется всего два. Радиус зависит от размера посуды, в которой вы будете готовить. Для небольшого котелка достаточно двух дисков от легковых авто стандартного 13-го или 14-го радиуса. А вот для объемного котла, рассчитанного на большую компанию, можно подыскать и колеса от грузовых машин.
Колесные диски
Совет! Лучше всего брать штампованные стальные диски, а вот литые прослужат недолго – их изготавливают из алюминиевых сплавов, неустойчивых к высоким температурам.
Способы изготовления печки из колесных дисков
Самый сложный инструмент для предстоящих работ — сварочный аппарат. Во-первых, он есть в арсенале далеко не у каждого домашнего умельца. А во-вторых, работа с ним требует особых навыков и соблюдения мер безопасности. Поэтому мы предлагаем два варианта изготовления печки из дисков для казана – с использованием сварочного аппарата и без него.
В любом случае начинать следует с обработки самих дисков. Бывшие в употреблении колеса и выглядят соответствующе: металл может потемнеть, иметь остатки облупившейся краски или пятнышки коррозии. Чтобы избавиться от этих нюансов, следует зачистить проблемные места шлиф шкуркой. Если диски были окрашены, можно прокалить их огнем или воспользоваться растворителем.
Сварочный метод
Работы выполняются поэтапно в следующем порядке:
- Варочная поверхность
Сначала изготавливается верхняя часть печки. Для этого один из дисков устанавливается так, чтобы сторона с крепежами была сверху. С помощью болгарки вырезается ровный круг (ориентирами послужат болтовые отверстия). Это будет варочная поверхность и одновременно подставка, удерживающая казан в печи. Окружность отшлифуйте с помощью крупнозернистой бумаги или той же болгарки.
Вырезаем круг для варочной поверхности
Важно! Не повредите при работе с болгаркой сам диск. От края обода до выреза под «варочную поверхность» должно оставаться не менее 2 см металла. Этот зазор необходим для легкой установки казана и равномерного окутывания его стен жаром пламени.
- Сварка корпуса
Теперь берем второй диск, переворачиваем его крепежной стороной вниз – это будет дно печи. На него устанавливаем подготовленную верхнюю часть так, чтобы поверхность с вырезанным кругом оказалась сверху. Место соединения двух дисков нужно проварить вкруговую, затем зачистить шов болгаркой. Каркас печи готов!
Собираем корпус
В нижней части каркаса прорезается отверстие для топки, через которую будут подкидываться дрова. Рекомендуемая высота для дверцы – 10-13 см, длина – 20-25 см.
Важно! Внизу должна остаться полоска металла достаточной высоты, чтобы удержать угли внутри печи (не менее 2 см).
У прорези и отреза края также нужно зашлифовать. Затем к отверстию приваривается 2 крупных болта, а на вырезанную часть диска – гайки в соответствующих местах (вместо ручки используется третий из больших болтов). После сварочных работ готовая дверца устанавливается в эту импровизированную петлю.
Привариваем дверцу на болты
Для удобства можно немного модернизировать конструкцию, оборудовав корпус держателями. Для этого нужно изогнуть проволоку в форме ручек, продеть ее на концы гайки и приварить их по обе стороны печи.
На заметку! Чтобы ручки не провисали и не прилегали к корпусу, сделайте для них упор, протянув пару сантиметров проволоки через гайку и согнув эти «лишние» края под прямым углом.
Ручки для корпуса печи, приваренные на гайки
Прямоугольную трубу разрезаем на 3 равные части длиной 25-30 см. После этого переворачиваем корпус дном вверх и привариваем ножки под небольшим углом — это необходимо для устойчивости конструкции.
Совет! Чтобы из днища не сыпались мелкие угольки, приварите к центральному отверстию в ступице небольшую металлическую заплатку.
Тренога для печки
Декорировать печь из автомобильных дисков можно с помощью термостойкой эмали. Так как печь будет постоянно контактировать с сажей, оптимальные цвета для окрашивания – черный, темно-синий и темно-коричневый. Другие оттенки быстро потеряют свою первоначальную яркость, придется чаще и тщательнее очищать стенки от гари.
Подгонка дисков по размеру
А теперь рассмотрим вариант изготовления печи из дисков под казан без помощи сварочного аппарата. Все подготовительные работы и прорезы здесь также обязательны, основное различие только в том, что части корпуса между собой не свариваются, а подгоняются по размеру.
Для этого один обод нужно немного разогнуть, а второй – согнуть (судя по отзывам домашних умельцев, диски, несмотря на прочную сталь, отлично поддаются обработке с помощью обычного молотка). Главное – обеспечить максимально плотное прилегание двух поверхностей, иначе большие зазоры могут сказываться на качестве тяги и расходе топлива.
Отсутствие сварочного аппарата изменяет и другие конструктивные детали:
- Дверцу в топке не приваривают, а просто оставляют небольшое отверстие, вырезанное с помощью болгарки. Еще проще вариант – не делать дверцу вообще, а дрова подкидывать через верх, периодически снимая казан с огня.
- Ручки, которые также прикрепить будет нечем, заменяют обычными кухонными прихватками.
- Вместо ножек из трубы можно установить печку на готовую треногу или подставить несколько кирпичей.
Печка под казан без сварки
Несмотря на простоту исполнения, такая конструкция обладает рядом преимуществ перед сварной моделью: ее удобнее чистить от золы, она быстро разбирается и компактно складывается по принципу матрешки, не занимая много места в гараже или багажнике авто. И самое главное – изготовить ее можно максимум за полчаса работы!
Впрочем, выбирать тип конструкции и способ ее изготовления предстоит вам. Если простой вариант с подгонкой дисков не устраивает, а сварочного аппарата в доме нет, всегда можно нанять мастера, который за пару минут выполнит все сварочные работы в лучшем виде.
Видеоурок: печь для казана из старых автомобильных дисков
расскажем как сделать своими руками печь размером почти с подставку
Поклонникам среднеазиатских блюд, готовящихся в казане, просто необходима печь под казан. Такие кирпичные печи не дешевы. Можно сделать печку под казан самому, например, из старых автомобильных дисков.
Потребуются стальные штампованные диски. Литые легкосплавные – не подойдут.
Делаем своими руками
То, что можно сделать полезную печь из тех самых дисков что валялись без дела – неоспоримый плюс.
В конце, вы получите компактную печь под казан (почти подставку) оригинального вида, но полностью функциональную.
Если вы никогда не держали в руках сварочный аппарат, сооружение подобной печки будет испытанием.
Последовательность
Нам обязательно понадобятся два 13-дюймовых штампованных колесных дисков. Можно на 15 дюймов, но больше 15 и меньше 13 дюймов – не стоит.
- Берем первый диск. По отверстиям как на фото вырезаем внутренности. Режем болгаркой, если есть — плазмой.
- Берем второй диск и завариваем центральное большое отверстие. Потребуется небольшой кусок не толстого листа (2 — 4 мм).
- Соединяем оба диска. Должно получится «ведро». Шов делайте сплошной. Если внешний вид печки для вас важен – обработайте шов болгаркой, сняв некрасивые наплывы сварки.
- Печка пока выходит неудобно низкая (да и устойчивость с учетом полного казана – так себе). Нам потребуются ножки.
Удобно сделать ножки съемными. Поэтому мы взяли три отрезка профильной трубы, куда потом будут вставляться ноги (мы заранее проверили, что ноги вставляются хорошо).
Эти части привариваются к нижней стороне (с дном) печи, как на фото.
Особая точность не требуется, но прикиньте как будут получаться ноги «в сборе».
- Из профильной трубы меньшего размера делаем ножки. Если ножки не вставляются по месту, подточите болгаркой.
- Для печи нужна дверка. Как на фото размечаем дверку и аккуратно вырезаем по разметке. Чем аккуратнее, тем опрятнее выйдет печка.
- Чтобы печная дверца открывалась, нужны петли. Простейшие петли можно сделать из болтов и гаек. Ручку тоже из гайки, приварив её к дверке.
- Конструкция получается неухватистая. Чтобы удобнее было переставлять, можно приварить ручки. Но эта деталь необязательная.
- Для выхода дыма сделаем треугольные надрезы в верхней кромке печки.
- Удалите старую краску. Можно обжечь и очистить щетками или с помощью пескоструя.
- Покрасим печку. Мы выбрали черный цвет. В тон копоти.
Как видите, сделать такую печь из дисков под казан можно самому. Уверены, у вас получится.
Полезное видео:
К сожалению, мы не снимали видео. Но мы нашли ролик про похожую печку:
Наша же печь гараж не покинет. Поучаствует в воскресных посиделках.
Поделиться в социальных сетях
Как правильно собрать печь из дисков автомобиля своими руками?
Делаем печь из колесных дисков: пошаговая инструкция
Приобретение переносной печи для дачи или банной печки – мероприятие, требующее наличия серьезной суммы. Задача садовой печи не настолько велика, чтобы тратить деньги на изделие заводского производства. Гораздо проще и дешевле изготовить печь из дисков. Негодные автомобильные диски владельцы часто выбрасывают, их можно недорого купить в приемках металла. Для сооружения печи из колесных дисков своими руками потребуются навыки работы с болгаркой и сварочным аппаратом.
Чем хороша печь из колесных дисков
Печь из колесных дисков выгодна тем, что материал для ее изготовления легко найти. Диски автомобиля выполняются из специальных сталей большой толщины, мало подверженных коррозии. Толщина металла имеет важную роль в работе любой печи. Повышенная толщина материала не дает деформироваться конструкции под воздействием высоких температур. Печь из автомобильных дисков работает на любом твердом топливе, даже на угле, имеющем очень высокую температуру сгорания. Толстый металл лучше аккумулирует тепло, хотя и уступает по инертности чугуну, остывает несколько быстрее.
Диски имеют особую конструкцию – торцевую часть с отверстиями. Этот конструктивный элемент пригоден для организации комфорки, снижает скорость уноса тепла, применяется для изготовления самодельной колосниковой решетки. Внешний обод диска выполнен с нелинейной поверхностью – это способствует увеличению площади теплоотдачи, оптимизирует движение дымовых газов при использовании для сооружения дымового канала. В отличие от чугунных печей стальная печь из дисков обладает высочайшей ударной прочностью, не боится попадания воды на раскаленные поверхности.
Главные критерии, говорящие о преимуществах печи из дисков, выполненной своими руками:
- Доступность материала изготовления;
- Высокая прочность, надежность;
- Выгодная конфигурация единичного элемента – автомобильного диска;
- Продолжительный срок службы;
- Простота изготовления;
- Универсальность по топливу.
Перечень материалов и оборудования для монтажа
Для изготовления печи из дисков потребуются, прежде всего, сами автомобильные диски. Лучше всего использовать диски от легковых автомобилей и малотоннажных грузовиков. Печи из дисков крупных грузовых автомобилей большой грузоподъемности получатся излишне громоздкими и тяжелыми, трудно добиться герметичности их соединений. Для самостоятельного монтажа и сборки понадобятся следующие материалы:
- Стальная арматура большого диаметра;
- Металлический уголок;
- Материал для изготовления решетки;
- Лист металла для монтажа дверки;
- Небольшие куски металла для упоров;
- Труба с толщиной стенки не менее 5 мм и диаметром от 100 мм;
- Стальная труба с толщиной стенки от 2,5 мм диаметром 80 – 100 мм.
Стальная арматура применяется для изготовления ножек садовой печи, ножки монтируют также из стального уголка. Металлический уголок используют как основание для укладки шампуров, его чаще выполняют съемным. Для укладки шампуров можно положить уголки на верхний раструб диска перпендикулярно шампурам. Стальная решетка служит для приготовления барбекю, гриля, служит основой для установки котла или казана. Решетку изготавливают из стальной арматуры.
Печи из дисков выполняют чаще с дверцей. Для этого потребуется лист металла, дверные петли или импровизированная петля из гаек и болтов разного диаметра. Наличие дверцы повышает безопасность печи, улучшает процесс горения.
Упоры, выполняемые по периметру, служат основанием для установки казана, прочно фиксируют съемную решетку. Толстостенная труба диаметром более 100 мм пригодится для изготовления печи для бани из дисков. Труба диметром от 80 мм и толщиной стенки потребуется для монтажа дымохода для садовой печи.
Для изготовления агрегата своими руками понадобятся следующие инструменты:
- Сварочный аппарат;
- Маска сварщика, электроды;
- При наличии – баллоны с газовым резаком;
- УШМ (болгарка) с отрезными и зачистными дисками;
- Кувалда;
- Молоток;
- Измерительный и разметочный инструмент – мел, карандаш, маркер и рулетка.
Газорезку удобнее использовать для резки металла – диски имеют выпуклые закругленные поверхности, их обработка болгаркой будет проходить с некоторыми трудностями. Прорезанное газовой горелкой окно проще обработать от нагара болгаркой с зачистным кругом. Кувалда пригодится для выправки сильно погнутых автомобильных дисков.
Правила пожарной безопасности при обустройстве самодельных печей
Соблюдение правил пожарной безопасности – важнейший аспект при эксплуатации и изготовлении самодельных печей. Это в равной степени относится и к печам заводского изготовления.
Поверхности печей имеют очень высокую температуру – это может вызвать возгорание легковоспламеняемых веществ. Что касается печей из дисков – они не имеют зольника, зола с частицами горячих углей может просыпаться через колосниковую решетку. Для их сбора необходимо установить емкость соответствующего диаметра, исключающего унос горячих частиц.
Немаловажный фактор – наличие дверцы топки. Закрытая дверца замедляет скорость сгорания топливной загрузки, предотвращает вылет горячих частиц, искр.
При строительстве банной печи из дисков или печи для сауны сгораемые строительные конструкции должны располагаться на безопасном расстоянии от раскаленных поверхностей, экранироваться слоем несгораемого материала. Несгораемый материал должен иметь низкий коэффициент теплопроводности. Расположение печи в саду, на даче не рекомендуется вблизи сгораемых конструкций и материалов.
Как сделать печь из дисков для бани своими руками
Диски из металла на банных печах служат надстроенным комплексом на каменной печи. Они выполняют следующие задачи:
- Служат поверхностью теплоотдачи в помещение бани;
- Являются основанием для сооружения каменки;
- Служат стволом дымохода;
- На их основе часто сооружается контур нагрева воды – устанавливается бак.
Монтаж самой печи из металлических дисков нецелесообразен. Возможно возникновение утечек дыма в негерметичности сварочных швов, металл обладает низкой инертностью и быстро остывает.
Процесс монтажа надстройки состоит из следующих этапов:
- На готовую каменную печь устанавливается первый диск. Диск устанавливается свободной стороной вниз. Стыки с поверхностью печи герметизируются.
- На лицевую сторону первого диска лицевой стороной устанавливается второй диск, они свариваются между собой.
- В центре сложенных вместе лицевых сторон вырезается отверстие, соответствующее диаметру подобранной трубы для дымохода. На вырезанное отверстие устанавливается труба, герметично приваривается.
- Во внутренне пространство второго диска вокруг трубы укладывается каменная подборка – она послужит каменкой. Камни обладают очень высокой инертностью, долго сохраняют тепло. Они принимают тепло от разогретых металлических дисков, разогреваются и при обливании водой производят пар.
- По периметру второго диска приваривают 4 стойки одинаковой длины.
- На стойки лицевой частью вниз устанавливают третий автомобильный диск, через него пропускают дымовую трубу.
- Третий диск приваривается к трубе дымохода.
- Поверх диска часто устанавливают самодельные баки с отверстием в центральной части для прохождения дымовой трубы. В баках производится нагрев воды.
- Место прохода горячей части трубы дымохода через строительные конструкции герметизируется несгораемыми материалами.
- В верхней части дымохода сооружается заслонка или шибер для регулирования силы тяги.
Иногда печи для бань с применением автомобильных дисков строят по упрощенной схеме. На поверхность топки устанавливают плиту, на нее ставят открытый бак для нагрева воды. Далее, за плитой, на дымовой канал вместо верхней стенки укладываются швеллера. Стыки швеллеров герметизируются глиной. Поверх швеллеров укладывается каменка.
После каменки сооружается вертикальный комплекс из сваренных между собой дисков. Комплекс служит каналом дымохода, работает как отопительный прибор, отдавая тепло в помещение. Подобная конструкция намного надежней и герметичней, не требуется сооружение бака для воды замысловатой формы с проходным пространством.
Садовая мини печь из автомобильных дисков
Владельцы земельных участков частных домов и дачники часто сооружают для приготовления блюд на открытом воздухе различные мангалы, жаровни и так далее. Отличным решением этой задачи послужит изготовление садовой печи из автомобильных дисков.
Изделие можно выполнить в универсальной конфигурации. На печи можно жарить шашлык, готовить плов в казане, приготовить различные продукты на решетке.
Монтаж садовой печи довольно прост. Потребуется два автомобильных диска. В одном диске вырезается центральная часть лицевой стороны. Диск устанавливается отверстием вниз. По периметру диска приваривают ножки из стальной арматуры большого диаметра или уголка. На вырезанное отверстие устанавливается самодельная колосниковая решетка.
Во втором диске лицевая сторона вырезается почти полностью, он приваривается к первому диску. Во втором диске (в верхней части) привариваются опоры для установки решетки. На опоры может устанавливаться казан (без решетки). Решетка изготавливается из арматуры или труб малого диаметра.
В боковой поверхности вырезают окно для дверцы. Дверцу из металла крепят с помощью заводских или самодельных петель, можно поступить проще – повесить на стальные крюки.
Садовые печи изготавливаются в двух вариантах – с дымовым патрубком или без него. Дымовой патрубок из куска метровой трубы уводит большую часть дымовых газов в канал, облегчая процесс приготовления блюд – через решетку проходит малая часть дымовых газов. При использовании сырых дров, древесных щепок в процессе горения образуется большое количество дыма. В этом случае сооружение дымохода обязательно. Иначе посуда излишне закоптится, пища приобретет резкий запах дыма.
Для монтажа дымохода в боковой поверхности второго (верхнего) диска прорезается отверстие соответствующего диаметра. К нему приваривается патрубок длиной 200 – 300 мм. К патрубку приваривается стальной отвод, к которому монтируют вертикальную трубу дымохода. Стыкование патрубка и вертикальной трубы иногда производят без отвода, через косой стык.
Инструкция по изготовлению буржуйки из колесных дисков своими руками
В холодное время года отапливать приходится не только жилые комнаты, но и ряд вспомогательных хозяйственных пристроек: теплиц, гаража, мастерских и др. Использовать для отопления подсобных помещений газ или электроэнергию слишком дорого. Альтернативным вариантом будет установка металлической буржуйки.
- Особенности конструкции
- Преимущества и недостатки
- Как сделать буржуйку из колесных дисков?
- Материалы
- Инструменты
- Пошаговая инструкция
- Пробная топка
- Вывод
Её можно топить не только качественным твёрдым топливом, но и древесными отходами, гнилым сушняком и т. п. Соорудить такой прибор своими руками вовсе не сложно, а если отказаться от покупки дорогостоящего металлопроката, и применить для изготовления корпуса старые автомобильные диски, то будет и недорого. Они производятся из толстостенного жаростойкого материала и отлично подходят для таких целей.
Особенности конструкции
При изготовлении печи из дисков автомобилей нужно учитывать одну особенность. По нормам для сооружения твердотопливных пламенных прибор расстояние между подом топочной камеры и колосниковой решёткой, т.е. от места закладки топлива до первой преграды выходу дымовых газов в вертикальном направлении (например свода топочного отдела) должно составлять минимум 45-50 см. Это в случае, если в буржуйку предполагается загружать кондиционный вид топлива. Когда топят сырыми дровами или древесными отходами, указанный размер должен быть увеличен до 65-80 см.
Объясняется это тем, что твёрдое топливо при горении выделяет пиролизный газ, который вылетает через прямой дымоход в атмосферу, унося с собой существенную долю тепла. При соприкосновении пиролизных газов с менее горячей поверхностью они остывают, не успев разделиться и догореть, и выпадает сажа. При дальнейшей эксплуатации такой печи свод топки и внутреннюю поверхность покроет плотный слой нагара, который не только снизит КПД прибора, но и повысит опасность возникновения пожара.
Схематичный вид буржуйки из колесных дисков
Буржуйка из колёсных дисков своими руками чаще топится именно бросовым топливом, а оптимальная схема печи из такого рада материала не позволяет создать высокий топочный отдел. Тогда используют не стандартные колосники, а изготавливают специальную конструкцию состоящую из:
- из листовой стали толщиной от 6 мм;
- прутьев арматуры диаметром 12-14 мм.
Нестандартная колосниковая решётка вкладывается в прибор с небольшим зазором (5-8 мм), который необходим из-за отличия в температурном коэффициенте линейного расширения материалов.
Такой вариант колосниковой системы решает и проблему очистки печи от золы. В качестве зольника в печи из дисков можно использовать жестяную банку диаметром 15-20 см. А, чтобы для процесса горения хватило воздуха дымоход должен быть диаметром не менее 100 мм и высотой от 2 м.
В горизонтальной модели печки из дисков колосники не устанавливаются, топливо горит непосредственно на поду. Для регулировки притока воздуха в поддувало устанавливают заслонку.
Преимущества и недостатки
К преимуществам использования печи из автомобильных дисков можно отнести:
- Низкую себестоимость. Сооружение отопительного прибора не требует больших вложений денежных средств, так как его самая материалоёмкая часть изготавливается из бесхозных колёсных дисков.
- Прочность и достаточно длительный срок эксплуатации. При производстве автомобильных дисков используют толстую сталь, которая обладает высокой прочностью, поэтому такой самодельный агрегат будет верно служит не один отопительный сезон.
- Высокую термическую устойчивость. Учитывая особенность сплава стали, из которого применяют для изготовления автомобильных дисков, прибор способен выдержать воздействие частого и длительного нагрева до высоких температур.
- Быстроту нагрева. Прибор такой конструкции может быстро нагреться до нужной температуры независимо от того, какой тип топлива будет в неё загружен.
- Отсутствие ограничений по габаритам. Для сооружения печи можно выбрать диски, более подходящего размера и поднять конструкцию вверх не только из двух, а и из трёх, четырёх и более дисков.
- Высокую теплоотдачу. КПД самодельной печку из автомобильных дисков достигает 80 — 85%.
Однако буржуйки из автомобильных дисков, собственно, как и другие металлические печки:
- неспособны накопить и сохранить тепло на долгое время. Корпус из металла быстро отдаёт тепло и остывает, поэтому такая буржуйка будет обогревать постройку, только пока в ней горят дрова или другой вид топлива;
- требуют установки высокой дымоотводной трубы. Для обеспечения достаточного уровня тяги, необходимо сооружать дымоотводную трубу высотой не менее 2 м;
- должны регулярно подвергаться чистке всех отделов, и особенно тщательно дымохода. Дымоотводную трубу большого диаметра нужно чистить не реже чем 1 раз в 1,5-2 месяца. Если её диаметр маленький, то эта процедура должна проводиться с периодичностью 1 раз в неделю.
к содержанию ↑
Как сделать буржуйку из колесных дисков?
Буржуйка из колёсных дисков будет переносной, что очень удобно, так как использовать такую конструкцию можно по мере необходимости в не только в гараже, но и в других помещениях. Она может устанавливаться как в горизонтальном, так и в вертикальном положении. Обе модели обладают высокой теплоотдачей, а отличаются друг от друга только наличием колосников и расположением дымоотводной трубы.
Материалы
Для сооружения буржуйки желательно использовать части от колёс легковых или грузовых автомашин малой грузоподъёмности. Диски от грузового многотоннажного автомобиля слишком массивные, буржуйка из них получится громоздкой и тяжёлой. В такой конструкции будет сложно обеспечить герметичность соединений при стыковке отдельных элементов.
Кроме самих дисков для сборки печи своими руками потребуются и несколько дополнительных материалов:
- пруты арматуры диаметром 20 — 24 мм;
- стальной уголок;
- листовой металл толщиной 4-5 мм;
- термостойкая краска;
- несколько болтов и гаек;
- труба диаметром 100 — 150 мм и толщиной стенки не менее 5 мм.
к содержанию ↑
Инструменты
Комплект инструментов, необходимый для сооружения буржуйки из автомобильных дисков, должен состоять из:
- сварочного агрегата и электродов;
- болгарки (УШМ) с набором зачистных и отрезных дисков;
- дрели;
- газового резака;
- наждачной бумаги;
- кисти;
- кувалды;
- молотка;
- измерительных и разметочных приспособлений: мела или маркера, рулетки и линейки
Для защиты поверхности тела и глаз от вредных излучений сварочной дуги, искр и брызг работать нужно в специальном обмундировании, укомплектованном брезентовым костюмом и рукавицами, закрытыми ботинками, головным убором под щиток, щитком сварщика и очками.
Пошаговая инструкция
Схемы устройства разных моделей печей-буржуек из дисков автомобильных колес
Чертёж вертикальной модели буржуйки из 4-х колёсных дисков
При самостоятельном изготовлении печи из дисков нужно соблюдать следующую последовательность действий:
- вырезать у всех четырёх дисков центральную часть болгаркой вместе со ступицами;
- опустить дымоотводную трубу в верхнее отверстие и заварить;
При изготовлении такой буржуйки нужно учитывать, что специальный состав сплава стали колёсных дисков не нормируется для сварочных работ. Поэтому при соединении дисков нужно выполнять следующие правила:
- за один раз допускается сварка только двух сопряжённых деталей, собирать сразу весь прибор запрещено;
- после того как образовался шов, детали со сваренными краями нужно оставить в покое примерно на 3 — 5 минут, чтобы произошло рассасывание остаточного внутреннего напряжения;
- на поверхности сварного шва должна отсутствовать какие-либо видимые дефекты: трещинки, брызги, раковинки или пузыри.
к содержанию ↑
Пробная топка
Готовая печь должна отстояться в течение суток для полного рассасывания тех же остаточных напряжений. После этого она должна быть подвергнута испытательной топке при полной закладке топлива в течение 3-х часов. При этом её дверцы топочная и поддувальная должны быть в открытом состоянии.
Во время первой пробной топки отжигаются и внутренние поверхности прибора. Если обнаружились мелкие дефекты сварочных швов, но не более двух на шов, их устраняют через сутки после того как печь остынет. Затем следует ещё раз повторить прогон прибора с отжигом.
Вывод
Буржуйка из автомобильных дисков хотя и сооружается из бывших в употреблении деталей, но очень добротных по своей конструкции. Толстая прочная сталь отслужила своё время в автотранспорте и получила определённую долю деформаций, но как материал для надёжного корпуса обогревательного прибора может прослужить не один год. Самое главное, что такая печь будет безопасна и эффективна в обогреве помещения, а решение вопроса по оформлению её внешнего вида зависит от фантазии владельца.
Шлем греческого Гоплита своими руками
Итак, мастер-класс по созданию Шлема Греческого Гоплита.
Мои сыновья учатся в школе. Ученики пятого класса в подобных школах изучают Древнюю Грецию, а в конце года показывают спектакль, в нашем случае по фрагментам «Илиады». Соответственно костюмы и декорации изготавливаются учениками и их родителями 🙂 Нам нужно было создать костюм Греческого Гоплита.
В этом мастер-классе я хотела бы рассказать, как мы делали Шлем. Надо сказать, что я перерыла весь русско- и англоязычный интернет и удовлетворяющей меня подробной информации не нашла, поэтому, я надеюсь, что мои изысканию еще хоть кому-нибудь пригодятся.
Так как с самого начала я не планировала написание статьи, то начальные этапы будут иметь скорее словесное описание.
Наш выбор пал на технологию папье-маше. За основу для Шлема можно использовать модель из скульптурного пластилина, болван из банки или цветочного горшка, ну и т. д., нам попался вот такой пластиковый шлем русского богатыря
1. Варим клейстер, я использовала следующий рецепт:
В 250 мл теплой кипяченой воды тщательно размешиваем 3 столовых ложки муки.
В кастрюлю наливаем 250 мл горячей кипяченой воды (говорят это важно) ставим на плиту, и туда, помешивая, тонкой струйкой вливаем мучную взвесь.
Варим, постоянно помешивая, до первых пузырей.
Даем остыть.
Добавляем строительный клей ПВА в пропорции 1:2 (1 – клей, 2 – клейстер).
Готовый клейстер лучше хранить в холодильнике, так как он быстро портится.
2. Рвем газеты на полосы, длина 8-10 см, ширина 2-3 см, все края кусочков должны быть рваными.
3. Так как Шлем изначально нашему мальчику был маловат, мы нарастили объем пупырчатой пленкой, а сверху закрыли все пищевой пленкой, чтобы заготовка потом легче снималась.
4. Начинаем наклеивать газету слой за слоем прямо на нашу болванку. В работе очень удобно использовать рекламные газеты, так как на них с одной стороны – цветная печать, а с другой – черно-белая. Соответственно можно чередовать слои цветной-черно-белый, а также по расположению клочков бумаги: вертикально-горизонтально.
5. Бумагу удобнее всего мазать прямо рукой, макая ее в клей, нужно тщательно следить, чтобы между слоями газет не было воздушных пузырей и излишков клея.
6. Таким образом мы нанесли 8 слоев газеты и оставили сушить на несколько суток. Торопиться снимать не стоит, так как верхние слои могут казаться совершенно сухими, а внизу, у пленки будет еще влажно.
7. Затем мы сняли заготовку с болванки, пришлось резать спереди по центральной линии практически до макушки, так как подсохшая заготовка очень плотно облегала болванку.
8. Вырезали глазницы и нарастили при помощи картона нащечники, все это обклеили еще несколькими слоями газеты, внимательно следя за тем, чтобы разрез не сместился. Получилась вот такая заготовка. Выклеивали ее уже, надев на кастрюлю, подходящего диаметра.
9. Теперь нужно сделать задник шлема и плюмаж. Задник мы сделали из нескольких слоев папье-маше на силиконовой форме для выпечки, получилась такая «полочка», выступающая наружу. Просушили и подклеили к задней части шлема.
10. Плюмаж сделан из гофрокартона, покрытого сверху слоем массы из яичных решеток.
Выглядит она вот так:
Под плюмаж вырезаем отверстие так, чтобы он оооочень плотно в него входил и вклеиваем в него клеем ПВА нашу заготовку. Изнутри выравниваем поверхность шлема этой же массой, вот так это выглядит в подсохшем виде:
На этом фото видно и часть шлема, которая выступает назад.
11. Прорезаем отверстие между нащечниками и из куска папье-маше, вырезанного между ними делаем наносник. Крепим его на место при помощи ПВА.
Весь шлем выклеиваем 3-4 слоями газеты, в итоге получаем вот такую заготовку.
12. Грунтуем шлем клейстером.
13. Покрываем шлем акриловой шпатлевкой
14. Шлифуем шкуркой №5, а затем нулевкой.
15. Намечаем карандашом контур будущей «чеканки»
16. Наносим 3D контуром полосы по намеченным линиям, получаем объемные элементы.
17. Грунтуем шпатлевку разведенной акриловой краской и покрываем Шлем краской-спреем «Медь молотковая». Стараемся не наносить краску слишком интенсивно, могут возникнуть подтеки. Просушиваем.
18. Наносим кисточкой битумную патину. Лучше это делать небольшими фрагментами. Удаляем излишки патины ватными дисками. Медь приобретает более желтый оттенок, в «раковинках» задерживается черный цвет.
Удаляем излишки патины ватными дисками. Медь приобретает более желтый оттенок, в «раковинках» задерживается черный цвет.
19. Для создания оперения Шлема мы использовали настоящий конский хвост.
20. При помощи ниток и текстильного клея делим хвост на маленькие пучки под размер щели в плюмаже.
21. Вклеиваем пучки в щель.
21. Ну, собственно и все, Шлем готов.
22. Вот несколько фото со спектакля.
Все шлемы сделаны из папье-маше на этой заготовке. Для плюмажей использовались: ворс от щетки, нитки, крашеный веник 🙂
Порадуйтесь за меня, так как я получила колоссальное удовольствие от процесса, особенно если учесть, что это моя первая попытка сделать что-то из папье-маше.
master_klassМастер-класс
каждый из нас – Мастер
Продолжение “Илиады” или Шлем Греческого Гоплита
Итак, обещанный ранее мастер-класс по созданию Шлема Греческого Гоплита.
Мои сыновья учатся в школе http://www.wsoglasie.ru
Ученики пятого класса в подобных школах изучают Древнюю Грецию, а в конце года показывают спектакль, в нашем случае по фрагментам «Илиады».
Соответственно костюмы и декорации изготавливаются учениками и их родителями 🙂
Нам нужно было создать костюм Греческого Гоплита.
В этом мастер-классе я хотела бы рассказать, как мы делали Шлем. Надо сказать, что я перерыла весь русско- и англоязычный интернет и удовлетворяющей меня подробной информации не нашла, поэтому, я надеюсь, что мои изысканию еще хоть кому-нибудь пригодятся.
Так как с самого начала я не планировала написание статьи, то начальные этапы будут иметь скорее словесное описание.
Наш выбор пал на технологию папье-маше. За основу для Шлема можно использовать модель из скульптурного пластилина, болван из банки или цветочного горшка, ну и т. д., нам попался вот такой пластиковый шлем русского богатыря
1. Варим клейстер, я использовала следующий рецепт:
В 250 мл теплой кипяченой воды тщательно размешиваем 3 столовых ложки муки.
В кастрюлю наливаем 250 мл горячей кипяченой воды (говорят это важно) ставим на плиту, и туда, помешивая, тонкой струйкой вливаем мучную взвесь.
Варим, постоянно помешивая, до первых пузырей.
Даем остыть.
Добавляем строительный клей ПВА в пропорции 1:2 (1 – клей, 2 – клейстер).
Готовый клейстер лучше хранить в холодильнике, так как он быстро портится.
2. Рвем газеты на полосы, длина 8-10 см, ширина 2-3 см, все края кусочков должны быть рваными.
3. Так как Шлем изначально нашему мальчику был маловат, мы нарастили объем пупырчатой пленкой, а сверху закрыли все пищевой пленкой, чтобы заготовка потом легче снималась.
4. Начинаем наклеивать газету слой за слоем прямо на нашу болванку. В работе очень удобно использовать рекламные газеты, так как на них с одной стороны – цветная печать, а с другой – черно-белая. Соответственно можно чередовать слои цветной-черно-белый, а также по расположению клочков бумаги: вертикально-горизонтально.
5. Бумагу удобнее всего мазать прямо рукой, макая ее в клей, нужно тщательно следить, чтобы между слоями газет не было воздушных пузырей и излишков клея.
6. Таким образом мы нанесли 8 слоев газеты и оставили сушить на несколько суток. Торопиться снимать не стоит, так как верхние слои могут казаться совершенно сухими, а внизу, у пленки будет еще влажно.
7. Затем мы сняли заготовку с болванки, пришлось резать спереди по центральной линии практически до макушки, так как подсохшая заготовка очень плотно облегала болванку.
8. Вырезали глазницы и нарастили при помощи картона нащечники, все это обклеили еще несколькими слоями газеты, внимательно следя за тем, чтобы разрез не сместился. Получилась вот такая заготовка. Выклеивали ее уже, надев на кастрюлю, подходящего диаметра.
9. Теперь нужно сделать задник шлема и плюмаж. Задник мы сделали из нескольких слоев папье-маше на силиконовой форме для выпечки, получилась такая «полочка», выступающая наружу. Просушили и подклеили к задней части шлема.
10. Плюмаж сделан из гофрокартона, покрытого сверху слоем массы из яичных решеток.
Выглядит она вот так:
Под плюмаж вырезаем отверстие так, чтобы он оооочень плотно в него входил и вклеиваем в него клеем ПВА нашу заготовку. Изнутри выравниваем поверхность шлема этой же массой, вот так это выглядит в подсохшем виде:
На этом фото видно и часть шлема, которая выступает назад.
11. Прорезаем отверстие между нащечниками и из куска папье-маше, вырезанного между ними делаем наносник. Крепим его на место при помощи ПВА.
Весь шлем выклеиваем 3-4 слоями газеты, в итоге получаем вот такую заготовку.
12. Грунтуем шлем клейстером.
13. Покрываем шлем акриловой шпатлевкой
14. Шлифуем шкуркой №5, а затем нулевкой.
15. Намечаем карандашом контур будущей «чеканки»
16. Наносим 3D контуром полосы по намеченным линиям, получаем объемные элементы.
Даем высохнуть.
17. Грунтуем шпатлевку разведенной акриловой краской и покрываем Шлем краской-спреем «Медь молотковая». Стараемся не наносить краску слишком интенсивно, могут возникнуть подтеки. Просушиваем.
18. Наносим кисточкой битумную патину. Лучше это делать небольшими фрагментами. Удаляем излишки патины ватными дисками. Медь приобретает более желтый оттенок, в «раковинках» задерживается черный цвет.
Удаляем излишки патины ватными дисками. Медь приобретает более желтый оттенок, в «раковинках» задерживается черный цвет.
19. Для создания оперения Шлема мы использовали настоящий конский хвост.
20. При помощи ниток и текстильного клея делим хвост на маленькие пучки под размер щели в плюмаже.
21. Вклеиваем пучки в щель.
льььб
21. Ну, собственно и все, Шлем готов.
22. Вот несколько фото со спектакля
Все шлемы сделаны из папье-маше на этой заготовке. Для плюмажей использовались: ворс от щетки, нитки, крашеный веник 🙂
Экипировка античных воинов: древнегреческий гоплит
В VIII веке до н.э. в Греции начался длительный период подъёма, сопровождавшийся появлением ряда крупных городских центров, развитием городского ремесла и сельского хозяйства. Социальной структурой общества в это время становится гражданская община-полис. Он представлял собой союз взрослых мужчин, земледельцев и воинов, населявших небольшие долины, на которые горными грядами была расколота страна. Политическая и военная организация полиса совпадали: гражданин был одновременно земледельцем и воином, обязанным защищать свою родину с оружием в руках.
Основой военной организации греков в это время являлась фаланга, которая представляла собой плотный пехотный строй тяжеловооруженных воинов, объединённых друг с другом общностью происхождения, родственных и соседских связей. Её эффективность на поле боя в большей степени определялась совместными действиями рядовых бойцов, нежели героизмом отдельных воинов. Мужество и военная доблесть заключались в том, чтобы сражаться, стоя на одном месте, локоть к локтю со своими боевыми товарищами. Победа в этих условиях также обезличивалась, становясь атрибутом всех воинов, что содействовало укреплению между ними отношений равенства и демократической политической организации.
Снаряжение сражавшихся в рядах фаланги воинов зависело от их социального происхождения. Богатые граждане служили в коннице, средний класс – в тяжеловооруженной пехоте, бедняки – в легковооруженной пехоте. Стандартное снаряжение тяжеловооруженного пехотинца, или гоплита, состояло из щита, шлема, доспеха, поножей, пары копий и меча. В новом интерактивном спецпроекте Warspot рассказывает об оружии и снаряжение греческих гоплитов VII – VI веков до н.э.
Вооружение и части снаряжения гоплита обозначены значками-маркерами. Чтобы ознакомиться с историей и описанием интересующего элемента, щёлкните по соответствующему маркеру.
Панцирь
Появление двустворчатой кирасы в Греции относится еще к Бронзовому веку. Широкое распространение она получила в VIII – VI веках до н.э. Из-за своей высокой стоимости по-настоящему массовым типом доспеха панцирь не стал, поскольку испытывал сильную конкуренцию со стороны льняных доспехов. По современным представлениям, такой панцирь носили лишь 10 процентов воинов, сражавшихся преимущественно в первых рядах фаланги. Вес современных реконструкций доспеха составляет примерно 6 кг.
Мастера изготавливали панцирь из бронзы, отбивая металлический лист на каменной форме. Доспех состоял из передней и задней створок, скреплявшихся на плечах и на боках при помощи вставлявшихся в прорезы петель или ремней. Собранный панцирь имел бочковидную форму, схематично повторявшую мускулатуру мужского торса. В обеих створках имеются вырезы для горла, рук и талии воина. Нижняя часть панциря имеет так называемую колоколовидную форму из-за характерных широких отбортовок. Такая форма позволяла воину сидеть, не снимая панцирь. Сам доспех был короткий и защищал корпус воина лишь до пояса.
Поверхность доспеха полировалась и начищалась до зеркального блеска. Элементом декора являлись чеканные и гравированные фигуры, которые в наиболее роскошных и дорогостоящих экземплярах образовывали целые композиции. При ношении такой доспех несколько сковывал движения. В то же время он был достаточно легок, обеспечивал защиту от метательного оружия и надежно защищал тело воина в рукопашной схватке.
Греческие шлемы VIII – VI веков до н.э. постепенно приобрели закрытую форму. Их характерными элементами являлись глубокий назатыльник, широкие нащечники, а также наносник, составлявшие единое целое с куполом. Такой шлем почти полностью закрывал голову, скулы и лицо воина, оставляя лишь глазные прорези и широкую щель для дыхания. В бою шлем обеспечивал своему владельцу надежную защиту от самых различных ударов. Большое количество археологических находок шлемов и изображений на вазописи свидетельствует о широком их распространении среди воинов.
Самые ранние модели шлемов изготавливались из двух или более половин, сваривавшихся друг с другом вдоль линии гребня. Постепенно мастера-оружейники научились создавать гораздо более надежные цельнокованные шлемы, приобретавшие со временем все более сложную и изящную форму. Толщина бронзы в разных частях шлема могла колебаться от 1,5 до 3 мм, его масса составляла 5 кг.
На голове шлем носили с мягким подшлемником, для крепления которого по всему периметру вдоль края проделывалась серия близко расположенных отверстий. На более поздних находках подобных отверстий нет: возможно, подшлемник мог просто приклеиваться к внутренней поверхности шлема.
Из-за плохой вентиляции и слышимости перед боем шлем носили высоко на макушке головы, опуская его на лицо лишь непосредственно перед атакой.
Гребень
Украшением шлема служил высокий гребень, изготавливавшийся из конского волоса. Гребень визуально увеличивал рост воина, придавая ему грозный, устрашающий вид. Для крепления гребня использовался съемный держатель, который, скорее всего, делался из дерева. Его вид известен по вазописи, рельефам и скульптурным изображениям. К поверхности шлема гребень крепился посредством системы петель и прорезей, которая в большинстве случаев оказалась утраченной.
Важнейшим элементом защитного снаряжения гоплита был щит, который имел круглую, слегка выпуклую форму и диаметр 0,8 – 1 м. Такой щит надежно прикрывал корпус воина от подбородка до колена, а также пространство слева от него, где мог располагаться легковооруженный напарник. Внутри полости щита находились две рукояти. В центральную рукоять – порпакс – просовывалась рука до локтя, у обода щита находилась другая рукоять, – антилабе, – которую он держал кистью. Таким образом, вес щита равномерно распределялся по левой руке и плечу.
Изготавливали щит из дерева, обычно тополя или ивы, снаружи его обтягивали бычьей кожей, а также иногда покрывали листовой бронзой. Чаще бронзовыми были только накладки на лицевой стороне, а также обод. Декор щита мог быть очень роскошным и включал иногда целые композиции фигур, выполненных из металла, слоновой кости и эмали.
Вес современной реконструкции щита колеблется от 7 до 10 кг. Дома и в походе щит хранился в кожаном чехле, в котором он мог носиться за спиной на погонном ремне.
Поножи
В VII веке до н.э. поножи были короткими и не закрывали колена. Они имели простую форму и крепились к ноге посредством пары ремней. В VI веке до н.э. эта деталь доспеха достигла полной длины от колена до подъема стопы. В это время им также стали придавать анатомическую форму, позволявшую поножам более плотно сидеть на ноге. Лишь сзади оставалась узкая щель, необходимая для их надевания.
Чтобы плотно закрепить доспех на ноге, его обвязывали двумя ремнями, один из которых проходил под коленным выступом, другой в области щиколоток.
Развитие формы греческих мечей VII–VI веков до н.э. следовало за прототипами эпохи Бронзового века. Меч этого времени имел прямой обоюдоострый клинок листовидной формы. Его длина не превышала 60 см, в нижней трети лезвие слегка расширялось. Клинок имел ромбовидное сечение и короткое острие. Рукоять состояла из пары деревянных плашек, заклепками крепившихся к рамочной основе. В наиболее роскошных экземплярах она изготавливалась из слоновой кости и украшалась золотыми гвоздиками. Перекрестье у меча отсутствовало.
Меч являлся преимущественно колющим оружием, его острием противника старались поразить в лицо, горло или верхнюю часть груди. Такая техника фехтования была предпочтительнее по совершенно прозаичной причине. Из-за несовершенства металлургии мастера часто перекаливали клинок, который становился от этого хрупким. При сильном ударе меч мог просто переломиться пополам.
Меч носили в деревянных, обтянутых кожей ножнах, с костяной бутеролью (нижней частью) и массивным окончанием. Ножны подвешивались к перевязи и носились высоко под мышкой на левом боку.
Копьё
Вазопись VII–VI веков до н.э. изображала воинов вооруженными двумя копьями, одно из которых они метали, а второе использовали в рукопашной схватке. С распространением гоплитской фаланги метательный бой отошел на второй план, гоплит стал сражаться одним копьём, а когда оно ломалось — брался за меч. На вазах гоплитские копья обычно изображались укороченными. По археологическим находкам можно высчитать длину древка, которое колебалось от 2,2 до 2,7 м. Для древка использовались различные породы древесины: ясень, ива, тополь, кизил.
Хитон
Греки одевали под панцирь хитон, который представлял собой широкую рубашку без рукавов с вырезом для головы и рук. Хитон изготавливался из двух прямоугольных кусков ткани, которые сшивались по бокам и на плечах, так что оставалось только место, чтобы просунуть голову и руки. На плечах широкие края хитона закрывали верхнюю часть рук, создавая впечатление ложных рукавов. Для большей свободы движений шов на правом плече иногда распускали.
Хитон, как правило, подпоясывался, иногда с напуском. Длина подола зависела от возраста и социального статуса. Воины обычно носили короткий хитон, достигавший середины бедер. Ткань могла окрашиваться в яркие цвета и украшаться узорной вышивкой.
Шлемы древних греков
История эволюции шлемов Древней Греции восходит к Микенской цивилизации с середины 2-го тысячелетия до нашей эры. Уже этим временем датируются находки самых ранних шлемов, а также их изображения на фресках. Кроме того, имеются письменные источники – Гомером в «Илиаде» были описаны конструкции шлемов героев Троянской войны (около 1200 годов до нашей эры). С этих пор начинается создание различных типов шлемов. Самые ранние шлемы, найденные на территории Древней Греции после Троянской войны, датируются 9-ым веком до нашей эры. В основном шлемы тех времен схожи по форме с ассирийскими шлемами. С 7 века до н. э. ремесленники Эллады стали производить полностью закрытые шлемы, которые в 6 веке до н. э. приобрели наиболее известную на сегодняшний день форму, названную коринфской. Коринфские шлемы стали одним из символов Древней Греции и обязательной принадлежностью гоплитов на фресках и керамики. С середины 5-го века до нашей эры коринфские шлемы видоизменялись с развитием центров ремесла в Аттике, Македонии, южной Италии и других местах. Появились новые, более открытые виды шлемов (беотийские, халкидские). С началом завоеваний Александра Македонского (330-е годы до н. э.) на поле боя побеждали в первую очередь массовые армии, для вооружения которых понадобились более практичные и унифицированные шлемы. К началу экспансии Древнего Рима во 2-ом веке до нашей эры самыми распространёнными были шлемы фракийского типа, и с тех пор развитие доспехов было связано уже с эволюцией римского вооружения.
Типы греческих шлемов:
- Предысторические шлемы (Archaic)
- Иллирийский тип (Illyrian)
- Коринфский или дорийский тип (Corinthian)
- Халкидский тип (Chalcidian)
- Аттический тип (Attic)
- Беотийский тип (Boeotian)
- Фригийский тип (Phrygian)
- Фракийский тип (Thracian)
Греческие шлемы из музея в Олимпии. 7-6 век до н.э.
Предысторические шлемы (Archaic)
В древности греки называли шлемы словом, которое означало шапку из собачьей кожи — κυνέη (дословно “собачья”). У Гомера в «Илиаде» словом κυνέη обозначаются как шапка, так и всякий шлем, кожаный или металлический, но без налобника, плюмажа и нащёчников. Медные шлемы с нащёчниками и плюмажем из конских волос Гомер называет словом κόρυς. По происхождению κόρυς родственно слову κέρας, “рог”, и возможно шлемы так называли из-за наличия украшений в виде рогов или плюмажа особой формы.
Геродот, описывая одеяния и вооружения персидской армии, говорит о лисьих шапках (шлемах?) на головах фракийцев. Также он упоминает о кожаных шлемах других племён. Значит, ещё в начале 5-го века до н. э. такие шлемы не были экзотикой. Шапки из войлока, шкур и кожи укрепляли пластинами железа, костями, клыками, деревом или любым другим прочным материалом, не требующим особых ремесленных навыков. Позже стали сгибать по форме головы бронзовые пластины, охватывающие подкладку из того же войлока и кожи. Шлемы героев Троянской войны, созданные не греками, сильно отличались от тех, которые греки рисовали спустя шесть веков на вазах, и состояли из четырёх пластин.
Ввиду примитивной конструкции составной шлем дошел до нашего времени из древности буквально в паре экземпляров. Первые цельнометаллические шлемы появились в Греции в 15 веке до нашей эры. В музее Ираклиона на Крите представлен частично сохранившийся бронзовый шлем с удлинёнными нащёчниками и заострённым кверху кумполом с навершием для крепления плюмажа из конского хвоста.
После Троянской войны (на рубеже 13—12 веков до нашей эры) случилось переселение народов. В Элладе настали «тёмные» века, и племена греков утеряли даже письменность, не говоря о ремесленных навыках. Первые найденные бронзовые шлемы в Элладе 1-го тысячелетия до нашей эры датируются 8 веком до н. э. и воспроизводят формы ассирийских шлемов с прямоугольным вырезом для лица, сформированным широкими треугольными нащёчниками, заострённым кумполом и высоким навершием с украшением в виде бронзовой дуги. Условно такие шлемы называют коническими. После исчезновения навершия и сглаживания кумпола к полусферической форме внешний вид шлема приближается к иллирийскому типу.
Иллирийский тип (Illyrian)
Иллирийские шлемы — первые цельнометаллические шлемы, производившиеся в Древней Греции после «тёмных веков». Листы бронзы выгибали по форме головы, соединяли внахлёст и скрепляли заклёпками в местах соприкосновения, в результате чего на макушке образовывались продольные рёбра жёсткости. Позднее греки научились ковать шлемы из цельной заготовки, традиционно сохраняя продольные рёбра. Шлемы подобного типа в основном обнаружены на территории, которую в античное время занимала Иллирия, что и дало название данному типу.
Характерной особенностью шлема служат отсутствие наносника, продольные рёбра на макушке, крупные треугольные «уши»-нащёчники и прямоугольный вырез для лица. Если добавить массивный наносник, прикрыть шею удлинённой затылочной частью, придать фигурную форму «ушам»-нащёчникам и выгнуть их вокруг лица, то шлем эволюционирует в разряд коринфских.
В 7-ом веке до нашей эры иллирийские шлемы вышли из употребления в Элладе, их вытеснило развитие ремесленного производства коринфских шлемов. Иллирийский тип применялся вплоть до 5-го века до нашей эры в менее технологически развитой на тот момент Македонии. Периодом 725-650 годов до н. э. датируются 30 ранних конических шлемов, столько же иллирийских и 17 коринфских. В более позднее время, в 650-575 годах до нашей эры конические шлемы исчезают, количество иллирийских сокращается до 7, а число коринфских достигает 90.
Коринфский или дорийский тип (Corinthian)
Коринфские шлемы появились в 7-ом веке до нашей эры. Наибольшую популярность получили в 5-ом веке до нашей эры в греко-персидских войнах. К концу пятого века до нашей эры коринфский тип вытесняется более удобными халкидскими шлемами. Коринфский тип представлял собой полностью закрытый шлем, украшенный гребнем из конских волос. Давал полную защиту головы, однако наносник и закрытое лицо ограничивали обзор. Вне боя шлем сдвигался на затылок, открывая лицо. Коринфский шлем является непременным атрибутом гоплита на изображениях древнегреческой керамики 6-го века до нашей эры, даже если воин сражается обнажённым. Появление этого шлема связывают с развитием тактики боя в плотном строю фаланги, где воину не требовался хороший обзор по сторонам.
Обычно шлем разделён в области рта, но в греческих полисах южной Италии (Апулии) находят сплошные шлемы 6—5 века до нашей эры, которые напоминают котелок с отверстиями для глаз и дыхания характерной Т-образной формы, наносник разделяет «T» надвое. Этот тип шлема называется апуло-коринфский.
Халкидский тип (Chalcidian)
Халкидские шлемы появились в 6-ом века до нашей эры и просуществовали три столетия, пока не были вытеснены из массового употребления более простыми пилосами и фракийскими шлемами в 3-ем веке до нашей эры. Наносник у этого шлема символический или вообще отсутствует, за счёт чего увеличивается обзор. В районе ушей, в отличие от коринфского шлема, появляется фигурный вырез. Такой шлем более комфортный, но хуже защищает владельца. Нащёчники достаточно широкие и плоские, прямоугольной или округлой формы, часто фронтальный край нащёчника волнообразный. Нащёчники могут крепиться на петлях. Визуально шлем состоит из двух частей: верхний полусферический купол и нижняя часть, соединяющиеся в районе рельефно выступающего ободка.
Аттический тип (Attic)
Аттические шлемы — вариация халкидского шлема, изготовленная ремесленной школой в Аттике. Известный автор Питер Конноли классифицирует аттический тип как разновидность халкидского, у которого отсутствует наносник. Из других отличий от халкидского можно отметить заострённые лунообразные формы нащёчников, которые обычно крепились на петлях. Халкидский шлем часто украшали плюмажем и перьями, а на аттическом красовался архаичный карийский конный гребень.
Беотийский тип (Boeotian)
Беотийский шлем — кавалерийский шлем открытого типа, прославленный в эпоху Александра Македонского. Появился вероятно в Беотии в 5-ом веке до нашей эры, затем его переняли в Фессалии. По форме напоминает древнегреческую крестьянскую шляпу с широкими полями для защиты от солнца. Древнегреческий автор Ксенофонт рекомендовал такой шлем для всадников наряду с изогнутым мечом типа кописа. Его взяли на вооружение македонские гетайры, и носили правители эллинистических государств Азии в третьем веке до нашей эры. Имеет широкие поля, которые предохраняют от удара мечом сверху и прикрывают шею. Комфортен для длительного ношения в жарком климате, не ограничивает обзора.
Фригийский тип (Phrygian)
Фригийский шлем воспроизводит шапку скифов, фракийцев, других восточных народов. Удлинённая макушка загибается каплей вперёд. В этих шлемах сражались воины македонской фаланги. Позднее на макушке стали загибать металлический гребень, такие шлемы называются фракийскими. В Македонии бронзовые фригийские колпаки ко 2-ому веку до нашей эры трансформировались во фракийские шлемы, с вытянутым вверх кумполом и простым невысоким металлическим гребнем или плюмажем из перьев.
Фракийский тип (Thracian)
Фракийский шлем имеет вытянутый вверх купол. Наносник обычно отсутствует, плоские нащёчники имеют фигурные очертания или отсутствуют. Также для фракийского шлема характерен металлический гребень, наложенный поверх сферы.
Во 2-ом веке до нашей эры, ко времени римского завоевания Древней Греции, фракийский шлем стал самым распространённым в греческих армиях. Гребень становится совсем невысоким, зато появляется козырёк. Преимуществом стало удобство такого шлема, хороший обзор и манёвренность, которые защищали лучше сплошной брони, особенно от тяжёлых мечей и железных пик. Название шлему дал тот факт, что во времена Римской империи в нём сражались гладиаторы из фракийцев, у которых он закрывал ещё и лицо полностью.
Переход на железные доспехи заставил отказаться от универсальных фракийских шлемов.
Пилос (Pilos)
Пилос — шлем для легковооруженной пехоты. Основной шлем спартиатов в классический период, в том числе в период Пелопоннесской войны. Технологичен в производстве. Представляет собой коническую закругленную бронзовую шапку. Первые образцы в конце 2-го тысячелетия до нашей эры собирали из чешуек бронзы. Цельнометаллические пилосы появились к 5-ому веку до нашей эры. В 3 веке до нашей эры пилосы были вытеснены из Эллады аттическими шлемами.
Схожие темы
Литература
– Цыбульский С. Военное дело у древних греков. Ч. I. Вооружение и состав греческого войска. Варшава, 1889.
- Frisk H. Griechisches etymologisches Wörterbuch, Band I. — Heidelberg: Carl Winter’s Universitätsbuchhandlung. — 1960. — С. 925-926. «Илиада», XXII, 314
- Музей Ираклиона, комната 6, 1450—1300 гг. до н. э.
- Anthony Snodgrass, Archaic Greece: The Age of Experiment, University of California Press, 1981, p. 105, ISBN 0-520-04373-1
2 причины, почему гоплиты Эллады сменили закрытый шлем на открытый
Мы привыкли представлять себе греческого воина-гоплита вполне определенно: большой бронзовый круглый щит, средней длины пехотное копье, панцирь-торакс. А главное – шлем. Острохарактерный, легко узнаваемый шлем коринфского типа. Он же – дорийский:
В подобных шлемах воевала вся Эллада примерно с VII по V века до нашей эры. Самые ранние образцы восходят к VIII веку, итого вся история “коринфянина” – порядка 300 лет. Общепринятое название, кстати, восходит к городу Коринфу, близкому соседу Спарты, который был основным центром производства этих шлемов.
Строение
Коринфский или дорийский шлем – полузакрытого либо полностью закрытого типа. Он имеет средних размеров вырезы для глаз и развитый наносник, закрывающий переносицу полностью. Большинство подтипов (вдаваться в детали классификации сейчас не будем) этих шлемов оснащены вертикальной прорезью для дыхания, образованной двумя лицевыми пластинами. Хотя есть закрытые представители класса – вот, например:
Это не деталь скафандра рептилоида-захватчика с планеты Нибиру, это всего-навсего апуло-коринфский тип шлема. Такие были в ходу в VI-V веке в Апулии (Южная Италия). Там тогда было несколько греческих городов-колоний.
И не антенны на макушке у него, а крепления под султаны!
Говоря кратко: классический шлем гоплита закрывает почти всю голову, включая подбородок. Единственное уязвимое место – дыхательная прорезь. Ширина вертикальной щели для дыхания может составлять от 5 мм до 3-4 см – в зависимости от пожеланий владельца шлема. Чем уже щель, тем меньше шансов словить копьем в зубы.
У апуло-коринфского шлема вообще прорези нет, как и какой-нибудь другой дыхательной перфорации. Но в походе такие шлема сдвигались на затылок, так что воин мог дышать, а в бою. В бою возможностью дышать свежим воздухом гоплит жертвовал в пользу защищенности. Ибо просунуть острие копья в вертикальную прорезь стандартного “коринфянина” вполне возможно. Хотя и сложно.
Шлемы этих двух типов (у каждого есть отдельные плюсы и минусы, для нас сейчас несущественные) почти идеально подходят для копейного боя фалангой. Они очень неплохо защищают голову от удара копьем. Но чу!
В V веке до нашей эры (греко-персидская война, бои за Пелопоннес между Афинами и Спартой) коринфский шлем внезапно. Начинает сдавать позиции. Ему на смену приходит халкидский, а также его подвид – аттический.
Парадокс в том, что это – открытые шлема!
Халкидский шлем с нащечниками на петлях
Халкидский шлем
Он появился в конце VI века до нашей эры в Южной Италии и на Сицилии, в городах-колониях, основанных греками из Халкиса (городишко близ Афин). Как отмечает известный исследователь военной истории Античности Питер Коннолли, в самой Греции халкидских шлемов было найдено очень мало, зато там развился аттический шлем – очень похожий на халкидский, но без наносника.
В течение V века и воины из греческих колоний, в том числе гоплиты, и воины городов исторической, континентальной Греции – Спарты, Афин, Коринфа и других – начинают отказываться от закрытого, хорошо защищающего старого шлема в пользу нового, гораздо более легкого, открывающего лицо почти полностью. У аттического шлема не всегда есть даже наносник, он оснащен лишь небольшим назатыльником и нащечниками (иногда отлитыми заодно с куполом, иногда – на петлях).
Но даже эти нащечники обеспечивают заметно более худшую защиту, чем литые полосы бронзы, прикрывавшие нижнюю часть головы у коринфского шлема. Как? Почему?
Наступает эпоха завоеваний Александра Македонского. На головах его сариссофоров – либо аттические, как выше, либо фригийские шлемы, у которых опять-таки полностью открыто лицо!
Также входят в моду совсем простые шлемы – пилосы. В пилосе на иллюстрации ниже щеголяет центральный фалангит.
Что, правила копейного боя изменились, что ли, и в столкновении двух фаланг схлопотать острием в зубы уже не так реально?
Нет, конечно. Причины здесь в другом.
Первая причина
Это – экономика. Период после окончания Пелопоннесской войны, отчасти соответствующий завоевательным походам Александра, называют иногда “эпохой наемников”. Греческие и македонские армии, прежде довольно маленькие (та же Спарта никогда не могла выставить больше 9 тысяч гоплитов) резко увеличиваются в численности. Греческое Средиземноморье кишит наемниками всех мастей – с Балкан, с Родоса, с Апеннин, с Балеарских островов, из колоний Анатолии.
Им всем нужны шлема. А коринфский шлем, при всех своих достоинствах, имеет существенный недостаток: он очень сложен и дорог в производстве. Его форма близка к анатомической, шлем необходимо после отливки подгонять под форму головы владельца, поэтому для вооружения действительно крупных армий он не подходит. Как всегда это и бывает, необходимость массовой штамповки губит ручную работу на корню. Рядовые греческие и македонские солдаты переходят на более простые аттические шлемы, или на совсем простые пилосы. Да, они защищают в копейной стычке гораздо хуже. Но они и намного дешевле!
Пилос с нащечниками и маленьким назатыльником. Этих атрибутов могло и не быть.
Примечание: был в ходу еще и фригийский шлем, довольно сложной конструкции – в частности, многие сохранившиеся образцы имеют нащечники, отлитые в виде бороды и усов.
Но они все равно обеспечивают слишком слабую защиту от копья в лицо. Во-первых, верхняя часть лица у “фригийца” открыта полностью, во-вторых, фигурные бронзовые нащечники со слабым креплением к ободу шлема при сильном ударе легко ломаются. В них ничего нет от монолитной прочности архаичного “дорийца”.
Такие шлемы были в ту эпоху скорее признаком статуса, т.к. стоили много дороже пилосов.
Вторая причина
Это – изменение условий войны.
Дело в том, что греки до войны с персами практически не имели никакого другого рода войск, кроме тяжелой пехоты – гоплитов. Конников использовали только в качестве гонцов. Лучники и дротикометатели (пельтасты) почти отсутствовали. Они массово появятся в армиях полисов только во время Пелопонесской войны (431 – 404 год до нашей эры) – и в ряде сражений докажут, что способны самостоятельно справляться даже с самыми крутыми тогдашними “танками” – гоплитами Спарты!
Понимаете, что изменилось? Изменилась потребность в секторе обзора!
Архаичному гоплиту смотреть в бою по сторонам не требовалось. Цель – боец из вражеской фаланги – находилась только впереди. Потому обзор у коринфского шлема сужен в пользу увеличения площади защиты.
Но! Как только на поле боя появились пельтасты и лучники, имевшие обыкновение заходить фаланге в правый, неприкрытый щитами фланг, или расстреливать ее с тыла, у гоплита резко возросла необходимость в боковом зрении. Пельтастов, паразитов, надо постоянно держать в поле зрения, постоянно закрываться от них щитом, особенно если фаланга уже разбита. Нужно видеть, что происходит у тебя сбоку!
С конницей – то же самое. Конники, которых появилось довольно много уже в середине афино-спартанского конфликта, никогда не атаковали “лес копий” в лоб – они налетали с фланга и тыла. Опять-таки гоплиту требовался хороший обзор, чтобы вовремя их замечать. А то выскочат из какого-нибудь распадка внезапно, врубятся в правый фланг – и понесут потом пехоту домой на собственных щитах.
Именно поэтому шлемы, во-первых, становятся открытыми, а во-вторых – более высокими и “обтекаемыми”. Показанный выше фригийский шлем плохо защищает от укола копьем в лицо – зато весьма качественно от рубящего удара махайрой сверху вниз, с высоты лошади.
Кстати, позднее, в Средневековье, пикинеры швейцарцев и ландскнехтов тоже будут предпочитать высокий морион или кабассет с хорошим обзором – шлему с забралом любого типа.
Понравилась статья? Подпишитесь на канал, чтобы быть в курсе самых интересных материалов
Печь из дисков автомобиля для казана, как сделать своими руками
На чтение 9 мин Просмотров 5.2к.
Необходимость обеспечить горячее питание и обогрев при организации длительного отдыха на природе или даче может стать настоящей проблемой. Для приготовления пищи, отопления небольшого жилого помещения, гаража или бани печь из дисков автомобиля для казана станет эффективным универсальным решением. Благодаря простоте конструкции и доступности материалов затруднений при ее изготовлении не возникнет.
Особенности конструкции
Качественным конструктивным отличием этой модели печи является использование готовых секций из автомобильных дисков. Применение полуфабрикатов позволяет прибегать к простой технологии, значительно снижая трудоемкость работы. Обладая начальными навыками электродуговой сварки, умением обращаться с угловой шлифовальной машинкой, можно без труда соорудить очаг из дисков своими руками. По своим характеристикам такое изделие мало чем отличается от дорогостоящих печей, приобретенных в магазине. Здесь также имеются топка, откидная дверца и выемка, в которую можно свободно установить походный котелок, кастрюлю, решетку для гриля или несколько шампуров. Конструкция подходит для приготовления плова в казане, в состоянии заменить барбекю и мангал, быстро поднимает температуру в гараже или бане.
Еще одна отличительная особенность подобной печи – возможность изменения объема топки. В зависимости от размеров казана, свод можно поднять, оснастив его дополнительной секцией, что позволит при необходимости отопить более габаритное помещение.
Преимущества и недостатки
Самодельная печь под казан из дисков с оригинальной конструкцией обладает рядом преимуществ:
- Она отличается высокой теплоотдачей и мобильностью. Эти свойства превращают ее в универсальный нагревательный элемент, обеспечивающий равномерный прогрев. Компактные размеры позволяют транспортировать изделие в багажнике автомобиля, делают комфортными пикник, рыбалку, отдых на даче или дальнюю поездку.
- Из эксплуатационных свойств особо выделяется долговечность. Гарантией, что печь прослужит долго, будет низкоуглеродистый металл толщиной 3-4 мм из стали 10 или 15, идущий на изготовление дисков колес к машине. Конструкция не прогорит во время приготовления плова, не деформируется при нагреве, не покроется ржавчиной после первого дождя.
- Печка для казана из дисков устойчива к нагрузкам, отличается высокой прочностью. Дополнительные опоры в виде подставки или ножек только усилят эти преимущества.
- Это печь пламенного горения. Топливом для нее служат уголь, древесина, которые характеризуются экологичностью, широкой доступностью.
- Изготовление печи не требует высокой квалификации. Трудоемкость минимальная. Материальные затраты низкие.
Среди недостатков печи из автомобильных дисков:
- Листовая сталь быстро остывает. Придется постоянно контролировать процесс горения, следить за его интенсивностью, запасом топлива.
- Печь слишком низкая. Для комфортного использования необходимо соорудить подставку. Это дополнительные трудозатраты и материалы.
Чтобы изготовить качественную по своим техническим и эксплуатационным характеристикам печь, лучше применять диски без видимых следов деформации.
Необходимые материалы и инструменты
Перед тем, как приступить к работе по изготовлению мобильной печки, необходимо просчитать ее размеры и определить расход материала. С этой задачей поможет справиться сводная таблица.
Наименование материала | Типоразмер | Количество | Деталь | Примечание |
Диск колеса | 13” | 3 штуки | Кожух печи | Допускается замена на диски большего диаметра |
Пруток | D8x200 | 1 штука | Ручка на заслонку* | Допускается замена на D10 |
Пруток | D8x250 | 2 штуки | Ручка для транспортировки | Допускается замена на D10 |
Труба | D50х1,5×1500 | 2 штуки | Дымоход | — |
* Материал для задвижки, шарнирных петель подбирается по месту из наличия.
Возможны небольшие отклонения, связанные с особенностями конкретной конструкции.
Базовый набор инструментов включает:
- сварочный аппарат;
- угловую шлифмашинку;
- набор насадок по металлу;
- набор слесарных инструментов;
- слесарные тиски.
Расходные материалы:
- сварочные электроды;
- отрезные диски;
- зачистные диски;
- средства индивидуальной защиты.
Важно соблюдать правила ТБ и работать только исправным инструментом.
Способы изготовления
Несмотря на простоту конструкции, для изготовления печи из дисков необходимо обладать навыками работы со сварочным аппаратом, болгаркой и некоторыми знаниями в области создания изделий из металла.
Сварочный метод
Наиболее распространенным способом создания металлической печки для пикника является именно сварка. Для того чтобы изготовить качественное изделие, необходимо следовать инструкции:
- Болгаркой на одном из дисков нужно сделать симметричный вырез со стороны крепежных болтов. Его размеры соответствуют диаметру казана на расстоянии 2/3 высоты. Отсчет ведется от вершины выпуклой части дна. Посадка в печь на эту глубину обеспечит равномерный нагрев всего объема емкости и снятие с огня без лишних усилий.
- Далее следует подготовить диски к сварке. Для этого: удаляют остатки краски, ржавчину, зачищают свариваемые поверхности, снимают фаски.
- После этого печная конструкция собирается на ровной поверхности в такой последовательности:
- нижний диск устанавливается выпуклой стороной вниз;
- сверху на него крепится второй, но уже выпуклой стороной вверх;
- оба элемента необходимо прихватить сваркой;
- третий диск устанавливается на второй вырезом вверх. Его также следует приварить в нескольких местах;
- производится окончательная сварка всех стыков;
- отбивается шлак, проводится осмотр швов, устраняются дефекты. Выполняется зачистка швов. Особенно тщательно зачищается посадочное место под казан;
- на высоте 200 мм от дна печи мелом размечаются контуры заслонки. Ее размеры 180 х 200 мм;
- из вырезанной заготовки изготавливается заслонка. На короткую сторону привариваются трубки. В них вставляются шарниры, которые затем монтируются к кожуху печи. Чтобы скрыть неровности реза, устранить неизбежные зазоры, добавить жесткости, сохранить эстетику внешнего вида, можно приварить по периметру пруток;
- ручка и шпингалет привариваются по месту;
- на противоположной от заслонки стороне в верхнем диске размечается и вырезается отверстие под дымоход. Устанавливается дымоходная труба, фиксируется сварными точками, затем обваривается вкруговую.
Вырезаем круг из дискаПроводим сварочные работыСваривать диски нужно со всех сторонДолжен получиться такой шовПодготавливаем арматуру для ножекПривариваем фиксаторы для ножекУстанавливаем ножкиПривариваем ручкиРазмечаем место дверцыДелаем и крепим петли дверцыСнимаем слой краскиКрасим в черный цветВо избежание коробления сварку стоит выполнять короткими симметричными швами, выдерживать время до полного остывания шва.
Подгонка дисков по размеру
При этом способе вся конструкция становится разъемной, жесткие соединения отсутствуют. Добиться этого можно раздачей наружного обода одного колеса и осадкой другого – результатом станет плотное стыковое соединение. Операция осуществляется с помощью молотка. В нижнем диске вырезается технологическое отверстие для загрузки топлива. При таком варианте изготовления показатели печи ухудшаются: она станет «прожорливой», теплоотдача снизится. Чтобы в полной мере сохранить эксплуатационные характеристики, боковое отверстие можно не вырезать. Дрова будут загружаться через верхний вырез, но для этого придется каждый раз снимать казан.
Такая конструкция печи более технологична. Она разборная и менее трудоемкая в реализации. Однако существенными недостатками становятся низкий КПД, повышенный расход твердого топлива, ухудшенная тяга.
Разновидностью методики является использование комбинированного способа. Это компромиссный вариант создания печи, сочетающий главные плюсы сварки и метода подгонки дисков. Сваривать их между собой не надо, они вставляются один в другой. Стыковое соединение позаимствовано из метода подгонки. При помощи сварки изготавливаются только заслонка, ручки. Для большей жесткости не лишним будет предусмотреть крепеж для стяжки секций между собой.
Берем два автомобильных дискаВырезаем центральную частьПримеряем, подходят ли элементыДелаем герметичную конструкцию с помощью молоткаВырезаем отверстие для подачи дровГотовоДополнительные рекомендации
Для того чтобы подставка под казан из автомобильных дисков стала более удобной и практичной в использовании, необходимо позаботиться о специальных возможностях:
- Дополнительную устойчивость сборке можно придать с помощью ножек. На их изготовление идет профилированный прокат, который режется в размер. Заготовки привариваются к боковинам печи или днищу и фланцам. Тренога – лучший вариант с точки зрения устойчивости и экономичности.
- Хорошим решением будет изготовление отдельной подставки под печку из дисков автомобиля для казана. Ее преимущество в том, что она не связана жестко с основной конструкцией и сможет служить опорой для чего угодно. При наличии подставки профилированное днище нижней секции будет работать как колосник. Это заметно увеличит тягу и повысит температуру свода.
- Упростить проект, снизить трудоемкость, сэкономить на материалах можно, если изготовить печь из двух сегментов. В этом случае свод конструкции станет ниже, что негативно отразится на теплоотдаче. Это обусловлено тем, что при горении выделяются пиролизные газы, их вклад в общее тепловыделение решающий. При недостаточно высоком своде они не успевают полностью сгореть. Соприкосновение с холодными стенками кожуха вызывает осаждение сажи. Со временем внутренняя поверхность свода закоксовывается. Теплоотдача печи заметно снижается. Не исключено возгорание сажи.
- Универсальность конструкции позволяет преобразовать печь для казана в мангал и барбекю с минимальными изменениями. Без лишних вырезаний можно обойтись готовыми отверстиями, имеющимися на поверхности изделия, – они создадут несколько температурных зон. Если сверху установить решетку, она совместит функции рассекателя пламени и рашпера – это позволит одновременно готовить ростбифы разной степени прожарки. Важно понимать, что для большой компании потребуется более солидная печь, для ее изготовления подойдут диски от «Газели». Их не нужно сваривать между собой, что несомненный плюс. С функциями сварного шва успешно справится жаростойкий клей по металлу.
- Хорошие печи-буржуйки получаются при горизонтальном расположении колесных дисков. Их выпуклые части лучше срезать болгаркой. Сваренные между собой секции образуют вместительную толстостенную полость со сложной поверхностью. Такая буржуйка будет быстрее нагревать помещение и дольше остывать. Для изготовления подобной печи лучше использовать колесные диски от грузовых автомобилей, они обеспечат достаточный объем топки и увеличат теплоотдачу. КПД таких устройств выше.
Площадь под опорами должна превышать параметры казана: чем выше будет это отношение, тем устойчивее окажется вся конструкция.
Удобные печи с установленными ножкамиМожно установить решетку и использовать как барбекюПечи-буржуйки лучше греют при горизонтальном расположении дисковВидео
Признаки неисправности или неисправности тормозного ротора / диска
Роторы дисковых тормозов — это металлические диски, которые работают вместе с тормозными колодками и суппортами для замедления автомобиля. Тормозные роторы прикреплены болтами непосредственно к ступице колеса, поэтому их вращение напрямую зависит от скорости вращения колеса. Когда педаль тормоза нажата, суппорты прижимают тормозные колодки к вращающимся роторам, замедляя и останавливая колеса и автомобиль. Поскольку роторы замедляют движение автомобиля за счет трения от прямого контакта с тормозными колодками, они со временем изнашиваются, и в конечном итоге их необходимо будет заменить.Когда роторы имеют проблемы, они обычно вызывают любой из следующих 4 симптомов, которые предупреждают водителя о том, что они требуют внимания.
1. Шумные тормоза
Один из первых симптомов неисправных тормозных роторов — это шум. Если роторы деформированы (то есть не идеально плоские) или сильно изношены, они могут издавать визжащие или скрипящие звуки. Обычно деформированные роторы издают скрип, а сильно изношенные роторы издают царапающий звук. Однако визг может быть вызван также изношенными тормозными колодками.
2. Колебания от тормозов
Еще одним признаком неисправных тормозных роторов является чрезмерная вибрация или пульсация тормозов. Деформированные или чрезмерно изношенные роторы могут неравномерно вибрировать и вызывать вибрации, которые могут ощущаться в педали, а иногда и в рулевом колесе или шасси автомобиля. Кроме того, при нажатии педаль тормоза может ощущаться пульсирующей из-за деформации тормозных дисков. Это происходит потому, что педаль больше не контактирует с поверхностью ротора.
3. Канавки или царапины на роторе
Еще одним признаком неисправных или неисправных роторов являются визуальные царапины или бороздки на лицевой стороне ротора. Эти следы со временем могут появиться при повторяющемся контакте с тормозными колодками. Роторы имеют такую толщину, которая со временем изнашивается. Однако, если он ухудшится до определенного уровня, это снизит общую безопасность транспортного средства.
4. Увеличенные тормозные пути
Зазубрины и канавки на роторе могут препятствовать его способности замедлять автомобиль, а также вызывать вибрацию и пульсацию, которые можно почувствовать в педали.Кроме того, когда педаль больше не взаимодействует с тормозным ротором, возникающая вибрация может создать ощущение, что автомобиль вообще не остановится. Невозможность остановиться или даже увеличенный тормозной путь могут быть очень опасными, особенно если водитель вынужден сделать экстренную остановку.
Роторы дисковых тормозов являются очень важной частью тормозной системы и, как следствие, имеют решающее значение для общей безопасности и характеристик управляемости транспортного средства. Если вы подозреваете, что ваши роторы могут быть изношены или повреждены, обратитесь к профессиональному технику для осмотра автомобиля, чтобы определить, нуждается ли ваш автомобиль в замене тормозного ротора / диска.
Почему тормозные диски деформируются?
Тормозные диски — это большие металлические диски, видимые за колесами автомобиля. Они вращаются вместе с колесами, так что, когда тормозные колодки зажимают их, они останавливают автомобиль. Тормозным дискам приходится выдерживать огромное количество тепла. Мало того, они должны отводить это тепло в воздух как можно быстрее, потому что тормоза, вероятно, будут снова нажаты через короткое время. Если поверхность диска со временем станет неровной, торможение станет неустойчивым и менее эффективным.Обычно это называют деформацией.
Как деформируются тормозные диски
Распространенное заблуждение, когда роторы называют «деформированными», состоит в том, что они больше не прямые при вращении (подобно тому, как велосипедное колесо деформируется). Для автомобилей, чтобы это было так, сами роторы должны быть дефектными, поскольку температура, необходимая для того, чтобы сделать металл, который стал достаточно мягким, чтобы его можно было просто гнуть, была бы огромной.
Вместо этого деформация на самом деле означает, что плоская поверхность ротора становится неровной.Тепло является причиной номер один и может вызвать деформацию более чем одним способом:
Покрытие тормозного ротора материалом с тормозной колодки . Это происходит потому, что тормозные колодки, как и шины, изготавливаются с разной степенью твердости и липкости в зависимости от предполагаемого назначения. Когда тормозные колодки, предназначенные для нормального использования на дорогах, сильно нагреваются от движения и торможения на высоких скоростях или от езды на тормозах в течение длительного периода времени, цепкий материал может стать слишком мягким и в основном «окрасить» тормозные диски.Это означает, что тормозные колодки не будут зацепляться за металл при повторном нажатии на тормоз, что приведет к снижению эффективности торможения, которое становится менее плавным, чем раньше.
Износ поверхности ротора и образование более твердых участков на металле остаются слегка приподнятыми над поверхностью . Причина того, что тормоза обычно не изнашиваются, в значительной степени связана с довольно простой концепцией. Поскольку металл ротора тверже, чем тормозная колодка, прикладывающая к нему трение, колодка изнашивается, в то время как ротор остается в значительной степени не затронутым.При чрезмерном нагревании металл становится достаточно мягким, чтобы колодка изнашивала поверхность ротора. Это означает, что немного менее плотные участки металла изнашиваются быстрее и более твердые участки выступают, вызывая коробление.
Как предотвратить деформацию тормозных дисков
Чтобы предотвратить застекление тормозных дисков материалом тормозных колодок, помните о том, сколько тормозит автомобиль по сравнению с тем, что происходит при нормальной работе. При длительном движении под уклон постарайтесь контролировать скорость автомобиля, переключая трансмиссию на более низкую передачу.Для автоматики единственный вариант — переключиться на «3», в то время как автомобили с механической или другой переключаемой коробкой передач могут выбрать лучшую передачу в зависимости от оборотов двигателя. Когда тормоза горячие, никогда не садитесь с нажатой педалью тормоза на одном месте.
Кроме того, при первой установке тормозных колодок их следует правильно сломать, чтобы не оставлять слишком много материала на тормозном роторе. Обычно это включает в себя доведение автомобиля до скорости движения и последующее торможение, пока он не разгонится на десять миль в час медленнее.После того, как это будет сделано несколько раз, вы можете перейти к торможению до полной остановки. Первые несколько полных остановок после этого следует делать осторожно. Это позволяет тормозной колодке работать лучше при резком торможении на дальней дороге.
Меры, которые можно предпринять для предотвращения чрезмерного износа поверхности тормозного ротора, аналогичны шагам по предотвращению остекления роторов. Избегайте резкого торможения, если тормозные диски стали горячими в результате длительного использования.
На что похожи деформированные роторы?
При диагностике деформации роторов необходимо обратить внимание на несколько симптомов:
Если тормозные диски застеклены, вы можете услышать сильный скрип при нажатии на тормоза или даже почувствовать запах горящей резины.
Если торможение внезапно становится неустойчивым и непостоянным, в первую очередь следует подозревать тормозные диски.
Если автомобиль вибрирует при остановке, скорее всего, тормозной ротор деформируется.
Что такое тормозная система и как ее избежать после карантина?
Недавний карантин привел к тому, что многие люди потеряли работу или начали работать из дома. По какой-то причине меньше людей водят свои машины, чем обычно, и при этом значительно снизился трафик.Хотя это может показаться идеальным для многих людей, это также может вызвать некоторые незначительные проблемы с вашим автомобилем, потому что он не используется или используется значительно реже. Одна из этих потенциальных проблем называется заеданием в тормозной системе, и об опасности оставить машину сидящей не так много говорят, но это может вызвать некоторые проблемы.
Независимо от того, простаивала ли ваша машина из-за того, что она не использовалась или из-за вспышки COVID-19, проверка тормозов на вашем автомобиле также является частью общей безопасности и технического обслуживания.
Что такое залипание тормоза и что его вызывает?
Тормозное заедание обычно является проблемой в более влажном климате или когда автомобиль припаркован на улице в непогоды, независимо от наличия тканевого покрытия автомобиля. Поскольку компоненты тормоза не используются, на них может начаться коррозия, и именно в этой коррозии начинается проблема.
Коррозия поверхностного слоя тормозов — обычное дело, даже если автомобиль простоял всего несколько дней. Проблема возникает, когда автомобиль простоял достаточно долгое время, например, несколько недель, и площадь коррозии увеличилась.Само заедание возникает, когда из-за этой коррозии компоненты тормозной системы буквально слипаются, что может быть проблематичным по нескольким причинам.
Автомеханик меняет тормозной диск Range Rover Evoque в гараже | Marijan Murat / picture allianceСВЯЗАННЫЙ: Вы можете неправильно использовать тормоза
Заедание может снизить способность автомобиля замедляться из-за нарушения работы тормозной системы. Это может быть опасно, если вы не можете вовремя остановиться, чтобы предотвратить столкновение.
Как предотвратить или избавиться от заедания в тормозной системе
Заедание в тормозной системе, вызванное несколькими днями коррозии, обычно можно устранить, управляя автомобилем умеренно и осторожно нажимая на тормоза.
В более серьезных случаях безопаснее и проще полностью заменить основные механические части тормозов, такие как роторы и тормозные колодки. Однако это не всегда самый экономичный вариант, поэтому, если вы сможете полностью предотвратить заедание тормозов, вы, вероятно, сэкономите дорогостоящую поездку к местному механику.
Тормозные колодки Toyota 4Runner TRD | ToyotaСВЯЗАННЫЙ: Следы на ваших тормозных роторах — плохой знак?
Если вам не нужно путешествовать каждый день, неплохо было бы завести машину и немного покататься на ней. Поездка во время карантина может быть хорошим способом выбраться из дома, даже если вы просто обойдете квартал.
В качестве альтернативы, вы можете медленно двигать автомобиль на ходу и назад в пределах нескольких ярдов от того места, где он уже припаркован, и несколько раз нажать на тормоза.Это не только хорошо для предотвращения или уменьшения трения в тормозной системе, но и для поддержания движения важнейших жидкостей внутри механических компонентов вашего автомобиля.
Тормозное заедание может существенно повлиять на способность вашего автомобиля останавливаться быстро и безопасно, и этого достаточно легко избежать, поэтому вам следует подумать о принятии необходимых мер предосторожности. Если вы находитесь в положении, когда вы не можете управлять своим автомобилем каждые несколько дней, например, скажем, вы оставили его в аэропорту на неделю или две, то важно водить осторожно и оставить дополнительное пространство и время для торможения до появления коррозии. износился с тормозных колодок.
Если вы продолжаете слышать визг тормозов через несколько миль или испытываете тряску при торможении, обратитесь к местному механику, чтобы убедиться, что тормоза можно восстановить, поскольку отказ тормозов может быть потенциально опасным.
TRW True Originals Тормозные диски
Будьте уверены, выбирая сменные тормозные диски от TRW, экспертов по оригинальной тормозной системе и мировых разработчиков систем безопасности оригинального оборудования.
- Исключительное покрытие европейского автопарка
- Безопасность, производительность и эффективность торможения в соответствии со стандартами оригинального оборудования и выше
- Жесткие производственные допуски для беспроблемной установки
- Упаковка без остатков — используйте прямо из коробки
Миллионы доверяют тормозным дискам TRW True Originals
Как всемирно признанные специалисты по тормозной системе, мы ежегодно производим более 12 миллионов тормозных дисков для производителей автомобилей и независимого рынка запасных частей.TRW True Originals — это всего лишь оригиналы, которые никогда не являются копией существующей модели. Мы проектируем и производим все с нуля, чтобы отвечать реальным вызовам, с которыми сталкиваются ваши клиенты, и, поскольку мы никогда не прекращаем исследования и разработки новых функций безопасности и производительности, вы всегда будете иметь доступ к последним разработкам в области тормозных технологий, чтобы перейти к ним. ваши клиенты.
Знаете ли вы, что мы упаковываем все наши тормозные диски в бумагу с VCI (летучим ингибитором коррозии), а не покрываем их маслом или средством для защиты от ржавчины? Вы просто достаете их из коробки и приступаете к работе — не нужно тратить время на чистку перед установкой.
Чтобы обеспечить повышенную коррозионную стойкость и производительность, наши разработчики разработали новую отраслевую концепцию: окрашенные в черный цвет тормозные диски. Покрывая части диска нашей специально разработанной черной краской, мы создаем уникальную поверхность, которая действует как защитный барьер от коррозии.
Жесткие допуски на рабочие характеристики чугунного дискаКогда мы производим TRW True Originals, мы контролируем каждую деталь каждой детали.Поскольку мы стремимся производить самые безопасные и высококачественные тормозные диски, мы используем тщательно контролируемую смесь сырья для производства лучшего серого чугуна. Осуществляя этот процесс, это означает, что мы можем быть уверены в наилучшем литье для наилучшего качества исполнения.
Все наши отливки производятся с жесткими допусками из высококачественного чугуна EN-GJL-150 или EN-GJL-200.
- Изменение толщины диска (DTV) никогда не превышает 10 мкм
- Биение не превышает 30 мкм
- Центральное отверстие закреплено по норме H8
Отливки перед отправкой на обработку проходят строгие испытания на безопасность и контроль.Эти жесткие допуски обеспечивают беспроблемную установку для вас и удобную работу для вашего клиента.
Повышенная безопасность торможения с установленными подшипниками
Ассортимент TRW True Originals включает тормозные диски со встроенными подшипниками и сенсорными кольцами ABS. Использование масла, изношенных или поврежденных подшипников увеличивает риск повреждения диска, поэтому тормозные диски TRW True Originals доступны в уже собранном виде с установленными колесными подшипниками. Мы также предлагаем зубчатые и магнитные кольца для датчиков ABS.
Более жесткие допуски на тормозные диски
Когда мы проектируем наше оригинальное оборудование, мы контролируем каждую деталь каждой детали и не идем на компромисс в отношении сырья или допусков на обработку. Все наши отливки изготавливаются из высококачественного материала GG20 или GG15HC для арбона H igh C . И мы строго контролируем три других допуска на обработку: DTV (изменение толщины диска) никогда не превышает 12 мкм; биение никогда не превышает 30 мкм; а центральное отверстие закреплено на норме H8.Это означает легкую установку и удобную работу без сюрпризов.
Дисковые тормоза с предохранителем из чугуна
Поскольку мы стремимся производить самые безопасные и высококачественные тормозные диски, для производства лучшего серого чугуна используется тщательно контролируемая смесь сырья. Качества процесса обработки недостаточно — это должна быть наилучшая смесь из начального литья для достижения наилучшего конечного качества работы.
Наши исчерпывающие тесты гарантируют:
- Высокое содержание углерода (текучесть облегчает отливку и механическую обработку, а также имеет низкую степень усадки)
- Низкая температура плавления (1140 ° C — 1200 ° C)
- Высокая износостойкость
- Высокая теплоемкость
- Высокая прочность на растяжение и сжатие, обеспечивающая высокую жесткость
Затем отливки проходят ряд строгих испытаний и проверок перед отправкой на обработку для обеспечения высочайшего уровня безопасности.
Полукомпонентные тормозные диски
В соответствии с европейскими правилами по выбросам CO2 производитель должен гарантировать, что средние выбросы всех новых автомобилей, которые он производит и которые зарегистрированы в Европейском сообществе, находятся на уровне или ниже допустимого уровня выбросов для его автомобиля. тип. Это привело к переходу автомобильного рынка в эпоху «облегчения» и активизации НИОКР с акцентом на следующих ключевых факторах:
- Уменьшение веса
- Экономия топлива и выбросы CO2
- Автомобиль с улучшенными характеристиками и управляемостью
BMW и Mercedes-Benz разработали линейки полукомпаундных дисков для нескольких моделей из своего портфолио, а ZF Aftermarket предлагает линейку высокопроизводительных двухкомпонентных тормозных дисков, предназначенных для повышения безопасности и производительности, а также увеличения срока службы в более тяжелых , более мощные автомобили, охватывающие дизайн BMW и Mercedes.
Повышенная безопасность с подшипниками и кольцом датчика ABS
Мы также предлагаем ассортимент тормозных дисков со встроенными подшипниками, сенсорными кольцами ABS и крепежными аксессуарами. Это значительно упрощает жизнь, когда дело доходит до установки, поскольку эти важные компоненты безопасности часто повреждаются при замене диска. Использование старого, изношенного или поврежденного подшипника также может увеличить риск повреждения самого диска. Тормозные диски TRW с установленными колесными подшипниками собраны так, чтобы обеспечить правильную запрессовку подшипника.В зависимости от требований мы поставляем как зубчатые, так и магнитные кольца датчиков ABS.
Превосходство TRW в вашей мастерской — посмотреть каталог
ТОП-24 производителей тормозных дисков OEM
Другой важной частью дисковой тормозной системы является тормозной диск, также называемый тормозным ротором.
Чтобы полностью остановить автомобиль, ротор должен соединяться с тормозными колодками для создания тормозного усилия.Тормозной диск работает всякий раз, когда на педаль оказывается давление, тормозной суппорт, в свою очередь, прижимает тормозные колодки к диску.
Тормозной диск в основном продается крупными компаниями вместе с суппортом и признан суппортом дискового тормоза. Непосредственный потребитель покупал его в комплекте, но некоторые крупные производители OEM по-прежнему упаковывали и продавали его по отдельности.
Обзор рынка тормозных дисков
Дисковые тормоза в настоящее время широко используются в тормозных системах большинства транспортных средств. Растущие требования к безопасности на дорогах увеличили спрос на дисковые тормоза и, как ожидается, в ближайшие годы будут постоянно оказывать положительное влияние на другие компоненты тормозов.
Самое главное, что открыт огромный рынок как для тормозных дисков, так и для их компонентов.
Согласно отчету об исследовании рынка, опубликованному в «Отчете о размере рынка тормозных дисков за 2019–2024 годы», к 2024 году рынок может достичь 8060 миллионов долларов при среднегодовом темпе роста 8,2%.
Источник: https://www.grandviewresearch.comТакже улучшенный тормозной диск, изготовленный из керамического сырья, оптимистично пользуется большим спросом на рынке США. Ожидается, что в течение прогнозного периода 2019-2025 гг. Показатель CARG вырастет на 2,6%.
Однако материальный компонент тормозного диска довольно дорогой, поэтому он предлагается производителями в качестве опции, а не в стандартной комплектации.
Доступны различные типы тормозных роторов: гладкий ротор, шлицевой ротор и перфорированный ротор
Используется как в легковых, так и в грузовых автомобилях.
Давайте перейдем к продукции с тормозными дисками от ведущих производителей автомобильного оборудования.
Список 24 ведущих производителей тормозных дисков OEM
Центрический ротор
Недавно Centric Parts объединилась с AP Emissions и образовала новую компанию под названием «APC Automotive Technologies».
Линейка продуктов APC насчитывает более 145 000 компонентов тормозной системы, а также компонентов шасси для легковых и средних грузовиков. Центрические тормозные диски являются одними из наиболее востребованных компонентов автозапчастей.
StopTech, еще один популярный во всем мире бренд, также производится APC.
Центрический тормозной ротор дает следующие преимущества конечному пользователю:
- Доступны роторы с покрытием и без покрытия
- Поставляется с направляющей, набором штифтов и уплотнениями
- Прямая установка без необходимости обкатки
- Сырье высшего сорта для улучшения характеристик
- Тормозной диск широкий выбор для 1-8 автомобилей средней и большой грузоподъемности
Чтобы узнать больше о центробежных роторах, распространяемых APC, вы можете посетить их официальную страницу и проверить их бесплатную презентацию продукта в формате pdf, указанную ниже.
Дополнительные ресурсы по центральным деталям:
Тормозной диск Brembo
Продукция Brembo пользуется доверием в течение многих лет, и тормозной диск, производимый ими, включен в комплект поставки. Тормозные диски производства Brembo упаковываются индивидуально, а также доступны для продажи как дисковые тормоза.
Непревзойденные опытные инженерыBrembo позволяют разработать универсальный и эффективный тормозной диск с точки зрения комфорта и производительности.
Сегмент дисковой продукции охватывает около 98% всего автомобильного рынка.Углеродно-керамические диски Brembo доступны для эксклюзивных автомобилей; плавающий в цельнолитый для спортивных моделей премиум-класса и неразъемный диск для средних и городских автомобилей.
Около 50 миллионов роторов в год производит и поставляет Brembo, широко распространенная в разных странах.
Эти дисковые продукты обеспечивают отличные функции улучшения в различных аспектах:
- Разработано УФ-лакокрасочное покрытие в сотрудничестве с производителями автомобилей
- Эксклюзивная система вентиляции на стойках, запатентованная Brembo
- Диски с отверстиями или прорезями для уменьшения нагрева, пыли и газов
- Все диски категории Спорт оцинкованы
- Композитный и плавающий диск предлагаются престижным автомобилям
- Тормозной диск из чугуна с высоким содержанием углерода для уменьшения вибрации
- Отверстия для тормозного диска на тормозных поверхностях для улучшения характеристик на мокрой дороге
- Доступны различные шаблоны для обработки диска в зависимости от конечного применения
Представлена новейшая концепция легкого тормозного диска, который примерно на 10-15% легче стандартного тормозного диска.Также предлагается сочетание двух различных материалов, таких как чугун и сталь.
Чтобы узнать больше о роторе Brembo, вы можете воспользоваться полезными ссылками, перечисленными ниже.
Дополнительные ресурсы компании Brembo:
Ротор EBC
ТормозаEBC стали популярными в автомобильной промышленности из-за тормозных колодок.
Еще одна деталь тормозов, которая признана и востребована во всем мире, — это ротор EBC.
EBC предлагает широкий спектр решений для автомобилей и грузовиков, но последние 35 лет специализируется на торможении мотоциклов и квадроциклов.
Выделенный улучшенный тормозной диск EBC — это то, что они назвали «Полностью плавающие двухкомпонентные тормозные диски». Доступны 3 варианта покупки:
1) Роторы SG2F EBC, которые служат прямой заменой для высокопроизводительных автомобилей, таких как Nissan GT-R
2) Тормозной диск G2FC EBC, преобразование из двух частей с плавающим ротором, которые модернизируют цельные чугунные роторы OEM
3) Роторы SG2FK, входящие в состав Balanced Brake Kits ™ компании EBC Brakes Racing.
Характеристики и развитие ротораEBC:
- G3500 сырьевой компонент для литого наружного кольца
- Всего 48 лопаток с изогнутыми левого и правого лопаток для повышения эффективности охлаждения
- Прецизионный станок для изготовления заготовок из алюминия
- Оцинкованные шпульки SD-Drive
- Обеспечьте легкость работы
- 20 Тормозной диск EBC, стандартный и специально разработанный для мотоциклов и скутеров категории
- Утвержденный ECE R90 Диск EBC, рекомендованный для грузовых автомобилей
Каждый тормозной диск EBC имеет уникальный дизайн в зависимости от типа транспортного средства, для которого он предназначен.EBC может быть разумным выбором, если вы намереваетесь инвестировать в мотоциклетную нишу.
Чтобы узнать больше о дисковых продуктах EBC, пожалуйста, проверьте доступные ресурсы ниже.
Дополнительные ресурсы EBC:
Ротор Гальфера
Galfer USA — ведущий поставщик и производитель тормозных систем для мотоциклов, гонок и велосипедов.
Роторные сегментыGalfer делятся на 5 классов: внедорожные, уличные, ATV SXS, велосипедные и V-образные.
Общее количество уникальных конструкций роторов Гальфера: 8 для внедорожного типа, 4 для уличной категории, 2 для гонок и 1 для квадроциклов и треков.
Преимущества и преимущества тормозного дискаGeneral Galfer перечислены ниже:
- 420 высокоуглеродистая нержавеющая сталь Используется компонент
- Пуговицы или шпульки из алюминия или нержавеющей стали
- Использует лазер для точной резки
- Параллельный двойной тормозной диск, заземление
- Обеспечены преимущества жаростойкости и коррозионной стойкости
- Варианты держателя доступны в вариантах из алюминия и нержавеющей стали
Другие дополнительные функции настройки предлагаются Galfer; цветные кнопки и специальное покрытие.
Чтобы узнать больше о тормозных дисках Galfer, ссылки на их официальный сайт доступны ниже.
Дополнительные ресурсы Galfer в США:
Ротор Bosch
В настоящее время, наряду с крупными и успешными производителями оригинального оборудования, Bosch является одним из ведущих производителей тормозных дисков. Ротор Bosch производит до 20 миллионов единиц в год на различных заводах. Среди азиатских брендов тормозных дисков Bosch является одной из крупнейших компаний, охватывающих в общей сложности 600 номеров деталей, обслуживающих такие крупные автомобильные компании, как Toyota, Nissan, Honda, Perodoa и Proton.
Тормозной дискBosch отличается высокой теплопроводностью, точной подгонкой и термостойкостью.
Недавно Bosch выпустила новую дисковую программу, которую можно использовать на автомобилях в 30 различных регионах. Ниже перечислены преимущества ротора Bosch:
.- Износостойкость
- Точное согласование с любым типом автомобиля
- Высокоуглеродистая технология для повышения комфорта при работе
- Отличные защитные кожухи дисков
- Качественное сырье, используемое в производстве
Если вы хотите познакомиться с роторами Robert Bosch, ниже приводится полезный источник, который вы можете посетить.Совершенствование компании Bosch, призванное объединить усилия для улучшения климата в мире, должно стать углеродно-нейтральным, начиная с 2020 года.
Тормоза Bosch Ресурсы:
Ротор Akebono
РоторыAkebono охватывают широкий выбор автомобилей и коммерческих автомобилей. Тормозной ротор Akebono гарантирует высокую тормозную силу.
РоторыAkebono распространяются и устанавливаются среди популярных автомобилей японских производителей, таких как Toyota, Honda, Mitsubishi и Isuzu.В том числе таких популярных мировых производителей, как GM, Mercedes Benz, Ford и Porches.
Это одни из немногих общих преимуществ ротора Akebono:
- Плоские гладкие поверхности для стабильного торможения
- Доступны как с просверленным, так и с шлицевым ротором
- 10 фунтов. легче стандартного ротора
- Интегрирован с двухкомпонентной прорезью типа
- Доступен с передним и задним ротором
- Фурнитура с цинковым покрытием
Ниже перечислены полезные ресурсы, если вы хотите узнать больше о роторах Akebono
.Дополнительные ресурсы по Акебоно:
Тормозной ротор WAGNER
Тормозной ротор WAGNER спроектирован совместно с тормозными колодками премиум-класса собственной компании.Обе тормозные составляющие имеют положительный спрос на рынке. Тормозные роторы Premium Wagner® легко устанавливаются без остатков масла. Ротор WAGNER имеет в наличии 926 тормозных деталей для транспортных средств Северной Америки, Азии и Европы.
Преимущества ротора WAGNER демонстрируются годами; В каждой поставленной и изготовленной единице продукции прослеживаются следующие особенности:
- Улучшение с защитным гальваническим покрытием на не тормозных поверхностях
- Черное специальное покрытие
- Улучшен за счет уникального дизайна ЛОПАТКИ
- В пакете с ингибитором паровой коррозии (VCI)
- Прецизионная обработка внешнего диаметра
Тормозной ротор WAGNER Подробная информация о других продуктах доступна на ресурсах, перечисленных ниже.
Дополнительные ресурсы WAGNER:
Ротор Wilwood
Wilwood предлагает широкий выбор роторов как для автомобилей, так и для мотоциклов, а также для грузовых автомобилей / внедорожников. Wilwood входит в число компаний, которые имеют полный комплект тормозных деталей в своей производственной линейке.
Тормозной дискWilwood имеет более 120 различных стилей и диаметров, доступных для их применения.
Как правило, диски Wilwood обладают следующими характеристиками и преимуществами.
- Наличие пазов и отверстий
- Состоит из высококачественной стали, углеродистой керамики и железа.
- Доступны индивидуальные отверстия и специальное покрытие
- Поверхности идеальной плоскостности
- Уникальные стили, разработанные лопатками
Одним из больших преимуществ выбора WAGNER является большой ассортимент их тормозных дисков.
Подробная информация о диске 120 WAGNER представлена на сайте компании, на который можно перейти по ссылкам, указанным ниже.
Дополнительные ресурсы Wilwood:
Диск тормозной ATE
Тормозной дискATE — еще одна тормозная деталь производства компании ATE. Ate обеспечивает исключительную экологичность всех продуктовых линеек.
Тормозные диски производства ATE доступны примерно для 98% автомобилей европейских поставщиков.
Чтобы просто проверить оригинальные запчасти ATE от компании, есть установленный код MAPP, который можно сканировать с упаковки продукта.
Для опций доступны различные категории стилей: тормозной диск с покрытием, тормозной диск с фиксирующим винтом, двухкомпонентный тормозной диск, тормозной диск со встроенным ступичным подшипником и, наконец, специальный тормозной диск ATE для Mercedes Benz.
Преимущества и преимущества тормозного дискаATE:
- Используются материалы высшего качества.
- Идеальный диск для каждой модели автомобиля
- Установить высокоуглеродистый компонент на все тормозные диски ATE
- Ворд-класс разработан
- Особенность высокого уровня коррозионной стойкости
- Тормозной диск легче обычного
- Сертификаты ECE R90 выполнены
Тормозной диск ATE настоятельно рекомендуется для европейских автомобилей.
Если вы являетесь владельцем бизнеса, розничной торговли или дистрибьютора европейской автомобильной ниши, ATE — это разумный выбор.
Дополнительные ресурсы по тормозам ATE:
Ротор Накамото
NAKAMOTO — это компания со штаб-квартирой на Тайване, основанная семьей Линь и более 35 лет работающая в обрабатывающей промышленности.
Их продукция сейчас распространяется по всему миру в 50 странах, и многие профессионалы предпочитают ее.
Доказанное качество роторов Nakamoto теперь признано, поскольку они вошли в число лучших производителей тормозных дисков.
Вот лишь некоторые характеристики ротора Nakamoto:
- оцинковка
- Меньшее преимущество в пылеобразовании
- Простая установка
- Представлен стиль просверленных отверстий и пазов
- Двойной шлифованный диск
- Идеальная посадка и форма оригинального оборудования
- Доступны в исполнении с прямой и направленной лопаткой
Nakamoto гордится тем, что сотрудничает с 1AAuto.com, онлайн-специалистом, занимающимся домашними делами, который занимает первое место в рейтинге «Сделай сам». Это позволяет легко разбираться в тормозах.
Чтобы узнать больше о тормозном диске Nakamoto, перейдите по ссылкам ниже.
Накамото Дополнительные ресурсы:
Ротор ACDelco
ACDelco — производитель оригинального оборудования для автомобилей GM. Тормозной диск, производимый ACDelco, относится к сегменту профессиональных дисковых тормозов.
Эта линейка продуктов предлагается как для автомобилей GM, так и для автомобилей других производителей.
- Ротор Advance ACDelco предлагает следующие характеристики и преимущества:
- Каждый тормозной ротор ACDelco проверяется на сбалансированное качество
- Протестировано на устойчивость к шуму / вибрации / жесткости
- Доступны варианты от тормозного диска ACDelco с покрытием до без покрытия
- Сделано с применением технологии нитро-науглероживания ферритина
- Изготовлен из нескольких сплавов для оптимального теплоотвода и рабочих характеристик
Чтобы узнать больше о роторе ACDelco, ниже доступны полезные ссылки.
Дополнительные ресурсы:
Диск тормозной ZIMMERMANN
Otto Zimmermann GmbH — немецкий производитель компонентов для автомобилей уже более шести десятилетий.
Тормозные дискиZimmermann уже давно доказали высокое качество тормозов.
В общей сложности 4000 различных компонентов тормозов, включая диск Zimmermann, поставляются в более чем 60 стран мира. Роторы производства Zimmermann доступны в легковых и легких коммерческих автомобилях.
Тормозной диск Zimmermann предлагает пять вариантов покупки: стандартный тормозной диск, спортивный тормозной диск, тормозной диск FusionZ, тормозной диск для легких коммерческих автомобилей и тормозной диск с покрытием Z.
Каждый ротор Zimmermann имеет уникальные особенности продукта, обычно преимущества диска следующие:
- Широкий ассортимент продукции с более чем 1000 предпочтениями клиентов
- Эквивалентные запасные части в соответствии с постановлением KFZ-GVO (ЕС) 330/2010
- Неизменно высокое качество продукции
- Для специальных покрытий
- Канавки и отверстия для лучшего отклика при торможении
- Широкий модельный ряд LCV типа
Если вам нужны тормозные диски немецкого качества, Otto Zimmermann GmbH — разумный выбор.
Вы можете ознакомиться с дисками Zimmermann и другими продуктами по указанным ссылкам.
Дополнительные ресурсы:
Ferodo тормозной диск
Ferodo — лидер рынка мирового класса и пользующийся доверием бренд. Лучший выбор в области трения для производителей оригинальных комплектующих, таких как Jaguar, Fiat, Lan Rover и Volkswagen.
Ferodo широко известна своими непревзойденными экологичными тормозными колодками. Компания тщательно спроектировала тормозной диск, идеально подходящий для своих колодок, чтобы добиться высочайшего качества тормозных характеристик.
Тормозные диски, производимые Ferodo, используются в широком спектре мотоциклов, легких и коммерческих автомобилей.
Все распространяемые диски Ferodo проверены и одобрены инженерами компании.
Такими характеристиками продвижения продукта являются:
- Исключительная металлургия и дизайн
- Диск демпфирования высокой вибрации
- Характеристики теплоотвода
- Ненаправленная обработка поверхности
- Постоянная маркировка кромок для полной прослеживаемости
- Установка без проблем
- Coat + технология исключает обезжиривание перед установкой для отдельных областей применения
- Улучшение с технологией Pillar Venting
- Широкий ассортимент продукции для мотоциклов
Вы можете ознакомиться с тормозным диском Ferodo и другими продуктами по ссылкам ниже.
Дополнительные ресурсы:
Диск континентальный
Continental AG, широко известная как Continental, — немецкая автомобильная компания, которая поставляет компоненты тормозных систем, внутреннюю электронику, автомобильную безопасность, компоненты трансмиссии и шасси, тахографы, шины и другие детали для автомобильной и транспортной промышленности.
Они заняли 4-е место среди крупных компаний по производству шин.
Недавно Continental AG выпустила тормозные диски для автомобилей Mercedes Benz.
OEM Континентальный тормозной диск, изготовленный простой, предназначен для легковых автомобилей:
- С простым электрическим стояночным тормозом — выключатель EPB
- Облегченный тормозной диск
- Встроенная функция экстренного торможения с высоким замедлением и стабильностью
- Система Plug and Play для OEM
- Реализация различных вспомогательных функций для обеспечения безопасности и комфорта
- Взаимозаменяемость между автоматическим и ручным режимом применения
- EPB Функциональность и комфорт в автомобилях класса A / B
Continental AG предлагает обширные линейки продуктов, но они гарантируют качество в каждой единице.Чтобы узнать больше о тормозных дисках Continental. Доступные полезные ссылки перечислены ниже.
Дополнительные ресурсы Continental AG:
TRW Ротор
TRW теперь является частью мирового лидера рынка OEM для автомобильной промышленности ZF Friedrichshafen.
С более чем 1250 тормозными дисками полностью покрывает 98% европейских автомобилей, которые превышают спецификации оригинального оборудования, — это то, что производит TRW.
В настоящее время в линейке роторов TRW запущен расширенный ассортимент дисков для электромобилей; Tesla Model S.Доступно только для диска передней оси.
РоторAdvance TRW имеет следующие характеристики:
- Диск с полным покрытием
- Экологически чистая окружающая среда
- Тормозной диск с черным цинковым покрытием
- Пакет без защитного масла для простой установки
- Улучшение с использованием высокоуглеродистого материала
- Диск идеальной балансировки
- Устанавливается с кольцом датчика ABS для большей безопасности
Тормозной диск TRW основан на более чем 100-летнем опыте и опыте.Диск гарантированно относится к тормозным деталям мирового класса на рынке.
Вы можете проверить ссылки ниже, чтобы узнать больше о тормозных дисках TRW.
Другие ресурсы по TRW ZF:
ПОВЕРХНОСТЬ Диск
Surface Transform — производитель углеродно-керамических тормозных дисков для автомобилей и самолетов.
Surface Transform — сертифицированный поставщик тормозных комплектов таких популярных автомобильных брендов, как Porsche, Nissan GT-R, Ferrari, Aston Martin и Rolls Royce.
Поверхностный диск с углеродно-керамической технологией обеспечивает отличное торможение для популярных моделей автомобилей.
Преимущество продукта поверхностного тормозного диска следующее:
- Экономия веса до 70%; около 20 кг
- Меньший уровень шума, вибрации и резкости
- Повышенная производительность в экстремальных погодных условиях
- С функцией уменьшения износа тормозов
- Не подвержен коррозии
Surface Transforms сертифицирован ISO и ITAF.Дополнительная информация о продукте доступна на официальном сайте Surface Transform.
Дополнительные ресурсы преобразования поверхности:
Диски тормозные JURID
Еще одним непревзойденным компонентом дисковых тормозов от Jurid являются тормозные диски.
Тормозной дискJurid тщательно разработан, протестирован на безопасность и точность для 98% легковых и коммерческих европейских автомобилей на дорогах.
Диск идеального качества, сочетающийся с тормозными колодками Jurid для непревзойденного тормозного усилия:
- Передовые технологии и дизайн в области металлургии
- Улучшено с применением антикоррозийной технологии NONOX
- Доступен с ненаправленной отделкой
- Гарантированная износостойкость и шумовое торможение
- Выдерживает экстремальные погодные условия
Если вам нравятся тормозные диски для европейских автомобилей, Jurid — это мудрый выбор.
Ссылка, указанная ниже, направит вас на официальные сайты JURID
JURID Тормоза Ресурсы:
Ротор Winhere
WINHERE Brake Parts, Inc. (WBPI), расположенная в Чикаго, является дистрибьюторским подразделением Winhere Auto-Part Manufacturing Co. Ltd. Winhere Auto, материнская компания, быстро становится крупнейшим производителем тормозных дисков / барабанов в Китае.
РоторWinhere обеспечивает более 99% покрытия легковых автомобилей, внедорожников, легких и средних грузовиков на дорогах.
Разнообразие тормозных дисковWinhere доступно от стандартных до высокоуглеродистых, с покрытием или без покрытия, с отверстиями или прорезями.
Тормозной диск производства Winhere называется ULTRAHC.
Преимущества тормозных дисков Winhere следующие:
- Тормозной диск с индивидуальной внешней отделкой
- С уменьшением теплового дрожания
- Бесшумное торможение
- Устойчивость к высоким температурам
- Улучшено с помощью технологий металлургии
- Опциональная конструкция лопатки для оригинального оборудования как с прорезями, так и с просверленными отверстиями
- Характеристики устойчивости к пульсации
Чтобы узнать о продуктах мирового класса Winhere, используйте следующие ссылки.
Дополнительные ресурсы Winhere:
Диск тормозной REMSA
REMSA имеет более чем 45-летний опыт производства деталей тормозов в автомобильной промышленности.
Тормозной дискREMSA предлагает широкий ассортимент для большинства автомобилей в Азии и Европе.
Диск производства REMSA идеально подходит для отличных тормозных характеристик.
Тормозные диски REMSA обладают следующими преимуществами и преимуществами продукта:
- С высоколегированным графитом
- Пройдите строгие испытания AK Master с помощью Dynamometer Simulation
- Поверхность ровная и ровная
- Производительность 20 миллионов дисков в год
Помимо тормозного диска REMSA, в их продуктовых линейках доступно больше высококачественных автомобильных запчастей.
Чтобы узнать больше о диске REMSA, дополнительные ресурсы доступны ниже.
Дополнительные ресурсы REMSA:
Delphi тормозной диск
Производители использовали преимущества использования новейших технологий, доступных при производстве дисковых тормозов, для улучшения тормозных характеристик. Delphi — один из наиболее конкурирующих крупных OEM-производителей. 1 ноября 2016 года они выпустили тормозные диски для новых автомобилей с сертификатом R90 наряду со старыми приложениями Delphi.
Тормозные диски производства Delphi доступны в 5 различных отливках и конфигурациях. Это высокоуглеродистые диски, перфорированные диски, вентилируемые диски, диски с подшипниками и, наконец, цельные чугунные диски.
Улучшение дискового тормоза Delphi улучшило характеристики продукта старого типа. Эти дополнительные функции:
- Пройти официальное тестирование ECE R90
- Предлагается со специальным цинково-чешуйчатым и серебряным покрытием Geomet
- Эстетичный дизайн
- Без масла, без труда и времени на обслуживание
- Простота установки и демонтажа Характеристики
Дополнительные ресурсы Delphi:
Получить цену тормозного диска
OPEN PARTS тормозной диск
Тормозной диск Open Parts производства Exo Automotive; Компонент тормозов, разработанный итальянской компанией.Этот тормозной диск является запасными частями, соответствующими европейским нормам качества.
Высококачественные тормозные диски Open Parts Характеристики продукта:
- Из серого чугуна GG20 с хлопьями графита
- Пройти строгий тест на безопасность
- Защищено антиоксидантной смазкой
- Интегрирован с кольцом ABS
- Доступен как с покрытием, так и без покрытия
- Покрытие широкого спектра французских автомобилей
Чтобы узнать больше о тормозном диске Open Parts, ссылки на официальный сайт EXO Automotive находятся ниже.
Дополнительные ресурсы:
Диск тормозной PILENGA
Другой итальянский тормозной диск OEM Fonderie Officine
Pietro Pilenga SpA пользуется большим спросом на рынке дисков.
Fonderie Officine Pietro Pilenga SpA является сертифицированным дистрибьютором BMW и других европейских брендов. Этот OEM-ротор затем справа от транспортных средств, которые он покрывает.
Тормозной дискPilenga имеет следующие преимущества и преимущества продукта:
- Стандартные тормозные диски, состоящие из двух частей
- Кольцо ротора чугунное
- На весь тормозной диск Pilenga нанесено специальное фосфатное покрытие.
- Доступна внешняя отделка как без покрытия, так и с покрытием
- Производственной мощностью 2 шт.5 миллионов штук
Fonderie Officine Pietro Pilenga SpA использует высокие технологии в механизмах, оборудовании и процессах для производства тормозных дисков.
Ссылки на их веб-сайт доступны ниже.
Дополнительные ресурсы:
TEXTAR тормозной диск
ТормозаTEXTAR спроектированы с высокой точностью для обеспечения превосходных тормозных характеристик с точки зрения безопасности и комфорта.
TEXTAR работает в обрабатывающей промышленности более 100 лет и признан ведущими мировыми производителями автомобилей.
Тормозной дискTEXTAR — это продукт немецкого производства, который предназначен для работы с тормозными колодками TEXTAR для достижения отличных тормозных характеристик.
Широкий ассортимент роторов TEXTAR насчитывает более 1 650 наименований для сектора легковых автомобилей для европейских автомобилей.
Преимущества тормозного диска Textar:
- Популярный французский автопроизводитель — диски со встроенным ступичным подшипником
- Улучшенный с высоким содержанием углерода
- Покрытие из специального материала для защиты от коррозии
- Модернизирован системой датчиков ABS
- Эстетичный дизайн
- Одобрено ECE R90
Подробную информацию о тормозных дисках TEXTAR можно найти в руководстве по тормозным дискам TEXTAR.
Чтобы узнать больше о высококачественном диске TEXTAR, вам помогут следующие ресурсы.
Дополнительные ресурсы:
Заключение
Инвестиции в тормозной ротор премиум-класса — это отличная возможность, но поиск надежных поставщиков действительно утомляет. Это основная причина, по которой мы собрали информацию, которая может помочь розничным торговцам, капиталистам, венчурным инвесторам, инвесторам, производителям оригинального оборудования, предприятиям и другим смежным отраслям найти лучшие тормозные диски или роторы на рынке.
Мы надеемся, что лучший поставщик станет партнером для вашего бизнеса по производству тормозных дисков.
Износ: Когда нужно менять тормозные диски и колодки?
Тормоза легкового автомобиля не только должны выдерживать чрезвычайно интенсивное использование. Тормозная система и все ее части также являются важным фактором безопасности. И поэтому безупречно работающие тормоза абсолютно необходимы.Именно поэтому их следует проверять каждый раз, когда машину забирают в сервис. Но когда нужно менять тормозные диски и колодки? И как узнать, когда они надеты?
Каков срок службы тормозов?К сожалению, невозможно сделать какие-либо общепринятые утверждения о сроке службы тормозных дисков и колодок. На продолжительность правильной работы тормозов влияет ряд факторов: на срок службы, в частности, влияют стиль вождения, вес автомобиля и материалы.Износ тормозов также зависит от того, много ли движется автомобиль по автомагистралям или больше в городском движении. Ясно одно: тормозные диски и тормозные колодки со временем изнашиваются, так как они преобразуют кинетическую энергию в тепловую за счет трения.
Для осторожных автомобилистов вполне возможно получить 100 000 и более километров пробега на одном комплекте тормозных колодок. Водителям, предпочитающим более быстрый стиль, придется менять тормозные колодки гораздо раньше. Интервалы от 10 000 до 15 000 километров не являются чем-то необычным.То же правило относится и к тормозным дискам: чем интенсивнее они используются — например, в результате частых и резких торможений — тем скорее их необходимо заменить.
Когда следует менять тормозные колодки?Тормозные колодки следует заменять не позднее, чем они изношены до толщины менее двух миллиметров. Большинство современных автомобилей оснащены индикаторами износа, предупреждающими водителя о необходимости замены.В случае электронных систем износ соответственно сигнализируется сигнальной лампой на приборной панели. В чисто механической версии металлический штифт, вставленный в колодку, при достижении предела износа издает неприятный шум из-за контакта металлического штифта с металлом тормозного диска.
Когда нужно менять тормозные диски?Важнейшим аспектом тормозных дисков является так называемая «минимальная толщина».Это минимальный размер, который должен иметь каждый тормозной диск и который указывается производителем. Он обозначается аббревиатурой «MIN TH» и находится на ободе или в камере тормозного диска. Обычно допускается износ от двух до трех миллиметров.
Естественный износ тормозного диска относительно легко обнаружить. Когда диск изношен, на ободе можно почувствовать заусенец, так как диск изнашивается только там, где наложена тормозная колодка. Чем более выражен заусенец, тем больше износ диска. Специалисты используют специальные инструменты для измерения толщины тормозных дисков.
BSD Диск
КОРРЕКЦИЯ ДЕФОРМАЦИИ РОТОРА, НЕИСПРАВНОСТИ РОТОРА И ИСКЛЮЧЕНИЕ ВИБРАЦИИ ТОРМОЗА
Есть две основные причины вибрации тормозов. Первый — это проблемы с геометрией рулевого управления, а второй — проблемы с установкой или биением ступицы.
ПРОБЛЕМЫ ГЕОМЕТРИИ — В каждом седьмом автомобиле в течение срока службы возникают проблемы с геометрией, которые могут повлиять на рулевое управление и вызвать вибрацию тормозов.Это НЕ проблема качества продукции !!!!!!. Это может произойти при простом движении по бордюру или проезду по выбоине. Не только EBC осознает эту проблему, но и является единственным поставщиком тормозов на планете, готовым предложить диагностику и РЕШЕНИЕ.
ПРОБЛЕМЫ УСТАНОВКИ ИЛИ ВЫПОЛНЕНИЯ ХАБА — Они вызывают так называемое DTV. На видео ниже показано, как исправить вибрацию тормозов, вызванную DTV (изменение толщины диска). ДТВ развивается в автомобиле после 3000-4000 км пробега из-за встроенного в автомобиль биения или из-за неправильной центровки роторов при установке.Это довольно распространенная неисправность современных автомобилей, и многие автомобили требуют ее при каждой замене ротора. Водители также путают деформацию ступицы с проблемой качества ротора, но в 99% случаев DTV — это проблема автомобиля, а не проблема качества ротора. Вы можете заменять роторы сколько угодно раз, пытаясь устранить вибрацию, и проблема исчезнет только через несколько тысяч миль, а затем вернется. Это означает, что вы добросовестно приобрели новые роторы, но проблема НЕ РЕШЕНА И НЕ ПРОЙДЕТ ПОСТОЯННО, пока вы не выполните эту процедуру.После этого скольжения с поверхности ротора у вас будут плавные тормоза, более эффективные тормоза и НУЛЕВАЯ вибрация. Это даже очень полезная практика при установке новых роторов, чтобы все четыре ротора были идеально выровнены на вашем автомобиле с помощью этой недорогой процедуры. Деформация ротора из-за DTV очень распространена, на самом деле ОДИН ИЗ СЕМЬ АВТОМОБИЛЕЙ имеет проблемы с геометрией рулевого управления либо когда он построен НОВЫМ, либо после того, как он наткнулся на бордюр или налетел на большую выбоину (очень часто после повреждения дорожного покрытия после зимних снежных периодов).Необразованные люди до сих пор говорят: «Мои роторы покоробились». Что ж, инженерные факты таковы: РОТОРЫ НЕ ИСКЛЮЧАЮТСЯ, они сделаны из чугуна, они очень прочные, их можно раз за разом нагревать до красного каления и охлаждать, и они не будут искажать, мы делаем это изо дня в день на наших динамометрических станциях в лаборатория EBC. Вот почему весь мир до сих пор использует чугун в качестве материала для тормозных дисков транспортных средств, его никогда не было, и, вероятно, никогда не будет. Станки Pro Cut РАБОТАЮТ НА ОБЕИХ ГЛАВНЫХ РОТОРАХ, И ДАЖЕ ЛУЧШЕ НА ПРОФИЛЬНЫХ И СВЕРЛЕННЫХ РОТОРАХ ВСЕХ ВИДОВ.
ПРОЧИТАЙТЕ ЭТОТ ТЕКСТ НА СТРАНИЦЕ 8 ЭТОЙ ССЫЛКИ, ЧТОБЫ ПОКАЗАТЬ ДОКАЗАТЕЛЬСТВО, ЧТО PRO CUT УТВЕРЖДАЕТ ИСПОЛЬЗОВАНИЕ СВОЕГО СТАНКА НА РОТОРАХ С ПЛИТОМ
https://www.procutinternational.com/pdf/pfmtrainingguide.pdf
Кто такие Pro-Cut ???? … Pro Cut — это многонациональная и чрезвычайно профессиональная корпорация, базирующаяся в США. Их машины используются и одобрены многими крупными производителями автомобилей и используются во всем мире, чтобы делать именно то, что они делают лучше всего, ПРАВИЛЬНО для несоосности ротора, независимо от того, как это происходит на автомобиле.Вы не можете добиться этого ни с одним другим устройством.
Щелкните здесь, чтобы получить информацию о центрах резки Pro
.